导言
脱模系统对于确保热成型机的效率和精度至关重要。这些系统旨在以安全、一致的方式将成型产品从模具中取出,从而有助于最大限度地减少缺陷、缩短停机时间并提高生产速度。随着热成型行业的不断发展,开发先进的脱模技术对于希望满足对高质量、高可靠性生产不断增长的需求的制造商来说变得越来越重要。
在本文中,我们将仔细研究脱模系统的主要方面,探讨不同类型、工作原理、设计注意事项、挑战以及该领域的最新趋势。无论您是热成型领域的制造商还是技术专家,深入了解这些系统都将有助于您做出更好的决策并提高生产效率。
什么是脱模系统?
脱模系统是热成型机的一项重要功能,用于自动将成型部件从模具中取出。塑料板通过真空成型、压力成型或机械成型等方法成型后,脱模系统可确保成品轻松快速地分离。根据操作需要,脱模系统可以使用机械、气动或机器人工具将成型部件从模具中取出。这有助于简化流程,减少对人工的需求,提高整体效率。
脱模系统的主要目标:
- 防止产品损坏或变形:该系统可小心处理精密复杂的部件,确保在移除这些部件时不会造成变形、划痕或其他损坏。这对于壁薄或形状复杂的产品尤为重要。
- 提高生产速度:通过自动脱模过程,该系统减少了拆卸每个部件的时间,从而可以快速进入下一个循环,提高整体生产效率。
- 保持稳定的质量:自动化可确保每次都以一致的方式、相同的力度和时间拆卸每个部件,这有助于在所有生产运行中保持统一的质量。
- 尽量减少人工劳动:通过自动脱模过程,该系统减少了人工参与的需要,降低了出错的风险,并通过限制直接接触高温或尖锐部件来提高工人的安全性。
脱模系统类型
脱模系统对于确保安全高效地从模具中取出成型零件至关重要。根据脱模过程中使用的机制,这些系统可分为不同类型。现代热成型机中最常见的四种脱模系统是机械系统、气动系统、液压系统和机器人系统。每种类型都有适合特定生产需求和零件复杂性的独特优势。
1.机械脱模系统
机械脱模系统广泛应用于热成型,利用顶针、滑块或推杆等机械部件将成型部件从模具中取出。这些系统对于设计较简单、对力的要求适中的零件最为有效。
顶针:顶针通常放置在模具内的重要位置。启动时,它们利用线性运动将成型零件推出模腔。这些顶针通常用于较小或不太复杂的零件,并提供可靠、经济的解决方案。通常,它们与弹簧或气缸搭配使用,以产生必要的运动。
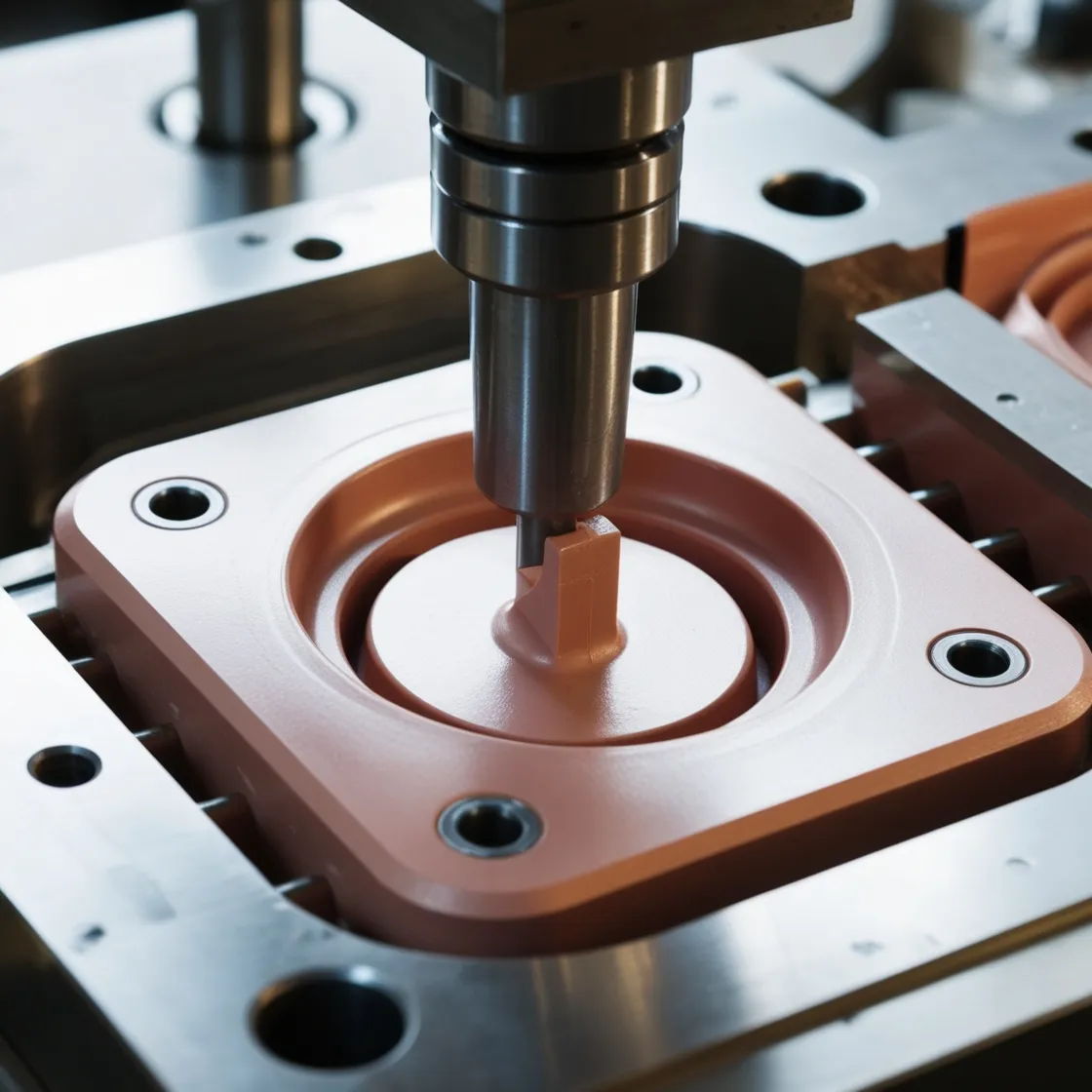
幻灯片:滑块是一种机械部件,可水平或垂直移动,用于脱模具有凹槽或复杂设计的注塑件,简单的线性运动无法脱模。这种机械装置可使模具在特定区域打开,从而更容易脱模具有复杂特征或更深型腔的零件。滑块对于确保形状复杂的产品无损脱模至关重要。
推杆:推杆是一种机械装置,可将零件水平或垂直推出模具。对于仅使用顶针无法取出的较大或较重的零件,它们尤其有用。推杆通常与气动或液压等其他系统结合使用,以确保顺利、高效地取出零件。
优势
- 设计简单,成本效益高,适用于不太复杂的部件。
- 用途广泛,易于适应各种模具形状。
- 可靠、坚固,是中等产量生产的理想选择。
2.气动脱模系统
气动脱模系统使用压缩空气将成型部件推出模具。通过精确控制气压,这些系统能产生足够的力将成型产品顶出,而不会造成变形或损坏。气动系统特别适用于生产轻型零件,因为它们可以轻柔地取出易碎物品,是易碎产品的理想选择。
气压应用:在这一系统中,受控的气流通过模具中战略性放置的通风口或端口喷出。这将对成型零件产生压力,迫使其脱离模具。对气压的精心管理确保了顺利的顶出过程,使其成为精密部件或薄壁部件的理想选择。
自动气流控制:先进的气动系统配有传感器和自动控制阀,可调节气流。这可确保注塑件稳定、顺畅地脱模,最大限度地降低部件变形的风险。该系统还能缩短生产周期,有助于提高整体生产效率。
优势
- 适用于需要轻柔处理的轻质易碎部件。
- 减少机械模具部件的磨损。
- 提供更平滑、更清洁的弹射过程,最大限度地减少表面损伤。
- 与机械系统相比,所需的维护更少。
局限性:
- 可能不适合较大、较重的部件,因为它们需要更大的力量才能移除。
如果不仔细校准,气压可能会波动。
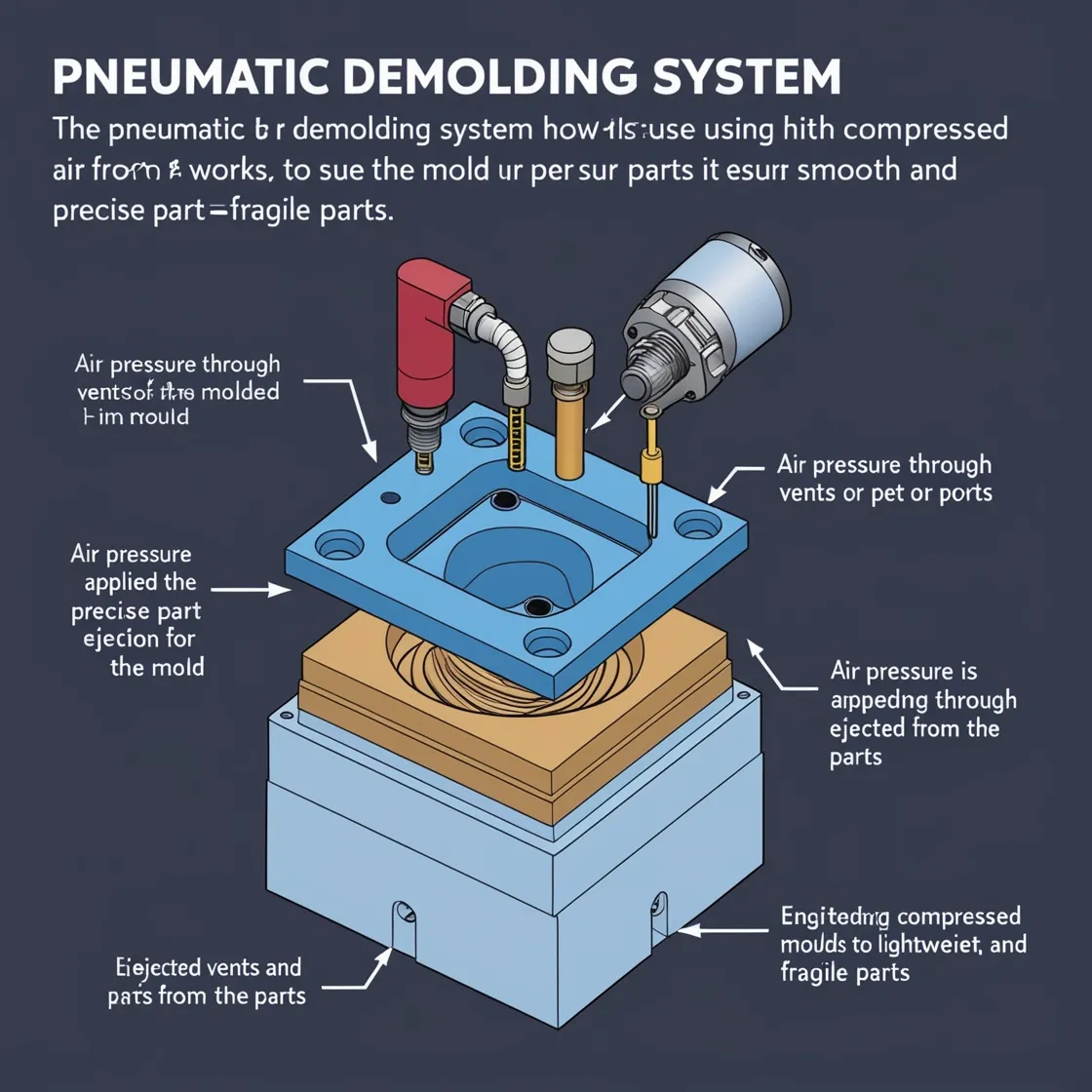
3.液压脱模系统
液压脱模系统使用加压流体驱动机械部件,帮助将成型件从模具中取出。这些系统非常适合需要高强度或精确控制的情况,尤其是在处理需要很大力量才能移除的大型或复杂零件时。
液压致动器:这些系统使用液压致动器,利用加压流体移动模具部件或将成型部件推出模腔。可对压力进行精确控制,以提供安全有效脱模所需的精确力。液压系统尤其适用于处理重型或厚壁产品。
精确控制:液压系统的最大优势之一是能够施加精确的力。这使它们成为具有复杂形状或细节特征的零件的完美选择。可调节的压力使这些系统能够处理各种材料和零件尺寸。
高强度能力:液压系统可提供比气动或机械系统大得多的力,因此是要求苛刻的应用场合的首选,在这些应用场合中,其他系统可能难以提供足够的力来移除工件。
优势
- 非常适合需要高精度的大型、重型或复杂零件。
- 力度大,精度高,是复杂设计的理想之选。
- 耐用可靠,适合大批量生产。
- 非常适合需要比气动或机械系统更强动力的应用。
局限性:
- 由于其复杂性,液压系统的设置和维护成本可能更高。
- 它们可能需要更大的空间和额外的设备来管理流体压力系统。
4.机器人脱模系统
机械手脱模系统为整个零件取出过程的自动化提供了先进的解决方案。这些系统使用机械臂或机械手将成型零件从机器中取出。机械手系统用途广泛,可以处理各种零件,从精密轻巧的零件到大型复杂的零件,因此非常适合现代化的柔性生产线。
机械臂技术:机械臂配有末端执行器,如抓手或吸盘,用于抓取和移动成型零件。根据零件的形状和尺寸,这些机械臂可以通过编程来执行特定的运动,如水平、垂直或旋转运动。
视觉系统:有些机械手系统带有集成视觉技术,使机械手能够 "看到 "成型零件。这样就可以调整机械手的动作,提高精度并确保可靠的移除,尤其是移除形状或尺寸各异的部件。
自动化集成:机器人系统可轻松集成到自动化生产线中,与其他热成型设备无缝连接。这样就能简化生产周期,减少人工操作。
优势
- 灵活,可处理各种零件类型和生产运行。
- 通过自动脱模过程,缩短生产周期,降低人工成本。
- 提供高精度,提高部件一致性并减少缺陷。
- 易于重新编程,可在不同设计和模具类型之间快速切换。
局限性:
- 由于机器人系统的复杂性,初始投资较高。
- 需要熟练的技术人员进行设置、编程和维护。
- 可能不是小批量、低产量生产的最佳选择。
根据生产要求,每种脱模系统都有自己的优势。机械系统适用于较简单的任务,气动系统是轻型部件的理想选择,液压系统为较重或复杂的产品提供必要的力,而机器人系统则为高端自动化设置提供最高的灵活性和精度。
在选择脱模系统时,重要的是要考虑零件的尺寸和复杂程度、所需的力、产量以及所需的自动化程度。选择合适的系统有助于提高生产效率、减少停机时间并提高产品质量。
脱模系统的工作原理
脱模过程是热成型的关键步骤,在成型部件冷却到足以保持其形状时进行。下面将逐步介绍该过程的典型展开过程:
开模:注塑周期结束且部件充分冷却后,模具开始打开,为进入注塑部件创造空间。这标志着脱模过程的开始。
部件弹射:在这一阶段,根据脱模系统的类型,机械顶针、气动气压或机械臂等工具将被激活,以轻柔或强制地将成型部件从模腔中脱出。目的是确保零件干净利落地脱模,不产生任何变形或损坏。
运输:一旦顶出,工件就会被传送到输送系统,如传送带或机械臂,以便进一步处理。工件或堆叠存放,或移至包装区进行最终加工。
周期重置:工件取出并输送后,系统会自动复位,为下一个循环做好模具准备。这包括重新启动顶出机构、关闭模具,并为下一块塑料板的成型做好准备。
每个步骤的时间安排和协调对于确保顺利、高效的生产至关重要。延迟或错位可能导致缺陷或停机,因此,一个组织良好的脱模系统对于保持最佳生产效率和稳定的产品质量至关重要。
脱模系统的设计考虑因素
设计有效的脱模系统需要深思熟虑,考虑到与产品和热成型机相关的具体因素。以下是影响脱模系统优化设计的关键因素:
产品几何形状:形状复杂、有凹槽或复杂细节的零件需要专门的机构才能顺利取出。为确保安全取出而不造成损坏,可能需要使用活动滑块、柔性顶出装置或多向推杆等功能。这些机构的精度对于避免精细区域或复杂设计变形至关重要。
材料特性:热成型所用材料对脱模系统的选择有很大影响。热塑性材料的刚性、弹性和热膨胀等因素都会产生影响。例如,刚性材料可能需要更大的弹射力,而柔性材料可能需要更温和的气动或机器人系统来防止脱模过程中的变形。
周期时间:尽量缩短生产周期对提高生产速度至关重要。脱模系统必须高效,以满足高速生产线的要求。气动或机器人系统通常是首选,可加快零件拆卸速度,缩短复位时间,在不影响零件质量的情况下最大限度地提高产量。
模具设计:模具设计本身对脱模过程有很大影响。在模具设计中加入有利于零件脱模的拔模角度和允许空气在成型过程中排出的排气通道等功能,可以显著提高效率。此外,在模具内部增加纹理表面有助于减少摩擦,确保部件更顺畅地脱模,并将损坏风险降至最低。
维护要求:设计精良的脱模系统应易于维护,部件易于清洁、检查和更换。定期维护是减少停机时间和确保性能稳定的关键。既坚固耐用又便于部件更换和维修的设计将提高系统的可靠性和使用寿命,减少生产中断。
通过仔细考虑这些设计因素,制造商可以开发出不仅高效,而且能够处理各种复杂零件的脱模系统,同时保持较高的生产速度,最大限度地减少停机时间。
结论
脱模系统对热成型工艺的效率和精度起着至关重要的作用,可确保成型产品始终如一地安全无损地从模具中取出。通过了解不同类型的脱模系统(机械式、气动式、液压式和机器人式),制造商可以根据生产要求和零件复杂性做出明智的决定。选择正确的系统不仅能最大限度地减少停机时间,还能提高整体生产速度、一致性和产品质量。随着技术的不断发展,脱模系统仍将是提高运营效率和满足现代制造业需求的关键因素。