De cero a uno: diseño, desarrollo y respuesta al mercado de la termoformadora de tres estaciones
Introducción
La máquina de termoformado de tres estaciones es un equipo ampliamente utilizado en la industria manufacturera moderna, que se utiliza especialmente para procesar materiales termoplásticos en productos de formas deseadas a través del calentamiento y la formación de moldes. Con la creciente demanda de productos de plástico en la producción industrial, las máquinas de termoformado tradicionales de una sola estación ya no pueden satisfacer los requisitos de una producción eficiente. Así surgió el diseño y desarrollo de la máquina de termoformado de tres estaciones. Su nacimiento ha pasado por varias etapas clave. A continuación se presenta en detalle su proceso de desarrollo.
1. Inicio del diseño
El punto de partida del diseño de la termoformadora de tres estaciones proviene de un profundo conocimiento de la demanda del mercado y de la eficiencia de la producción. La idea original es aumentar el número de estaciones para poder realizar simultáneamente los procesos de calentamiento, conformado y enfriamiento, acortando así enormemente el ciclo de producción. El punto de partida del diseño mecánico suele partir de modelos de productos, dibujos o muestras facilitados por los clientes. En esta fase, el diseño se centra principalmente en la estructura general y el principio de funcionamiento del equipo.
El equipo de diseño tiene que estudiar cómo lograr el trabajo en colaboración de varias estaciones bajo la premisa de garantizar la estabilidad del equipo, a fin de mejorar la eficiencia global de la producción. La fase de diseño no solo implica la optimización de la estructura mecánica, sino que también requiere una investigación en profundidad de tecnologías clave como la distribución del calor y el control de la presión.
2. Selección del material
Es fundamental conocer el tipo de material de lámina que utilizará el producto. Seleccione los materiales adecuados (como la degradación del almidón, la fotodegradación, el PP, el PS, el PET, el PVC, el PLA, el CPLA, el CPET, el carbonato cálcico, el OPS y otras láminas) para garantizar que mantienen sus características inherentes durante el proceso de extrusión y evitar los inconvenientes de los frecuentes ajustes de parámetros durante el proceso de termoformado. La elección de los materiales afecta directamente a la calidad del producto final y a la estabilidad de la producción.
En el proceso de selección de materiales no sólo se tienen en cuenta sus propiedades físicas y químicas, sino que también hay que evaluar su rentabilidad y su impacto ambiental. Con las normativas medioambientales cada vez más estrictas, la selección de materiales degradables y respetuosos con el medio ambiente se ha convertido en una parte importante del proceso de diseño.
3. Preparación de la bobina
Una vez determinado el material, la bobina que se va a procesar se instala en el dispositivo de desenrollado, que suministra la cantidad adecuada de chapa con una precisión exacta. A continuación, la chapa se introduce en la termoformadora y pasa entre las placas de calentamiento superior e inferior. La temperatura se ajusta de forma independiente en función del material y el grosor para garantizar la precisión del proceso de conformado. La fase de preparación de la bobina es la base de todo el proceso de termoformado y determina el buen desarrollo de los siguientes eslabones.
Los dispositivos de desbobinado modernos suelen estar equipados con sistemas automáticos de control de la tensión para garantizar que la lámina mantenga siempre la tensión adecuada durante la transmisión, a fin de evitar los defectos de formación causados por una tensión desigual. Además, un sistema de alimentación eficiente puede mejorar significativamente el nivel de automatización de la línea de producción, reducir las operaciones manuales y mejorar la eficiencia de la producción.
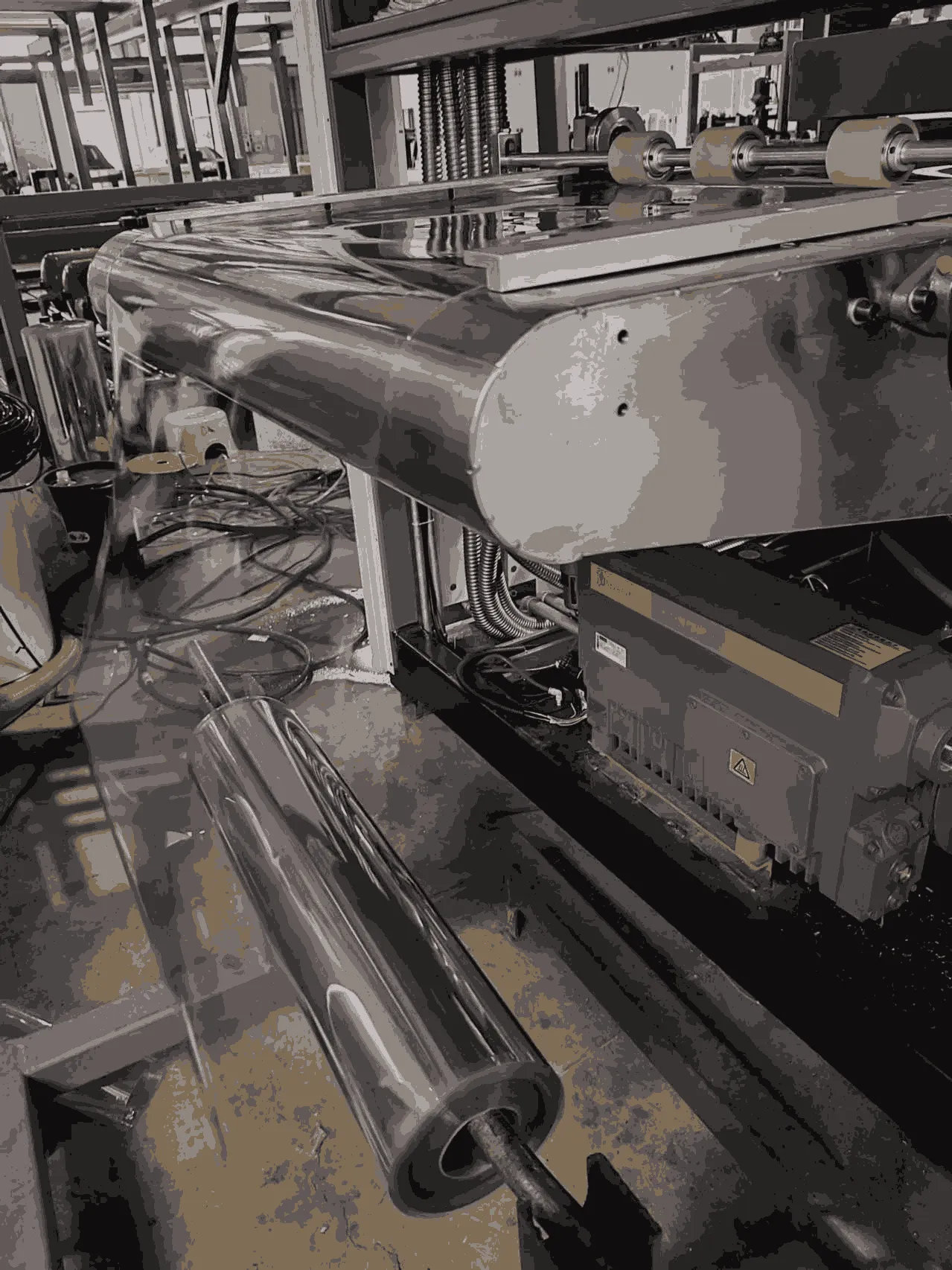
4. Personalización de moldes
Basándose en las características del producto y en la información sobre el material, diseñe cuidadosamente el número de cavidades y el tiempo de ciclo previsto del molde. El molde consta de dos mitades, que se instalan en la platina móvil de la prensa de codo vertical. El diseño y la fabricación del molde es un eslabón clave en el desarrollo de la máquina de termoformado, que está directamente relacionado con la forma, el tamaño y la calidad de la superficie del producto. Los moldes de alta precisión no sólo pueden mejorar la tasa de calificación del producto, sino también reducir el desperdicio de material y el desgaste de los equipos.
El diseño del molde no solo debe tener en cuenta la forma geométrica del producto, sino que también debe optimizar el sistema de refrigeración del molde para garantizar que el producto moldeado pueda enfriarse y moldearse rápidamente, acortando así el ciclo de producción. Las tecnologías modernas de fabricación de moldes, como la impresión 3D y el mecanizado CNC de alta precisión, han mejorado aún más la precisión de fabricación y la complejidad del molde.
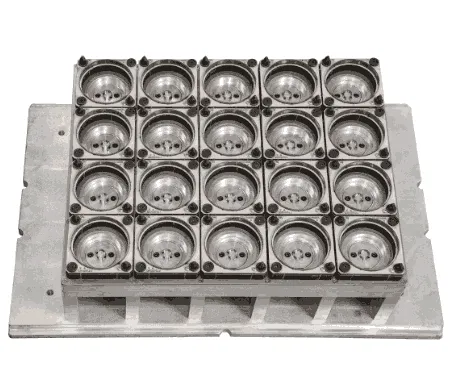
5. Moldeo de plásticos
La lámina de plástico plana se introduce en la máquina, y el elemento calefactor emite calor para hacer el plástico maleable, sentando una base clave para la etapa de moldeo. El plástico se ablanda mediante el primer calentamiento, combinado con presión de vacío o presión de aire, y el material se moldea en el molde, se retira tras enfriarse y se transporta a la siguiente estación mediante una cadena dentada. La clave técnica de la etapa de moldeo es controlar la temperatura de calentamiento y la presión de moldeo para garantizar la uniformidad y estabilidad del producto.
La temperatura y la presión de cada estación deben controlarse con precisión durante el proceso de moldeo para evitar defectos de moldeo causados por un calentamiento excesivo o un enfriamiento desigual del plástico. Los equipos de moldeo modernos suelen estar equipados con sistemas de control avanzados que pueden supervisar y ajustar los parámetros de producción en tiempo real para garantizar una calidad constante del producto.
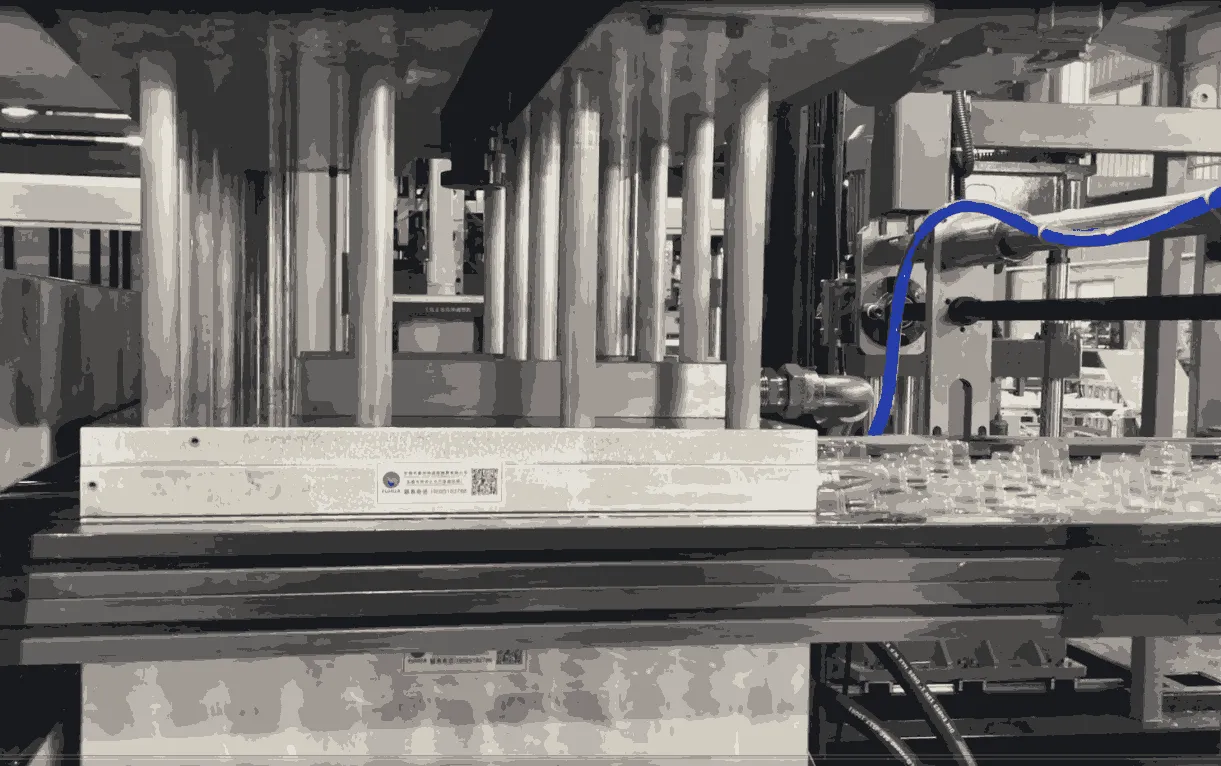
6. Corte de precisión
En la segunda estación, la placa calefactora de resistencia realiza un corte limpio para garantizar la precisión y uniformidad del tamaño del producto y cumplir estrictas normas de calidad. El producto cortado se fija a la placa y sigue pasando por la máquina hasta la estación final. La precisión del proceso de corte afecta directamente al aspecto y el rendimiento del producto final, por lo que se requieren equipos de corte de alta precisión y tecnología de control avanzada.
El proceso de corte no sólo requiere precisión y velocidad de corte, sino también el reciclaje de los residuos de corte. Optimizando la trayectoria de corte y el sistema de manipulación de residuos, se pueden reducir eficazmente los residuos de material y mejorar la protección del medio ambiente y los beneficios económicos de la producción.
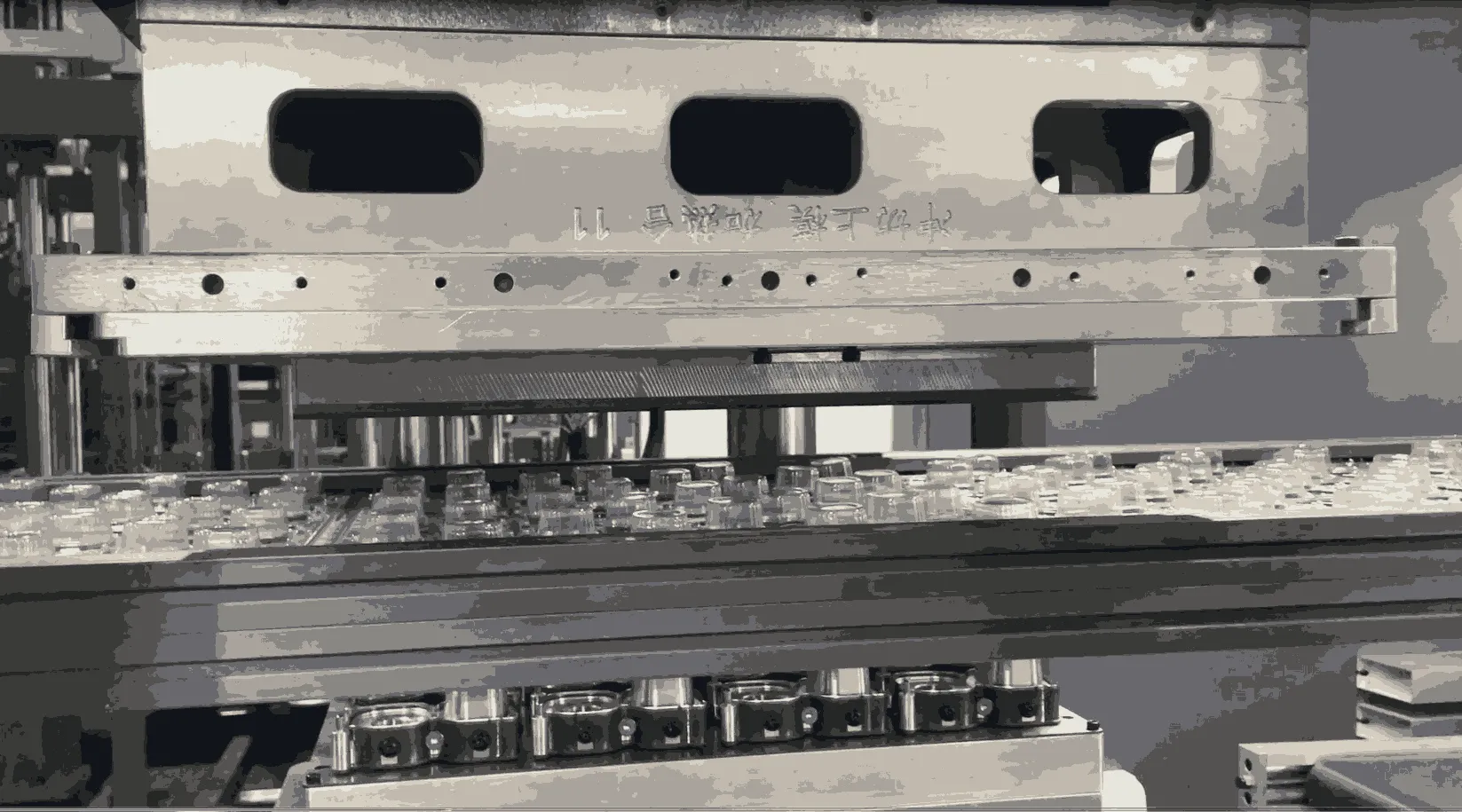
7. Apilamiento eficaz
En la tercera estación, los productos se apilan y organizan cuidadosamente para su posterior manipulación y envasado eficientes. El uso de estaciones de apilado no sólo simplifica el proceso de producción, sino que también mejora significativamente la eficiencia global de la producción. Un sistema de apilado eficaz puede reducir significativamente las operaciones manuales y mejorar el nivel de automatización de la producción, al tiempo que garantiza la consistencia y fiabilidad de cada lote de productos.
Los sistemas de apilado eficientes suelen combinar sensores inteligentes y software de control para ajustar automáticamente el método de apilado en función del tamaño y el peso del producto, garantizando una calidad de apilado uniforme para cada lote de productos. Al mismo tiempo, el sistema de apilado automático también puede conectarse perfectamente con el sistema de envasado posterior para mejorar la eficiencia de toda la línea de producción.
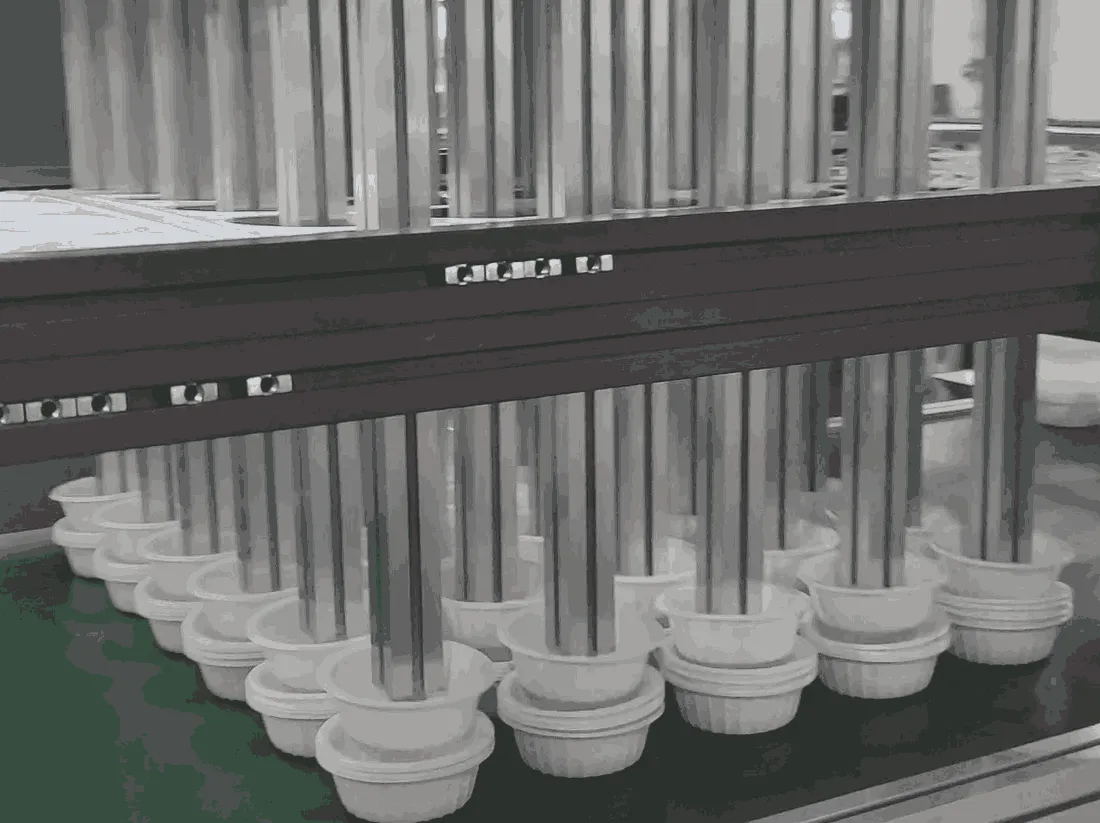
I+D tecnológica y optimización del diseño
Tras la concepción del moldeo, el equipo de I+D comenzó a abordar los problemas técnicos. El diseño de la máquina de termoformado de tres estaciones necesita resolver múltiples problemas técnicos, incluyendo:
Uniformidad de la distribución del calor: Garantice una distribución uniforme del calor en cada estación para evitar defectos en el producto durante el proceso de moldeo. La distribución uniforme del calor puede lograrse mediante una avanzada tecnología de control del calentamiento y un diseño optimizado del calentador.
Precisión del molde: Mejorar la precisión de fabricación del molde para garantizar la calidad del producto moldeado. La tecnología de procesamiento CNC de alta precisión y el estricto proceso de control de calidad son la clave para conseguir moldes de alta precisión.
Control de automatización: Introducir sistemas avanzados de control de automatización para mejorar la comodidad de manejo y la eficiencia de producción de los equipos. Los sistemas de control de automatización modernos no solo pueden lograr un control preciso de los equipos, sino también optimizar el proceso de producción mediante sensores y análisis de datos.
Durante el proceso de investigación y desarrollo tecnológico, es necesario realizar continuos experimentos y pruebas para verificar la viabilidad y el potencial de optimización del esquema de diseño. Mediante la simulación por ordenador y las pruebas de laboratorio, se puede predecir de antemano el rendimiento del equipo en la producción real, lo que reduce el ciclo y el coste de desarrollo.
Fabricación y ensayo de prototipos
Una vez determinado el esquema de diseño, se fabricó el primer prototipo de la termoformadora de tres estaciones. Mediante una serie de pruebas y ajustes, se optimizan continuamente el rendimiento y la estabilidad del equipo. Durante las pruebas, se hizo hincapié en los siguientes aspectos:
Eficiencia de producción: En comparación con los equipos tradicionales de una sola estación, la eficiencia de producción de la máquina termoformadora de tres estaciones mejora significativamente. Mediante la optimización de los parámetros del proceso y la estructura del equipo, se puede lograr una mayor velocidad de producción y un menor consumo de energía.
Calidad del producto: Ajustando la temperatura de calentamiento y la presión de moldeo, se garantiza que los productos moldeados cumplan los estándares de calidad esperados. Los productos de alta calidad no sólo pueden satisfacer la demanda del mercado, sino también mejorar la competitividad de las empresas en el mercado.
Fiabilidad del equipo: Garantice la fiabilidad y durabilidad de los equipos mediante pruebas de funcionamiento a largo plazo. Un equipo fiable puede reducir el tiempo de inactividad y mejorar la continuidad y estabilidad de la producción.
Durante la prueba, el equipo de I+D registrará y analizará diversos datos, averiguará los factores clave que afectan al rendimiento del equipo e introducirá mejoras específicas. Mediante repetidas pruebas y optimizaciones, se determinan finalmente los parámetros óptimos del equipo y los procedimientos de funcionamiento.
Puesta en producción y respuesta del mercado
Tras muchas rondas de pruebas y mejoras, la máquina de termoformado de tres estaciones se puso finalmente en el mercado. Gracias a su eficiente capacidad de producción y a la excelente calidad del producto, se ganó rápidamente el reconocimiento del mercado. Los comentarios de los usuarios promovieron aún más la optimización y mejora del equipo. Los datos y los comentarios sobre el uso real no sólo pueden ayudar a mejorar el diseño del equipo, sino también orientar la investigación y el desarrollo de nuevos productos.
La recogida de opiniones del mercado es una base importante para la mejora de los equipos. Gracias a la estrecha colaboración con los clientes, los fabricantes pueden comprender a tiempo las necesidades de los usuarios y los cambios del mercado, ajustar rápidamente las estrategias de producción y las direcciones de I+D, y mantener la competitividad del mercado.
Mejora continua e innovación
Para adaptarse a la siempre cambiante demanda del mercado y al progreso tecnológico, la investigación y el desarrollo de máquinas termoformadoras de tres estaciones no se ha detenido. Los fabricantes siguen introduciendo nuevas tecnologías, como sistemas de control inteligente, tecnologías de recuperación de energía, etc., para mejorar aún más el rendimiento y los efectos de ahorro de energía de los equipos. En el futuro, con la aplicación de tecnologías como la inteligencia artificial y el big data.