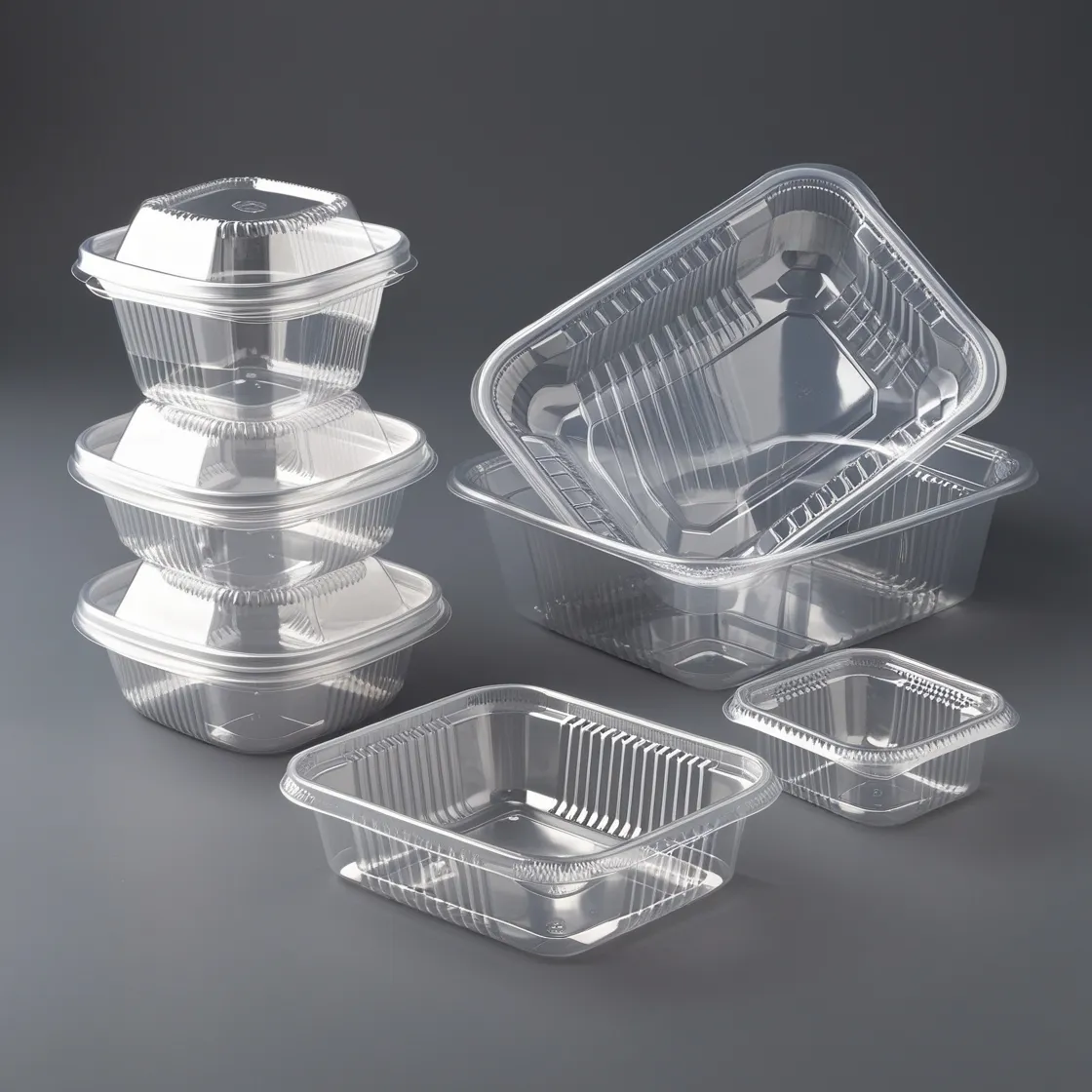
مقدمة
Thermoforming multi-station machines play a crucial role in the modern plastics processing industry. Their efficient production capabilities and wide range of applications make them the preferred choice for many companies. However, the performance and stability of the heating system directly impact the final product quality and production efficiency. This article will discuss common heating issues encountered in thermoforming multi-station machines, their causes, and corresponding solutions, providing in-depth technical guidance and references for industry professionals.
I. Basic Principles of the Heating System
The heating system of a thermoforming multi-station machine primarily heats thermoplastic sheets to a softened state for forming operations. The core components of the heating system include heaters, temperature sensors, controllers, and the heating zone. Heaters convert electrical energy into thermal energy to heat the plastic sheets; temperature sensors monitor the temperature of the heating zone in real-time; controllers adjust the heater’s power based on feedback from the temperature sensors to maintain a stable heating temperature.
Types of Heaters
Common types of heaters include resistance heaters, infrared heaters, and hot air heaters. Resistance heaters generate heat by passing current through resistive materials, often used where uniform heating is required; infrared heaters use infrared radiation to heat plastic sheets, known for their fast heating speed and energy efficiency; hot air heaters use convection to heat large areas, suitable for applications requiring extensive heating.
التحكم في درجة الحرارة
Temperature control is a crucial aspect of the heating system. By monitoring the heating zone temperature with sensors in real-time, the controller adjusts the heater’s operating state to ensure stable and uniform heating. Modern thermoforming multi-station machines often use PID control algorithms to achieve precise temperature control.
II. Common Heating Issues and Cause Analysis
During the actual use of thermoforming multi-station machines, several heating issues may arise, directly affecting production efficiency and product quality. Here are some common heating issues and their causes:
1.even Heating
Issue
Uneven heating is a common problem in thermoforming, manifested as localized overheating or underheating of the plastic sheet during heating, resulting in unstable product quality and potential waste.
Causes
·Improper Heater Arrangement: The position and number of heaters are not properly arranged, leading to uneven heat distribution in the heating zone.
·Heater Malfunction: Some heaters are damaged or malfunctioning, causing certain areas to be inadequately heated.
·Temperature Sensor Failure: Improper installation or malfunction of temperature sensors results in inaccurate temperature monitoring, affecting temperature control.
·Insufficient Heating Power: The heater power is insufficient to meet the demands of large-area heating, resulting in uneven heating.
2. Slow Heating Speed
Issue
Slow heating speed extends the production cycle and affects production efficiency. It is characterized by the plastic sheet taking a long time to reach the forming temperature during heating.
Causes
·Insufficient Heater Powe: The heater power is not adequately designed to heat the plastic sheet quickly.
·Large Heating Area: The heating area is too large, and the heater’s thermal output is insufficient to quickly heat the entire area.
·Aging Heating System: The performance of the heating system declines over long-term use, resulting in slower heating speed.
·Inaccurate Temperature Control: The temperature control system responds slowly and adjusts inadequately, leading to slow heating speed.
3. Large Temperature Fluctuations
Issue
Large temperature fluctuations during heating lead to unstable forming temperatures, affecting product quality and consistency.
Causes
·Unstable Temperature Control System: The control system algorithm is imperfect and cannot achieve precise temperature control.
·Low-Precision Temperature Sensors: The temperature sensors are not precise enough, leading to inaccurate temperature measurements.
·Heater Power Fluctuations**: Unstable power supply voltage to the heaters causes power fluctuations.
·Environmental Temperature Changes: Significant changes in the external environment temperature affect the stability of the heating zone temperature.
III. Solutions and Optimization Measures
To address the aforementioned heating issues, several measures can be taken to solve and optimize them, thereby improving the heating efficiency and stability of thermoforming multi-station machines.
1. Optimize Heater Arrangement
Arrange the positions and numbers of heaters reasonably to ensure uniform heat distribution in the heating zone. For large-area heating zones, multiple groups of heaters can be used for zoned heating to avoid localized overheating or underheating.
2. Increase Heater Power
Select heaters with suitable power based on the characteristics and heating requirements of the plastic sheets. For applications requiring fast heating speed, high-power heaters can be used to shorten the heating time.
3. Use Advanced Temperature Control Systems
Employ temperature control systems with PID control algorithms to achieve precise temperature control. Regularly calibrate temperature sensors to ensure accurate temperature measurements. For scenarios with large temperature fluctuations, increase the number of temperature sensors to improve monitoring precision and response speed.
4. Maintain and Service the Heating System
Regularly inspect and maintain the heating system to timely detect and resolve heater and temperature sensor faults. Replace aging heaters and temperature sensors promptly to ensure the normal operation of the heating system.
5. Improve Environmental Conditions
Improve the environmental conditions of the heating zone to avoid the influence of external temperature changes on the heating process. Insulation measures can be used to reduce the impact of environmental temperature fluctuations on the heating system, maintaining temperature stability in the heating zone.
6. Use Efficient Heating Technologies
Adopt efficient heating technologies such as infrared heating to improve heating efficiency and uniformity. Infrared heating features fast heating speed and low energy consumption, making it suitable for optimizing the heating systems of thermoforming multi-station machines.
Causes
·Unstable Temperature Control System: The control system algorithm is imperfect and cannot achieve precise temperature control.
·Low-Precision Temperature Sensors: The temperature sensors are not precise enough, leading to inaccurate temperature measurements.
·Heater Power Fluctuations: Unstable power supply voltage to the heaters causes power fluctuations.
·Environmental Temperature Changes: Significant changes in the external environment temperature affect the stability of the heating zone temperature.
IV. Case Studies
Analyzing specific case studies provides a more intuitive understanding of heating problem solutions and their effects. Here are two typical case studies:
Case Study 1: Heating System Optimization in a Plastic Packaging Company
الخلفية
A plastic packaging company encountered issues of uneven heating and slow heating speed while using thermoforming multi-station machines to produce plastic cup lids, resulting in low yield and low production efficiency.
Problem Analysis
Analysis revealed that the company’s thermoforming machine had improperly arranged heaters, insufficient heater power, and a slow-response temperature control system, leading to uneven heating and slow heating speed.
Solutions
·Optimize Heater Arrangement: Rearrange the positions and numbers of heaters, using multiple groups of heaters for zoned heating to ensure uniform heat distribution.
·Increase Heater Power: Replace with high-power heaters to improve heating speed and shorten heating time.
·Upgrade Temperature Control System**: Implement a temperature control system with PID control algorithms to enhance temperature control precision and response speed.
·Regular Maintenance and Service**: Establish a regular maintenance and servicing system to promptly inspect and replace aging heaters and temperature sensors.
النتائج
These measures effectively resolved the heating issues, significantly improving the yield and increasing production efficiency by over 30%.
Case Study 2: Heating System Improvement in an Automotive Parts Factory
الخلفية
An automotive parts factory faced issues of large temperature fluctuations and frequent heater malfunctions during the production of automotive interior parts, affecting product quality and production continuity.
Problem Analysis
Analysis revealed that the factory’s thermoforming machine had low-precision temperature sensors, unstable heater power supply voltage, and significant environmental temperature changes, leading to large temperature fluctuations and frequent heater malfunctions.
Solutions
·Upgrade Temperature Sensors**: Replace with high-precision temperature sensors to improve the accuracy of temperature measurements.
·Stabilize Power Supply Voltage: Use a stabilized power supply to ensure stable heater power supply voltage and reduce power fluctuations.
·Improve Environmental Conditions: Implement insulation measures to reduce the impact of external temperature changes on the heating zone, maintaining temperature stability.
·Regular Maintenance**: Establish a regular maintenance and inspection system to timely detect and resolve heater faults.
النتائج
These measures effectively resolved the heating issues, significantly improving product quality and ensuring production continuity.
الخاتمة
The performance and stability of the heating system in thermoforming multi-station machines are crucial factors affecting production efficiency and product quality. By optimizing heater arrangement, increasing heater power, using advanced temperature control systems, maintaining and servicing the heating system regularly, improving environmental conditions, and using efficient heating technologies, common heating issues can be effectively resolved. Case studies also demonstrate that these measures can significantly improve production efficiency and product quality, bringing considerable economic benefits to enterprises.
With continuous technological innovation and optimization, the heating systems of thermoforming multi-station machines will become more efficient and stable, providing strong support for the development of the plastics processing industry. It is hoped that the discussion and analysis in this article can provide useful references and guidance for industry professionals, promoting the further development and application of thermoforming technology.