In thermoforming, mold selection is central to achieving desired product quality, precision, and manufacturing efficiency. The two primary types of molds—male (positive) and female (negative) molds—each impart unique benefits and limitations, making them suited to specific applications within thermoforming. This guide provides an in-depth comparison of these molds to help manufacturers optimize their process and product quality.
Understanding Male (Positive) and Female (Negative) Molds in Thermoforming
Molds in thermoforming determine the shape and structural precision of the final product by providing a framework for shaping heated plastic sheets. Male molds, or positive molds, are convex in shape, with the plastic formed around the mold’s exterior. Conversely, female molds, or negative molds, are concave, with the plastic shaped by pressing into the mold’s cavity. Both mold types affect the product’s dimensional accuracy, wall thickness distribution, and surface finish.
Male (Positive) Molds: Inner Dimensional Precision with Some Limitations
Male molds, also referred to as positive molds, consist of a convex shape. In this process, a heated plastic sheet is drawn tightly against the mold’s outer surface using either vacuum or air pressure. Due to this setup, the inner surface of the plastic directly contacts the mold, which results in high precision for the product’s internal dimensions.
This inner dimensional accuracy makes male molds ideal for applications requiring strict internal measurements, such as specific containers or specialized packaging solutions. However, a limitation of male molds is the uneven thickness distribution across the product’s surface. Thickness tends to be greater at the top of the mold and thinner at intersections between the sides and bottom, especially in deeper products. This variation can affect the durability and strength of the final product.
Female (Negative) Molds: External Precision and Uniform Thickness
Female molds, or negative molds, are concave in design. During thermoforming, heated plastic sheets are suctioned into the mold cavity, allowing the plastic to conform tightly to the mold’s inner surface. This technique prioritizes the precision of the product’s outer dimensions, making female molds an excellent choice for items that require precise external measurements, like food packaging trays or protective casings.
Female molds provide a more uniform wall thickness, which is advantageous for products with complex shapes or greater depths. Additionally, female molds yield finer surface details and higher surface quality due to direct outer surface contact with the mold, making them suitable for applications where appearance is a priority.
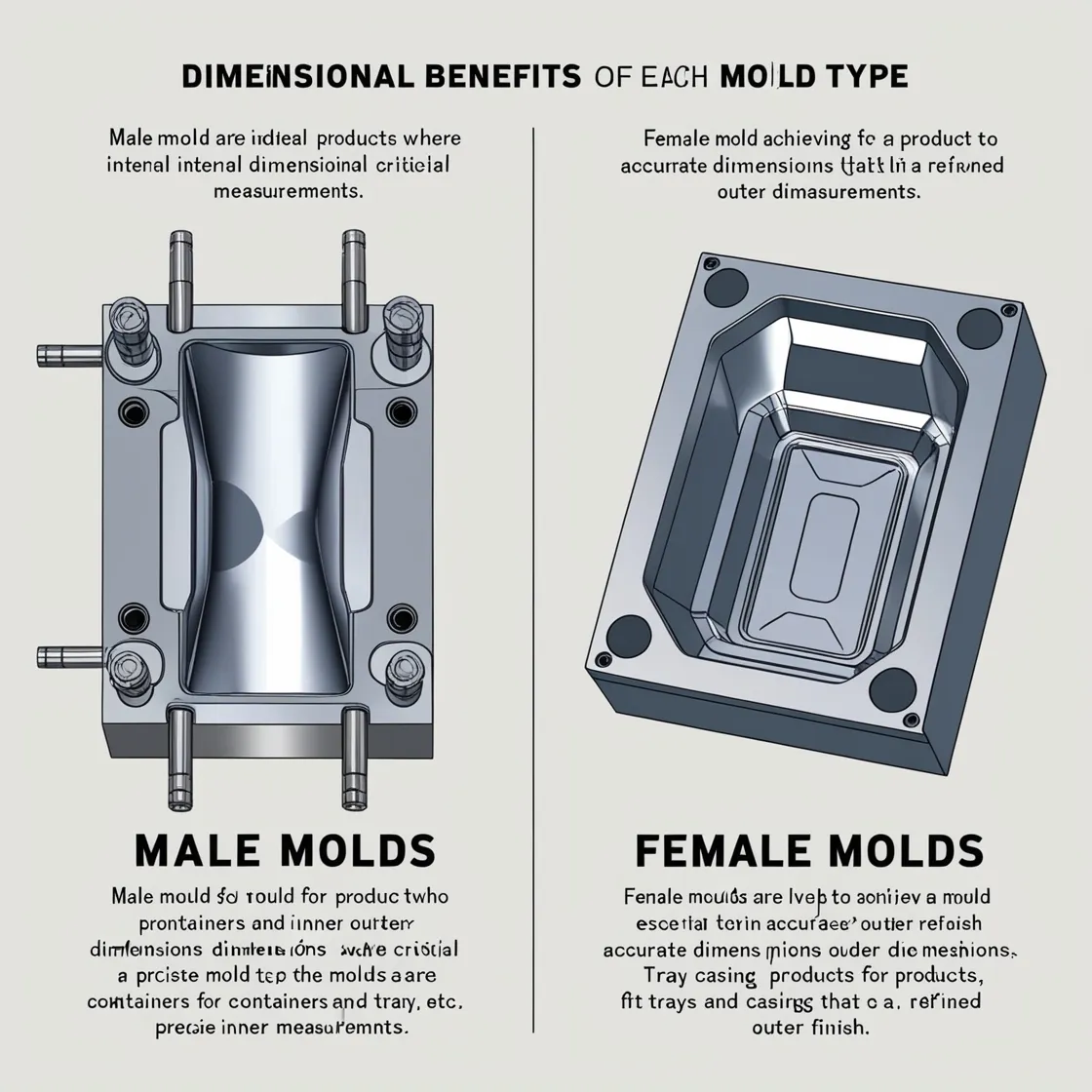
Comparing Dimensional Precision and Wall Thickness Distribution
Both male and female molds serve distinct purposes in dimensional precision, wall thickness distribution, and applications.
Dimensional Precision
– Male Molds (Positive Molds): Deliver high internal dimensional accuracy due to the direct contact between the inner surface of the plastic and the mold. This precision is beneficial for products that need exact internal structures.
– Female Molds (Negative Molds): Provide high external dimensional accuracy, with the outer surface of the product conforming to the mold. This is ideal for items with strict external measurement requirements.
Thickness Distribution
– Male Molds (Positive Molds): Typically produce products with thicker top sections and thinner intersections between the sides and bottom. This thickness distribution can be problematic, especially for products with significant depth.
– Female Molds (Negative Molds): Allow for more uniform wall thickness, which is essential for complex or deep designs.
Application Scenarios for Male and Female Molds
Choosing between male and female molds largely depends on the intended application and product requirements.
– Male Molds: Suitable for applications that prioritize internal precision, like specialized containers and packaging solutions.
– Female Molds: Better suited for items requiring exact external measurements, such as food trays and aesthetic casings.
Advantages and Disadvantages of Positive (Male) and Negative (Female) Molds
Each mold type has specific advantages and disadvantages based on the process requirements and product specifications.
Advantages of Positive (Male) Molds
1. High Surface Finish: Positive molds create smoother surfaces, resulting in high-quality finishes that are ideal for products where aesthetics are important.
2. Lower Initial Investment: Male molds typically require less upfront investment in mold-making, and they tend to have a longer lifespan.
Disadvantages of Positive (Male) Molds
1. Pattern Detail Loss: In some cases, detailed patterns may become shallow or even disappear due to stretching during the molding process.
2. Simple Geometries Only: Male molds work best for products with simple shapes, as there are limitations regarding intricate patterns and corner radii.
3. Size Constraints: Male molds are less suited for larger workpieces due to difficulties in achieving uniform thickness and dimensional accuracy.
Advantages of Negative (Female) Molds
1. Reduced Mold-Making Costs: Negative molds often require lower costs for mold production and operational setup.
2. High-Quality Surface Patterns: They provide detailed surface patterns, making them ideal for complex designs that require a polished aesthetic.
3. Versatility for Large and Complex Parts: Negative molds are capable of accommodating larger-sized products and intricate workpiece designs.
Disadvantages of Negative (Female) Molds
1. Lower Material Utilization: Material waste can be higher with female molds, as more plastic is used to achieve uniform thickness.
2. Surface Quality Limitations: Products made with female molds may have surface quality issues due to variations in thickness or cooling inconsistencies.
3.Higher Investment Costs: Female molds generally require more significant equipment and investment costs due to their complexity.
Specific Considerations in the Production of Positive Molds
The design and production of positive molds require attention to specific aspects to maintain quality and functionality in the final product.
High Right Angles and Draw Line Wrinkles
Positive molds with pronounced right angles can lead to “draw line wrinkles” due to limited material flow around sharp corners. These wrinkles can compromise both appearance and function. To minimize this, mold designs should incorporate rounded edges or smooth transitions for uniform material distribution.
Cooling Streaks at Corners
Cooling streaks can appear at mold corners due to uneven cooling rates, impacting both the appearance and integrity of the finished product. This can be mitigated by enhancing the cooling system, ensuring even heat distribution throughout the mold to achieve a consistent surface finish.
Uneven Wall Thickness
Positive molds are prone to uneven wall thickness, particularly at the male edges. This variation can weaken product durability and reliability. Careful design and attention to wall thickness distribution can alleviate these issues.
Demolding Challenges
Insufficient sidewall slope can make demolding difficult, potentially causing product damage during removal. Incorporating adequate draft angles helps streamline demolding, preserving the product’s shape and surface quality.
Specific Considerations in the Production of Negative Molds
Similarly, female mold production requires attention to detail to ensure consistent product quality.
Edge Thickness Uniformity
Achieving uniform edge thickness is essential for maintaining product performance and structural integrity. Variations can lead to stress concentrations that weaken the product. Implementing precise manufacturing techniques and regular mold inspections can help maintain uniformity.
Monitoring Thin Corner Areas
Corners are especially susceptible to thinning during thermoforming, which can cause failure or perforation. Reinforcing these areas in the mold design and performing regular quality checks can prevent weak points in the final product.
Choosing Between Negative and Positive Molds in Thermoforming
Selecting a mold type depends on specific production requirements and workpiece characteristics.
– Negative Mold Thermoforming: For complex workpieces or larger products, negative molds are typically the better option. They accommodate intricate designs and large-scale applications, providing high detail and durability.
– Positive Mold Thermoforming: When focusing on simple geometries or superior surface quality, positive molds are preferable. They offer high efficiency and smoother finishes, making them suitable for applications where uniformity is critical.
Process Requirements in Thermoforming Mold Design
Demolding Slope
To facilitate smooth release, mold sides should have a specific inclination, or “demolding slope.” A greater angle increases efficiency and prevents deformation, improving overall cycle time. An inclination exceeding 1 degree is generally recommended for optimal results.
Aspect Ratio
The width-to-height ratio is critical in mold design. Male molds can allow slightly lower height-to-width ratios due to the pre-stretching effect, while female molds require a ratio of 1.4 or higher for efficiency.
Importance of Water Tightness Testing in Thermoforming Molds
Water tightness testing is essential for mold integrity, as it helps ensure optimal thickness distribution and durability in thermoformed parts.
1. Mold Preparation: The mold is sealed, leaving one access point for water entry. This setup prevents leaks during testing.
2. Filling and Pressure Testing: Water is gradually added, then pressurized to simulate operational conditions, revealing any potential weak points or flaws.
This testing is particularly crucial in high-impact polystyrene (HIPS) thermoforming, where even thickness distribution is essential for product strength and reliability. By conducting thorough water tightness testing, manufacturers can ensure mold integrity, avoiding inefficiencies and product failures.
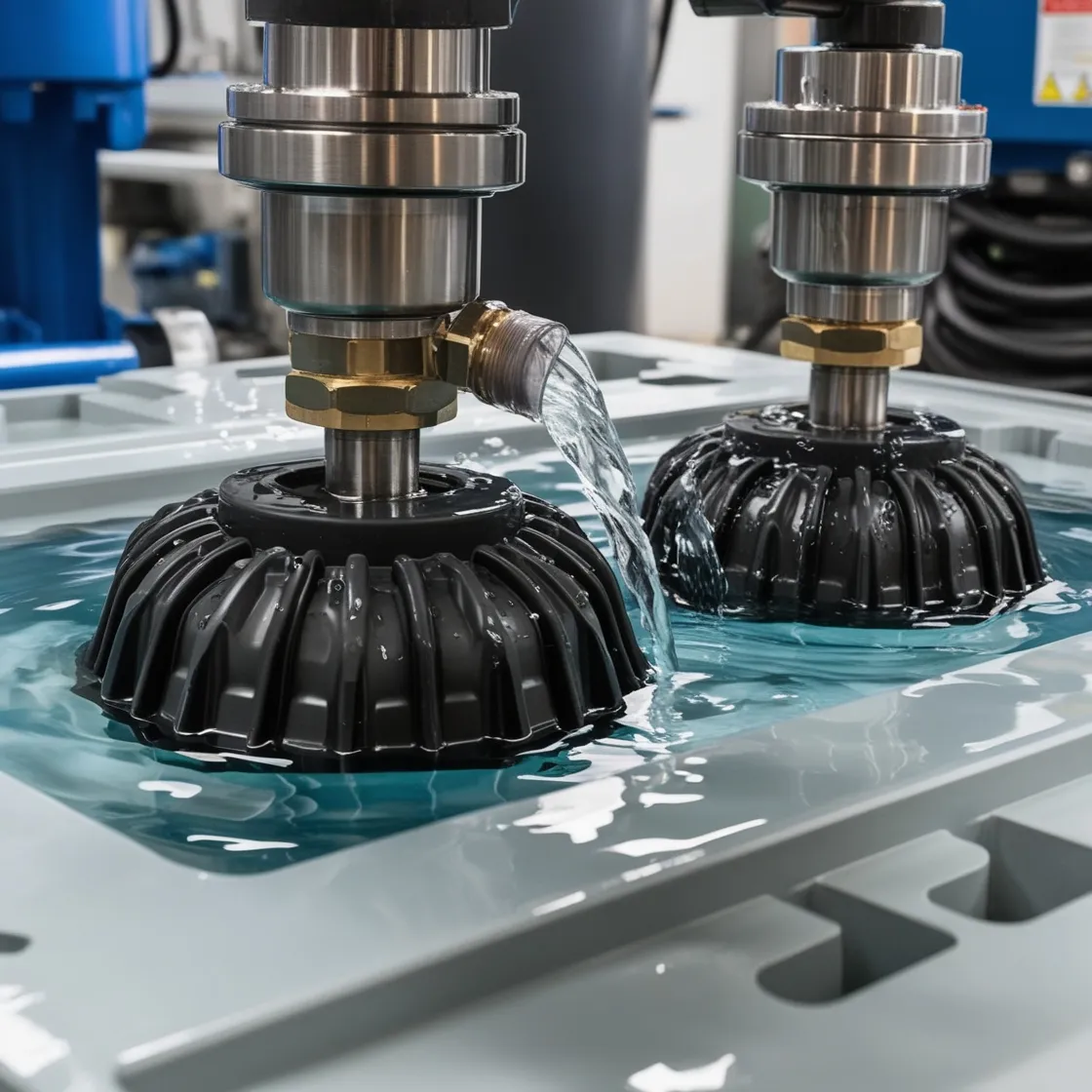
Conclusion
Choosing between positive and negative molds in thermoforming requires evaluating specific production needs and product characteristics. Both mold types offer unique benefits, and understanding their differences helps manufacturers optimize their processes. Through careful mold selection, companies can achieve consistent quality, improve efficiency, and reduce production costs in thermoforming.