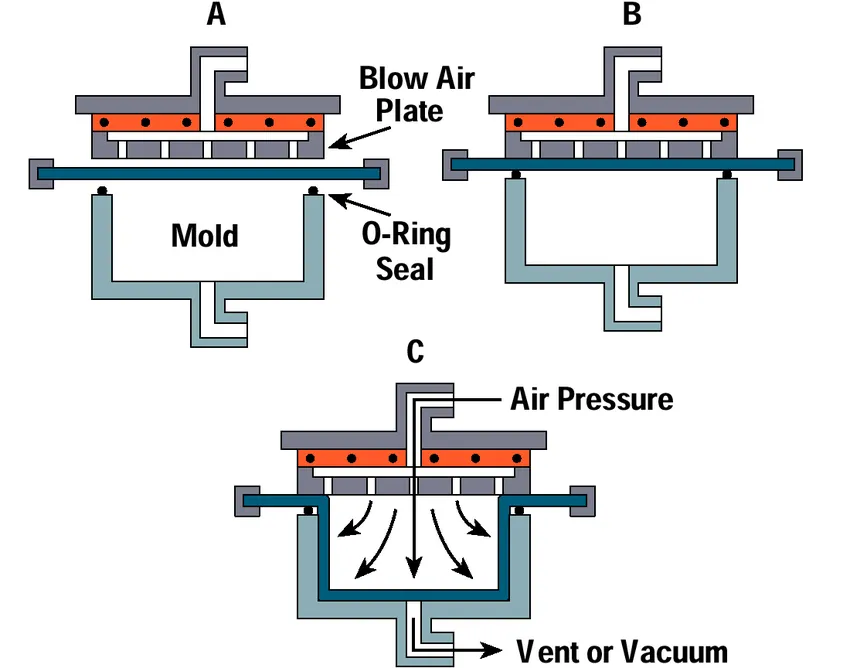
Optimización de los tiempos de ciclo en los procesos de termoformado
Introducción
En el competitivo mundo de la fabricación de plásticos, la optimización de los tiempos de ciclo en los procesos de termoformado es crucial para mejorar la productividad, reducir los costes y mantener unos estándares de alta calidad. El termoformado, un proceso que consiste en calentar láminas de plástico y darles formas específicas mediante moldes, se utiliza ampliamente en diversos sectores, como el envasado, la automoción y los dispositivos médicos. Este artículo explora las estrategias para optimizar los tiempos de ciclo en los procesos de termoformado, proporcionando información detallada y estudios de casos reales para ilustrar una aplicación eficaz.
Comprender los tiempos de ciclo en el termoformado
La duración del ciclo de termoformado se refiere al tiempo total necesario para completar un ciclo de producción, desde el calentamiento de la lámina de plástico hasta la expulsión de la pieza acabada del molde. Consta de varias etapas:
- Tiempo de calentamiento: El tiempo necesario para calentar la lámina de plástico a la temperatura de conformado requerida.
- Tiempo de formación: El tiempo necesario para dar forma a la lámina de plástico calentada utilizando el molde.
- Tiempo de enfriamiento: Duración del enfriamiento del plástico conformado para que conserve su forma.
- Tiempo de eyección: Tiempo necesario para extraer la pieza acabada del molde.
- Tiempo de carga y descarga: El tiempo dedicado a la carga de materias primas y a la descarga de productos acabados.
Cada etapa influye en la duración total del ciclo, y la optimización de estas fases puede dar lugar a mejoras significativas de la productividad y la rentabilidad.
Estrategias para optimizar los tiempos de ciclo
1. Sistemas avanzados de calefacción
Uno de los factores críticos para reducir la duración de los ciclos es la eficacia del sistema de calentamiento. Las tecnologías de calentamiento avanzadas, como los calentadores de infrarrojos (IR) y los calentadores cerámicos, pueden proporcionar un calentamiento más rápido y uniforme en comparación con los sistemas tradicionales.
Estudio de caso: Calentamiento por infrarrojos a alta velocidad en Plastipack
Empresa: Plastipack
Industria: Embalaje
Desafío: Plastipack se enfrentaba a largos tiempos de calentamiento, lo que prolongaba la duración de los ciclos y limitaba la capacidad de producción.
Solución: La empresa se ha modernizado con sistemas de calentamiento por infrarrojos de alta velocidad, que ofrecen un calentamiento rápido y uniforme.
Aplicación: Los calentadores IR se instalaron en las máquinas de termoformado, reduciendo el tiempo de calentamiento en 30%. El nuevo sistema permitió un control preciso de la temperatura, garantizando propiedades constantes del material.
Resultado: Plastipack experimentó una reducción de 25% en el tiempo total del ciclo, lo que se tradujo en un aumento significativo del rendimiento de la producción y una disminución del consumo de energía.
2. Diseño y refrigeración eficientes del molde
Optimizar el diseño del molde y los sistemas de refrigeración puede reducir drásticamente los tiempos de conformado y enfriamiento. El uso de materiales con alta conductividad térmica y la incorporación de canales de refrigeración avanzados pueden mejorar la eficacia de la refrigeración.
Caso práctico: Canales de refrigeración optimizados en AutoForm
Empresa: AutoForm
Industria: Automoción
Desafío: Tiempos de enfriamiento prolongados debido a un diseño ineficiente del molde, lo que provoca cuellos de botella y un aumento de los costes de producción.
Solución: AutoForm rediseñó sus moldes utilizando aluminio, que tiene mejor conductividad térmica que el acero. Además, integraron canales de refrigeración conformados avanzados.
Aplicación: Los nuevos moldes se fabricaron con tecnología de impresión 3D para crear complejos canales de refrigeración que se ajustaran a la forma de las piezas.
Resultado: Los tiempos de enfriamiento se redujeron en 40%, y la duración total de los ciclos disminuyó en 20%. Esto supuso un aumento de 15% en la eficiencia de la producción y una mejora de la calidad de las piezas gracias a un enfriamiento uniforme.
3. Automatización y robótica
La integración de la automatización y la robótica en el proceso de termoformado puede reducir significativamente los tiempos de carga, descarga y expulsión. Los sistemas automatizados garantizan una manipulación uniforme y rápida de los materiales, lo que reduce los errores humanos y aumenta la eficiencia general.
Caso práctico: Integración robótica en MedPlast Solutions
Empresa: Soluciones MedPlast
Industria: Productos sanitarios
Desafío: Los procesos manuales de carga y descarga eran lentos y propensos a errores, lo que prolongaba los tiempos de ciclo.
Solución: MedPlast Solutions integró brazos robotizados en sus líneas de termoformado para automatizar los procesos de carga y descarga.
Aplicación: Los brazos robóticos se programaron para manipular con precisión láminas de plástico y piezas acabadas. Los sensores y sistemas de visión garantizaban una colocación precisa y una inspección de calidad.
Resultado: La automatización redujo los tiempos de carga y descarga en 50%, lo que se tradujo en una disminución de 20% en la duración total de los ciclos. La manipulación uniforme mejoró la calidad del producto y redujo los residuos, lo que contribuyó a un mayor rendimiento.
4. Supervisión y control de procesos
La implantación de sistemas de supervisión y control de procesos en tiempo real ayuda a identificar los cuellos de botella y a optimizar cada fase del proceso de termoformado. Los sensores avanzados y el software pueden proporcionar datos valiosos para tomar decisiones informadas.
Caso práctico: Supervisión en tiempo real en PackPro
Empresa: PackPro
Industria: Envasado de bienes de consumo
Desafío: Tiempos de ciclo incoherentes debido a la falta de seguimiento y control del proceso en tiempo real, lo que da lugar a programas de producción impredecibles.
Solución: PackPro implantó un sistema de supervisión en tiempo real integrado en sus máquinas de termoformado.
Aplicación: Se instalaron sensores para controlar parámetros clave como la temperatura, la presión y el tiempo de ciclo. Los datos se analizaron mediante software especializado para identificar ineficiencias y optimizar los ajustes.
Resultado: La supervisión en tiempo real permitió a PackPro reducir la variabilidad de la duración de los ciclos en 15% y lograr programas de producción más predecibles. La capacidad de ajustar rápidamente los parámetros en función de los datos permitió reducir en 10% la duración total de los ciclos y mejorar la uniformidad de los productos.
5. Selección y pretratamiento del material
La elección de los materiales adecuados y su pretratamiento también pueden influir en la duración de los ciclos. Los materiales con propiedades de calentamiento y enfriamiento más rápidas, así como los pretratamientos que mejoran la conductividad térmica, pueden mejorar el proceso de termoformado.
Estudio de caso: Optimización de materiales en EcoPack
Empresa: EcoPack
Industria: Envases sostenibles
Desafío: Largos tiempos de ciclo debido al uso de láminas de plástico estándar con malas propiedades térmicas.
Solución: EcoPack cambió a materiales plásticos de alto rendimiento con mejores propiedades térmicas e incorporó procesos de pretratamiento para mejorar la conductividad del material.
Aplicación: Se comprobaron las propiedades de termoformado de los nuevos materiales y se aplicaron procesos de pretratamiento, como la rugosidad de la superficie, para mejorar la transferencia de calor.
Resultado: Los materiales y pretratamientos optimizados redujeron los tiempos de calentamiento y enfriamiento en 20%, lo que supuso una reducción de 15% en la duración total de los ciclos. La mejora de las propiedades térmicas también aumentó la calidad de los productos finales.
Conclusión
Optimizar los tiempos de ciclo en los procesos de termoformado es esencial para lograr una mayor productividad, ahorrar costes y mejorar la calidad del producto. Mediante la implantación de sistemas avanzados de calentamiento, un diseño eficiente de los moldes, la automatización, la supervisión en tiempo real y la optimización de los materiales, los fabricantes pueden mejorar significativamente sus operaciones de termoformado.
Los estudios de casos reales de Plastipack, AutoForm, MedPlast Solutions, PackPro y EcoPack ilustran los beneficios tangibles de estas estrategias. Cada empresa abordó con éxito sus retos específicos y logró mejoras sustanciales en los tiempos de ciclo, lo que se tradujo en una mayor eficiencia y competitividad.
A medida que la industria manufacturera siga evolucionando, la adopción de estas estrategias de optimización será crucial para mantenerse por delante de la competencia y satisfacer las crecientes demandas de los clientes. Innovando y perfeccionando continuamente sus procesos, los fabricantes pueden garantizar un crecimiento sostenible y el éxito en el dinámico mercado del termoformado.