Plastic Sheeting Machine: Complete Guide to Sheet Extrusion and Industrial Applications
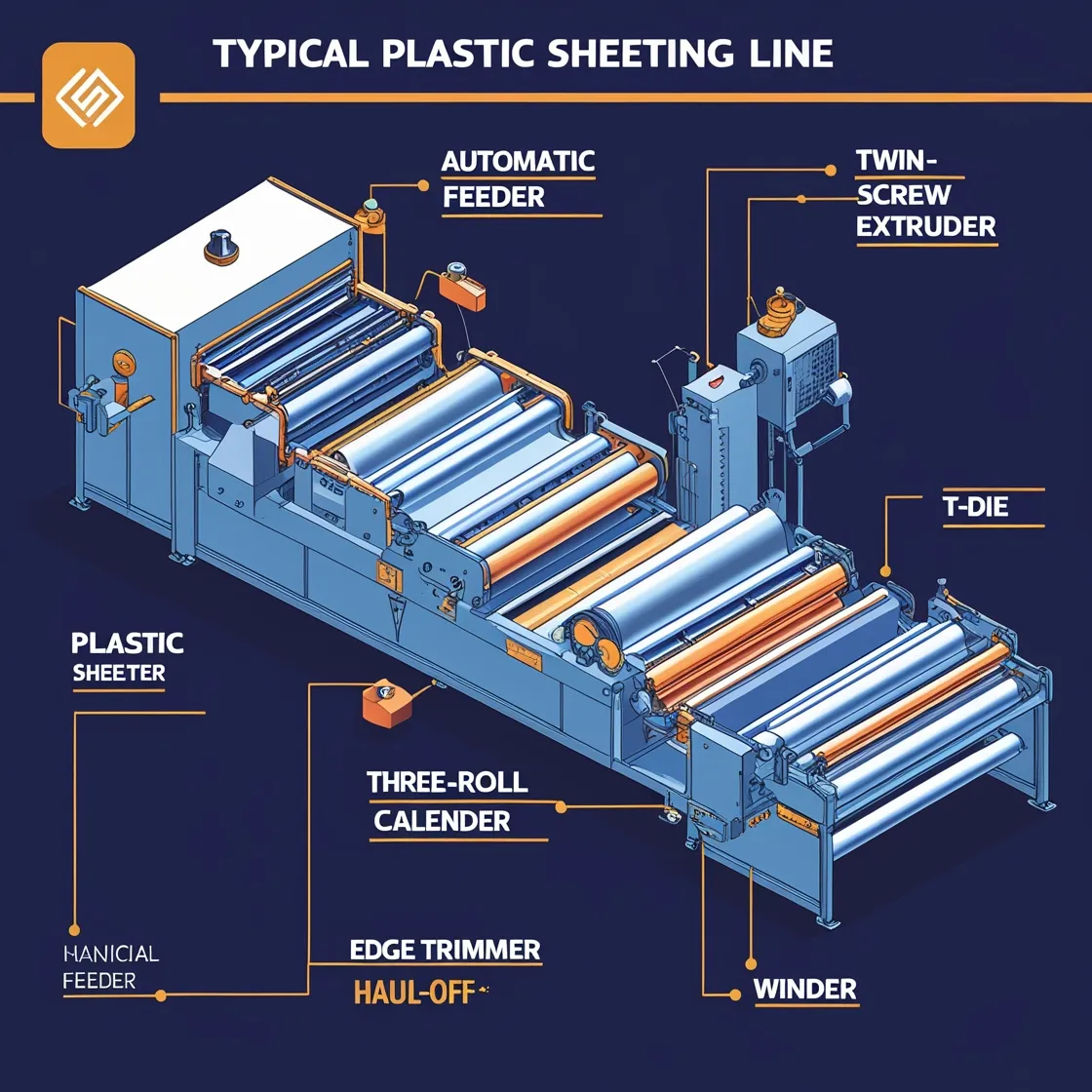
Introduction The plastic sheeting machine is one of the most essential and widely used pieces of equipment in the modern plastic processing industry. Its primary function is to convert granular or pelletized plastic raw materials into continuous sheet products, which serve as foundational materials across a variety of industries. From food packaging and electronic device casings […]
Complete Guide to Thermoforming: Key Processes, Material Selection, Applications, and Benefits for Cost-Effective Production
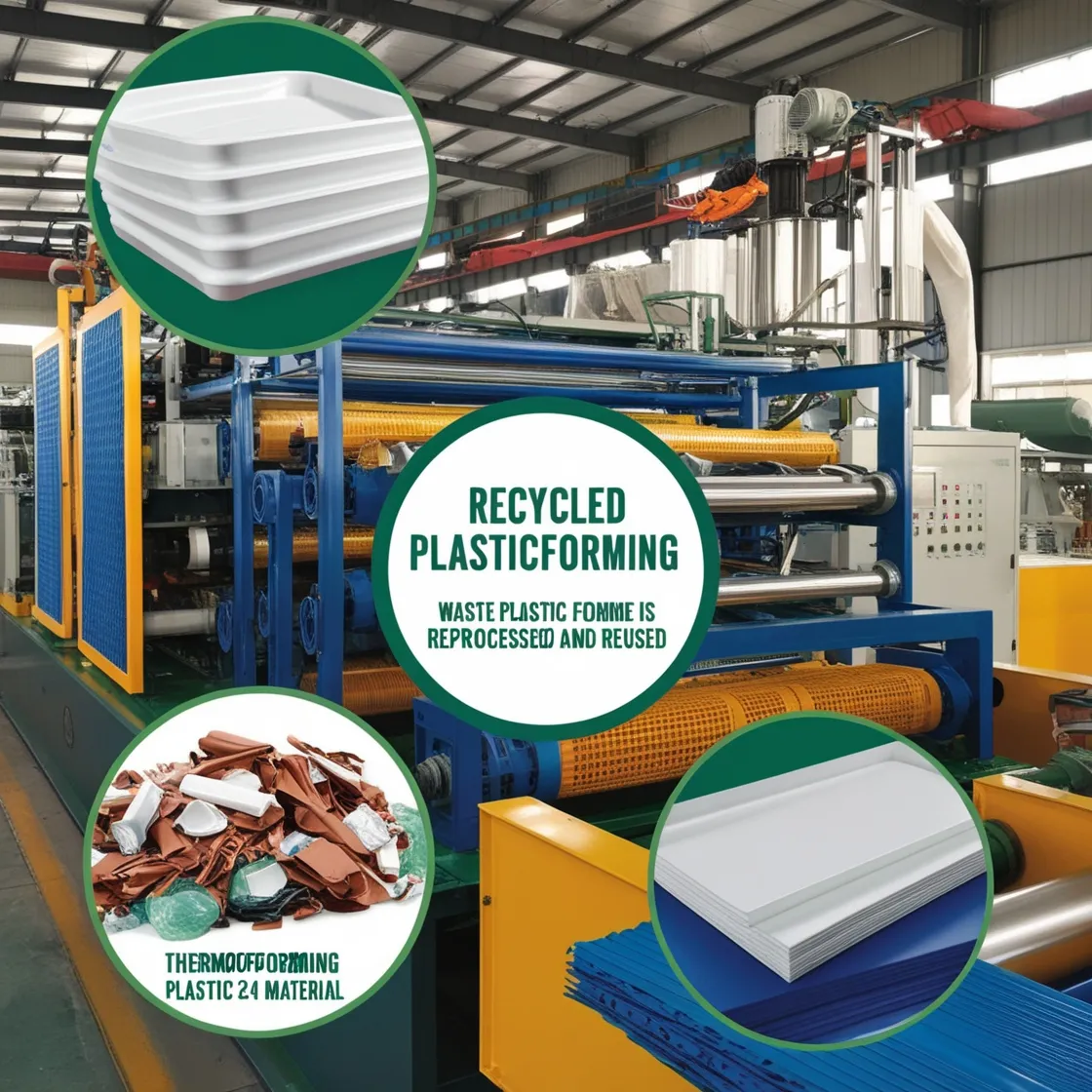
Thermoforming is a highly versatile process that finds applications across a wide range of industries, from food packaging to aerospace and even auto parts manufacturing. Thermoplastics, the core material in thermoforming, are indispensable to many sectors, making it essential to understand their uses and variations. Key Elements of Material Selection Thermoforming is a versatile manufacturing […]
The Impact of Thickness on Thermoformed Products: Factors, Techniques, and Quality Testing
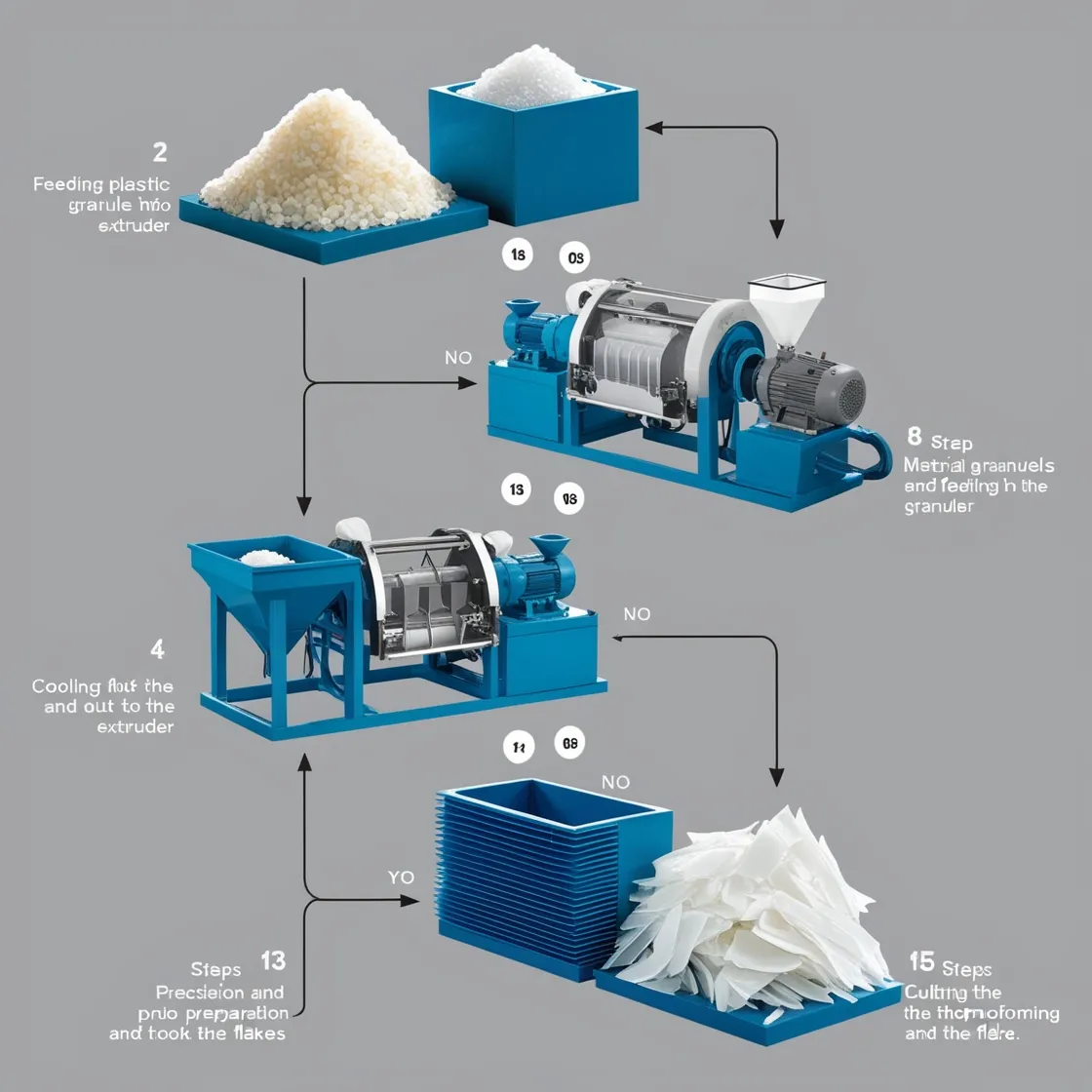
What are the reasons for the variation of thickness in products formed by the thermoforming process? Thermoforming is a flexible manufacturing technique that molds plastic films and sheets into various products, where thickness variation is crucial for both design and functionality. Material Selection and Thickness: The type of plastic used significantly impacts the thickness of […]
Thermoforming vs Thermosetting Plastics: Key Differences, Applications, and Benefits
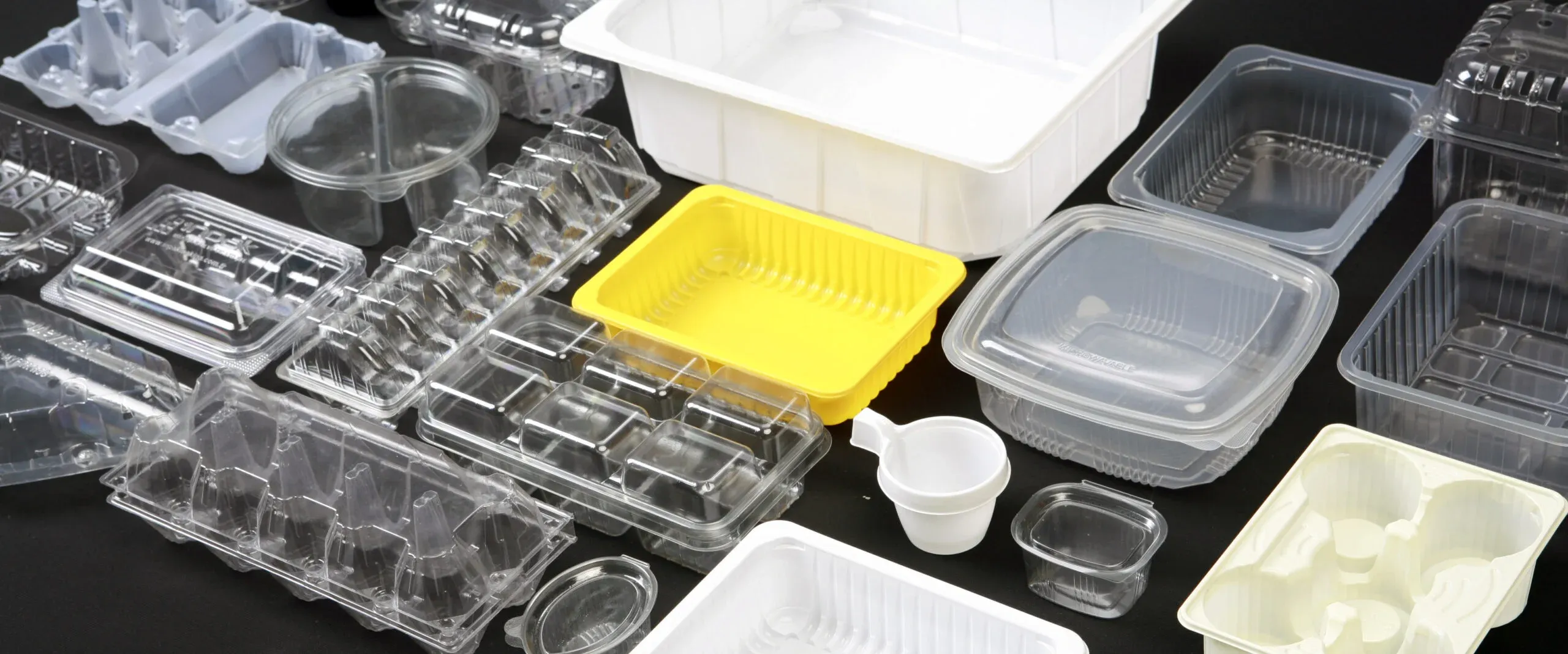
In the world of plastic products, thermoforming plastics and thermoset plastics play their own unique roles. Although they are both the cornerstone of plastic product manufacturing, they differ greatly in how they react to heat, application scenarios, and performance in everyday use. A solid understanding of these differences is critical for engineers, manufacturers, and product […]
Compression Moulding vs Thermoforming: Key Differences
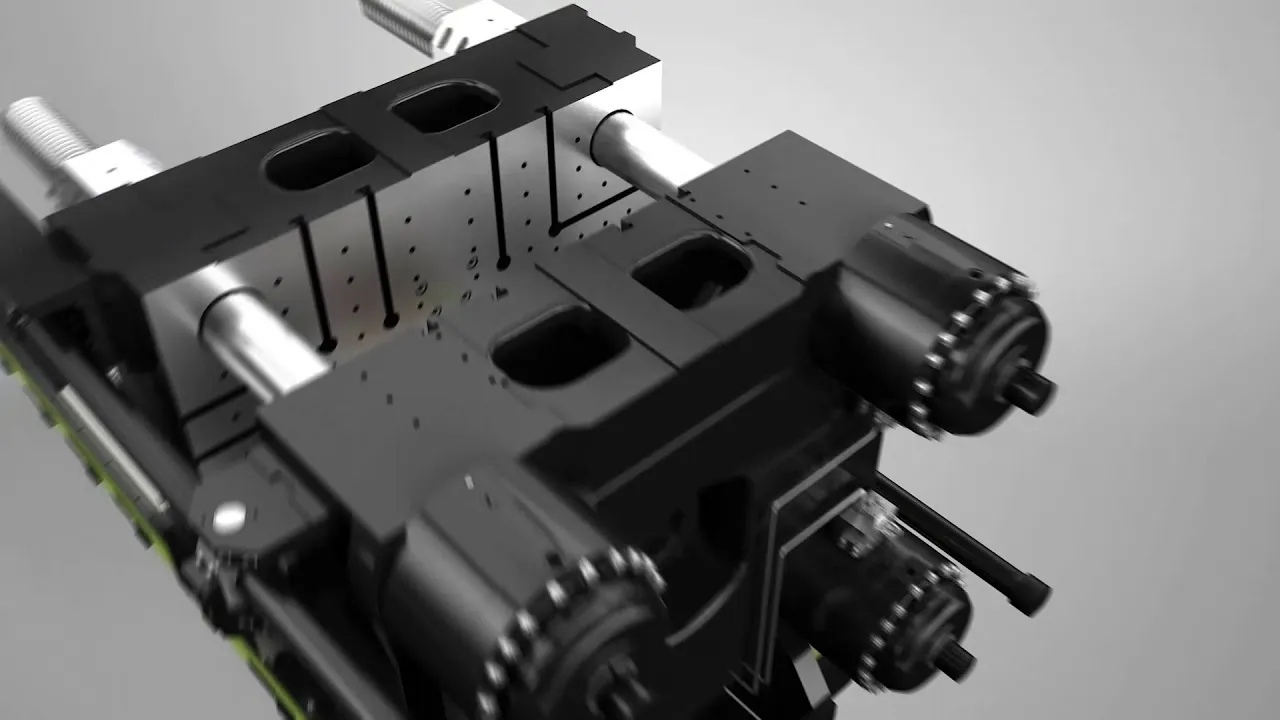
Compression Moulding vs Thermoforming: Key Differences Compression moulding involves placing a moulding material in an open, heated mould cavity. Pressure forces the material to contact all mould areas. Thermoset composites often serve as the primary material in this process. Prepreg materials, pre-mixed materials, and blanks are common choices. In contrast, thermoforming uses heated plastic sheets shaped by vacuum […]
How Thermoforming Cooling Systems Operate
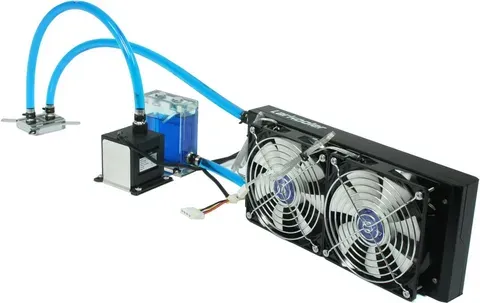
How Thermoforming Cooling Systems Operate Thermoforming involves shaping a heated thermoplastic sheet over a mould. The process relies heavily on energy, with the heating system consuming more than 70% of the energy requirement. Basic principles of thermoforming include heating, moulding, and cooling. Cooling plays a vital role in solidifying the formed sheet, ensuring product quality and integrity. […]
Precision Heating: The Secret Weapon of Modern Plastic Product Manufacturing
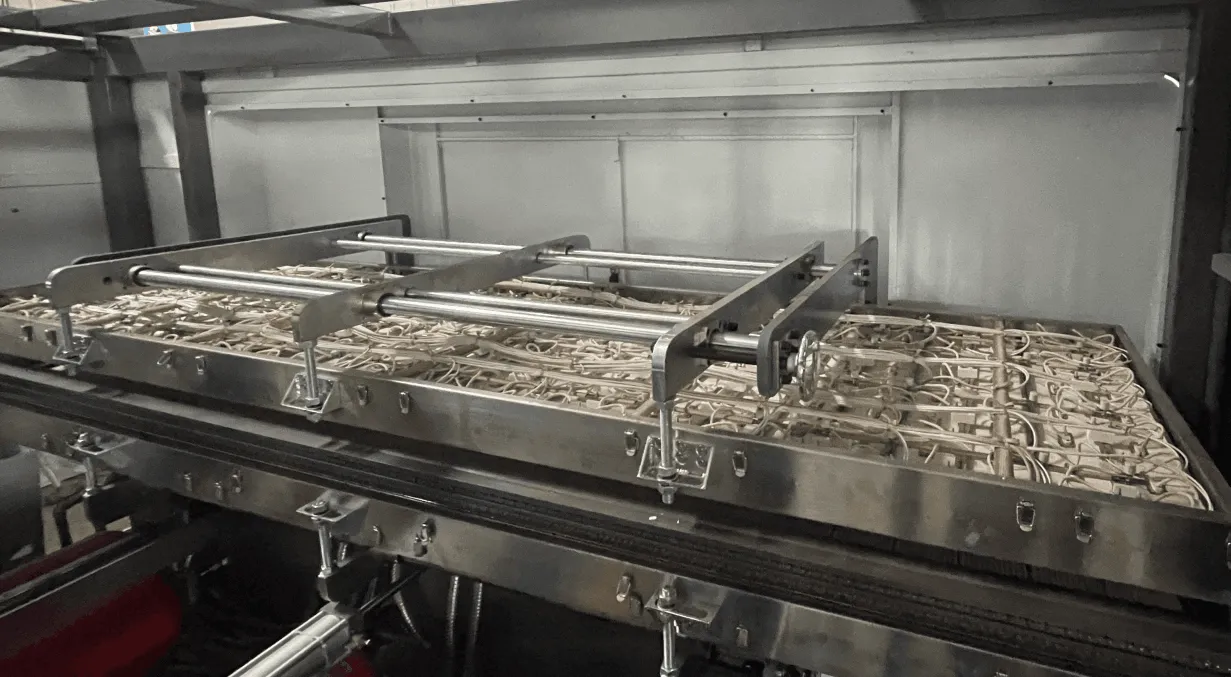
Precision Heating: The Secret Weapon of Modern Plastic Product Manufacturing Introduce In modern industrial production, thermoforming machines are the core equipment for plastic processing, and the choice of heating technology directly affects production efficiency and product quality. This article will explore the four-stage and five-stage heating technologies of thermoforming machines in depth to help you […]
Precision and Efficiency: Unveiling the Core Process of Multi-Station Thermoforming Machine Molding Stations
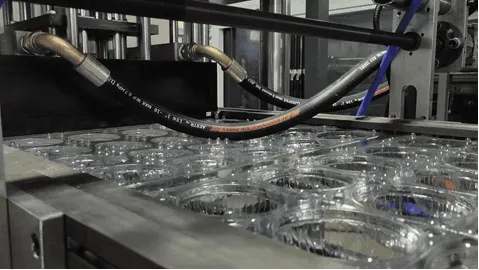
The heart of the thermoforming machine: revealing the precision process of the molding station Introduce In the field of plastic processing, multi-station thermoforming machines are highly favored for their efficient and flexible production capacity. This article will introduce the molding station in the multi-station thermoforming machine in detail, explore its working principle, key components and […]
From Zero to One: The Design, Development, and Market Feedback of the Three-Station Thermoforming Machine
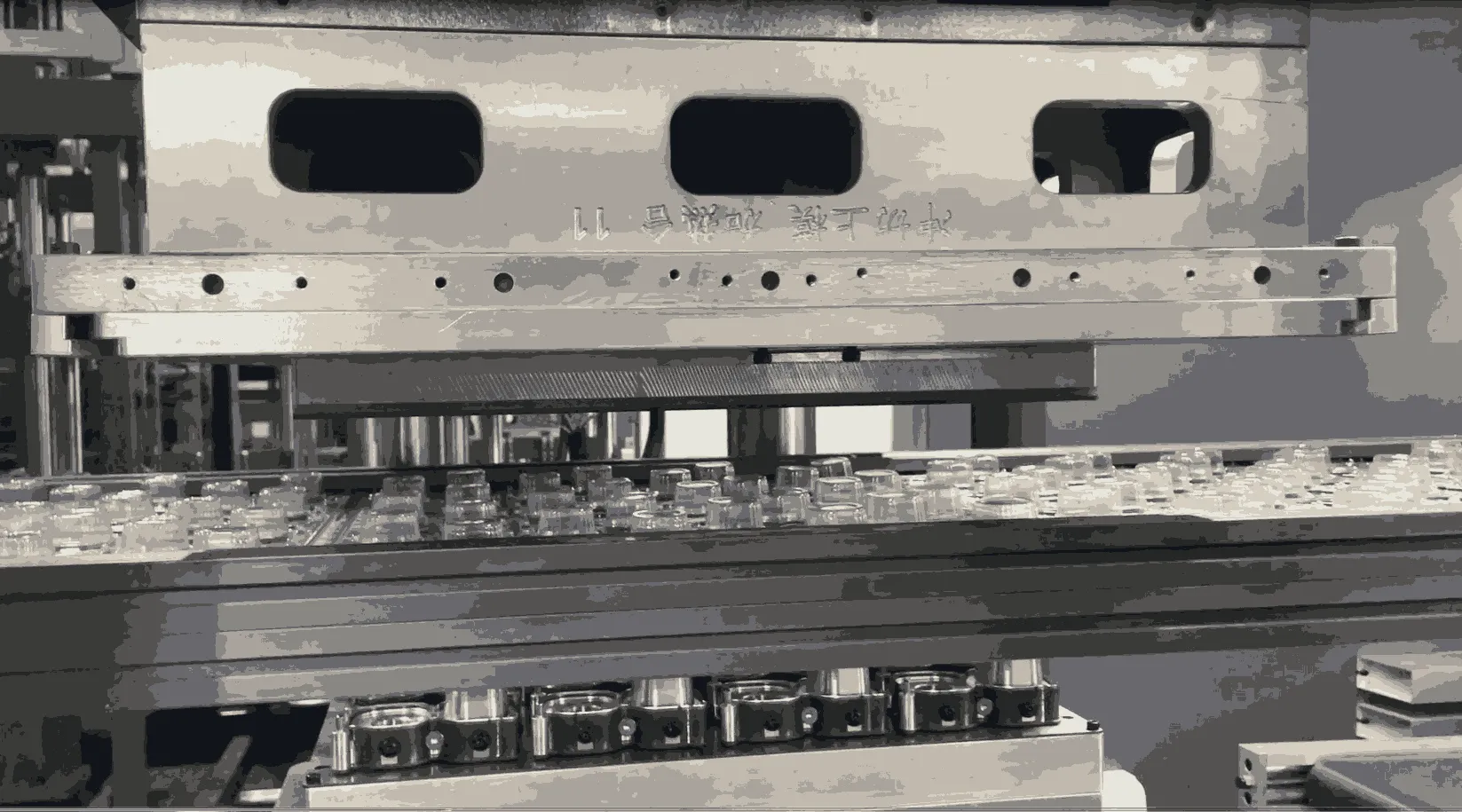
From Zero to One: The Design, Development, and Market Feedback of the Three-Station Thermoforming Machine Introduction The three-station thermoforming machine is a widely used equipment in modern manufacturing industry, which is specially used to process thermoplastic materials into products of desired shapes through heating and mold forming. With the increasing demand for plastic products in […]