Каковы причины изменения толщины изделий, полученных методом термоформования?
Термоформование - это гибкая технология производства, которая позволяет формовать пластиковые пленки и листы в различные изделия, где изменение толщины имеет решающее значение как для дизайна, так и для функциональности.
Выбор материала и толщина: Тип используемого пластика существенно влияет на толщину готовых изделий. Например:
Пленки из полистирола (PS): Обычно используется для изготовления прозрачных одноразовых стаканов, толщина которых обычно не превышает 0,5 мм.
Полипропиленовые (ПП) листы: Используется для цветных стекол или контейнеров из пенополистирола, толщина которых обычно превышает 0,5 мм.
Программирование продуктов: Важным элементом проектирования изделий является программирование изделий, в котором указываются необходимые толщины и размеры для каждого применения. В случае с бутылками этот процесс называется Parison Programming - метод, впервые разработанный Денесом Ханкаром в Цинциннати.
Бутылки и вариации толщины: Возьмем, к примеру, бутылку для безалкогольных напитков: у нее более толстые горлышко и дно, а корпус остается тонким. Такая конструкция служит важнейшим целям:
Горлышко требует дополнительной толщины, чтобы создать герметичное уплотнение для правильной укупорки.
Основание должно быть толще, чтобы обеспечить необходимый вес и опору для бутылки.
Вариации толщины имеют решающее значение для улучшения характеристик термоформованных изделий. Например, одинаковая толщина таких изделий, как химические резервуары, может привести к недостаточной жесткости и устойчивости. Таким образом, преднамеренное изменение толщины позволяет обеспечить эффективное соответствие каждого изделия его функциональным требованиям.
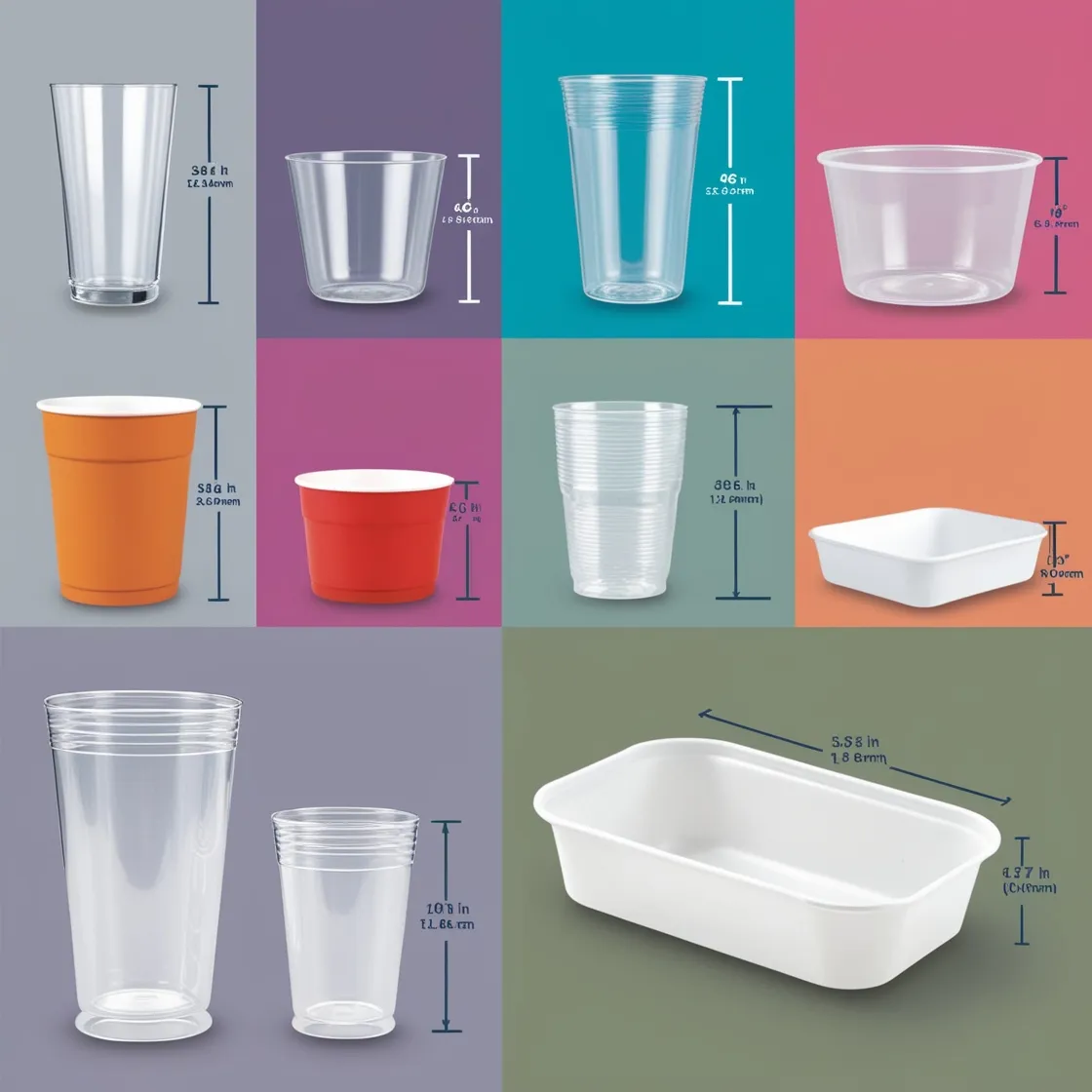
Стратегии повышения твердости термоформованных изделий из ПП и ПЭВП
После процесса термоформования существует несколько вторичных методов повышения жесткости или ударной прочности полипропилена (ПП) и полиэтилена высокой плотности (ПЭВП). Хотя эти термопластичные полимеры сохраняют свою прочность и устойчивость к химическим веществам после формования, следующие методы могут повысить их твердость:
Химическая сшивка: Высокоэффективной стратегией является химическая обработка, способствующая сшиванию полимеров. Этот процесс включает в себя образование связей между полимерными цепями, создавая жесткую сеть, которая повышает устойчивость к тепловой деформации.
Физическое старение: Другим эффективным методом является физическое старение, которое заключается в хранении термоформованной детали при температуре окружающей среды или слегка повышенной температуре в течение длительного периода времени. Это позволяет полимерным цепям стабилизироваться и увеличивать жесткость со временем. Однако этот процесс может быть постепенным и не обеспечит желаемой твердости для всех областей применения.
УФ-стабилизация: Воздействие ультрафиолетового (УФ) излучения также может способствовать упрочнению ПП и ПЭВП в результате процесса стабилизации. Добавление УФ-стабилизаторов повышает устойчивость деталей к атмосферным воздействиям, а длительное воздействие может привести к увеличению твердости.
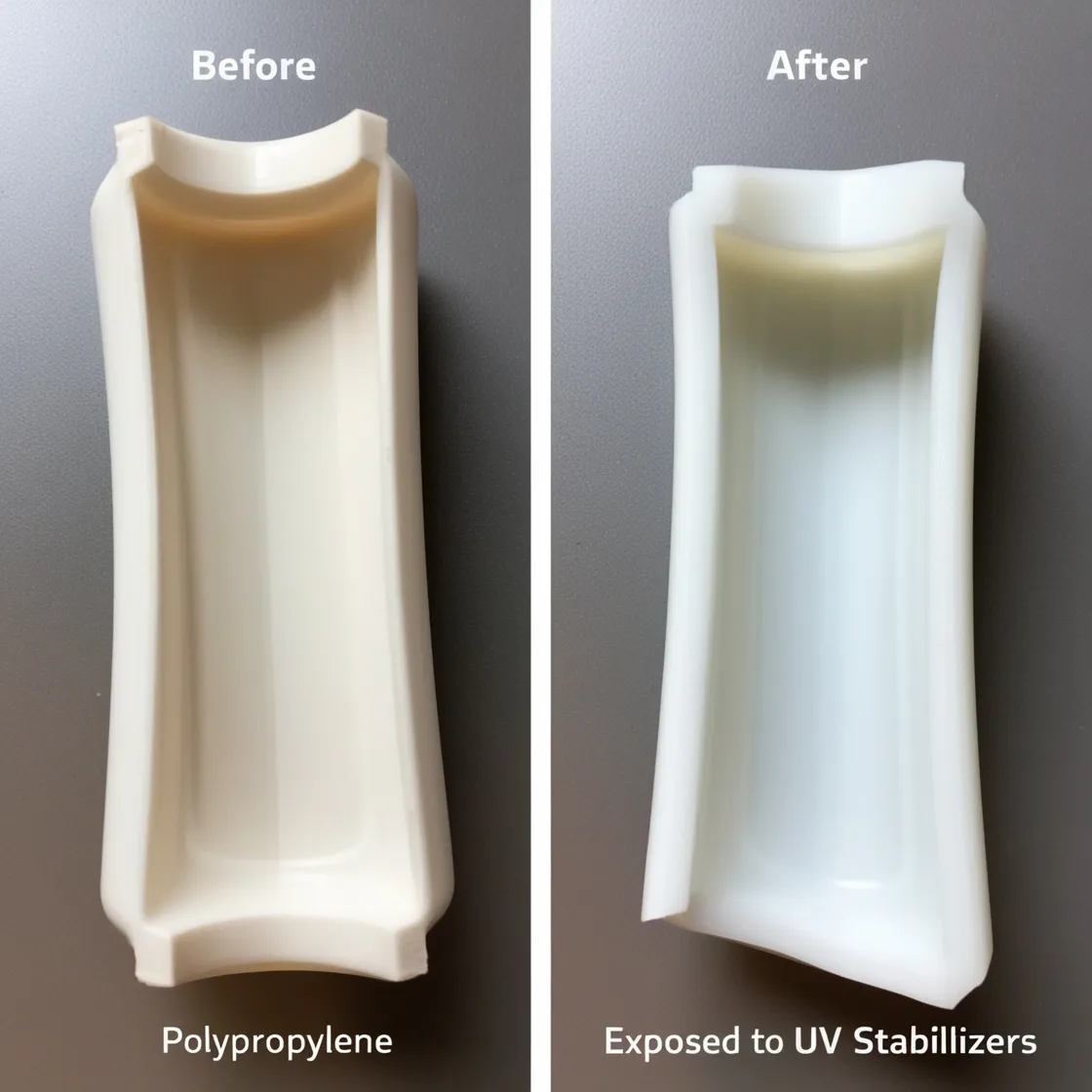
Посттермоформовочный отжиг: Отжиг - это контролируемый процесс, который включает в себя нагрев материала до определенной температуры с последующим медленным охлаждением. Этот метод позволяет снять внутренние напряжения и может привести к повышению твердости. Важно тщательно управлять этим процессом, чтобы предотвратить коробление или деформацию детали.
Влияние толщины материала: При оценке этих методов упрочнения большое значение имеет глубина формовки. Более глубокие формы обычно требуют большего растяжения материала, что может привести к уменьшению толщины в этих областях. Такой эффект утонения может привести к увеличению гибкости, что может свести на нет все усилия по упрочнению. Поэтому очень важно оценивать методы упрочнения с учетом этих изменений толщины, чтобы конечный продукт отвечал своим функциональным требованиям.
Каждый метод повышения твердости имеет свои преимущества и недостатки. Выбор наиболее подходящего процесса зависит от конкретной области применения и желаемых эксплуатационных характеристик термоформованного компонента.
Как проверяется качество термоформованных листов?
Чтобы гарантировать качество термоформованных листов, используются различные методы испытаний, каждый из которых сосредоточен на различных характеристиках материала. Вот основные методы испытаний:
- Визуальный осмотр:
Первоначальная проверка включает в себя поиск поверхностных дефектов, таких как царапины, пузырьки или обесцвечивание.
- Измерение толщины:
С помощью штангенциркуля или микрометра измеряют толщину листа в нескольких точках, чтобы убедиться в ее равномерности.
- Механические испытания:
- Тест на прочность на разрыв: этот тест оценивает, насколько хорошо материал выдерживает растягивающие усилия.
- Испытание на прочность при изгибе: оценивается способность материала сопротивляться изгибу.
- Тест на ударопрочность: измеряет прочность листа при внезапных ударах.
- Испытание на термостойкость:
В ходе этой процедуры проверяется работоспособность материала при более высоких температурах, что позволяет убедиться в сохранении его свойств без деформации.
- Испытание на стабильность размеров:
При этом оценивается, насколько сильно материал сжимается или деформируется под воздействием различных условий окружающей среды, например, тепла или влажности.
- Испытание на химическую стойкость:
Этот тест оценивает способность материала выдерживать воздействие различных химических веществ без разрушения.
- Тест на поверхностную энергию:
Поверхностная энергия измеряется, чтобы определить, насколько материал подходит для склеивания, печати или нанесения покрытия.
- Тест на прозрачность и ясность:
Для прозрачных или полупрозрачных листов оценивается оптическая чистота и светопропускные свойства.
- Тест на барьерные свойства:
Этот метод позволяет определить эффективность защиты листа от газов и влаги, что очень важно для упаковки.
- Испытание на адгезию:
Это определяет, насколько хорошо покрытия или отпечатки прилипают к поверхности листа.
Как материал переходит от гранулы на хлопья?
Подготовка материалов:
Выберите подходящие пластиковые гранулы, обычно включающие полистирол (PS), полипропилен (PP) и полиэтилентерефталат (PET). Убедитесь, что материал высушен для удаления влаги, что позволит избежать образования пузырьков или дефектов при нагревании.
Процесс экструзии:
Кормление:
Пластиковые гранулы подаются в бункер экструдера под действием силы тяжести или механическим способом (например, шнековым конвейером). Бункер обычно оснащен датчиками для контроля скорости подачи, что обеспечивает стабильность подачи.
Нагревание и плавление:
Экструдер имеет несколько зон нагрева, постепенно повышающих температуру. Каждая зона может регулироваться независимо, чтобы соответствовать характеристикам плавления различных материалов. Расплавленный пластик проталкивается шнеком через эти зоны, достигая однородного расплавленного состояния.
Микширование:
Конструкция шнека (глубина, шаг и форма) играет решающую роль в смешивании, обеспечивая равномерное распределение добавок (например, цветных маточных смесей, антиоксидантов и т. д.) по основному материалу, предотвращая несовместимость материала.
Экструзия:
Расплавленный пластик экструдируется через фильеру, образуя непрерывный лист. Конструкция фильеры определяет ширину и толщину листа, обычно используется плоская фильера.
Во время экструзии для обеспечения однородности листа необходимо поддерживать соответствующее давление и температуру.
Охлаждение и затвердевание:
Горячий лист сразу же попадает в охлаждающее устройство, обычно это охлаждающие валки или водяная баня. Охлаждающие валки используют водяное или воздушное охлаждение для быстрого снижения температуры листа, предотвращая его деформацию.
Процесс охлаждения можно регулировать, чтобы контролировать скорость охлаждения, обеспечивая равномерную толщину и застывание листа.
Резка и намотка:
Охлажденный лист может быть свернут в рулоны или разрезан на части определенной длины и ширины. Резка обычно выполняется автоматически с помощью ножей для обеспечения ровных краев.
Термоформование:
Отопление:
Нарезанные листы помещаются в термоформовочную машину, где они нагреваются до состояния размягчения с помощью инфракрасного или конвекционного нагрева, обычно в диапазоне от 160 до 200°C.
Формирование:
Размягченный лист помещают в форму, где он плотно прилегает к форме с помощью вакуумного формования (путем удаления воздуха из формы) или прессования (путем подачи давления воздуха).
Во время формовки лист закрепляется в форме, чтобы обеспечить точное формирование.
Охлаждение и формовка:
Сформированный лист охлаждается, обычно с помощью воды или воздуха. После охлаждения конечный продукт извлекается из формы.
Постобработка:
Готовые изделия подвергаются обрезке, перфорации или другой последующей обработке, чтобы соответствовать конкретным требованиям. На некоторых изделиях может потребоваться печать или другие украшения.
Проверка качества:
Наконец, готовый продукт проходит всестороннюю проверку качества, включая измерение размеров, визуальный осмотр и тестирование физических свойств, что гарантирует соответствие спецификациям и стандартам.
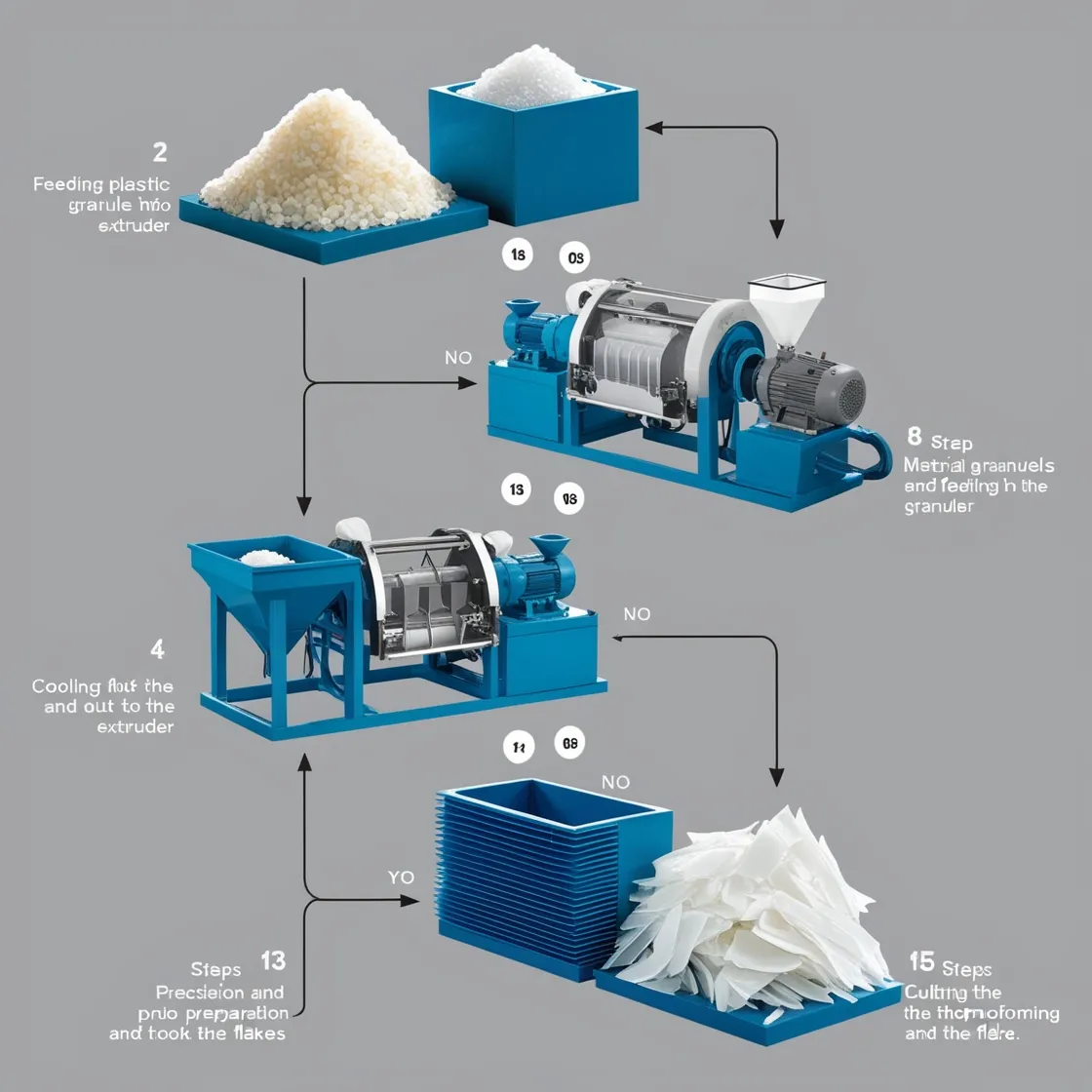
Освоение термоформованных листов: Как толщина материала влияет на качество и функциональность
Если вы рассматриваете вариант термоформовки для своего проекта, обратите внимание: термоформованные листы бывают разной толщины. Это связано с тем, что этот универсальный процесс может использоваться для изготовления всего: от упаковки для пищевых продуктов (например, стаканчиков для йогурта) до дверных панелей автомобилей. И для разных продуктов часто требуется разная толщина материала.
Хотите, чтобы ваши термоформованные изделия выглядели великолепно и работали безупречно? Вы можете не задумываться о том, какой толщины должен быть пластиковый лист, когда вы придаете ему форму. Он не может быть слишком тонким или слишком толстым, если вы хотите добиться идеального результата. Мы расскажем вам все, что нужно знать о выборе оптимального калибра (так измеряется толщина) для успешной термоформовки, будь то красивая упаковка, демонстрирующая ваши дизайнерские способности, или прочные детали автомобиля, которые не сломаются в самый нужный момент. В этом блоге вы узнаете, как выбрать правильный калибр пластикового материала, чтобы достичь максимальной функциональности, формы и эстетики в ваших термоформованных изделиях.
Роль толщины материала при термоформовании
Свойства термоформованного изделия зависят от его толщины. Это касается как прочности и устойчивости к повреждениям, так и качества поверхности и даже веса. Знание того, какой диапазон толщины лучше всего подходит для этих факторов, очень важно, если вы хотите, чтобы ваши изделия были качественными, а также если вы хотите сделать их экономически выгодными с помощью термоформования!
Структурная целостность и ударопрочность
Более толстые листы обеспечивают усиленную структурную поддержку и повышенную устойчивость к ударам, что делает их подходящими для изделий, требующих долговечности, например, корпусов для электронных устройств или защитных крышек для машин.
Качество поверхности
Такие предметы, как электроника или упаковка, выглядят лучше, если они имеют тонкую отделку. Для этого в термоформовке используются материалы, которые можно превратить в гладкие поверхности без дорогостоящей полировки - иногда с помощью очень тонких листов материала.
Весовые соображения
Многие отрасли промышленности предпочитают легкие изделия, потому что их дешевле перевозить, они потребляют меньше топлива и ими легче управлять. Используя более тонкие листы или материалы, которые при этом остаются достаточно прочными, чтобы не ломаться и не рассыпаться, производители могут изготавливать конечные продукты, которые весят гораздо меньше.
Максимальная толщина листа
Толщина термоформованных листов обычно не превышает 0,5 дюйма (12,7 мм). Однако такая толщина встречается реже. Как правило, она используется для тяжелых работ, требующих особо прочных деталей: например, автомобильных деталей, элементов крупного оборудования и корпусов некоторых приборов. Термоформовочные листы такой толщины обычно называют толстолистовой термоформовкой.
Бывают случаи, когда термоформовка требует использования максимально толстого пластикового материала. Это особенно актуально для некоторых изделий, которые должны быть прочными или иметь большую глубину. Вот почему вы можете выбрать более толстый пластик - и какие преимущества он может дать.
- Термоформование глубокой вытяжкой
Если вы хотите сделать большие пластиковые изделия с помощью техники глубокой вытяжки - и такие, которые не будут истончаться или расслаиваться при формовке, - вам понадобится много материала и пластиковые листы большой толщины.
- Промышленные компоненты для тяжелых условий эксплуатации
Если вам нужны компоненты, способные выдерживать жесткие промышленные условия, вам определенно нужны компоненты, изготовленные из толстостенных материалов. Эти материалы обеспечивают непревзойденную долговечность - они противостоят повреждениям и износу от грубой эксплуатации гораздо лучше, чем другие типы.
- Крупногабаритные изделия
Для таких изделий, как ванны, вкладыши для постели грузовиков и специальные автомобильные детали, требуется более толстый пластик, чтобы он хорошо держался при эксплуатации - особенно на больших площадях - и продолжал исправно работать.
Минимальная толщина
С другой стороны, тонкие листы могут достигать 0,014 дюйма (0,35 мм) при термоформовке тонколистового материала, который часто используется для изготовления одноразовых стаканчиков, крышек, лотков, контейнеров и других упаковочных изделий. Быстрое производство и экономичность в использовании материалов являются преимуществами тонколистовой термоформовки, что важно для такой отрасли, как производство упаковки, которая в значительной степени ориентирована на получение прибыли.
Откройте для себя искусство и эффективность тонкостенного термоформованияОзнакомьтесь с тем, как эта техника позволяет производителям изготавливать тонкие, детализированные изделия с высокой точностью - и при этом экономить деньги.
Минимальная толщина материала: Утонение для точности
- Экономия средств
Более тонкие листы позволяют сэкономить деньги на их покупке, а также сократить время на нагрев листов и придание им формы - таким образом, вы расходуете меньше энергии на эту часть процесса, и продукция также изготавливается быстрее.
- Детализированные и сложные формы
Если вам нужны замысловатые конструкции и мелкие детали, вам подойдут тонколистовые материалы. Они лучше передают нюансы поверхности пресс-формы и инструмента, а значит, позволяют получить высокодетализированные изделия, которые к тому же хорошо выглядят.
- Гибкая упаковка
Тонкостенная термоформовка сыграла важную роль в росте популярности гибкой, прозрачной упаковки в пищевой, розничной и медицинской промышленности. Этот тип материала обеспечивает отличный барьер для защиты продукции, а также хорошую видимость для потребителей.
Факторы, влияющие на выбор толщины
Толщина термоформованного изделия определяется несколькими факторами, в том числе:
Требования к прочности: Более тяжелые и прочные предметы требуют более толстого пластика.
Потребности в гибкости: Гибкие изделия, например, некоторые виды упаковки, могут выиграть от использования более тонких материалов.
Контуры пресс-формы: Сложность и глубина формы может потребовать корректировки толщины пластикового материала для достижения желаемой детализации и структурной целостности.
Тип материала: Различные пластики имеют разные характеристики прочности и гибкости, что может повлиять на оптимальную толщину для конкретного применения. Обычно используются такие материалы, как ABS, полистирол, полиэтилен и ПВХ.