In the plastic packaging industry, positive and negative pressure thermoforming machines are widely used for producing disposable food containers, blister trays, folding boxes, and other products due to their high efficiency and precise forming capabilities. In such equipment, cylinders act as critical actuators whose performance directly impacts forming quality, motion stability, and production efficiency.
This article provides a systematic analysis of the working principle of cylinders in positive and negative pressure thermoforming machines, key differences, and optimization recommendations to help enterprises improve their equipment configuration and maintenance standards, further supporting high-quality automated production lines.
Introduction to Positive and Negative Pressure Thermoforming Machines
These machines use softened plastic sheets, formed by applying both vacuum (negative pressure) and compressed air (positive pressure) to press the material into a mold cavity. Compared to single-pressure forming methods, this technique is more suitable for producing complex, high-precision, and deep-draw products.
Positive pressure pushes the sheet into the mold, while negative pressure pulls it by vacuum suction. This dual-pressure coordination improves product detail, wall thickness uniformity, and overall forming quality—ideal for food-grade packaging or high-precision industrial blister products.
Because the forming process involves multiple synchronized steps, cylinders must operate in tight coordination with the vacuum and pressure systems. Their quality and performance determine the overall reliability and consistency of the thermoforming machine. Without accurate cylinder control, even the most advanced forming molds or heaters cannot deliver consistent product results.
Key Cylinder Applications in Thermoforming Equipment
In positive and negative pressure thermoforming machines, cylinders are typically used in the following locations:
- Mold lifting systems– for upper and lower mold opening/closing;
- Clamping frames– to fix and stabilize heated plastic sheets;
- Ejector mechanisms– to push formed products out of the mold cavity;
- Stacking systems– for product collection, counting, and neat stacking;
- Sheet feeding/pushing systems– to move sheets from the heating to forming station;
- Assistive vacuum/blow control parts– to synchronize with pressure cycles.
These operations rely on cylinders for frequent, highly repetitive motions, requiring fast response, precise positioning, excellent sealing, and long life. Each of these components interacts with the machine’s PLC system, which governs the sequence of operations based on timing, sensor input, and preset forming parameters. The role of cylinders in these stations is not only mechanical but also involves accurate response to electronic signals, ensuring the entire thermoforming cycle functions seamlessly.
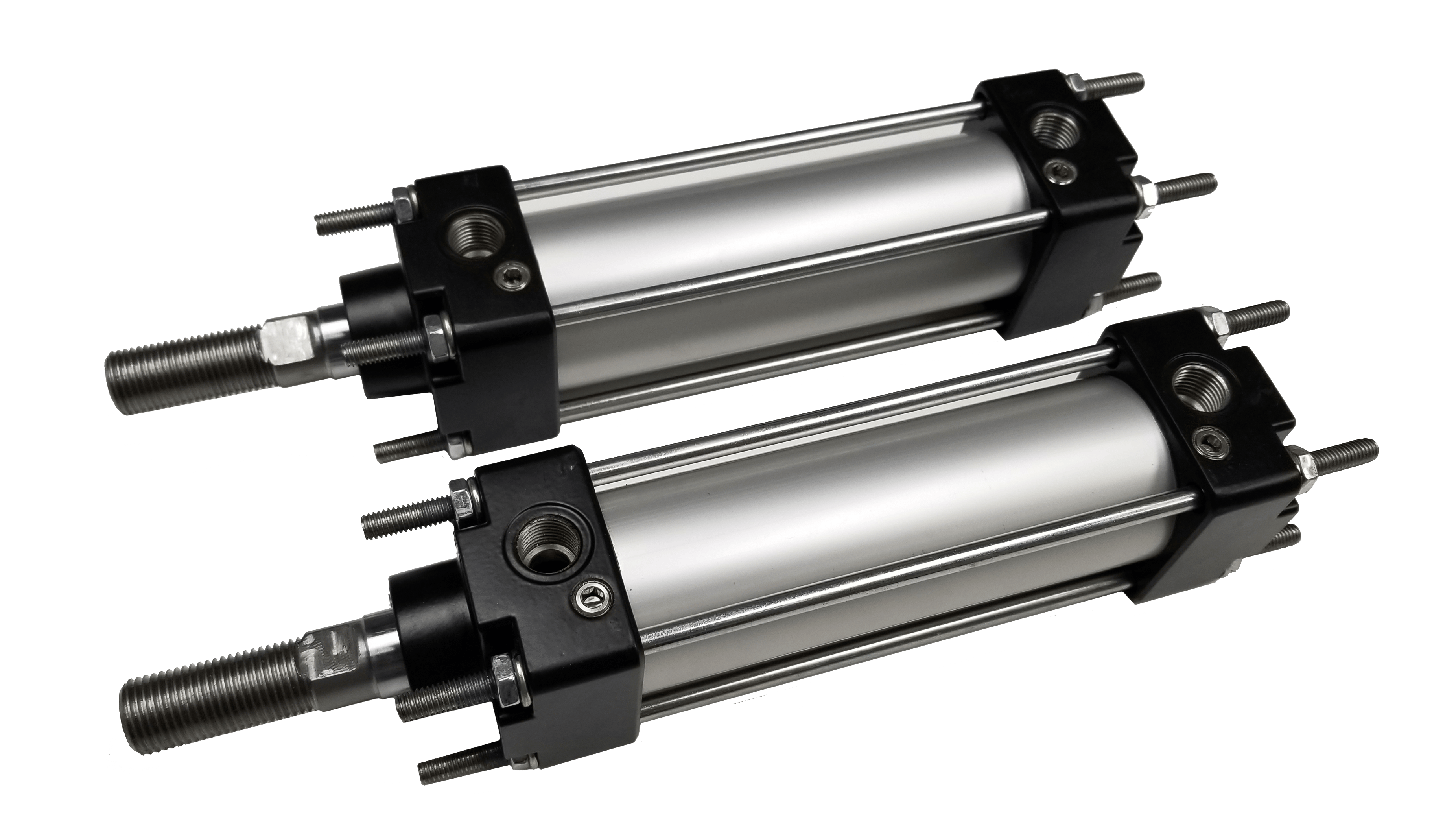
Working Principle of Cylinders in the Forming Process
Although the basic principle of a cylinder is to convert compressed air into linear or reciprocating motion via a piston, its role in a positive and negative pressure system requires additional coordination with vacuum and pressure processes:
1.Mold Closing and Opening
- Cylinders drive the mold to close smoothly with cushioning to avoid misalignment or sheet displacement.
- The clamping frame must engage first to ensure proper sealing before mold closure, ensuring vacuum efficiency.
- Mold opening must be quick and safe to avoid suction-related sticking, and ideally designed with adjustable air exhaust speed to reduce sudden retraction.
2.Clamping and Sealing
- Cylinders rapidly engage the clamping frame, applying consistent pressure to form a sealed environment.
- Any deviation in clamping pressure or stroke length can result in vacuum leaks, affecting the final product.
- Precision in these actions is typically managed through sensor-monitored feedback systems.
3. Ejecting and Demolding
- After forming, ejector cylinders initiate movement to lift or push the formed part out of the mold cavity.
- This must be done gently enough to prevent part damage, particularly for thin-wall or delicate packaging products.
- High-end systems often use guided cylinders or segmented ejection designs to prevent product warping.
4. Stacking and Product Handling
- Stacking operations rely on rapid-response, compact-stroke cylinders that push products into stacking trays.
- Some lines use dual-cylinder pushers for synchronized motion that maintains product orientation.
- These cylinders are frequently mounted on slide tracks with adjustable stroke stops to fit different product sizes.
In addition to these main forming actions, some thermoforming systems also utilize miniature cylinders to control air release valves, cooling plate positioning, or sheet tension arms. Each of these tasks may seem minor, but collectively they ensure smooth and stable operation of the entire thermoforming process.
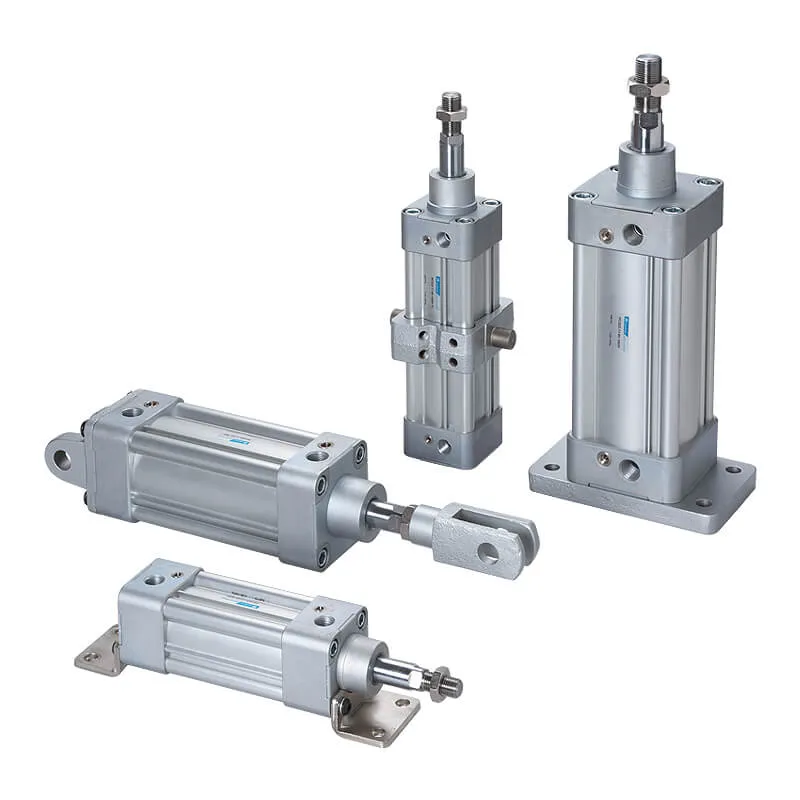
Special Requirements for Cylinders in Thermoforming
In positive and negative pressure thermoforming machines, cylinders must meet several key technical requirements to ensure optimal performance:
First, motion synchronization is critical. Multiple cylinders often operate simultaneously in different parts of the machine, and their actions must be precisely coordinated to prevent mechanical interference or forming errors. This is particularly important when mold lifting, clamping, and vacuum activation must occur within milliseconds of one another.
Second, air tightness is essential. High sealing performance in both the cylinder body and its connections prevents air leaks that could compromise the vacuum forming process. Any small air leak can reduce negative pressure within the forming chamber, resulting in poor definition or incomplete parts.
Third, real-time feedback is necessary. Many cylinders are equipped with magnetic switches or sensors that provide accurate position feedback, allowing the control system to monitor and adjust operations in real time. This capability is critical in modern high-speed thermoforming lines.
Fourth, smooth motion and cushioning are vital. Cylinders need to be equipped with throttle valves or built-in cushions to regulate movement speed and reduce impact, especially in mold lifting or clamping actions. Adjustable cushioning helps prevent hard stops, which could damage the tooling or misalign parts.
Lastly, the cylinders must support high-frequency operation. Since thermoforming is a continuous, high-speed process, the cylinders must have long service life, high repeatability, and minimal downtime to meet 24/7 production demands. This typically involves using corrosion-resistant materials, high-performance seals, and precision-machined cylinder bores.
Optimization Recommendations for Cylinder Performance
1. Use Reputable Brands and Quality Seals
Brands like SMC, FESTO, and Airtac offer industrial-grade cylinders with high reliability and long service life. These brands also provide a wide range of stroke lengths, bore diameters, and mounting options to match different thermoforming needs.
2. Integrate Smart Control Systems
Use PLC-controlled solenoid valves for precise timing. Combine with sensors to achieve closed-loop control and avoid malfunction. In addition, software optimization can help fine-tune cylinder motion curves for smoother transitions between forming steps.
3. Add Air Treatment Units
Use air filters, regulators, and oil mist lubricators to ensure clean air enters the cylinder, preventing internal wear. Moisture or contaminants in the air line can cause seal degradation, increase friction, or create inconsistent cylinder response.
4. Configure Proper Cushioning and Speed
Avoid shocks by setting buffer chambers and throttle valves based on mold weight and stroke. Smooth motion ensures machine stability and prolongs the life of surrounding components like frames and linear bearings.
5. Establish Maintenance Protocols
- Inspect air pipes and joints daily for leaks or signs of wear.
- Lubricate piston rods and sliders regularly with appropriate grease.
- Replace aging seals and O-rings every 3 to 6 months, depending on usage frequency.
- Keep maintenance logs and use predictive diagnostics to schedule part replacements before failure.
A well-maintained pneumatic system not only prolongs the lifespan of cylinders but also enhances the stability of the forming process, reducing waste and improving overall equipment effectiveness (OEE).
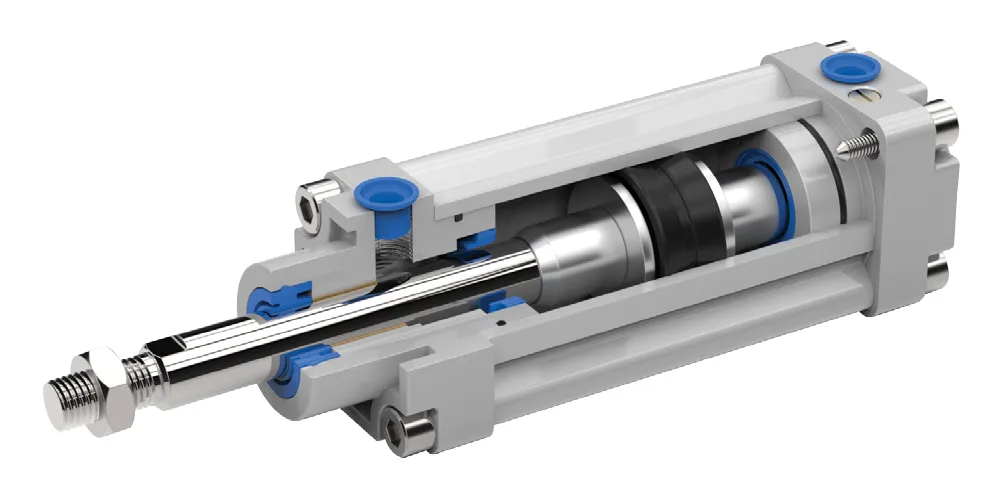
Case Study and Practical Insights
In a three-station positive and negative pressure thermoforming line for fruit blister boxes, engineers replaced traditional single-acting frame cylinders with double-acting cushioned ones. They also added magnetic sensors for position feedback, achieving synchronized clamping and mold closing. This upgrade improved forming pass rate by 12% and reduced downtime by 30%.
In another case involving PET folding box production, optimization of the ejection cylinder’s stroke and the addition of a shock absorber led to a 20% increase in throughput and reduced product deformation complaints by half. These examples highlight how even minor changes in cylinder design or layout can yield significant operational benefits.
Some companies have also upgraded their stacking station cylinders to intelligent servo-cylinder combinations, improving stacking accuracy for lightweight packaging and reducing secondary waste from misaligned stacks. These innovations are becoming essential for high-volume producers.
This demonstrates that optimizing cylinder structure and control logic in thermoforming significantly enhances product quality and equipment efficiency.
Conclusión
In positive and negative pressure thermoforming machines, cylinders are not just basic actuators—they are essential to ensuring precision, sealing, and production capacity. Understanding their working principles and optimizing their configuration improves product quality and reduces equipment failure.
For both machine builders and users, choosing the right cylinder type and control strategy is key to achieving high-performance thermoforming. Optimized cylinder design and control directly support the realization of “high-precision blister forming,” “automated food packaging equipment,” and “multi-station thermoforming efficiency enhancement.”
As demand continues to grow for lightweight, recyclable, and intricately shaped packaging, investing in high-performance pneumatic systems, including reliable cylinders, will remain a cornerstone of modern thermoforming line upgrades.