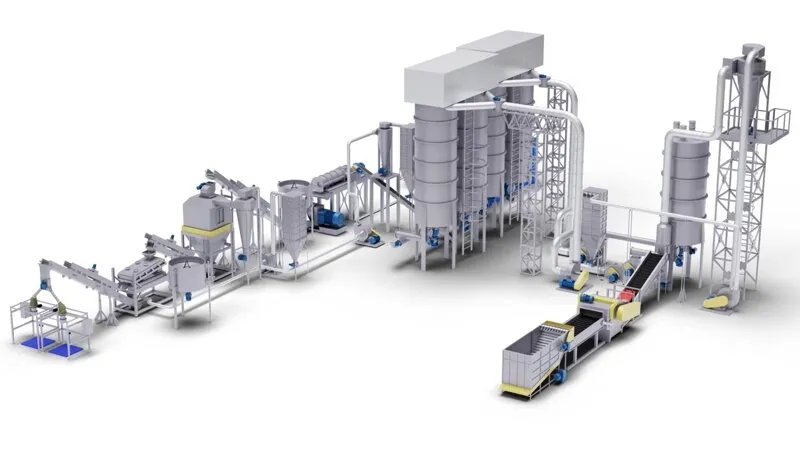
الاستفادة من ماكينات التشكيل الحراري للتصنيع المخصص والدفعات الصغيرة
In the ever-evolving landscape of manufacturing, the ability to adapt to changing market demands and produce custom or small batch products efficiently is becoming increasingly important. Thermoforming machines, with their versatility and flexibility, offer a compelling solution for businesses looking to meet the growing demand for customized and low-volume production. In this article, we will explore how thermoforming machines can be leveraged for custom and small batch manufacturing, supported by specific case studies to illustrate real-world applications and benefits.
Introduction to Thermoforming Machines in Custom Manufacturing
Thermoforming is a manufacturing process that involves heating a thermoplastic sheet to a pliable temperature, forming it into a specific shape using a mold, and then cooling it to create a finished product. Unlike traditional manufacturing methods that often require expensive tooling and long lead times, thermoforming offers a cost-effective and efficient solution for producing custom and small batch products. With the ability to quickly change molds and adapt to different shapes and sizes, thermoforming machines enable manufacturers to meet diverse customer requirements with ease.
Benefits of Thermoforming Machines for Custom and Small Batch Manufacturing
1. Cost-effectiveness
Thermoforming eliminates the need for expensive molds and tooling typically associated with other manufacturing processes such as injection molding or CNC machining. This cost savings makes it an attractive option for producing custom or small batch products without incurring high upfront expenses.
2. Quick Setup and Changeover
Thermoforming machines feature rapid setup and changeover capabilities, allowing manufacturers to switch between different products or designs with minimal downtime. This flexibility is particularly advantageous for custom manufacturing, where frequent design changes and short production runs are common.
3. Design Freedom
Thermoforming offers virtually unlimited design freedom, allowing manufacturers to create complex shapes, textures, and features with ease. This versatility enables the production of highly customized products tailored to specific customer requirements, without compromising on design aesthetics or functionality.
4. Material Variety
Thermoforming machines can process a wide range of thermoplastic materials, including ABS, PET, PVC, and polycarbonate, among others. This versatility in material selection allows manufacturers to choose the most suitable material for each application, whether it be for its mechanical properties, appearance, or cost-effectiveness.
Case Studies: Real-world Applications of Thermoforming Machines in Custom Manufacturing
Case Study 1: Custom Packaging Solutions
الشركة: ABC Packaging Solutions
التحدّي: A client in the consumer electronics industry required custom packaging solutions for their products, each with unique shapes and dimensions. Traditional packaging methods were costly and time-consuming, making it difficult to meet the client’s requirements for customization and quick turnaround times.
الحل: ABC Packaging Solutions invested in a thermoforming machine equipped with rapid changeover capabilities and advanced design software. This allowed them to quickly create custom molds for each product variant and produce packaging trays with precise fit and protection. The flexibility of thermoforming also enabled them to accommodate design revisions and new product launches without significant lead times.
النتيجة: By leveraging thermoforming for custom packaging solutions, ABC Packaging Solutions reduced production costs by 30% and shortened lead times by 50%. They were able to meet the client’s demands for customization and small batch production, enhancing their competitiveness in the market.
Case Study 2: Personalized Medical Devices
الشركة: XYZ Medical Devices
التحدّي: XYZ Medical Devices specializes in the production of orthopedic implants and surgical instruments. They received requests from surgeons for personalized implants tailored to each patient’s anatomy, requiring precise customization and small batch production.
الحل: XYZ Medical Devices integrated thermoforming machines into their manufacturing process to produce personalized orthopedic implants and surgical guides. Using patient-specific 3D scans, they designed custom molds for each implant and fabricated them using thermoforming technology. This approach allowed them to produce implants with precise fit and alignment, improving patient outcomes and surgical efficiency.
النتيجة: By leveraging thermoforming for personalized medical devices, XYZ Medical Devices enhanced patient care and surgical outcomes. They reduced lead times for custom implants from weeks to days, enabling surgeons to perform procedures more efficiently. Additionally, the cost-effectiveness of thermoforming allowed them to offer personalized solutions at competitive prices, strengthening their position in the market.
الخاتمة
Thermoforming machines offer a compelling solution for custom and small batch manufacturing, enabling businesses to meet diverse customer requirements with cost-effective and efficient production methods. With benefits such as cost-effectiveness, quick setup and changeover, design freedom, and material variety, thermoforming machines empower manufacturers to create highly customized products tailored to specific needs.
Real-world case studies demonstrate the practical application of thermoforming technology in various industries, from custom packaging solutions to personalized medical devices. By leveraging thermoforming machines, businesses can enhance their competitiveness, meet evolving customer demands, and drive innovation in the manufacturing sector. As the demand for customization and small batch production continues to grow, thermoforming remains a valuable tool for businesses looking to stay ahead in today’s dynamic marketplace.