¿Cuáles son las razones de la variación de grosor en los productos formados por el proceso de termoformado?
El termoconformado es una técnica de fabricación flexible que moldea láminas y películas de plástico en diversos productos, en los que la variación del grosor es crucial tanto para el diseño como para la funcionalidad.
Selección de material y grosor: El tipo de plástico utilizado influye significativamente en el grosor de los productos finales. Por ejemplo:
Películas de poliestireno (PS): Normalmente se utiliza para vidrios transparentes desechables, con espesores generalmente inferiores a 0,5 mm.
Hojas de polipropileno (PP): Empleado para vasos de colores o envases de espuma de poliestireno, que suelen tener espesores superiores a 0,5 mm.
Programación de productos: Un elemento importante del diseño de productos es la Programación del Producto, que especifica los espesores y dimensiones necesarios para cada aplicación. En el caso de las botellas, este proceso se denomina Programación Parison, un método desarrollado por primera vez por Denes Hankar en Cincinnati.
Botellas y variación de grosor: Tomemos como ejemplo una botella de refresco: el cuello y la base son más gruesos, mientras que el cuerpo es más delgado. Este diseño cumple una función esencial:
El cuello requiere un grosor adicional para crear un cierre hermético que permita taparlo correctamente.
La base debe ser más gruesa para proporcionar el peso y el soporte necesarios para la botella.
Las variaciones de grosor son fundamentales para mejorar el rendimiento de los productos termoformados. Por ejemplo, un grosor uniforme en artículos como tanques químicos podría dar lugar a una rigidez y estabilidad insuficientes. Así pues, se incorporan variaciones intencionadas de grosor para garantizar que cada producto cumpla eficazmente los requisitos funcionales previstos.
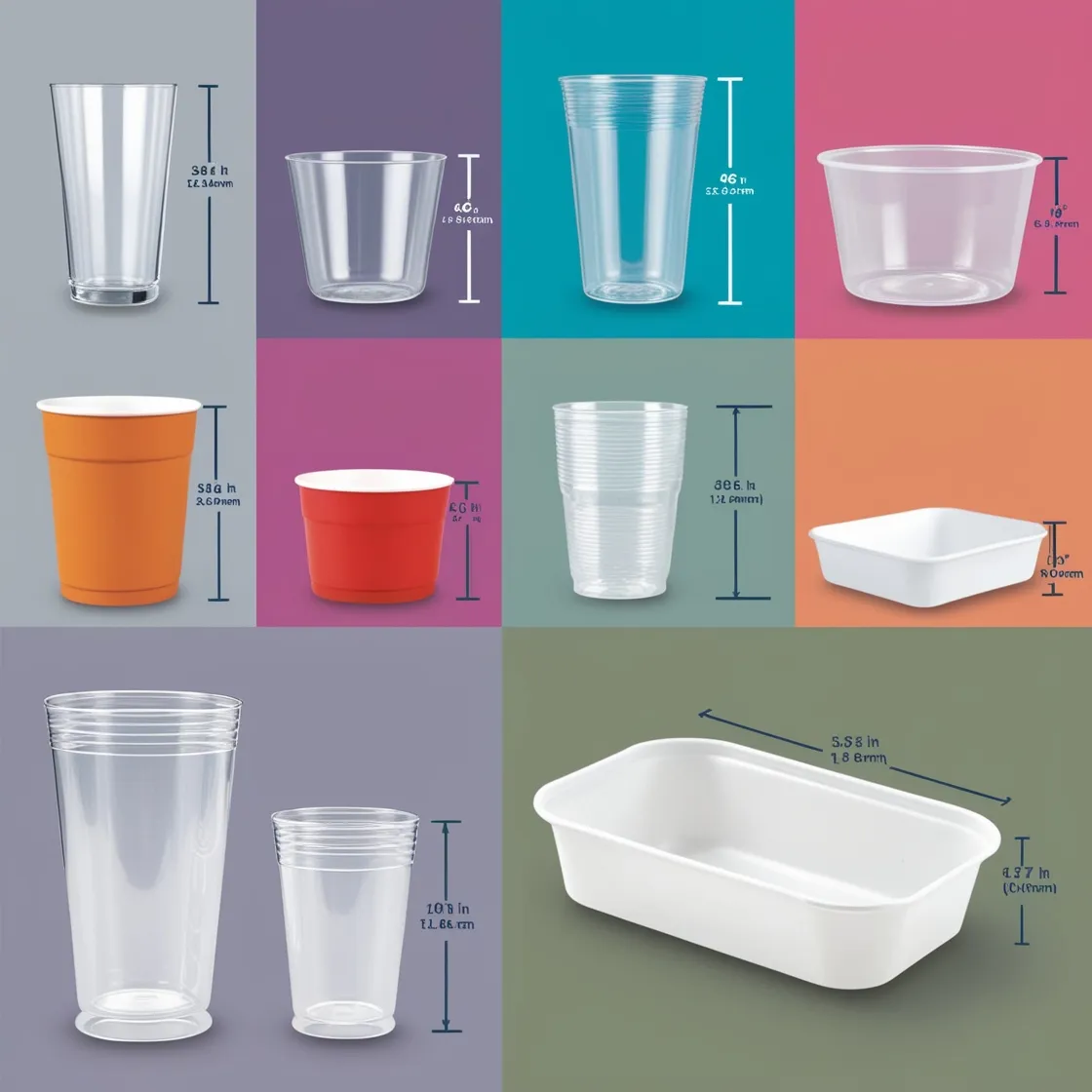
Estrategias para aumentar la dureza de los productos termoformados de PP y HDPE
Tras el proceso de termoformado, existen varias técnicas secundarias para mejorar la rigidez o la resistencia al impacto del polipropileno (PP) y el polietileno de alta densidad (HDPE). Aunque estos polímeros termoplásticos conservan su dureza y resistencia a los productos químicos tras el conformado, los siguientes métodos pueden mejorar su dureza:
Reticulación química: Una estrategia muy eficaz consiste en aplicar tratamientos químicos que favorezcan la reticulación dentro de los polímeros. Este proceso consiste en formar enlaces entre las cadenas poliméricas, creando una red rígida que mejora la resistencia a la deformación por calor.
Envejecimiento físico: Otro método viable es el envejecimiento físico, que consiste en almacenar la pieza termoformada a temperatura ambiente o ligeramente elevada durante un periodo prolongado. Esto permite que las cadenas de polímero se estabilicen y aumenten su rigidez con el tiempo. Sin embargo, este proceso puede ser gradual y puede no proporcionar la dureza deseada para todas las aplicaciones.
Estabilización UV: La exposición a la radiación ultravioleta (UV) también puede contribuir al endurecimiento del PP y el HDPE como resultado del proceso de estabilización. La adición de estabilizadores UV mejora la resistencia de la pieza a la intemperie, y una exposición prolongada puede aumentar aún más su dureza.
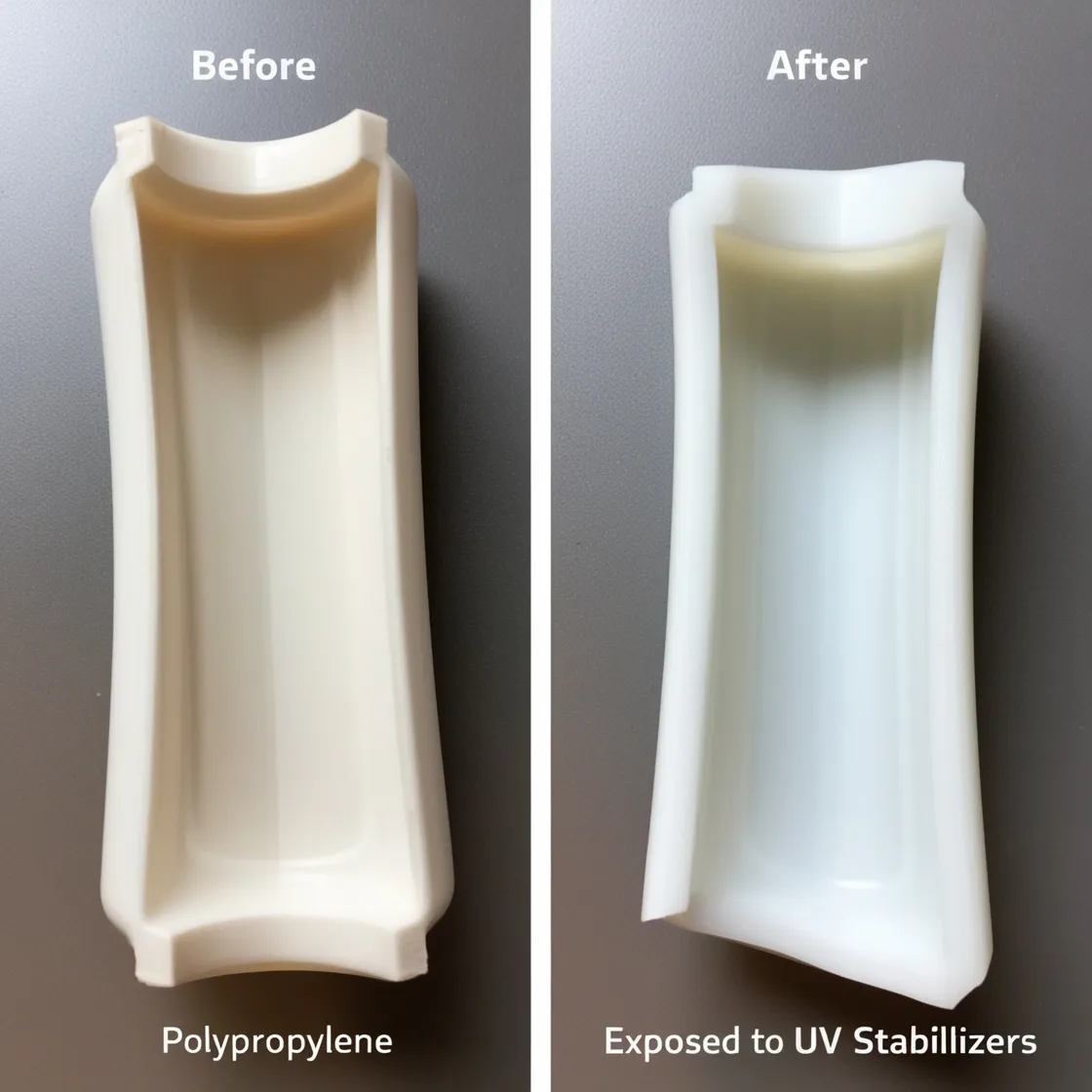
Recocido posterior al termoformado: El recocido es un proceso controlado que consiste en calentar el material a una temperatura específica seguida de una fase de enfriamiento lento. Este método puede aliviar las tensiones internas y dar lugar a una mayor dureza. Es esencial gestionar este proceso con cuidado para evitar el alabeo o la deformación de la pieza.
Influencia del grosor del material: Al evaluar estas técnicas de endurecimiento, la profundidad del conformado es una consideración importante. Las formas más profundas suelen requerir un mayor estiramiento del material, lo que puede provocar una reducción del grosor en esas zonas. Este efecto de adelgazamiento podría aumentar la flexibilidad, contrarrestando potencialmente los esfuerzos de endurecimiento previstos. Por lo tanto, es fundamental evaluar los métodos de endurecimiento teniendo en cuenta estas variaciones de grosor para garantizar que el producto final cumpla sus requisitos funcionales.
Cada método para aumentar la dureza tiene ventajas e inconvenientes distintos. La elección del proceso más adecuado dependerá de la aplicación específica y de las características de rendimiento deseadas del componente termoformado.
¿Cómo se comprueba la calidad de las planchas termoformadas?
Para garantizar la calidad de las planchas termoformadas, se utilizan diversas técnicas de ensayo, cada una de ellas centrada en diferentes atributos del material. Estos son los principales métodos de ensayo:
- Inspección visual:
La comprobación inicial consiste en buscar defectos superficiales como arañazos, burbujas o decoloración.
- Medición del espesor:
Se emplean calibradores o micrómetros para medir el grosor de la lámina en varios puntos y garantizar su uniformidad.
- Pruebas mecánicas:
- Prueba de resistencia a la tracción: Esta prueba evalúa la capacidad del material para soportar fuerzas de tracción.
- Ensayo de resistencia a la flexión: evalúa la capacidad del material para resistir la flexión.
- Prueba de resistencia al impacto: mide la durabilidad de la lámina cuando se somete a impactos repentinos.
- Prueba de resistencia al calor:
Este procedimiento examina el comportamiento del material a temperaturas más elevadas, verificando que conserva sus propiedades sin deformarse.
- Prueba de estabilidad dimensional:
Esta evaluación examina cuánto se encoge o deforma el material en diferentes condiciones ambientales, como el calor o la humedad.
- Prueba de resistencia química:
Este ensayo evalúa la capacidad del material para soportar la exposición a diversas sustancias químicas sin degradarse.
- Prueba de energía superficial:
La energía superficial se mide para determinar la idoneidad del material para el pegado, la impresión o el revestimiento.
- Prueba de transparencia y claridad:
En el caso de las láminas transparentes o translúcidas, esta evaluación valora la claridad óptica y las propiedades de transmisión de la luz.
- Prueba de propiedades de barrera:
Este método examina la eficacia de la lámina frente a los gases o la humedad, algo vital para el envasado.
- Pruebas de adherencia:
Esto determina lo bien que se adhieren los revestimientos o las impresiones a la superficie de la lámina.
¿Cómo pasa el material de gránulos ¿a copos?
Preparación del material:
Seleccione gránulos de plástico adecuados, que suelen incluir poliestireno (PS), polipropileno (PP) y tereftalato de polietileno (PET). Asegúrese de secar el material para eliminar la humedad y evitar la formación de burbujas o defectos durante el calentamiento.
Proceso de extrusión:
Alimentación:
Los gránulos de plástico se introducen en la tolva de la extrusora por gravedad o mediante transporte mecánico (como un transportador de tornillo). La tolva suele tener sensores para controlar la velocidad de alimentación, lo que garantiza una alimentación estable.
Calentamiento y fusión:
La extrusora dispone de varias zonas de calentamiento que aumentan gradualmente la temperatura. Cada zona puede controlarse independientemente para adaptarse a las características de fusión de los distintos materiales. El plástico fundido es empujado a través de estas zonas por el tornillo, logrando un estado de fusión uniforme.
Mezclando:
El diseño del tornillo (como la profundidad, el paso y la forma) desempeña un papel crucial en la mezcla, ya que garantiza que los aditivos (como el masterbatch de color, los antioxidantes, etc.) se distribuyan uniformemente por el material base, lo que evita la inconsistencia del material.
Extrusión:
El plástico fundido se extruye a través de una matriz, formando una lámina continua. El diseño de la matriz determina la anchura y el grosor de la lámina.
Durante la extrusión, es esencial mantener la presión y la temperatura adecuadas para garantizar la uniformidad de la lámina.
Enfriamiento y solidificación:
La chapa caliente entra inmediatamente en un dispositivo de enfriamiento, normalmente rodillos de enfriamiento o un baño de agua. Los rodillos de enfriamiento emplean agua o aire frío para bajar rápidamente la temperatura de la chapa, evitando su deformación.
El proceso de enfriamiento puede ajustarse para controlar la velocidad de enfriamiento, garantizando un grosor y una solidificación uniformes de la chapa.
Corte y bobinado:
La chapa enfriada puede enrollarse en bobinas o cortarse en longitudes y anchuras específicas. El corte suele realizarse automáticamente con cuchillas para garantizar bordes lisos.
Termoformado:
Calefacción:
Las láminas cortadas se colocan en una termoformadora, donde se calientan hasta ablandarse mediante infrarrojos o convección, normalmente entre 160 °C y 200 °C.
Formando:
La lámina ablandada se coloca en un molde, donde se ajusta firmemente a la forma del molde mediante conformado al vacío (eliminando el aire del molde) o conformado a presión (aplicando presión de aire).
Durante el conformado, la chapa se fija en el molde para garantizar una forma precisa.
Enfriamiento y desmoldeo:
La lámina formada se enfría, normalmente con agua o aire, para solidificarse. Una vez enfriado, el producto final se extrae del molde.
Post-procesamiento:
El producto acabado se somete a recorte, punzonado u otro tratamiento posterior para cumplir los requisitos específicos de la aplicación. Algunos productos también pueden requerir impresión u otras decoraciones.
Inspección de calidad:
Por último, el producto acabado se somete a una exhaustiva inspección de calidad, que incluye mediciones dimensionales, inspección visual y pruebas de propiedades físicas, para garantizar el cumplimiento de las especificaciones y normas.
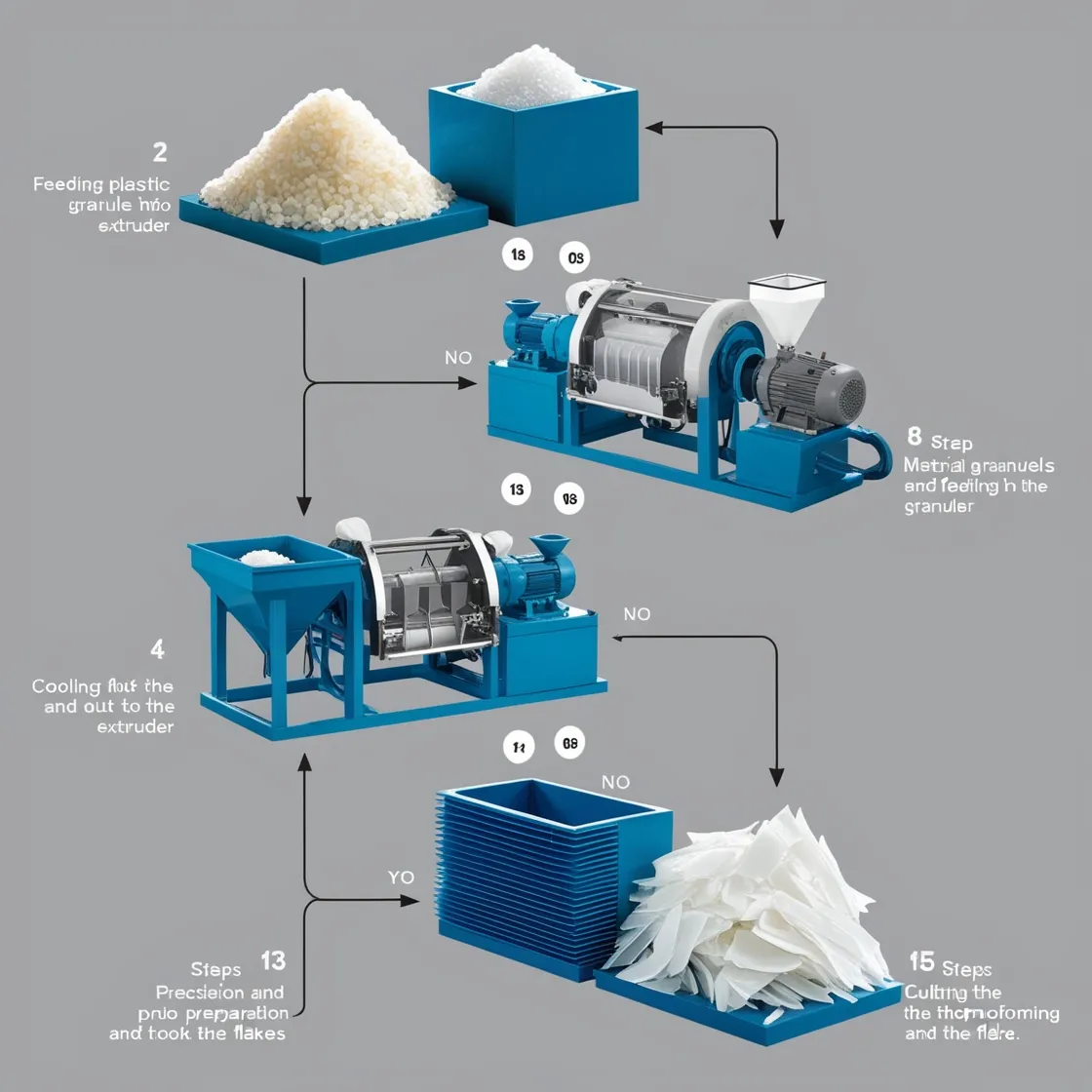
Dominio de las planchas termoformadas: Cómo influye el grosor del material en la calidad y la funcionalidad
Si está considerando el termoformado para su proyecto, tome nota: las planchas termoformadas tienen muchos grosores. Esto se debe a que este versátil proceso puede utilizarse para fabricar cualquier cosa, desde envases de alimentos (por ejemplo, vasos de yogur) hasta paneles de puertas de vehículos. Además, los distintos productos suelen requerir espesores de material diferentes.
¿Quiere asegurarse de que sus productos termoformados tienen un aspecto estupendo y funcionan a la perfección? Una cosa en la que quizá no piense es en el grosor que debe tener la lámina de plástico al darle forma. No puede ser ni demasiado fina ni demasiado gruesa si quiere que quede perfecta. Le contaremos todo lo que necesita saber para elegir el mejor calibre (así es como se mide el grosor) para un termoformado satisfactorio, tanto si quiere conseguir un envase bonito que muestre sus habilidades de diseño como si quiere piezas de vehículos resistentes que no se rompan cuando más se necesitan. En este blog, aprenderá a elegir el calibre de material plástico adecuado para lograr la máxima funcionalidad, forma y estética en sus productos termoformados.
El papel del grosor del material en el termoformado
Las propiedades de un producto termoformado dependen de su grosor. Esto incluye todo, desde la fuerza y la resistencia a los daños, hasta el acabado de la superficie e incluso el peso. Saber qué rango de grosor es el mejor para estos factores es importante si quiere que sus productos sean de buena calidad, pero también si quiere fabricarlos de forma económica utilizando el termoconformado.
Integridad estructural y resistencia al impacto
Las planchas más gruesas proporcionan un mayor soporte estructural y una mayor resistencia a los impactos, lo que las hace adecuadas para productos que requieren durabilidad, como carcasas para dispositivos electrónicos o cubiertas protectoras para maquinaria.
Calidad de la superficie
Artículos como los electrónicos o los envases tienen mejor aspecto si presentan acabados finos. Para lograrlo, el termoformado utiliza materiales que pueden convertirse en superficies lisas sin necesidad de un costoso pulido, a veces utilizando láminas muy finas del material.
Consideraciones sobre el peso
Muchas industrias prefieren ahora productos ligeros porque son más baratos de transportar, consumen menos combustible y son más fáciles de manejar. Utilizando láminas más finas o materiales que sigan siendo lo bastante resistentes -para que no se rompan ni se deshagan-, los fabricantes pueden hacer productos finales que pesen mucho menos.
Espesor máximo de la hoja
Las planchas termoformadas no suelen tener un grosor superior a 12,7 mm (0,5 pulgadas). Sin embargo, este grosor es menos habitual. Suele utilizarse para trabajos pesados que requieren piezas muy resistentes: piense en piezas de automóvil, elementos de maquinaria de gran tamaño y carcasas de algunos equipos. Las planchas de termoconformado de este grosor suelen denominarse termoconformado de calibre grueso.
Hay ocasiones en las que el termoformado requiere utilizar el material plástico más grueso posible. Esto es especialmente cierto en el caso de determinados productos que deben ser resistentes o tener mucha profundidad. A continuación le explicamos por qué elegir un plástico más grueso y qué ventajas puede ofrecerle.
- Termoformado de embutición profunda
Si desea fabricar artículos de plástico de gran tamaño con técnicas de embutición profunda -y que no presenten ningún adelgazamiento o hendidura al darles forma-, necesitará utilizar mucho material y láminas de plástico de gran calibre.
- Componentes industriales pesados
Si necesita componentes que puedan soportar condiciones industriales duras, sin duda querrá que estén fabricados con materiales de gran espesor. Estos materiales ofrecen una durabilidad inigualable: resisten los daños y el desgaste provocados por el uso rudo mucho mejor que otros tipos.
- Productos a gran escala
Productos como bañeras, revestimientos de lechos de camiones y piezas específicas de vehículos requieren un plástico más grueso para aguantar bien el uso -sobre todo en grandes superficies- y seguir funcionando correctamente.
Espesor mínimo
En el otro extremo del espectro, las láminas termoformadas pueden ser tan finas como 0,35 mm (0,014 pulgadas) durante el termoformado de calibre fino, a menudo utilizado para vasos desechables, tapas, bandejas, contenedores y otros artículos de envasado. La rapidez de producción y la rentabilidad por el uso de materiales son ventajas del termoformado de calibre fino; consideraciones importantes en una industria muy centrada en ser rentable como la del envasado.
Descubra el arte y la eficacia del termoformado de calibre finoExplore cómo esta técnica permite a los fabricantes crear artículos delicados y detallados con precisión, y todo ello ahorrando dinero.
Espesor mínimo del material: Adelgazamiento de precisión
- Ahorro de costes
Las láminas más finas ahorran dinero al comprarlas y también significan que el calentamiento de la lámina y el moldeado requieren menos tiempo, por lo que se consume menos energía en esta parte del proceso y, además, los productos se fabrican más rápidamente.
- Formas detalladas y complejas
Si busca diseños intrincados y detalles finos, los materiales de calibre fino son la mejor opción. Estos materiales pueden captar mejor los matices de la superficie de un molde y una herramienta, lo que significa que producen artículos muy detallados que también tienen un buen aspecto.
- Envases flexibles
El termoformado de calibre fino ha desempeñado un papel fundamental en la popularidad de los envases flexibles y transparentes en las industrias alimentaria, minorista y médica. Este tipo de material proporciona una excelente barrera para proteger los productos, así como una buena visibilidad para los consumidores.
Factores que influyen en la elección del grosor
Varios factores determinan el grosor adecuado para un producto termoformado, entre ellos:
Requisitos de durabilidad: Los artículos más pesados y duraderos necesitan un material plástico más grueso.
Necesidades de flexibilidad: Los artículos flexibles, como ciertos tipos de envases, pueden beneficiarse de materiales más finos.
Contornos del molde: La complejidad y profundidad del molde pueden requerir ajustes en el grosor del material plástico para conseguir el detalle y la integridad estructural deseados.
Tipo de material: Los distintos plásticos tienen diferentes características de resistencia y flexibilidad, lo que puede afectar al grosor óptimo para una aplicación determinada. Los materiales más utilizados son el ABS, el poliestireno, el polietileno y el PVC.