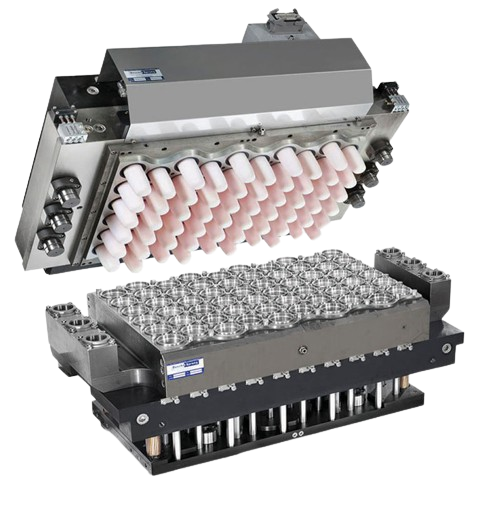
Troubleshooting Common Issues with Thermoforming Machines
Thermoforming machines are indispensable tools in the manufacturing industry, used for shaping plastic materials into various products. However, like any complex machinery, they are prone to encountering issues that can disrupt production and affect product quality. In this article, we will explore some common problems that arise with thermoforming machines and provide detailed troubleshooting solutions, accompanied by specific case studies to illustrate real-world scenarios.
Introduction to Thermoforming Machine Issues
Thermoforming machines perform a series of precise and interconnected processes to transform plastic sheets into finished products. Despite their reliability, various factors such as material variations, mold issues, and operational errors can lead to malfunctions and downtime. Identifying and resolving these issues promptly is crucial for maintaining productivity and ensuring product quality.
Common Thermoforming Machine Issues and Troubleshooting Solutions
1. Heating Inconsistencies
Issue: Uneven heating of plastic sheets can result in inconsistent forming and poor product quality.
Troubleshooting Solution: Check the heating elements for wear or damage. Clean or replace any faulty elements. Ensure proper alignment of heating elements and adjust settings for uniform heating. Consider upgrading to advanced heating systems for precise temperature control.
Case Study: XYZ Plastics encountered heating inconsistencies in their thermoforming machine, leading to warped products. After inspecting the heating elements and recalibrating the temperature settings, they implemented an advanced heating system with zone control. This resulted in uniform heating across the plastic sheet, reducing scrap rates by 30%.
2. Mold Defects
Issue: Mold defects such as cracks, warping, or improper alignment can affect product integrity and lead to rejects.
Troubleshooting Solution: Inspect the mold for damage or wear. Repair or replace damaged sections. Ensure proper alignment and closure of the mold. Regularly clean and maintain the mold to prevent buildup of residue. Consider investing in high-quality, precision-engineered molds.
Case Study: ABC Packaging Solutions experienced mold defects causing misalignment and flash formation in their products. By conducting regular maintenance and replacing worn-out mold components, they improved mold performance and reduced reject rates by 25%.
3. Vacuum System Failures
Issue: Vacuum system failures can result in incomplete forming, air bubbles, or wrinkling of plastic sheets.
Troubleshooting Solution: Check vacuum pump for leaks, clogs, or mechanical issues. Replace worn-out components such as seals or valves. Optimize vacuum settings for the specific material and product being formed. Implement regular maintenance schedules for vacuum systems.
Case Study: DEF Industries faced vacuum system failures causing poor product definition and excessive scrap. After inspecting and repairing the vacuum pump, they implemented preventive maintenance measures, including regular lubrication and seal replacements. This improved vacuum system reliability and reduced scrap rates by 20%.
4. Material Feed Issues
Issue: Irregular material feeding can result in misaligned or incomplete products.
Troubleshooting Solution: Inspect material feed mechanisms for jams, misalignment, or wear. Clean or repair feed components as needed. Adjust feeding speed and tension settings to ensure smooth material flow. Train operators on proper material handling procedures.
Case Study: LMN Manufacturing encountered material feed issues causing misfeeds and interruptions in production. By conducting thorough inspections and adjustments to the material feed system, they optimized material flow and reduced downtime by 15%.
5. Cooling Problems
Issue: Inadequate cooling can lead to improper product setting, warping, or deformation.
Troubleshooting Solution: Check cooling systems for proper functionality and water flow. Clean or replace cooling channels to remove debris or scaling. Optimize cooling cycle times based on material and product specifications. Monitor product cooling process to ensure uniformity.
Case Study: GHI Plastics experienced cooling problems resulting in uneven product cooling and dimensional inaccuracies. By upgrading cooling channels and adjusting cooling parameters, they achieved consistent product quality and reduced rejection rates by 20%.
Conclusion
Troubleshooting common issues with thermoforming machines is essential for maintaining efficient production and ensuring product quality. By promptly identifying and addressing issues such as heating inconsistencies, mold defects, vacuum system failures, material feed problems, and cooling issues, manufacturers can minimize downtime, reduce scrap rates, and improve overall productivity.
Real-world case studies highlight the practical application of troubleshooting solutions, demonstrating how proactive maintenance, regular inspections, and targeted repairs can mitigate issues and optimize thermoforming machine performance. With a proactive approach to troubleshooting and maintenance, manufacturers can maximize the reliability and efficiency of their thermoforming operations, ultimately driving business success and customer satisfaction.