Introduction
Multi-station thermoforming machine plays a vital role in modern manufacturing, especially in the field of plastic products. Its integrated multiple process steps can efficiently process plastic materials into various required shapes and structures. Punching and shearing station, as one of the key steps, plays an irreplaceable role. This article will discuss the punching and shearing station in multi-station thermoforming machine in detail, analyze its importance and specific role in precision manufacturing, especially the impact on plastic products.
Definition and principle of punching and shearing station
The punching and shearing station is a key station in multi-station thermoforming machine, and its main function is to shear the formed plastic sheet. Unlike the punching process, the punching and shearing process focuses on accurately cutting the finished product out of the plastic sheet. Its working principle can be summarized as follows: after the plastic sheet is thermoformed in the forming station, it enters the punching and shearing station, where it is precisely positioned by the punching and shearing die, and then the plastic sheet is cut into the required shape by the high-pressure shearing machine. The whole process requires extremely high precision and stability to ensure that the size and shape of the final product meet the design requirements.
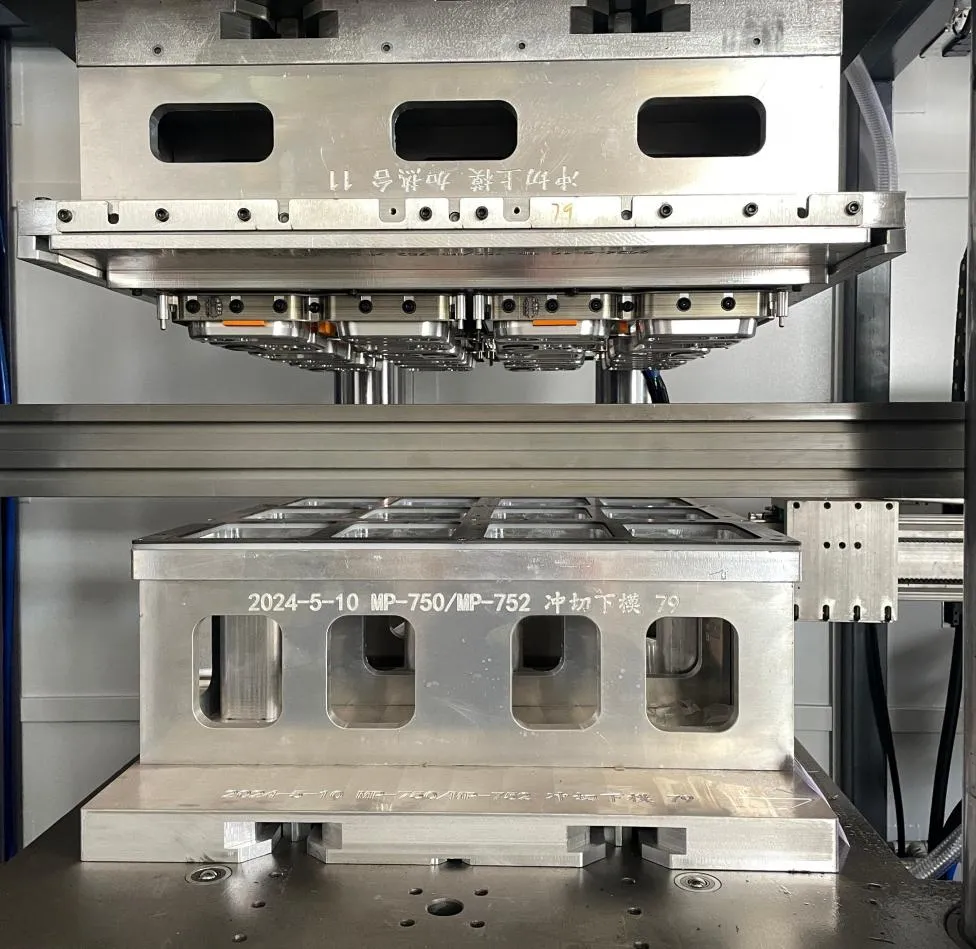
Importance of Punching and Shearing Stations
1. Precision and consistency: Punching and shearing stations play a decisive role in the entire production process, and their precision directly affects the quality of the final product. Through precise punching and shearing processes, it can be ensured that the size and shape of each product meet the design specifications, thereby improving product consistency.
2. Production efficiency: The punching and shearing stations of multi-station thermoforming machines can achieve efficient automated production, reducing the errors and time of manual operation. Efficient punching and shearing processes can greatly improve production efficiency and reduce production costs.
3.Material utilization: Through optimized punching and shearing die design, raw materials can be maximized, waste generation can be reduced, and material utilization can be improved. This not only reduces production costs, but also has important environmental significance.
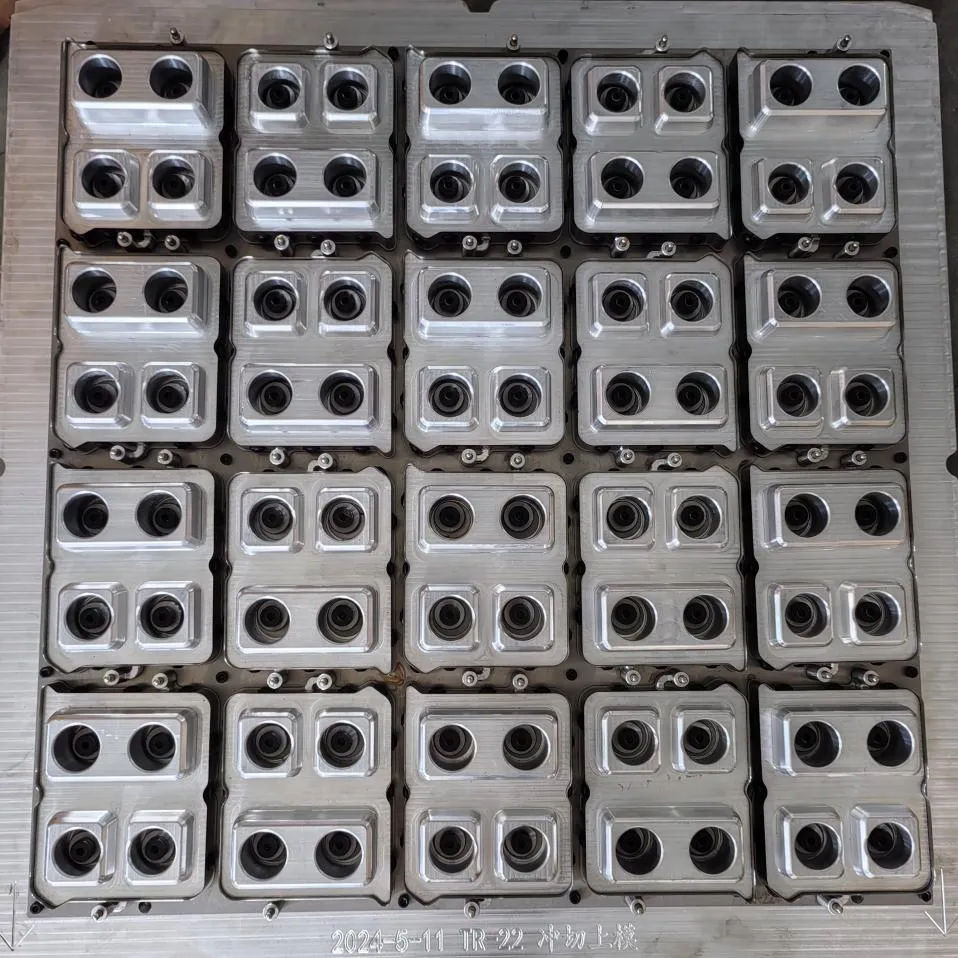
Specific functions of the punching and shearing station
Shearing
Shearing is the basic function of the punching and shearing station, which is mainly used to cut the formed plastic sheet into the required shape. The shearing process usually includes the following steps:
· Positioning: accurately position the thermoformed plastic sheet on the punching and shearing die.
· Clamping: fix the plastic sheet through the clamping device to prevent it from moving during the shearing process.
· Shearing: cut the plastic sheet with a shear knife or die.
The shearing process requires extremely high precision, especially when producing high-precision plastic products, the shearing error must be controlled within the micron level. Through the precise shearing process, it can be ensured that the size and shape of the final product meet the design requirements.
Application of punching and shearing stations in plastic products
1. Lunch box manufacturing
In the manufacturing of lunch boxes, the punching and shearing stations of multi-station thermoforming machines are widely used in the production of various lunch boxes, such as fast food boxes, take-out boxes, etc. These lunch boxes require high precision and complex structures. Through precise punching and shearing processes, high-quality lunch boxes that meet the design requirements can be produced, thereby improving the overall performance and durability of the product.
During the production process of lunch boxes, plastic sheets are heated and formed into the basic shape of lunch boxes at the forming station, and then enter the punching and shearing station for precise shearing. Through precise positioning and high-pressure shearing, the size and shape of each lunch box are ensured to be consistent, and the edges are neat and smooth, which will not affect the user experience.
2. Disposable packaging
In the disposable packaging industry, the punching and shearing stations of multi-station thermoforming machines are widely used in the production of various disposable plastic packaging products, such as food packaging containers, beverage cups, and pharmaceutical packaging. These packaging products require high precision and complex structures. Through precise punching and shearing processes, high-quality packaging products that meet the design requirements can be produced, thereby improving the overall quality and market competitiveness of the products.
During the production of disposable packaging, plastic sheets are heated and formed into the required packaging container shape in the forming station, and then enter the punching and shearing station for shearing. Through precise shearing, the size and shape of each packaging container are ensured to meet the design requirements, the edges are neat, and there will be no burrs or irregular cuts, ensuring the beauty and practicality of the packaging.
Advantages of the punching and shearing station
1. High precision
A significant advantage of the punching and shearing station is its high-precision shearing ability. Disposable plastic products, such as lunch boxes and packaging containers, require very high precision in size and shape to ensure the practicality and beauty of the product. Through precise molds and advanced automatic control systems, the punching and shearing station can achieve extremely high shearing accuracy to ensure that the size and shape of each product meet the design requirements.
2. Efficient production
The punching and shearing station of the multi-station thermoforming machine can greatly improve production efficiency. Compared with traditional manual shearing or simple mechanical shearing, the punching and shearing station has a higher degree of automation and can complete the shearing of a large number of disposable plastic products in a short time. This can significantly reduce production costs and improve market competitiveness for enterprises that mass-produce disposable plastic products.
3. Material saving
Through precise punching and shearing processes, material waste can be minimized. Traditional shearing methods often produce a large amount of scraps, while punching and shearing stations can minimize waste through optimized mold design and precise shearing control. This not only helps to reduce material costs, but also has important environmental significance and meets the requirements of modern enterprises for sustainable development.
4. Diversified production
The punching and shearing station can adapt to the shearing needs of disposable plastic products of different shapes and sizes. This flexibility allows shearing companies to quickly adjust production lines according to market demand and produce diversified plastic products. For example, in the lunch box manufacturing industry, lunch boxes of different sizes and shapes can be quickly produced by replacing molds to meet the needs of different customers. Similarly, in the production of disposable beverage cups and food containers, diversified product production can also be achieved by adjusting mold design.
Challenges and solutions of punching and shearing stations
Although punching and shearing stations have many advantages in the manufacture of plastic products, they also face some challenges. For example, high-precision shearing requirements place high demands on the manufacturing process of molds and equipment. In addition, the heat generated during the punching and shearing process may cause deformation and quality degradation of plastic sheets.
To address these challenges, the following measures can be taken:
1. Mold optimization
By optimizing the design and manufacturing process of the mold, the accuracy and durability of the punching and shearing stations can be improved. For example, using high-strength alloy materials to manufacture the mold, and performing precision machining and heat treatment, the hardness and wear resistance of the mold can be improved, thereby extending the service life of the mold and ensuring the shearing accuracy.
2. Cooling system
The introduction of an efficient cooling system can effectively control the temperature during the punching and shearing process and reduce the deformation of the plastic sheet. Water cooling or air cooling technology can quickly reduce the temperature of the shearing area, maintain the stability of the plastic sheet, and improve the shearing quality.
3. Automated control
Advanced automated control systems can be used to achieve real-time monitoring and precise control of the punching and shearing process. For example, CNC technology can accurately control the motion trajectory and force of the shearing tool to ensure the accuracy and consistency of each shearing. In addition, intelligent sensors can monitor various parameters in the shearing process, such as temperature, pressure, etc. in real time, and adjust process parameters in time to ensure the stability of the production process.