What are the reasons for the variation of thickness in products formed by the thermoforming process?
Thermoforming is a flexible manufacturing technique that molds plastic films and sheets into various products, where thickness variation is crucial for both design and functionality.
Material Selection and Thickness: The type of plastic used significantly impacts the thickness of the final products. For instance:
Polystyrene (PS) Films: Typically utilized for clear disposable glasses, with thicknesses generally below 0.5 mm.
Polypropylene (PP) Sheets: Employed for colored glasses or Styrofoam containers, which usually have thicknesses exceeding 0.5 mm.
Product Programming: An important element of product design is Product Programming, which specifies the required thicknesses and dimensions for each application. In the case of bottles, this process is referred to as Parison Programming, a method first developed by Denes Hankar in Cincinnati.
Bottles and Thickness Variation: Take a soft drink bottle as an example: it features a thicker neck and base while the body remains thinner. This design serves essential purposes:
The neck requires additional thickness to create an airtight seal for proper capping.
The base needs to be thicker to provide the necessary weight and support for the bottle.
Thickness variations are critical for enhancing the performance of thermoformed products. For example, a uniform thickness in items like chemical tanks could lead to insufficient rigidity and stability. Thus, intentional variations in thickness are incorporated to ensure that each product meets its intended functional requirements effectively.
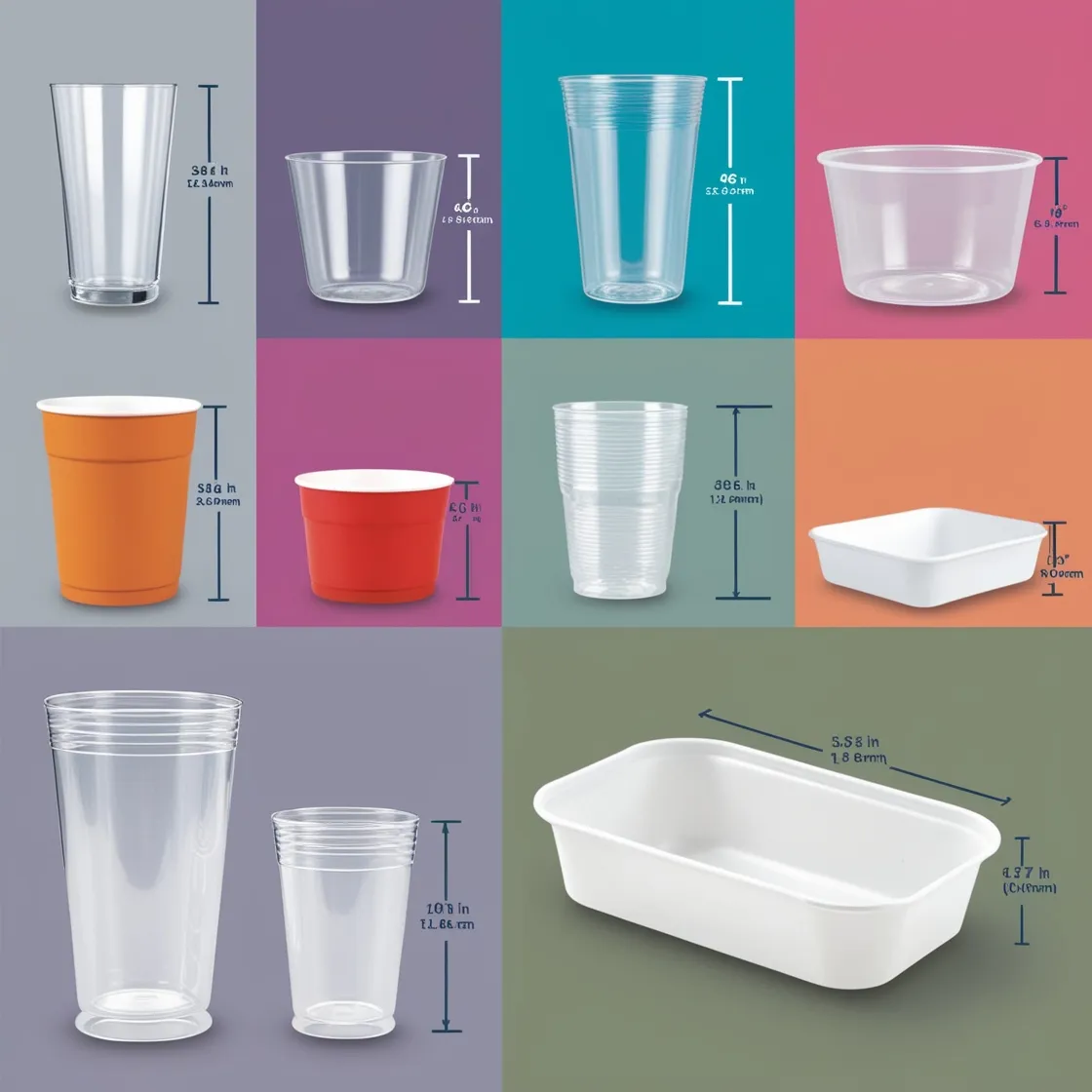
Strategies for Enhancing Hardness in Thermoformed PP and HDPE Products
Following the thermoforming process, there are several secondary techniques available to enhance the rigidity or impact strength of polypropylene (PP) and high-density polyethylene (HDPE). While these thermoplastic polymers retain their toughness and resistance to chemicals after shaping, the following methods can improve their hardness:
Chemical Crosslinking: A highly effective strategy is to apply chemical treatments that promote crosslinking within the polymers. This process involves forming bonds between polymer chains, creating a rigid network that enhances resistance to heat deformation.
Physical Aging: Another viable method is physical aging, which involves storing the thermoformed part at ambient or slightly elevated temperatures over an extended period. This allows the polymer chains to stabilize and increase in rigidity over time. However, this process can be gradual and may not deliver the desired hardness for all applications.
UV Stabilization: Exposure to ultraviolet (UV) radiation can also contribute to the hardening of PP and HDPE as a result of the stabilization process. The addition of UV stabilizers enhances the part’s resistance to weathering, and prolonged exposure can further lead to increased hardness.
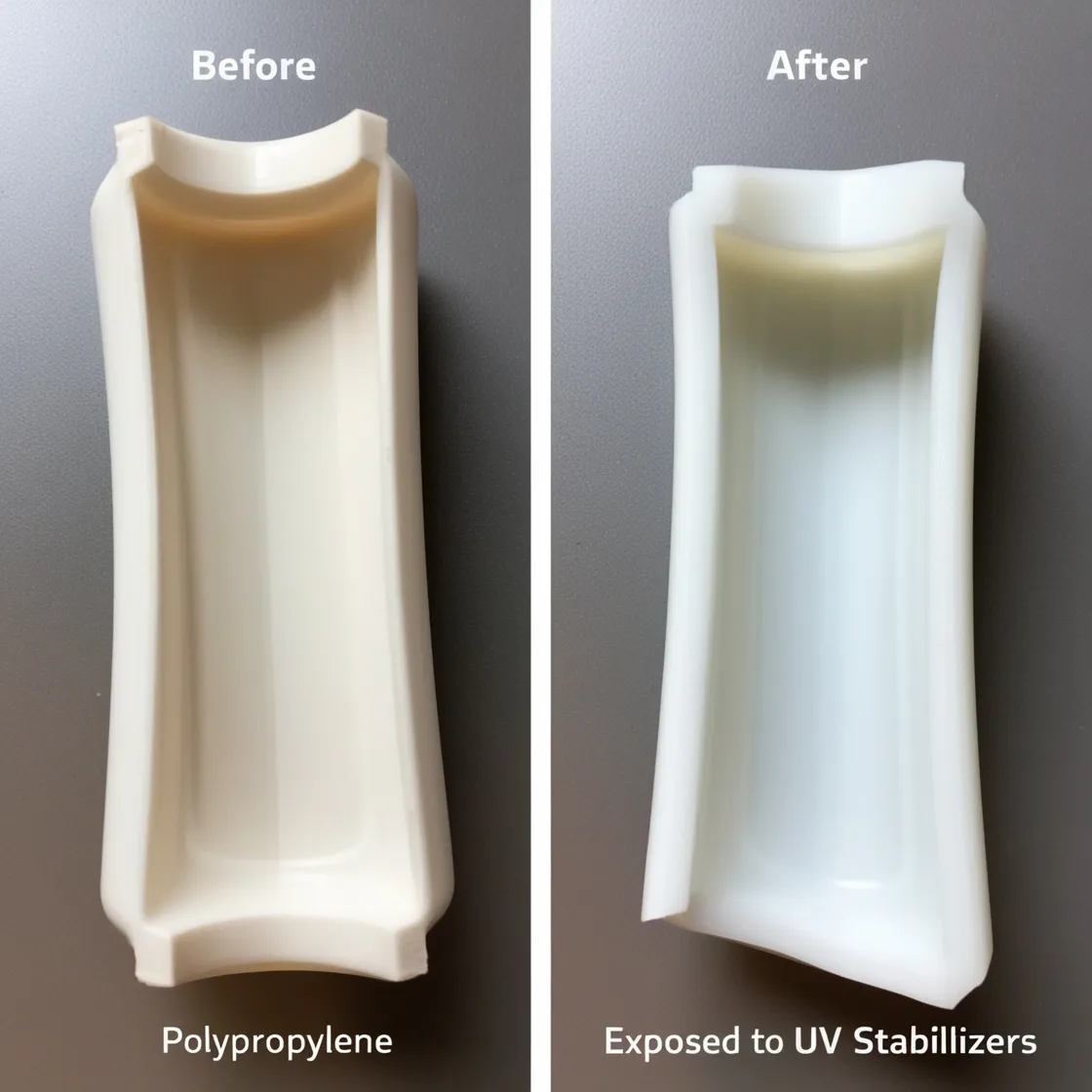
Post-Thermoforming Annealing: Annealing is a controlled process that involves heating the material to a specific temperature followed by a slow cooling phase. This method can relieve internal stresses and may result in greater hardness. It is essential to manage this process carefully to prevent warping or deformation of the part.
Influence of Material Thickness: When evaluating these hardening techniques, the depth of forming is a significant consideration. Deeper forms usually necessitate more stretching of the material, which can result in reduced thickness in those areas. This thinning effect might increase flexibility, potentially counteracting the intended hardening efforts. Therefore, it’s crucial to evaluate hardening methods while considering these thickness variations to ensure that the final product fulfills its functional requirements.
Each method for enhancing hardness has distinct advantages and drawbacks. The choice of the most appropriate process will be influenced by the specific application and the desired performance characteristics of the thermoformed component.
How is the quality of thermoformed sheets tested?
To guarantee the quality of thermoformed sheets, various testing techniques are utilized, each concentrating on different material attributes. Here are the primary Testing methods:
- Visual Inspection:
The initial check involves looking for surface flaws like scratches, bubbles, or discoloration.
- Thickness Measurement:
Calipers or micrometers are employed to measure the sheet’s thickness at several points to ensure it is uniform.
- Mechanical Testing:
– Tensile Strength Test:This test assesses how well the material can withstand pulling forces.
– Flexural Strength Test:This evaluates the material’s ability to resist bending.
– Impact Resistance Test:This measures the durability of the sheet when subjected to sudden impacts.
- Heat Resistance Test:
This procedure examines the material’s performance at higher temperatures, verifying that it retains its properties without warping.
- Dimensional Stability Test:
This assessment looks at how much the material shrinks or distorts under different environmental conditions, such as heat or humidity.
- Chemical Resistance Test:
This test evaluates the material’s capability to endure exposure to various chemicals without degradation.
- Surface Energy Test:
Surface energy is measured to determine how suitable the material is for bonding, printing, or coating.
- Transparency and Clarity Test:
For sheets that are clear or translucent, this evaluation assesses optical clarity and light transmission properties.
- Barrier Properties Test:
This method examines the sheet’s effectiveness against gases or moisture, which is vital for packaging purposes.
- Adhesion Testing:
This determines how well coatings or prints stick to the sheet’s surface.
How does the material go from granules to flakes?
Material Preparation:
Select suitable plastic granules, commonly including polystyrene (PS), polypropylene (PP), and polyethylene terephthalate (PET). Ensure the material is dried to remove moisture, preventing bubbles or defects during heating.
Extrusion Process:
Feeding:
Plastic granules are fed into the extruder’s hopper by gravity or mechanical conveyance (like a screw conveyor). The hopper typically has sensors to monitor the feed rate, ensuring stable feeding.
Heating and Melting:
The extruder has multiple heating zones, gradually increasing the temperature. Each zone can be independently controlled to suit the melting characteristics of different materials. The molten plastic is pushed through these zones by the screw, achieving a uniform molten state.
Mixing:
The screw design (such as depth, pitch, and shape) plays a crucial role in mixing, ensuring that additives (like color masterbatch, antioxidants, etc.) are evenly distributed throughout the base material, preventing material inconsistency.
Extrusion:
The molten plastic is extruded through a die, forming a continuous sheet. The die design determines the width and thickness of the sheet, typically using a flat die.
During extrusion, maintaining appropriate pressure and temperature is essential to ensure uniformity in the sheet.
Cooling and Solidification:
The hot sheet immediately enters a cooling device, usually cooling rolls or a water bath. Cooling rolls employ water or air cooling to rapidly lower the temperature of the sheet, preventing deformation.
The cooling process can be adjusted to control the cooling speed, ensuring uniform thickness and solidification of the sheet.
Cutting and Winding:
The cooled sheet can either be rolled into coils or cut into specific lengths and widths. Cutting is typically performed automatically with knives to ensure smooth edges.
Thermoforming:
Heating:
The cut sheets are placed in a thermoforming machine, where they are heated to a softening state using infrared or convection heating, typically between 160°C and 200°C.
Forming:
The softened sheet is placed in a mold, where it is tightly fitted to the mold shape using vacuum forming (by removing air from the mold) or pressure forming (by applying air pressure).
During forming, the sheet is secured in the mold to ensure accurate shaping.
Cooling and Demolding:
The formed sheet is cooled, usually using water or air to solidify. Once cooled, the final product is removed from the mold.
Post-processing:
The finished product undergoes trimming, punching, or other post-processing to meet specific application requirements. Some products may also require printing or other decorations.
Quality Inspection:
Finally, the finished product undergoes comprehensive quality inspection, including dimensional measurement, visual inspection, and physical property testing, ensuring compliance with specifications and standards.
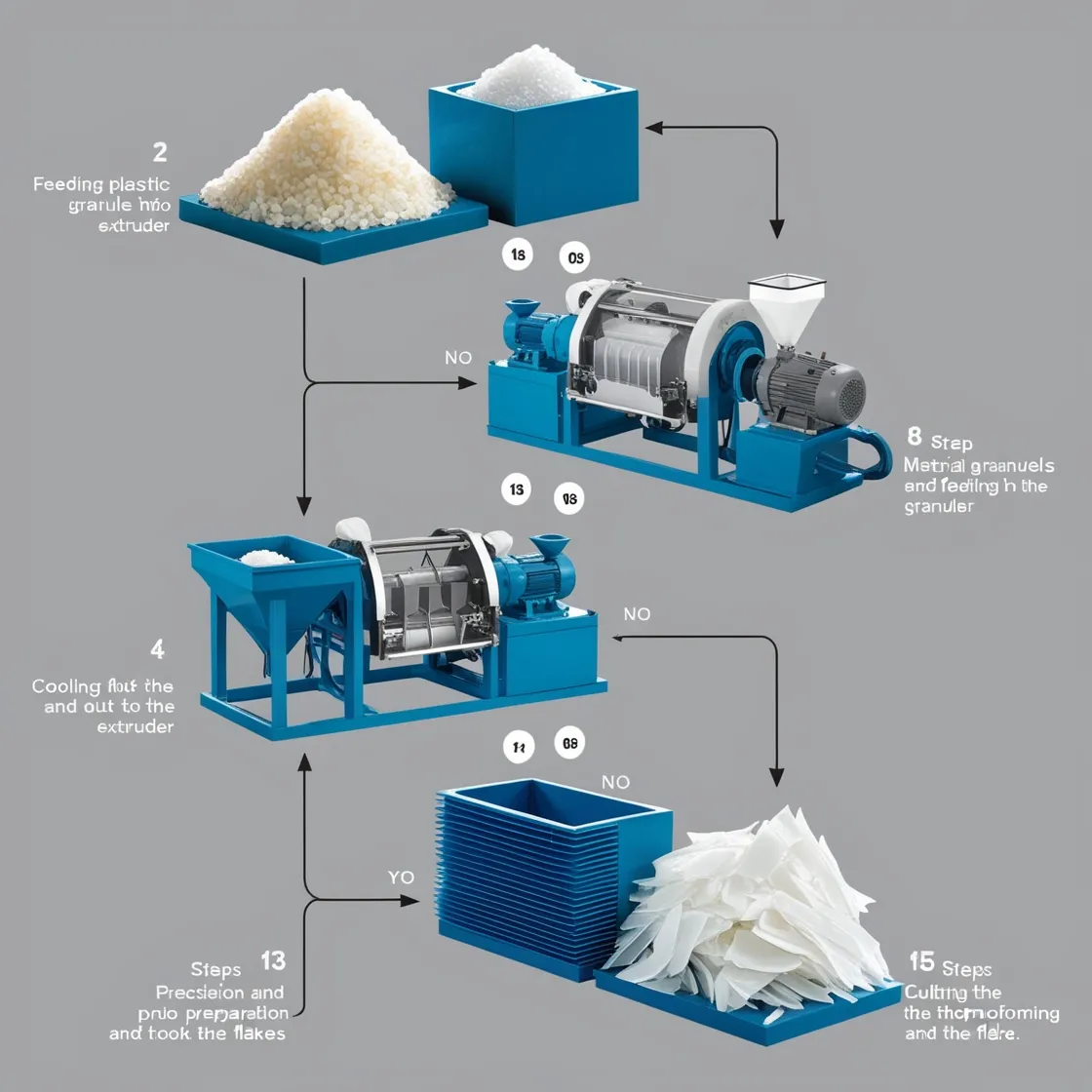
Mastering Thermoformed Sheets: How Material Thickness Impacts Quality and Functionality
If you’re considering thermoforming for your project, take note: thermoformed sheets come in many thicknesses. That’s because this versatile process can be used to make everything from food packaging (think: yogurt cups) to vehicle door panels. And different products often require different material thicknesses too.
Want to make sure your thermoformed products look great and work perfectly? One thing you might not think about is how thick the plastic sheet should be when you’re shaping it. It can’t be too thin or too thick if you want to get it just right. We’ll tell you everything you need to know about choosing the best gauge (that’s how thickness is measured) for successful thermoforming; whether you’re going for beautiful packaging that shows off your design skills or tough vehicle parts that won’t break when they’re needed most. In this blog, learn how to choose the right plastic material gauge to achieve peak functionality, form, and aesthetics in your thermoformed products.
The Role of Material Thickness in Thermoforming
The properties of a thermoformed product are influenced by its thickness. This includes everything from how strong and resistant to damage it is, through to the surface finish and even weight. Knowing what thickness range is best for these factors is important if you want your products to be good quality – but also if you want to make them economically using thermoforming!
Structural Integrity & Impact Resistance
Thicker sheets provide enhanced structural support and higher resistance to impacts, making them suitable for products that require durability, such as casings for electronic devices or protective covers for machinery.
Surface Quality
Items such as electronics or packaging look better if they have fine finishes. To achieve this, thermoforming use materials that can be made into smooth surfaces without lots of expensive polishing – sometimes by using very thin sheets of the material.
Weight Considerations
Many industries now prefer lightweight products because they are cheaper to transport, use less fuel and are easier to manage. By using thinner sheets or materials that are still strong enough – so they don’t break or fall apart – manufacturers can make final products that weigh much less.
Maximum Sheet Thickness
Thermoformed sheets are usually no thicker than 0. 5 inches (12. 7 mm). However, such thickness is less common. It tends to be for heavy-duty jobs needing extra-strong parts: think car bits, big machinery elements and some equipment housings. Thermoforming sheets of this thickness are generally referred to as thick-gauge thermoforming.
There are times when thermoforming requires using the thickest possible plastic material. This is especially true for certain products that need to be strong or have a lot of depth. Here’s why you might choose thicker plastic – and what advantages it can offer.
- Deep Draw Thermoforming
If you want to make big plastic items using deep-draw techniques – and ones that don’t have any thinning or split when you’re shaping them – you’ll need to use plenty of material and heavy gauge plastic sheets.
- Heavy-Duty Industrial Components
If you need components that can handle tough industrial conditions, you definitely want ones made from heavy-gauge materials. These materials provide unmatched durability—they resist damage and wear from rough use much better than other types do.
- Large-Scale Products
Products such as bathtubs, truck bed liners, and specific vehicle parts require thicker plastic in order to hold up well with use — particularly over large areas — and continue working correctly.
Minimum Thickness
On the other end of the spectrum, thermoformed sheets can be as slim as 0. 014 inches (0. 35 mm) during thin-gauge thermoforming—often used for disposable cups, lids, trays, containers, and other packaging items. Rapid production and cost-effectiveness through material usage are benefits to thin-gauge thermoforming; important considerations in an industry focused heavily on being profitable such as packaging.
Discover the Art and Efficiency of Thin-Gauge ThermoformingExplore how this technique allows manufacturers to craft delicate, detailed items with accuracy – all while saving money.
Minimum Material Thickness: Thinning for Precision
- Cost Savings
Thinner sheets save money on buying them and also mean that heated sheet and shaping takes less time – so you use less energy for this part of the process, and products get made more quickly as well.
- Detailed and Complex Shapes
If you’re looking for intricate designs and fine detail, thin-gauge materials are the way to go. These can better capture the nuances of a mold and tool surface—meaning they produce highly detailed items that also look good.
- Flexible Packaging
Thin-gauge thermoforming has played a major role in the popularity of flexible, see-through packaging within the food, retail and medical industries. This type of material provides an excellent barrier to protect products as well as good visibility for consumers.
Factors Influencing Thickness Choice
Several factors determine the appropriate thickness for a thermoformed product, including:
Durability Requirements: Heavier, more durable items need thicker plastic material.
Flexibility Needs: Flexible items, such as certain types of packaging, may benefit from thinner materials.
Mold’s Contours: The complexity and depth of the mold can require adjustments in plastic material thickness to achieve the desired detail and structural integrity.
Material Type: Different plastics have varying strength and flexibility characteristics, which can affect the optimal thickness for a given application. Commonly used materials include ABS, polystyrene, polyethylene, and PVC.