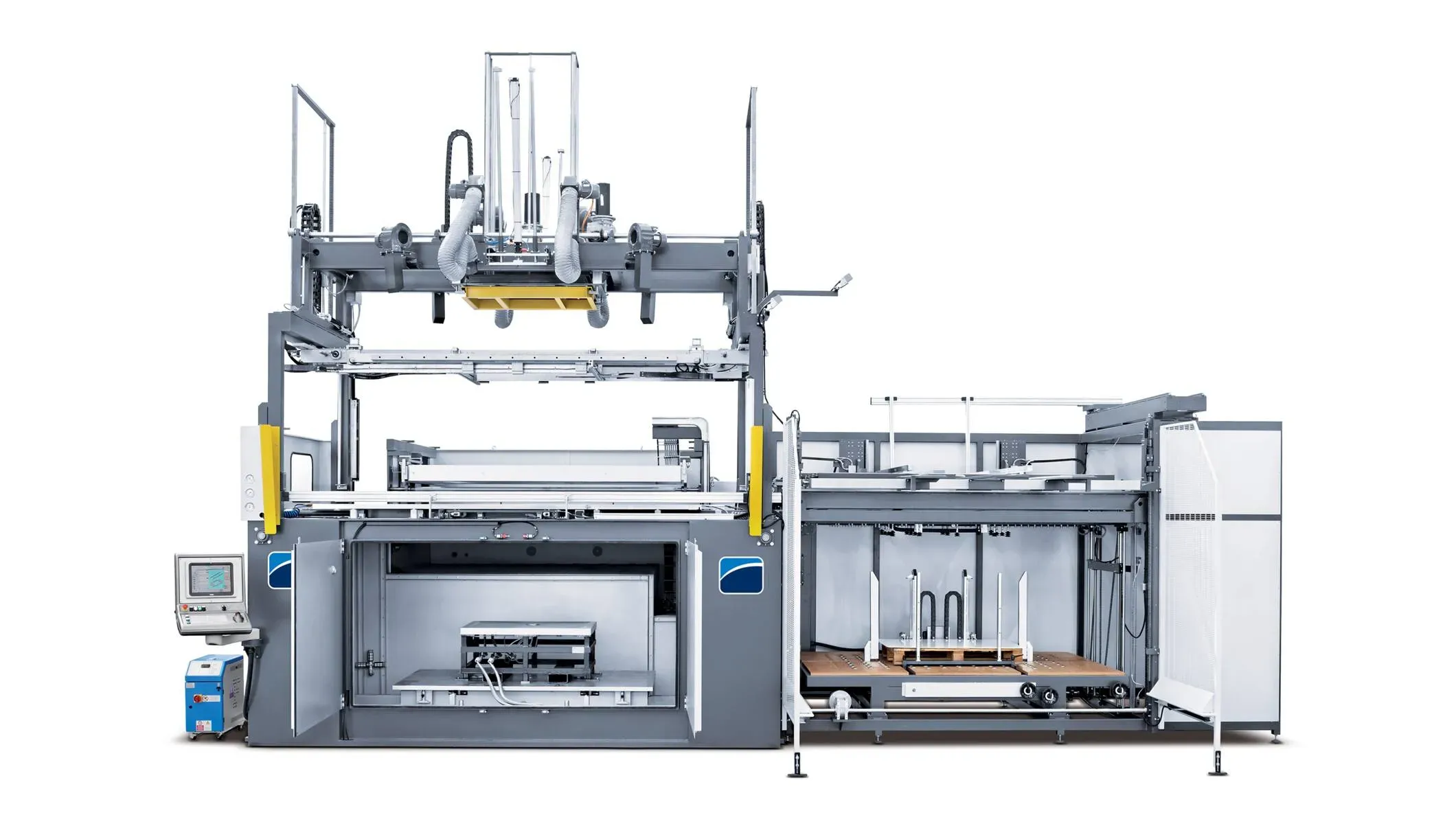
Mejora de la utilización de materiales en operaciones de termoformado
Introducción
La utilización de materiales es un factor crítico en la eficiencia y rentabilidad de las operaciones de termoformado. Maximizar el uso de materias primas no sólo reduce los residuos y el impacto medioambiental, sino que también mejora la rentabilidad y la competitividad. Este artículo explora las estrategias para mejorar la utilización de materiales en los procesos de termoformado, proporcionando información detallada y estudios de casos reales para ilustrar su aplicación efectiva.
Comprender la utilización de materiales en el termoformado
La utilización de material en el termoformado se refiere a la relación entre la cantidad real de material utilizado en el producto final y la cantidad total de material cargado inicialmente en la máquina. Una alta utilización del material significa que un mayor porcentaje del material de entrada se convierte en productos acabados, lo que minimiza los residuos y reduce los costes. Los factores clave que influyen en la utilización del material son el grosor de la chapa, los patrones de corte, el diseño del molde y los parámetros del proceso.
Estrategias para mejorar la utilización del material
1. Optimización del grosor de la chapa
Una de las formas más directas de mejorar la utilización del material es optimizar el grosor de las láminas de plástico utilizadas en el termoformado. Utilizar el grosor mínimo necesario para cumplir las especificaciones del producto puede reducir significativamente el consumo de material.
Implantación:
- Realice un análisis exhaustivo de los requisitos del producto para determinar el grosor óptimo de la chapa.
- Utilice el software de análisis de elementos finitos (FEA) para simular el rendimiento del producto e identificar las áreas en las que puede reducirse el grosor del material sin comprometer la calidad.
- Aplicar medidas de control de calidad para garantizar un grosor constante de la chapa durante la producción.
Caso práctico: Reducción del grosor de las láminas en PackRight
Empresa: PackRight
Industria: Embalaje
Desafío: PackRight pretendía reducir los costes de material optimizando el grosor de sus productos de envasado termoformado.
Solución: La empresa realizó un estudio de elementos finitos para determinar el grosor mínimo necesario para sus productos manteniendo la integridad estructural. A continuación, implantaron nuevos procesos de control de calidad para garantizar un grosor uniforme de las chapas.
Resultado: PackRight consiguió una reducción de 15% en el uso de material, lo que supuso un importante ahorro de costes y una mejor utilización del material. La calidad de los productos finales siguió siendo alta, sin comprometer el rendimiento.
2. Técnicas avanzadas de corte y recorte
La eficacia de los procesos de corte y recorte puede mejorar significativamente la utilización del material al minimizar los desechos y maximizar el uso de la lámina de plástico.
Implantación:
- Invierta en equipos de corte y recorte de alta precisión para reducir el desperdicio de material.
- Utilice el software de anidamiento para optimizar los patrones de corte y maximizar el número de piezas producidas a partir de cada chapa.
- Implantar sistemas automatizados de recorte para garantizar cortes uniformes y precisos.
Estudio de caso: Software de anidado en AutoTrim
Empresa: AutoTrim
Industria: Automoción
Desafío: AutoTrim se enfrentaba a un elevado desperdicio de material debido a patrones de corte ineficaces en su proceso de termoformado.
Solución: La empresa adoptó un avanzado software de anidado para optimizar los diseños de corte y minimizar los desechos. También invirtió en equipos de recorte de alta precisión para mejorar la exactitud del corte.
Resultado: AutoTrim redujo el desperdicio de material en 20%, mejorando significativamente la utilización del material. Los patrones de corte optimizados permitieron producir más piezas a partir de cada chapa, mejorando la productividad global.
3. Mejora del diseño de moldes
Un diseño eficiente del molde puede reducir el desperdicio de material al garantizar una distribución uniforme del mismo y minimizar el uso de material sobrante.
Implantación:
- Diseñe moldes con un grosor de pared uniforme para reducir el desperdicio de material.
- Utilice moldes de cavidades múltiples para producir varias piezas simultáneamente, mejorando la eficiencia del material.
- Aplicar el análisis de flujo de moldes para identificar y abordar las áreas de posible desperdicio de material.
Caso práctico: Espesor de pared uniforme en MedForm
Empresa: MedForm
Industria: Productos sanitarios
Desafío: MedForm experimentó un desperdicio de material debido a la falta de uniformidad en el grosor de las paredes de sus componentes de dispositivos médicos termoformados.
Solución: La empresa rediseñó sus moldes para garantizar un grosor uniforme de las paredes y realizó análisis de flujo de moldes para optimizar la distribución del material.
Resultado: MedForm redujo el desperdicio de material en 25%, mejorando la utilización del material y reduciendo los costes de producción. Los moldes rediseñados también mejoraron la calidad y consistencia del producto.
4. Optimización de los parámetros del proceso
La optimización de los parámetros del proceso, como la temperatura, la presión y la duración del ciclo, puede mejorar el aprovechamiento del material al aumentar la eficacia del conformado y reducir los defectos.
Implantación:
- Utilice sistemas de supervisión en tiempo real para controlar y ajustar los parámetros del proceso para obtener un rendimiento óptimo.
- Aplicar el control estadístico de procesos (CEP) para identificar y eliminar las variaciones del proceso.
- Realizar el mantenimiento y la calibración periódicos de los equipos para garantizar un funcionamiento constante.
Caso práctico: Supervisión en tiempo real en CleanPack
Empresa: CleanPack
Industria: Envasado de bienes de consumo
Desafío: CleanPack se enfrentaba a un aprovechamiento irregular del material debido a variaciones en los parámetros del proceso durante el termoformado.
Solución: La empresa implantó sistemas de supervisión en tiempo real para controlar los parámetros clave del proceso y realizar los ajustes necesarios. También utilizaron el SPC para identificar y abordar las variaciones del proceso.
Resultado: CleanPack mejoró la utilización del material en 18%, reduciendo los residuos y mejorando la consistencia del producto. El sistema de supervisión en tiempo real permitió realizar ajustes inmediatos, garantizando un rendimiento óptimo del proceso.
5. Reciclaje y reutilización de material de desecho
El reciclaje y la reutilización del material de desecho pueden mejorar aún más la utilización de los materiales al reducir la necesidad de nuevas materias primas.
Implantación:
- Implantar un sistema interno de reciclaje para procesar y reutilizar la chatarra.
- Utilizar material rectificado en piezas no críticas para reducir el consumo de materiales vírgenes.
- Trabajar con los proveedores para desarrollar programas de reciclaje de circuito cerrado para las láminas de plástico.
Estudio de caso: Reciclaje interno en EcoTherm
Empresa: EcoTherm
Industria: Envases sostenibles
Desafío: EcoTherm se propuso reducir su impacto ambiental reciclando y reutilizando material de desecho en su proceso de termoformado.
Solución: La empresa invirtió en un sistema de reciclaje interno para procesar el material de desecho y reintroducirlo en la producción. También trabajó con proveedores para desarrollar un programa de reciclaje de circuito cerrado para sus láminas de plástico.
Resultado: EcoTherm redujo su dependencia de materiales vírgenes en 30%, mejorando significativamente la utilización de materiales. Las iniciativas de reciclaje también reforzaron los esfuerzos de sostenibilidad de la empresa y redujeron los costes generales de producción.
6. Selección de materiales
Elegir materiales más fáciles de procesar y con mejores propiedades de conformado puede mejorar la utilización del material.
Implantación:
- Seleccione materiales con alta conformabilidad y bajos índices de contracción para reducir los residuos.
- Trabajar con los proveedores de materiales para desarrollar fórmulas personalizadas que optimicen la eficacia del conformado.
- Realizar ensayos de materiales para evaluar y comparar el rendimiento de diferentes plásticos.
Caso práctico: Formulación de materiales a medida en FlexiForm
Empresa: FlexiForm
Industria: Electrónica de consumo
Desafío: FlexiForm buscaba mejorar la utilización del material seleccionando materiales con mejores propiedades de conformado para sus componentes electrónicos termoformados.
Solución: La empresa colaboró con proveedores de materiales para desarrollar fórmulas de plástico personalizadas que optimizasen la eficacia del conformado y redujesen los residuos. Realizaron ensayos exhaustivos de materiales para evaluar el rendimiento.
Resultado: FlexiForm mejoró la utilización del material en 22%, reduciendo los residuos y mejorando la calidad del producto. Las fórmulas personalizadas proporcionaron mejores propiedades de conformado, lo que dio lugar a procesos de producción más eficientes.
7. Formación de los empleados y buenas prácticas
Formar a los empleados en las mejores prácticas y técnicas eficientes de manipulación de materiales puede mejorar significativamente la utilización del material.
Implantación:
- Impartir periódicamente sesiones de formación sobre manipulación eficaz de materiales y optimización de procesos.
- Desarrollar procedimientos normalizados de trabajo (PNT) para la manipulación de materiales y el control de procesos.
- Fomentar la mejora continua y la retroalimentación de los empleados para identificar y abordar las ineficiencias.
Estudio de caso: Formación de empleados en PackTech
Empresa: PackTech
Industria: Envases industriales
Desafío: PackTech se enfrentaba a una utilización incoherente del material debido a la falta de procedimientos normalizados y de formación de los empleados.
Solución: La empresa implantó un completo programa de formación centrado en la manipulación eficaz de materiales y la optimización de procesos. También desarrollaron procedimientos normalizados de trabajo para estandarizar las mejores prácticas.
Resultado: PackTech mejoró la utilización de material en 15%, reduciendo los residuos y aumentando la eficiencia de la producción. El programa de formación capacitó a los empleados para identificar y abordar las ineficiencias, fomentando una cultura de mejora continua.
Conclusión
Mejorar la utilización del material en las operaciones de termoformado es esencial para aumentar la productividad, reducir los costes y minimizar el impacto medioambiental. Optimizando el grosor de la chapa, aplicando técnicas avanzadas de corte y recorte, mejorando el diseño de los moldes, optimizando los parámetros del proceso, reciclando y reutilizando el material de desecho, seleccionando los materiales adecuados y formando a los empleados, las empresas pueden conseguir mejoras significativas en la utilización del material.
Los estudios de casos reales de PackRight, AutoTrim, MedForm, CleanPack, EcoTherm, FlexiForm y PackTech demuestran los beneficios tangibles de estas estrategias. Cada empresa abordó con éxito sus retos específicos y logró mejoras sustanciales en la utilización de materiales, lo que se tradujo en un ahorro de costes, una mayor sostenibilidad y una mejora de la calidad del producto.
A medida que la industria manufacturera siga evolucionando, será fundamental centrarse en la utilización de los materiales para mantener la competitividad y satisfacer la creciente demanda de prácticas de producción sostenibles y rentables. Innovando y perfeccionando continuamente sus procesos, los fabricantes pueden garantizar el éxito a largo plazo y contribuir a un futuro más sostenible.