คำอธิบายโดยละเอียดของเทคโนโลยีการขึ้นรูปพลาสติกใสด้วยความร้อน: การเลือกวัสดุ การไหลของกระบวนการ และขอบเขตการใช้งาน
Introduction
Transparent plastics are popular for their high transparency, good mechanical properties and wide application fields. Among the many molding methods, thermoforming is an important and better technology, especially suitable for the production of transparent plastic products with large size and complex shape. This article will introduce the thermoforming process of transparent plastics in detail, including its technical principles, material selection, process flow, application fields and advantages.
Thermoforming technology principle
Thermoforming is a process that softens the plastic sheet by heating it and then molding it on the mold. This process can be divided into the following main types:
·Vacuum forming
Vacuum forming is one of the most common thermoforming methods. The heated plastic sheet is pulled onto the mold and vacuumed to make it close to the mold surface to form the desired shape. This method is suitable for the production of various transparent plastic products with thin thickness and shallow depth.
·Pressure forming
Pressure forming adds air pressure on the basis of vacuum forming, so that the plastic sheet fits the mold more closely, which is suitable for plastic products with more complex and fine structures. This method is often used to make transparent plastic parts that require high precision and detail.
·Double-sheet molding
Double-sheet molding uses two molds to sandwich the heated plastic sheet in the middle and form the product through double-sided pressure. This method is suitable for producing large, deep transparent plastic products.
Transparent plastic material selection
The material selection of transparent plastic is crucial to the molding quality and final product performance. Commonly used transparent plastic materials include:
·Polyethylene terephthalate (PET)
PET has excellent transparency, strength and chemical resistance and is widely used in food and pharmaceutical packaging. Its good processing properties make it an ideal material for thermoforming.
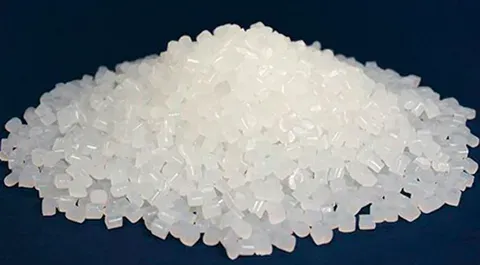
·Polylactic acid (PLA)
PLA is a biodegradable plastic with good transparency and biocompatibility, suitable for environmentally friendly packaging and disposables. PLA is increasingly popular due to its excellent thermoforming properties and environmental friendliness.
·Polypropylene (PP)
PP is a plastic with high transparency and excellent chemical properties, suitable for medical devices and food packaging. PP has excellent thermoforming properties and its low density makes it an ideal choice for lightweight products.
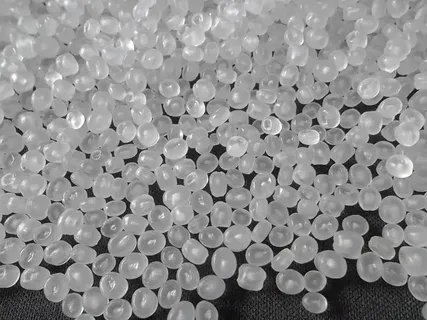
Thermoforming process
The thermoforming process of transparent plastics includes the following key steps:
·Material preparation
Select the appropriate transparent plastic sheet according to the product requirements and ensure that its surface is free of scratches and contaminants to ensure the molding quality of the finished product.
·Heating
The plastic sheet is heated to its softening temperature, which varies for different materials. The heating method can be infrared heating, convection heating or contact heating.
·Molding
The heated plastic sheet is placed on the mold and molded by vacuum, pressure or double-sheet molding. This step requires strict control to ensure that the plastic is evenly distributed and to avoid bubbles and stretch marks.
·Cooling
The molded plastic products need to be cooled quickly to solidify their shape. The cooling method can be natural cooling, air cooling or water cooling.
·Trimming and processing
Remove the excess plastic corners and perform necessary trimming and post-processing on the products, such as punching, polishing and printing.
Application areas of transparent plastic thermoforming
Transparent plastic thermoforming has a wide range of applications in multiple industries, mainly including:
·Packaging industry
Transparent plastics are widely used in the packaging of food, medicine and cosmetics. The thermoforming process can effectively produce packaging containers with complex shapes and high transparency.
·Medical devices
Transparent plastics are increasingly used in medical devices, especially in disposable diagnostic equipment and drug packaging. The thermoforming process can ensure the sterility and transparency of the products.
·Building decoration
Transparent plastics such as PC are widely used in building decoration. Thermoforming process can produce transparent decorative panels of various shapes for ceilings, walls and light boxes.
·Electronics
Transparent plastics are commonly used in electronic products for display screens, touch panels and protective covers. Thermoforming technology enables the manufacture of transparent parts with high precision and complex shapes.
·Automotive industry
In the automotive industry, transparent plastics are used to manufacture headlight covers, dashboards and interior trims. Thermoforming technology ensures the high transparency and durability of these parts.
Advantages of Thermoformed Transparent Plastics
Thermoformed transparent plastics have many significant advantages:
·High transparency
Thermoforming technology of transparent plastics can maintain the high transparency of the material, making it widely used in products that require good visual effects.
·Design flexibility
Thermoforming technology can produce complex and diverse shapes to meet various design requirements and adapt to applications in different industries.
·Cost-effectiveness
Compared with injection molding, thermoforming has lower mold costs, which is particularly suitable for small and medium-sized batch production and reduces manufacturing costs.
·Production efficiency
Thermoforming has a short production cycle, can quickly respond to market demand, and improve production efficiency.
·Environmental protection
Many transparent plastics, such as PET and PLA, can be recycled, and the thermoforming process can also reduce material waste and has good environmental protection.
Conclusion
Thermoforming of transparent plastics is widely used in many industries because of its high efficiency, flexibility and cost-effectiveness. By correctly selecting materials, optimizing process flow and strictly controlling production conditions, manufacturers can produce high-quality transparent plastic products to meet the diverse needs of the market. With the continuous advancement of technology, the transparent plastic thermoforming process will play its advantages in more fields and bring more possibilities for future development.