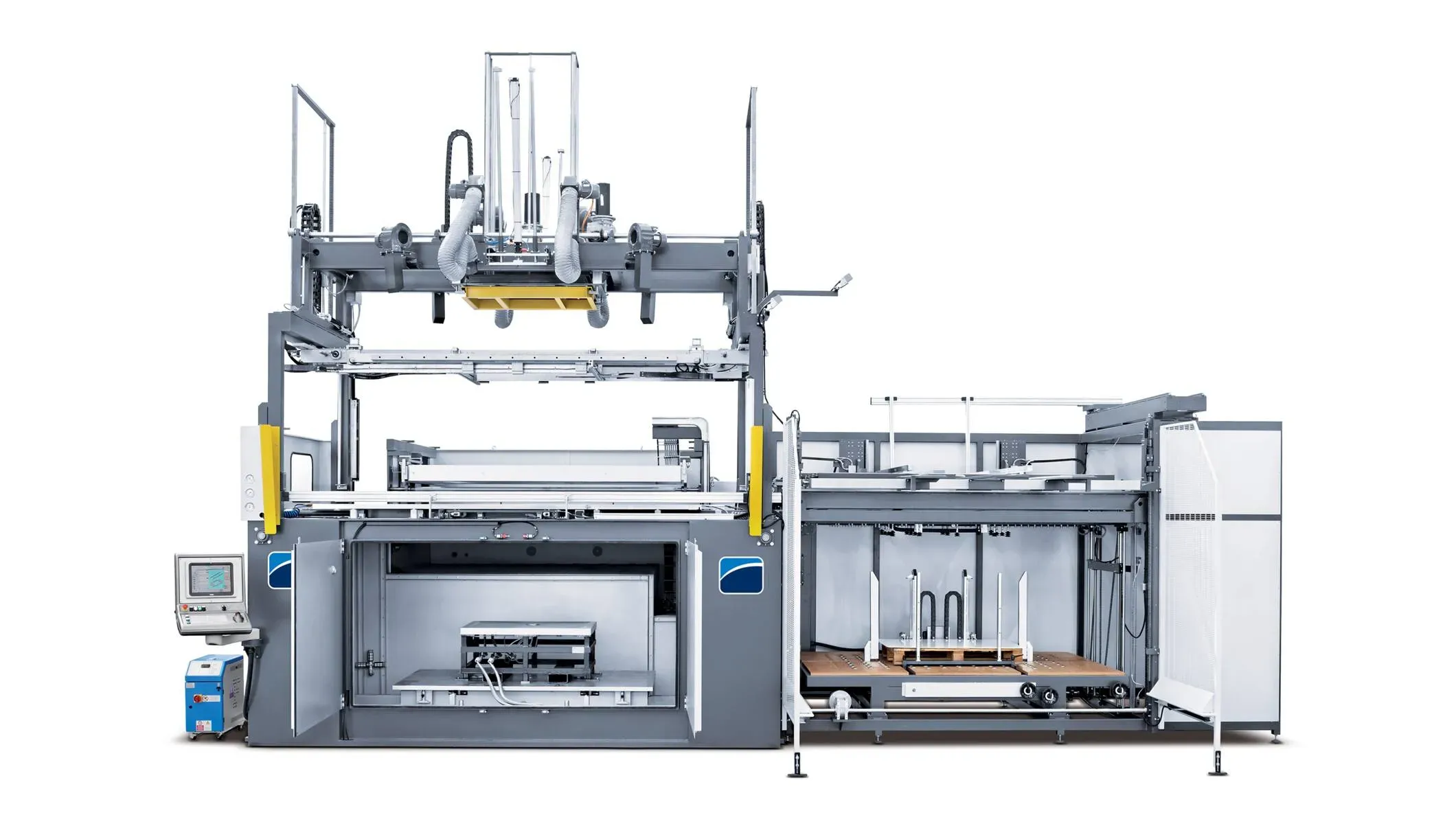
提高热成型操作中的材料利用率
导言
材料利用率是热成型操作效率和成本效益的关键因素。最大限度地利用原材料不仅能减少浪费和对环境的影响,还能提高盈利能力和竞争力。本文探讨了在热成型工艺中提高材料利用率的策略,提供了详细的见解和实际案例研究,以说明有效的实施方法。
了解热成型中的材料利用
热成型中的材料利用率是指最终产品中实际使用的材料量与最初装入机器的材料总量之比。材料利用率高意味着输入材料中有更大比例转化为成品,从而最大限度地减少浪费和降低成本。影响材料利用率的关键因素包括板材厚度、切割模式、模具设计和工艺参数。
提高材料利用率的策略
1.优化板材厚度
提高材料利用率的最直接方法之一是优化热成型所用塑料板的厚度。使用满足产品规格所需的最小厚度可以大大减少材料消耗。
实施:
- 对产品要求进行全面分析,以确定最佳板材厚度。
- 使用有限元分析 (FEA) 软件模拟产品性能,确定在不影响质量的前提下可减少材料厚度的区域。
- 实施质量控制措施,确保生产过程中板材厚度保持一致。
案例研究:在 PackRight 减少纸张厚度
公司: 包装权利
行业: 包装
挑战: PackRight 的目标是通过优化热成型包装产品的厚度来降低材料成本。
解决方案 该公司进行了一项有限元分析研究,以确定其产品在保持结构完整性的同时所需的最小厚度。然后,他们实施了新的质量控制流程,以确保板材厚度的一致性。
结果 PackRight 的材料用量减少了 15%,大大节约了成本,提高了材料利用率。最终产品的质量依然很高,性能丝毫无损。
2.高级切割和修剪技术
高效的切割和修剪工艺可以最大限度地减少废料,最大限度地利用塑料板,从而显著提高材料利用率。
实施:
- 投资高精度切割和修剪设备,减少材料浪费。
- 使用套料软件优化切割模式,最大限度地增加每张板材生产的零件数量。
- 采用自动修剪系统,确保切割的一致性和准确性。
案例研究:AutoTrim 的套料软件
公司: 自动修剪
行业: 汽车
挑战: AutoTrim 在热成型过程中,由于切割模式效率低下,材料浪费严重。
解决方案 该公司采用了先进的套料软件,以优化切割布局,尽量减少废料。他们还投资购买了高精度切边设备,以提高切割精度。
结果 AutoTrim 减少了 20% 的材料浪费,显著提高了材料利用率。优化的切割模式使每张板材可以生产更多零件,从而提高了整体生产率。
3.改进模具设计
高效的模具设计可确保材料分布均匀,最大限度地减少多余材料的使用,从而减少材料浪费。
实施:
- 设计壁厚均匀的模具,减少材料浪费。
- 使用多腔模具同时生产多个零件,提高材料利用率。
- 实施模流分析,以确定并解决潜在的材料浪费问题。
案例研究:MedForm 的均匀壁厚
公司: MedForm
行业: 医疗设备
挑战: MedForm 的热成型医疗器械部件因壁厚不均匀而造成材料浪费。
解决方案 该公司重新设计了模具,以确保壁厚均匀,并进行了模流分析,以优化材料分布。
结果 MedForm 减少了 25% 的材料浪费,提高了材料利用率,降低了生产成本。重新设计的模具还提高了产品质量和一致性。
4.工艺参数优化
优化温度、压力和周期时间等工艺参数可以提高成型效率,减少缺陷,从而提高材料利用率。
实施:
- 使用实时监控系统跟踪和调整工艺参数,以实现最佳性能。
- 实施统计过程控制 (SPC),识别并消除过程变异。
- 对设备进行定期维护和校准,以确保稳定运行。
案例研究:清洁包装公司的实时监控
公司: 清洁包
行业: 消费品包装
挑战: 由于热成型过程中工艺参数的变化,CleanPack 面临着材料利用率不一致的问题。
解决方案 该公司采用实时监控系统跟踪关键工艺参数,并根据需要进行调整。他们还使用 SPC 来识别和处理工艺变化。
结果 CleanPack 将材料利用率提高了 18%,减少了浪费并提高了产品的一致性。实时监控系统可进行即时调整,确保最佳工艺性能。
5.废料的回收和再利用
回收和再利用废料可以减少对新原材料的需求,从而进一步提高材料利用率。
实施:
- 实施内部回收系统,对废料进行处理和再利用。
- 在非关键部件中使用再磨材料,以减少原始材料的消耗。
- 与供应商合作,制定塑料板的闭环回收计划。
案例研究:EcoTherm 的内部回收利用
公司: EcoTherm
行业: 可持续包装
挑战: EcoTherm 的目标是在热成型过程中回收和再利用废料,从而减少对环境的影响。
解决方案 该公司投资建立了一套内部回收系统,用于处理废料并将其重新投入生产。他们还与供应商合作,为塑料板制定了一个闭环回收计划。
结果 EcoTherm 对原始材料的依赖减少了 30%,大大提高了材料利用率。回收措施还增强了公司的可持续发展能力,降低了总体生产成本。
6.材料选择
选择更易于加工、成型性能更好的材料可以提高材料的利用率。
实施:
- 选择成型性高、收缩率低的材料,以减少浪费。
- 与材料供应商合作开发定制配方,优化成型效率。
- 进行材料试验,评估和比较不同塑料的性能。
案例研究:FlexiForm 的定制材料配方
公司: FlexiForm
行业: 消费电子产品
挑战: FlexiForm 希望为其热成型电子元件选择具有更好成型性能的材料,从而提高材料利用率。
解决方案 该公司与材料供应商合作开发定制塑料配方,以优化成型效率并减少浪费。他们进行了广泛的材料试验,以评估性能。
结果 FlexiForm 提高了 22% 的材料利用率,减少了浪费并提高了产品质量。定制配方具有更好的成型性能,从而提高了生产流程的效率。
7.员工培训和最佳做法
对员工进行最佳实践和高效材料处理技术的培训,可以大大提高材料的利用率。
实施:
- 定期举办有关高效材料处理和流程优化的培训课程。
- 制定材料处理和流程控制的标准操作程序 (SOP)。
- 鼓励员工不断改进和反馈,以发现和解决效率低下的问题。
案例研究:PackTech 的员工培训
公司: 包装技术
行业: 工业包装
挑战: 由于缺乏标准化程序和员工培训,PackTech 面临着材料利用率不一致的问题。
解决方案 该公司实施了一项全面的培训计划,重点是高效材料处理和流程优化。他们还制定了 SOP,以规范最佳实践。
结果 PackTech 将材料利用率提高了 15%,减少了浪费并提高了生产效率。培训计划增强了员工识别和解决低效问题的能力,培养了持续改进的文化。
结论
提高热成型操作中的材料利用率对于提高生产率、降低成本和减少对环境的影响至关重要。通过优化板材厚度、采用先进的切割和修边技术、改进模具设计、优化工艺参数、回收和再利用废料、选择正确的材料以及培训员工,企业可以显著提高材料利用率。
PackRight、AutoTrim、MedForm、CleanPack、EcoTherm、FlexiForm 和 PackTech 的真实案例研究展示了这些战略的实际效益。每家公司都成功地解决了各自面临的具体挑战,大幅提高了材料利用率,从而节约了成本,增强了可持续发展能力,并提高了产品质量。
随着制造业的不断发展,关注材料的利用率对于保持竞争力以及满足对可持续和具有成本效益的生产实践日益增长的需求至关重要。通过不断创新和改进工艺,制造商可以确保长期成功,并为更可持续的未来做出贡献。