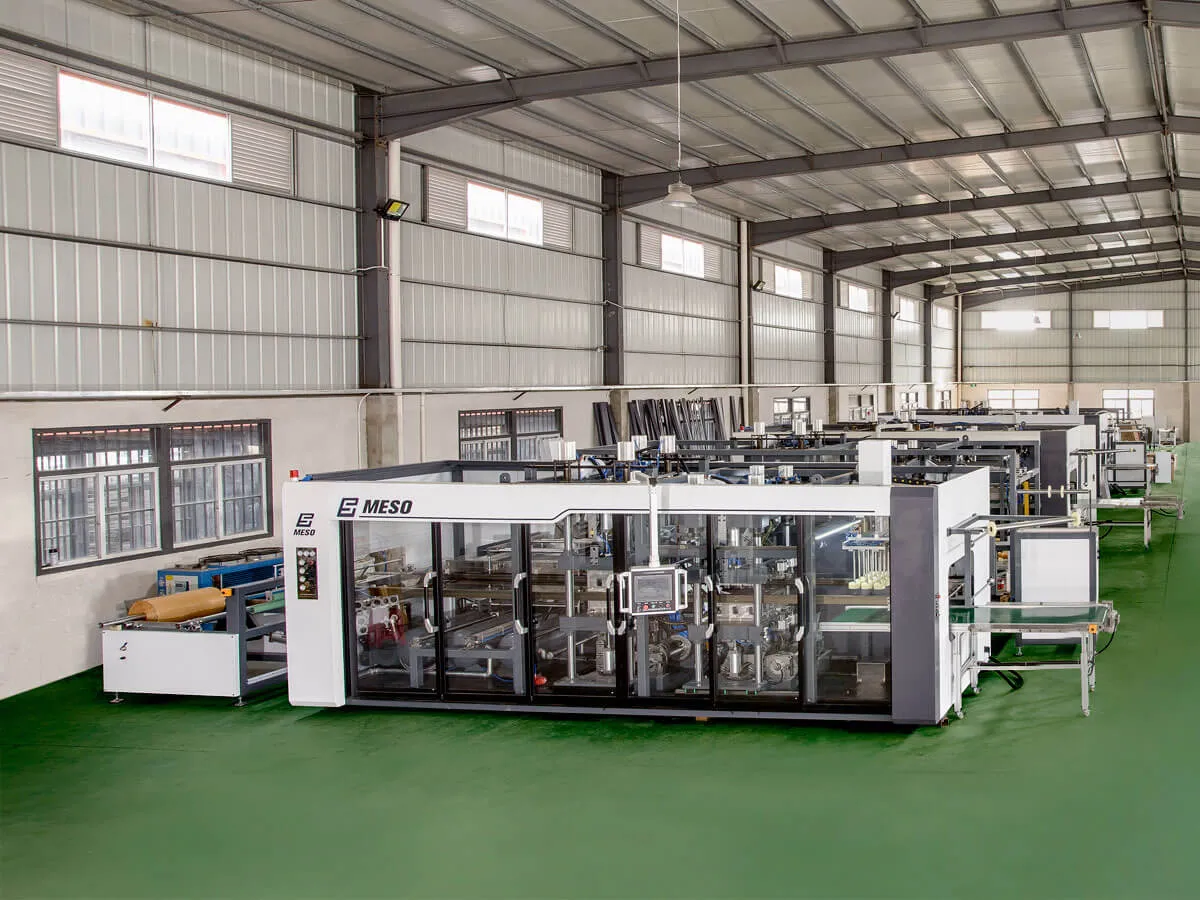
Custom Thermoforming Machines: Tailoring Solutions to Industry Needs
In today’s competitive manufacturing landscape, the demand for high-quality, cost-effective, and innovative products is ever-increasing. Thermoforming machines play a pivotal role in various industries, enabling the production of a wide range of plastic products. However, off-the-shelf solutions often fall short of meeting specific production requirements. This is where custom thermoforming machines come into play, offering tailored solutions that cater to the unique needs of different industries. This article explores the benefits, applications, and considerations involved in adopting custom thermoforming machines.
Introduction to Custom Thermoforming Machines
Thermoforming is a manufacturing process where a plastic sheet is heated to a pliable temperature, formed to a specific shape in a mold, and trimmed to create a usable product. While standard thermoforming machines are designed for general applications, custom thermoforming machines are specifically engineered to address the unique requirements of specific industries and products.
The Need for Customization
Custom thermoforming machines provide several advantages over standard machines, including:
- Enhanced Productivity: Tailored to optimize production processes, reducing cycle times and increasing throughput.
- Improved Quality: Designed to meet specific quality standards, ensuring consistent and high-quality output.
- Cost Efficiency: Minimized waste and optimized material usage lead to cost savings.
- Flexibility: Adaptable to various product designs and materials, enabling manufacturers to diversify their product lines.
Key Benefits of Custom Thermoforming Machines
Enhanced Productivity
Custom machines are designed to streamline the production process. By integrating specific features and functionalities, these machines can significantly reduce cycle times and increase overall productivity. This leads to higher output rates and the ability to meet demanding production schedules.
Improved Product Quality
Customization allows for precise control over the thermoforming process, ensuring that the final products meet stringent quality standards. This includes accurate temperature control, uniform material distribution, and precise forming techniques that reduce defects and ensure consistency.
Cost Efficiency
By optimizing material usage and reducing waste, custom thermoforming machines can lead to substantial cost savings. Additionally, tailored solutions often result in lower maintenance costs and longer machine lifespans, further enhancing cost efficiency.
Flexibility and Versatility
Custom thermoforming machines can be designed to handle a wide range of materials and product designs. This flexibility allows manufacturers to diversify their product offerings and quickly adapt to changing market demands.
Applications of Custom Thermoforming Machines
Packaging Industry
The packaging industry requires thermoforming machines that can produce a variety of packaging solutions, from simple trays to complex blister packs. Custom machines can be designed to accommodate different materials, thicknesses, and designs, ensuring that packaging products meet specific requirements for durability, protection, and aesthetics.
Automotive Industry
In the automotive industry, thermoforming is used to produce interior and exterior components such as dashboards, door panels, and bumper covers. Custom thermoforming machines can be tailored to handle the specific materials and precision required for these components, ensuring high quality and consistency.
Medical Industry
The medical industry demands high precision and hygiene standards. Custom thermoforming machines are essential for producing medical trays, packaging, and equipment housings that meet stringent regulatory requirements. These machines can be designed with specialized features such as cleanroom compatibility and precise temperature control.
Consumer Goods
From household appliances to toys and electronics, the consumer goods industry relies on thermoforming for a variety of products. Custom machines enable manufacturers to produce complex shapes and designs, ensuring that products are both functional and aesthetically pleasing.
Food Industry
Thermoforming is widely used in the food industry for producing packaging solutions such as trays, clamshells, and containers. Custom thermoforming machines can be designed to handle different food-grade materials and meet specific requirements for freshness, safety, and convenience.
Considerations for Adopting Custom Thermoforming Machines
Understanding Specific Needs
The first step in adopting a custom thermoforming machine is to thoroughly understand the specific needs of your production process. This involves analyzing product specifications, material requirements, production volumes, and quality standards. Collaborating with experienced engineers and machine manufacturers can help identify the features and capabilities needed for your custom solution.
Selecting the Right Materials
Different materials have varying properties that can affect the thermoforming process. It is crucial to select the right materials that meet the requirements of your products while ensuring compatibility with the custom machine. Factors to consider include material thickness, flexibility, temperature resistance, and regulatory compliance.
Designing for Flexibility
While custom thermoforming machines are tailored to specific needs, it is also important to design them with flexibility in mind. This allows for adjustments and modifications as production demands change. Features such as adjustable molds, interchangeable components, and programmable controls can enhance the versatility of the machine.
Ensuring Quality Control
Quality control is paramount in any manufacturing process. Custom thermoforming machines should be equipped with advanced quality control systems to monitor and maintain consistent product quality. This includes temperature sensors, pressure controls, and automated inspection systems that detect defects and ensure compliance with quality standards.
Training and Support
Investing in custom thermoforming machines also requires investing in training and support for your staff. Ensuring that operators are well-trained in the use and maintenance of the machines is crucial for maximizing productivity and minimizing downtime. Additionally, partnering with a reliable machine manufacturer that offers ongoing support and maintenance services can enhance the longevity and performance of the custom machine.
Case Studies: Successful Implementations of Custom Thermoforming Machines
Case Study 1: Automotive Industry
An automotive parts manufacturer required a custom thermoforming machine to produce complex dashboard components with high precision and consistency. The custom solution included advanced temperature control systems, precise mold alignment features, and automated quality inspection. The result was a significant reduction in defect rates, increased production speed, and enhanced product quality, allowing the manufacturer to meet stringent industry standards and customer demands.
Case Study 2: Medical Industry
A medical device company needed a custom thermoforming machine to produce sterile packaging for surgical instruments. The custom machine was designed with cleanroom compatibility, precise temperature control, and automated handling systems to ensure hygiene and quality. The implementation of this custom solution enabled the company to meet regulatory requirements, improve production efficiency, and maintain high standards of product quality.
Case Study 3: Food Industry
A food packaging company sought a custom thermoforming machine to produce environmentally friendly packaging solutions. The custom machine was designed to handle biodegradable materials and included features for precise forming and cutting. This allowed the company to produce high-quality, eco-friendly packaging products that met market demands for sustainability while maintaining cost efficiency and production speed.
Future Trends in Custom Thermoforming Machines
Automation and Industry 4.0
The integration of automation and Industry 4.0 technologies is transforming the landscape of custom thermoforming machines. Advanced robotics, IoT connectivity, and data analytics are enabling smarter and more efficient production processes. Custom machines equipped with these technologies can offer predictive maintenance, real-time monitoring, and adaptive control systems, further enhancing productivity and quality.
Sustainable Manufacturing
As sustainability becomes a key focus in manufacturing, custom thermoforming machines are being designed to support eco-friendly practices. This includes the ability to handle recycled and biodegradable materials, energy-efficient operation, and waste reduction features. Adopting custom solutions that prioritize sustainability can help manufacturers meet regulatory requirements and market demands for greener products.
Advanced Materials
The development of new and advanced materials is opening up new possibilities for thermoforming applications. Custom machines are being designed to handle these materials, offering enhanced performance, durability, and functionality. This includes high-performance plastics, composites, and materials with unique properties such as antimicrobial resistance and thermal stability.
Conclusion
Custom thermoforming machines offer tailored solutions that cater to the unique needs of various industries. By enhancing productivity, improving product quality, reducing costs, and providing flexibility, these machines enable manufacturers to stay competitive in a rapidly evolving market.
Understanding specific production needs, selecting the right materials, designing for flexibility, ensuring quality control, and investing in training and support are key considerations for adopting custom thermoforming machines. With successful implementations across industries such as automotive, medical, and food, custom solutions are proving to be a valuable investment for manufacturers.
Looking ahead, the integration of automation, sustainable manufacturing practices, and advanced materials will continue to drive the evolution of custom thermoforming machines. By embracing these trends, manufacturers can unlock new opportunities for innovation, efficiency, and growth.