تعد صيانة ماكينة التشكيل الحراري ضرورية لضمان الكفاءة والأداء الأمثل على المدى الطويل. في حين أن المكونات الشائعة مثل عناصر التسخين وأنظمة التفريغ غالبًا ما تحظى بأكبر قدر من الاهتمام، فإن الأجزاء الرئيسية الأخرى تحتاج أيضًا إلى عناية منتظمة لمنع الأعطال والحفاظ على جودة المنتج. يغطي هذا الدليل أهم المكونات، ويقدم نصائح الصيانة لمساعدتك على إطالة عمر الماكينة وتقليل وقت التوقف عن العمل.
صيانة المحركات المؤازرة وأنظمة الدفع
تعتبر المحركات المؤازرة وأنظمة الدفع ضرورية للتحكم الدقيق والتشغيل الفعال لماكينات التشكيل الحراري. إن العناية المناسبة بهذه المكونات هي المفتاح لمنع حدوث مشكلات في الأداء.
1.التنظيف والفحص المنتظم للمحرك من الخارج
يمكن أن يؤدي تراكم الغبار والأوساخ إلى انسداد فتحات التبريد ويؤدي إلى ارتفاع درجة حرارة المحرك. نظّف المحرك بانتظام بالهواء المضغوط لإزالة الغبار من الفتحات. امسح السطح الخارجي بقطعة قماش ناعمة، باستخدام محلول تنظيف خفيف للبقع الصعبة - احرص على عدم السماح للسائل بدخول المحرك.
2.فحص التوصيلات الكهربائية والأسلاك
قد تتسبب التوصيلات المفكوكة أو التالفة في حدوث اضطرابات في تشغيل المحرك. افحص الكابلات والموصلات للتأكد من عدم وجود تآكل أو تلف، واختبر ثبات الجهد باستخدام مقياس متعدد لضمان ثبات مستويات الجهد.
3.تشحيم الأجزاء المتحركة وفحص المحامل
تحتوي المحركات المؤازرة على مكونات متحركة تحتاج إلى تشحيم مناسب لتقليل الاحتكاك. افحص التشحيم وجدده كل ثلاثة أشهر، وافحص محامل المحرك بحثًا عن أي تآكل أو ضوضاء. قم بتدوير عمود المحرك يدويًا لضمان سلاسة الحركة.
4.معايرة نظام المؤازرة بانتظام
تعد معايرة المؤازرة أمرًا بالغ الأهمية للحفاظ على الدقة وجودة المنتج المتسقة. قم بإجراء المعايرة كل ستة أشهر باتباع تعليمات الشركة المصنعة وضبط معلمات المؤازرة حسب الضرورة.
5.مراقبة درجة الحرارة ومستويات الاهتزازات
قد تشير الحرارة أو الاهتزازات المفرطة إلى وجود مشاكل ميكانيكية. تتبع درجة حرارة المحرك وتأكد من أن نظام التبريد يعمل بشكل جيد. استخدم محلل الاهتزازات لاكتشاف أي اهتزازات غير طبيعية قد تشير إلى وجود خلل في المحاذاة أو مكونات مهترئة.
6.الحفاظ على تحديث البرامج وتحسين أداء النظام
يمكن أن تؤدي تحديثات البرامج المنتظمة وتحسين النظام إلى تحسين أداء المحرك بشكل كبير. تحقق من وجود تحديثات على موقع الشركة المصنعة على الويب وقم بتثبيتها حسب توفرها. بالإضافة إلى ذلك، قم بتحسين معلمات المؤازرة من خلال أدوات البرامج لتحسين استجابة المحرك.
7.إجراء اختبار الحمل المنتظم
محاكاة أحمال الإنتاج الحقيقية لتحديد المشكلات المحتملة قبل أن تتسبب في حدوث أعطال. استخدم اختبار الأحمال للتحقق من دقة المحرك أثناء دورات الإنتاج ومعالجة أي تناقضات على الفور.
صيانة آلية تشبيك القالب
تُعد آلية تثبيت القالب ضرورية للقولبة الدقيقة، حيث إنها تثبت القالب أثناء التسخين والتشكيل والتبريد. وتساعد الصيانة الدورية على منع تلف القالب وتضمن جودة المنتج الثابتة.
1.الفحص المنتظم لآلية التشبيك
تساعد عمليات الفحص الروتينية في تحديد المشكلات مبكرًا. افحص مكونات التشبيك (المشابك وقضبان التوجيه ودعامات القوالب) بحثًا عن وجود تآكل أو تلف أو اختلال في المحاذاة. ابحث أيضًا عن أي تسريبات في الوصلات الهيدروليكية أو الهوائية.
2.تشحيم الأجزاء المتحركة
تتطلب الأجزاء المتحركة في آلية التشبيك تشحيمًا منتظمًا لتقليل الاحتكاك ومنع التآكل. ضع مواد التشحيم الموصى بها على الأجزاء المتحركة كل ثلاثة إلى ستة أشهر. استخدم دائمًا مواد تشحيم عالية الجودة متوافقة مع النظام.
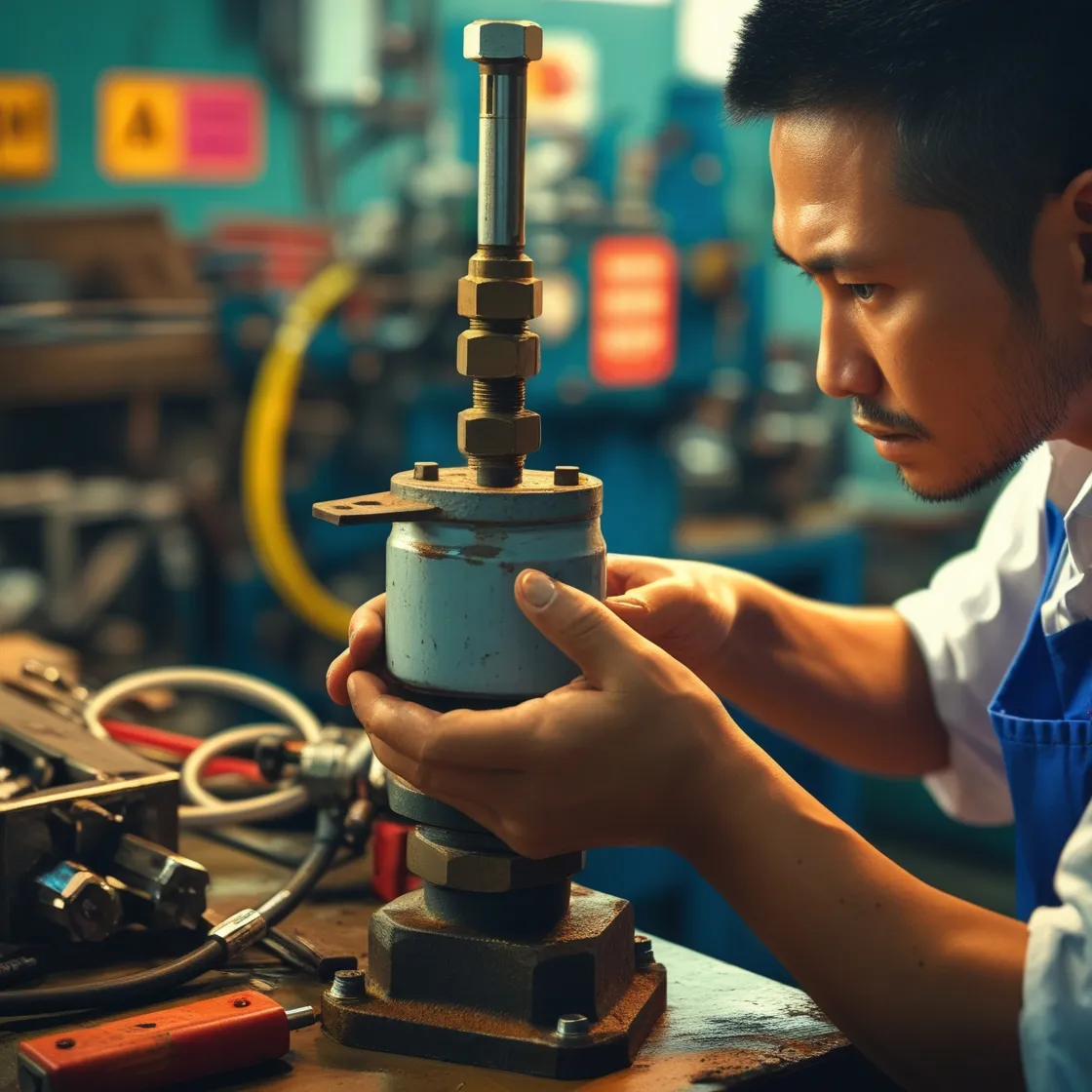
3.فحص الأنظمة الهيدروليكية والهوائية
الأنظمة الهيدروليكية والهوائية ضرورية لتطبيق قوة التشبيك الصحيحة. تأكد من أن مستويات السوائل الهيدروليكية ضمن النطاق الموصى به وأن الخراطيم خالية من التآكل أو التسريبات. قم بتنظيف المرشحات والصمامات بانتظام للحفاظ على كفاءة النظام.
4.افحص قوة التشبيك واضبطها إذا لزم الأمر
لضمان ثبات جودة المنتج، تحقق من قوة التشبيك بانتظام. استخدم مقياس الضغط لمراقبة القوة وضبط الإعدادات حسب الحاجة للحفاظ على الضغط الأمثل.
5.التحقق من محاذاة القالب وموضعه
المحاذاة الدقيقة للقالب ضرورية من أجل صب متناسق. افحص محاذاة القالب قبل وبعد كل دورة إنتاج، وتحقق من آلية قفل القالب للتأكد من أنها آمنة.
6.تنظيف وفحص ألواح التثبيت وفحصها
يساعد تنظيف ألواح التثبيت بعد كل دورة على منع تلف العفن. استخدم فرشاة ناعمة ومنظف غير كاشط لإزالة الحطام وفحص الألواح بحثًا عن أي علامات تشوه أو تشقق.
7.إجراء الصيانة الوقائية لأجهزة الاستشعار وأنظمة التحكم
تنظم المستشعرات وأنظمة التحكم قوة التشبيك ومحاذاة القالب. اختبر دقة أجهزة الاستشعار بانتظام، وحافظ على تحديث برنامج التحكم لتحسين الأداء.
صيانة أجهزة تنظيم الضغط والضواغط وصيانة الضواغط
تعتبر منظمات الضغط والضواغط ضرورية للحفاظ على ضغط هواء ثابت طوال عملية التشكيل. تضمن الصيانة السليمة التشغيل السلس وتمنع إهدار الطاقة.
1.فحص منظّمات الضغط وتنظيفها بانتظام
يمكن أن يؤثر الغبار والحطام على أداء منظمات الضغط. افحص المنظم بحثًا عن وجود تلف أو تسربات أو أصوات غير معتادة، ونظف المكونات الداخلية بالهواء المضغوط أو بقطعة قماش ناعمة.

2.مراقبة أداء الضاغط
توفر الضواغط الهواء اللازم للقولبة، وصيانتها أمر بالغ الأهمية لتحقيق الكفاءة. افحص مستويات الزيت في الضواغط المشحمة بالزيت، وافحص الأحزمة والبكرات للتأكد من عدم تآكلها. استبدل الزيت بانتظام بناءً على توصيات الشركة المصنعة.
3.تصريف الرطوبة من خزانات الهواء
يمكن أن يؤدي تراكم الرطوبة في خزانات الهواء إلى التآكل وانخفاض كفاءة الضاغط. قم بتفريغ خزان الهواء يوميًا، خاصة في البيئات الرطبة، وفكر في إضافة فاصل رطوبة لتقليل بخار الماء الداخل إلى نظام الهواء.
4.استبدل فلاتر الهواء بانتظام
تقلل فلاتر الهواء المسدودة من تدفق الهواء، مما يجعل الضاغط يعمل بجهد أكبر. افحص المرشحات شهريًا بحثًا عن أي انسدادات واستبدلها وفقًا لإرشادات الشركة المصنعة.
5.فحص التسريبات في نظام الهواء
يمكن أن تؤدي التسريبات إلى فقدان الضغط وعدم اتساق القوالب. قم بإجراء اختبارات التسرب باستخدام الماء والصابون أو أجهزة الكشف بالموجات فوق الصوتية، وقم بإصلاح أي تسربات على الفور لتجنب فقدان الطاقة.
6.معايرة مقاييس الضغط
تعد قراءات الضغط الدقيقة ضرورية للحفاظ على ثبات ضغط التشكيل. اختبر مقاييس الضغط بشكل دوري، وقارن قراءاتها بمعيار معايرة. احتفظ بالمقاييس بعيدًا عن درجات الحرارة الشديدة والاهتزازات لتجنب عدم الدقة.
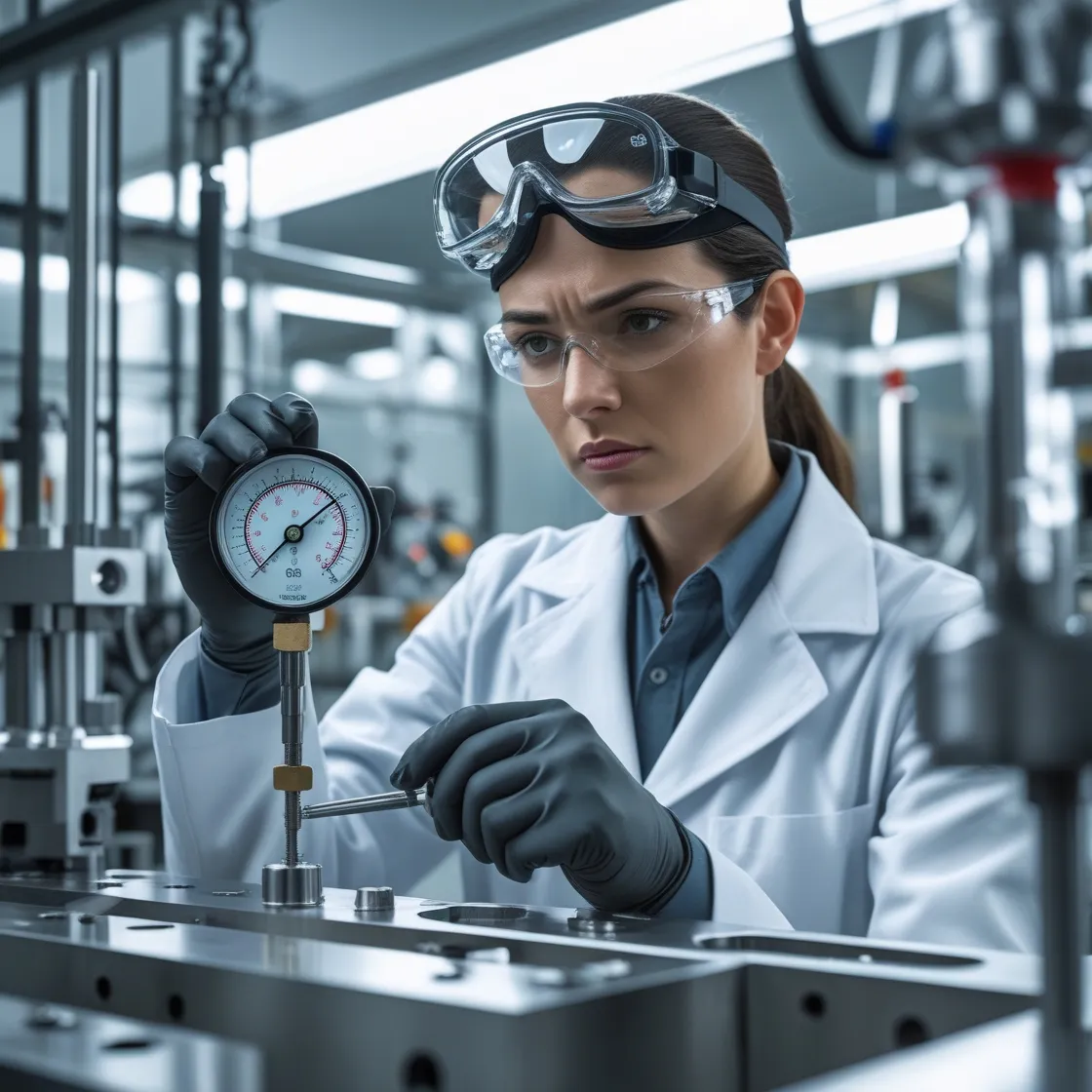
7.تشحيم مكونات الضاغط
يقلل التشحيم المناسب من الاحتكاك ويطيل عمر مكونات الضاغط. اتبع جدول التشحيم الموصى به من الشركة المصنعة، وتأكد من استخدام مادة التشحيم الصحيحة للنظام.
8.ضمان التهوية المناسبة
تولد الضواغط حرارة، لذا فهي تحتاج إلى تهوية كافية. قم بتركيب الضواغط في مناطق جيدة التهوية، وحافظ على نظافة زعانف التبريد الخاصة بها لضمان كفاءة تبديد الحرارة.
9.إجراء فحوصات الصيانة الوقائية
يمكن أن تساعد عمليات الفحص المجدولة في تحديد المشاكل المحتملة قبل أن تصبح مشاكل كبيرة. قم بإجراء فحص كامل للضاغط ومكوناته كل ثلاثة إلى ستة أشهر. احتفظ بسجلات صيانة مفصلة لتتبع الأداء ومعالجة المشاكل المتكررة.
الخاتمة
من خلال اتباع إرشادات الصيانة هذه، يمكنك تعزيز كفاءة ماكينة التشكيل الحراري لديك وموثوقيتها وعمرها الافتراضي. ستساعد عمليات الفحص والتنظيف والمعايرة المنتظمة على منع الأعطال غير المتوقعة وضمان استمرار عملية الإنتاج بسلاسة وفعالية من حيث التكلفة.