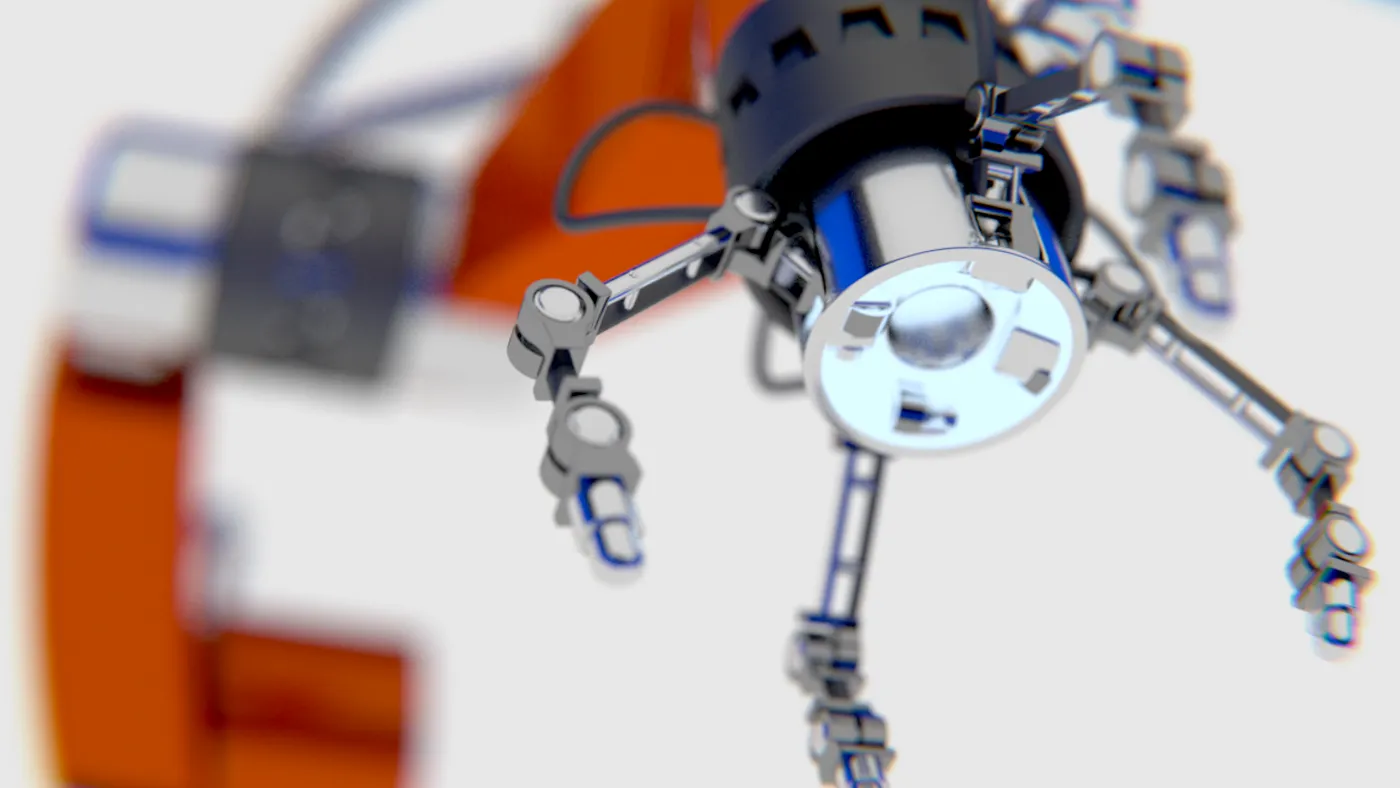
Integrating Robotic Arms with Thermoforming Machines for Increased Efficiency
مقدمة
In today’s competitive manufacturing environment, efficiency and precision are paramount. One of the most transformative advancements in the field is the integration of robotic arms with thermoforming machines. This combination not only enhances productivity but also ensures higher quality and consistency in the production of plastic components. This article delves into the benefits, technical considerations, and real-life applications of integrating robotic arms with thermoforming machines, highlighting specific case studies to illustrate the tangible advantages of this technology.
Benefits of Integrating Robotic Arms with Thermoforming Machines
Enhanced Productivity
Robotic arms significantly increase the speed and efficiency of the thermoforming process. By automating repetitive tasks such as loading and unloading materials, trimming, and stacking, robotic arms reduce cycle times and minimize downtime. This leads to higher throughput and allows manufacturers to meet tight production deadlines.
Improved Precision and Consistency
Robotic arms offer unparalleled precision, which is crucial for maintaining the quality and consistency of thermoformed products. They can execute complex movements with high accuracy, ensuring that each component is formed and trimmed to exact specifications. This level of precision reduces the likelihood of defects and enhances the overall quality of the final products.
Labor Cost Savings
Automation through robotic arms can lead to significant labor cost savings. By handling tasks that are typically labor-intensive, robots free up human workers to focus on more complex and value-added activities. This not only reduces labor costs but also improves overall operational efficiency.
Enhanced Safety
Integrating robotic arms with thermoforming machines enhances workplace safety by reducing the need for human operators to engage in potentially hazardous tasks. Robots can handle hot materials and sharp tools with ease, minimizing the risk of workplace injuries and ensuring a safer working environment.
Flexibility and Scalability
Robotic arms are highly flexible and can be easily programmed to perform a variety of tasks. This makes it easier for manufacturers to adapt to changing production needs and scale their operations. Whether producing small batches of custom components or large volumes of standard products, robotic arms can be configured to meet specific requirements.
Technical Considerations for Integration
التوافق
One of the first considerations when integrating robotic arms with thermoforming machines is ensuring compatibility between the two systems. The robotic arm must be able to interface seamlessly with the thermoforming machine’s control system. This often involves using standardized communication protocols and ensuring that both systems can be synchronized for optimal performance.
Payload Capacity
The payload capacity of the robotic arm must be sufficient to handle the weight of the materials and components being processed. This includes not only the plastic sheets being formed but also any additional tools or fixtures that the robot may need to carry. Choosing a robotic arm with the appropriate payload capacity is crucial for maintaining efficiency and avoiding mechanical strain.
Reach and Mobility
The reach and mobility of the robotic arm are also important factors. The arm must be able to access all areas of the thermoforming machine and perform the required tasks without obstruction. This may involve selecting a robotic arm with multiple axes of movement and a sufficient range of motion to cover the entire work area.
End-of-Arm Tooling
End-of-arm tooling (EOAT) refers to the devices attached to the end of the robotic arm that enable it to interact with objects. Common types of EOAT used in thermoforming applications include grippers, suction cups, and cutting tools. Selecting the right EOAT is essential for ensuring that the robot can perform tasks such as picking up sheets, trimming excess material, and stacking finished components efficiently.
Programming and Integration
Programming the robotic arm to perform specific tasks involves creating detailed instructions and sequences. This requires a thorough understanding of both the robotic arm and the thermoforming machine’s operation. Advanced software tools can simplify this process by providing graphical interfaces and simulation capabilities, allowing engineers to design and test programs before deploying them on the factory floor.
دراسات حالة واقعية
Case Study 1: Automating Sheet Loading and Unloading
الشركة: Plastiform Technologies
الصناعة: Packaging
التحدّي: Plastiform Technologies, a leading manufacturer of plastic packaging, faced challenges in meeting increasing demand due to labor shortages and high turnover rates in their manual sheet loading and unloading process. The company needed a solution to improve efficiency and reduce reliance on manual labor.
الحل: Plastiform Technologies integrated a robotic arm with their thermoforming machine to automate the sheet loading and unloading process. The robotic arm was equipped with a custom EOAT featuring suction cups designed to handle the plastic sheets without causing damage.
التنفيذ: The integration process involved retrofitting the existing thermoforming machine with sensors and communication interfaces to synchronize with the robotic arm. Engineers programmed the robot to pick up plastic sheets from a stack, place them onto the thermoforming machine, and remove the formed components once the process was complete.
النتيجة: The integration led to a 30% increase in production throughput and a significant reduction in labor costs. The automated system operated continuously, minimizing downtime and allowing the company to meet increased demand without the need for additional workforce. The improved efficiency and consistency in the sheet handling process also resulted in higher product quality and reduced scrap rates.
Case Study 2: Precision Trimming and Stacking
الشركة: AutoParts Plastics
الصناعة: السيارات
التحدّي: AutoParts Plastics, a manufacturer of automotive interior components, needed to enhance the precision and consistency of their trimming process. Manual trimming was prone to errors, leading to inconsistent product quality and increased rework.
الحل: AutoParts Plastics integrated a robotic arm with their thermoforming machine to automate the trimming and stacking process. The robotic arm was equipped with a specialized EOAT featuring a cutting tool for precise trimming and a gripper for stacking the finished components.
التنفيذ: Engineers programmed the robotic arm to follow a precise trimming path based on CAD models of the components. The robotic arm trimmed the excess material from each formed part and stacked the finished components in organized batches. The system was configured to adjust the trimming path automatically based on variations in the formed parts.
النتيجة: The integration resulted in a 25% reduction in cycle times and a significant improvement in product quality. The robotic arm’s precision trimming ensured consistent dimensions and reduced the need for rework. The automated stacking process also streamlined downstream operations, enhancing overall production efficiency. The company reported a return on investment (ROI) within 18 months of implementing the robotic system.
Case Study 3: High-Volume Production of Medical Trays
الشركة: MedPlast Solutions
الصناعة: Medical Device Manufacturing
التحدّي: MedPlast Solutions, a producer of medical trays, faced challenges in maintaining high production volumes while ensuring stringent quality standards. The manual handling process was time-consuming and prone to contamination risks.
الحل: MedPlast Solutions integrated a robotic arm with their thermoforming machine to automate the handling and packaging of medical trays. The robotic arm was equipped with a gripper designed to handle sterile trays without compromising cleanliness.
التنفيذ: The robotic arm was programmed to remove the formed medical trays from the thermoforming machine and place them directly into sterile packaging. The system was integrated with a vision system to inspect each tray for defects before packaging, ensuring only high-quality products were shipped.
النتيجة: The integration led to a 40% increase in production efficiency and a significant reduction in contamination risks. The automated handling process maintained a sterile environment, enhancing product safety and quality. The vision system’s defect detection capabilities further improved quality control, resulting in fewer customer complaints and returns. MedPlast Solutions successfully met their high-volume production targets while maintaining the highest standards of quality.
الخاتمة
The integration of robotic arms with thermoforming machines represents a significant advancement in manufacturing technology, offering numerous benefits such as enhanced productivity, improved precision, labor cost savings, and increased safety. By automating tasks such as loading, unloading, trimming, and stacking, manufacturers can achieve higher throughput, consistent product quality, and reduced operational costs.
The real-life case studies of Plastiform Technologies, AutoParts Plastics, and MedPlast Solutions demonstrate the tangible advantages of integrating robotic arms with thermoforming machines. These companies successfully addressed their production challenges and achieved significant improvements in efficiency, quality, and overall performance.
As the manufacturing industry continues to evolve, the integration of robotic arms with thermoforming machines will play an increasingly important role in driving innovation and competitiveness. By embracing this technology, manufacturers can stay ahead of the curve and meet the growing demands of their customers while maintaining the highest standards of quality and efficiency.