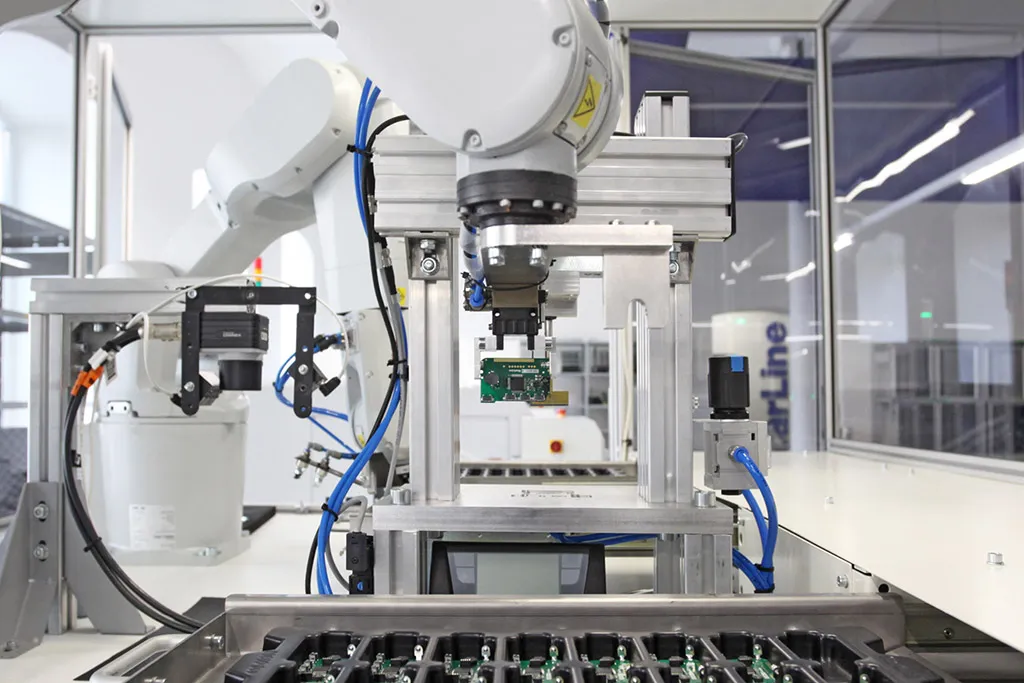
Thermoforming Machine Maintenance: Tips for Longevity and Performance
Thermoforming machines are vital tools in the plastic manufacturing industry, transforming plastic sheets into usable products through heat and molding processes. Ensuring the longevity and optimal performance of these machines requires regular and meticulous maintenance. This article provides comprehensive maintenance tips that can help businesses extend the lifespan of their thermoforming machines and maintain high performance levels.
Introduction to Thermoforming Machine Maintenance
Maintaining a thermoforming machine involves a series of preventive and corrective measures aimed at ensuring the machine operates efficiently and reliably. Proper maintenance can prevent unexpected breakdowns, reduce downtime, and save costs in the long run. This article covers various aspects of maintenance, including daily checks, scheduled servicing, and troubleshooting common issues.
Importance of Regular Maintenance
Prolonging Machine Lifespan
Regular maintenance helps in identifying and addressing minor issues before they escalate into major problems. By doing so, the overall lifespan of the thermoforming machine is extended, providing better returns on investment.
Ensuring Consistent Product Quality
A well-maintained machine operates smoothly and consistently, leading to uniform heating, forming, and cooling processes. This consistency is crucial for producing high-quality products with minimal defects.
Reducing Downtime and Costs
Preventive maintenance reduces the likelihood of unexpected breakdowns, thereby minimizing downtime. It also helps in avoiding costly repairs and production losses associated with machine failures.
Daily Maintenance Checks
Visual Inspection
Start each day with a thorough visual inspection of the machine. Look for signs of wear and tear, loose components, and any abnormalities. Check for:
- Leaks: Ensure there are no leaks in the hydraulic, pneumatic, or cooling systems.
- Cables and Connections: Inspect electrical cables and connections for any signs of damage or wear.
- Cleanliness: Keep the machine and surrounding area clean to prevent dust and debris from affecting performance.
Lubrication
Proper lubrication is essential for reducing friction and wear on moving parts. Check and lubricate:
- Bearings: Ensure bearings are adequately lubricated to avoid overheating and wear.
- Chains and Belts: Apply appropriate lubricants to chains and belts to maintain smooth operation.
- Guides and Rails: Lubricate guides and rails to facilitate smooth movement of the forming table and other components.
Checking Operating Temperatures
Monitor the operating temperatures of the heating elements and cooling systems. Ensure they are within the specified ranges to prevent overheating or insufficient heating, which can affect product quality.
Safety Systems
Verify the functionality of all safety systems, including emergency stops, safety guards, and interlocks. These systems are crucial for preventing accidents and ensuring operator safety.
Scheduled Maintenance
Weekly Maintenance
- Detailed Cleaning: Perform a more thorough cleaning of the machine, focusing on areas that are hard to reach during daily cleaning.
- Check and Tighten Fasteners: Inspect and tighten all bolts, nuts, and screws to ensure they are secure.
- Inspect Heating Elements: Check heating elements for signs of wear or damage. Replace any elements that are not functioning correctly.
Monthly Maintenance
- Calibration: Calibrate the temperature sensors and controls to ensure accurate heating.
- Inspect Molds: Examine molds for wear and damage. Clean them thoroughly and replace if necessary to maintain product quality.
- Check Hydraulic and Pneumatic Systems: Inspect hoses, valves, and cylinders for leaks or damage. Ensure all connections are secure and functioning properly.
Quarterly Maintenance
- Electrical System Inspection: Conduct a detailed inspection of the electrical system. Check for loose connections, damaged wires, and ensure all electrical components are functioning correctly.
- Cooling System Maintenance: Clean and inspect the cooling system. Check for leaks and ensure the coolant levels are adequate.
- Review Software and Firmware: Update the machine’s software and firmware to the latest versions to benefit from new features and improvements.
Annual Maintenance
- Comprehensive Inspection: Perform a comprehensive inspection of the entire machine. This should include all mechanical, electrical, and hydraulic systems.
- Professional Servicing: Consider hiring a professional technician to perform a detailed service, including alignment checks, system calibrations, and any necessary repairs.
- Evaluate Overall Performance: Assess the overall performance of the machine. Review production logs and maintenance records to identify any recurring issues that need addressing.
Troubleshooting Common Issues
Inconsistent Heating
Causes:
- Faulty heating elements
- Inaccurate temperature sensors
- Inconsistent power supply
Solutions:
- Replace or repair faulty heating elements.
- Calibrate or replace temperature sensors.
- Ensure a stable power supply and check for electrical issues.
Poor Forming Quality
Causes:
- Worn or damaged molds
- Incorrect forming temperatures
- Inadequate material preparation
Solutions:
- Inspect and replace worn molds.
- Adjust and monitor forming temperatures.
- Ensure plastic sheets are properly prepared and free of contaminants.
Machine Downtime
Causes:
- Mechanical failures
- Electrical issues
- Lack of preventive maintenance
Solutions:
- Perform regular maintenance checks and address issues promptly.
- Inspect and repair electrical components as needed.
- Implement a comprehensive preventive maintenance schedule.
Excessive Material Waste
Causes:
- Incorrect cutting settings
- Misaligned molds
- Poor material handling
Solutions:
- Adjust cutting settings to minimize waste.
- Align molds correctly and ensure they are securely fastened.
- Improve material handling procedures to reduce damage and waste.
Best Practices for Thermoforming Machine Maintenance
Develop a Maintenance Schedule
Create a detailed maintenance schedule that outlines daily, weekly, monthly, and annual maintenance tasks. Ensure that all maintenance activities are documented and tracked.
Train Operators and Technicians
Provide comprehensive training for machine operators and maintenance technicians. Ensure they are familiar with the machine’s operation, maintenance procedures, and safety protocols.
Use High-Quality Spare Parts
Always use high-quality, manufacturer-recommended spare parts for repairs and replacements. Using inferior parts can lead to premature failures and affect machine performance.
Monitor Machine Performance
Implement a system for monitoring machine performance and logging production data. Use this data to identify trends, predict maintenance needs, and optimize machine settings.
Implement Predictive Maintenance
Consider adopting predictive maintenance techniques, such as vibration analysis and thermal imaging, to identify potential issues before they cause machine failure.
Maintain a Clean and Organized Work Environment
A clean and organized work environment helps in maintaining machine performance and safety. Regularly clean the machine and surrounding area, and keep tools and spare parts organized.
Conclusion
Proper maintenance of thermoforming machines is crucial for ensuring their longevity and optimal performance. By following a comprehensive maintenance schedule, training personnel, using high-quality parts, and monitoring machine performance, businesses can minimize downtime, reduce costs, and maintain high product quality.
Investing time and resources in regular maintenance not only extends the life of the thermoforming machine but also enhances operational efficiency and productivity. Implementing the tips and best practices outlined in this article will help businesses achieve these goals and maximize their return on investment in thermoforming technology.