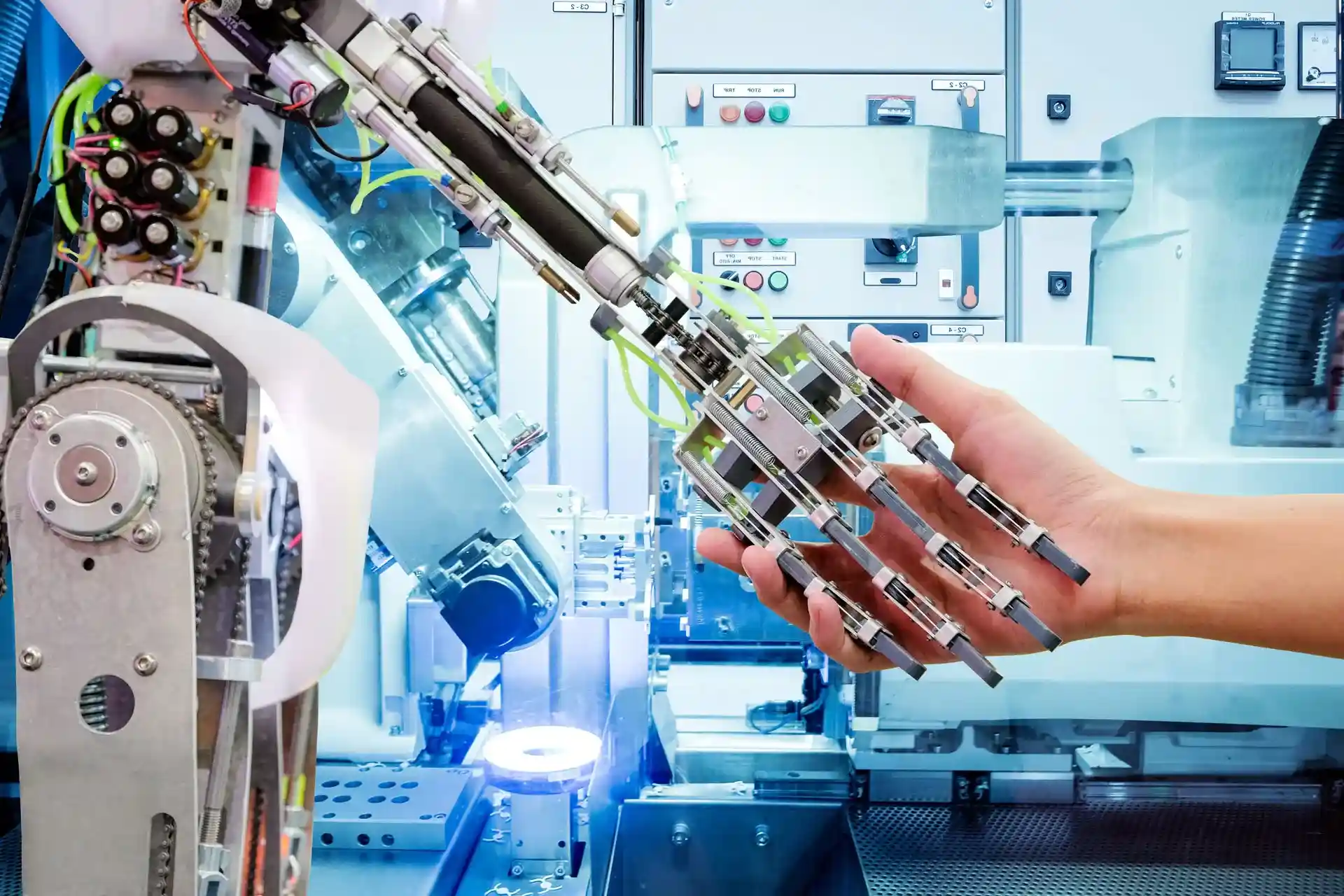
Reducing Scrap Rates in Thermoforming: Technologies and Processes
مقدمة
In the competitive landscape of modern manufacturing, reducing waste is a critical factor for both economic and environmental sustainability. In the thermoforming industry, high scrap rates can significantly impact profitability and resource efficiency. This article explores various technologies and processes aimed at minimizing scrap rates in thermoforming operations, providing a comprehensive guide for manufacturers seeking to optimize their production.
Understanding Scrap in Thermoforming
Scrap in thermoforming refers to any material that is not part of the finished product, including trimmings, defective parts, and setup sheets. High scrap rates can result from several factors:
- Material inconsistencies
- Improper heating
- Poor mold design
- Inefficient trimming
Technologies for Reducing Scrap Rates
1. Advanced Heating Systems
One of the primary causes of scrap in thermoforming is uneven or improper heating of the plastic sheet. Advanced heating systems ensure uniform temperature distribution, which is crucial for achieving consistent material properties.
Infrared Heating
Infrared heating systems use radiative heat transfer to evenly heat plastic sheets. They provide precise control over the heating process, reducing the likelihood of overheating or underheating.
Case Study: Precision Thermoforming Inc.
- Problem: High scrap rates due to uneven heating.
- الحل: Installed an infrared heating system with multiple zones to control temperature distribution.
- النتيجة: Scrap rates reduced by 20%, improving overall material utilization and product quality.
2. Automated Process Control
Automation in process control allows for real-time adjustments during thermoforming, reducing errors and improving consistency.
PLC Systems
Programmable Logic Controllers (PLC) can automate various aspects of the thermoforming process, from temperature control to vacuum and pressure settings.
Case Study: AutoForm Plastics
- Problem: Variability in product quality due to manual process control.
- الحل: Implemented a PLC system to automate heating, forming, and cooling cycles.
- النتيجة: Achieved a 15% reduction in scrap rates, with more consistent part quality and reduced cycle times.
3. High-Precision Molds
Mold design plays a crucial role in the thermoforming process. High-precision molds reduce material waste by ensuring accurate and repeatable part formation.
CNC Machined Molds
Computer Numerical Control (CNC) machining creates molds with high precision and repeatability, minimizing defects and improving part consistency.
Case Study: MoldMasters Corp.
- Problem: Frequent defects due to inconsistencies in mold dimensions.
- الحل: Transitioned to CNC machined molds for all thermoforming operations.
- النتيجة: Scrap rates decreased by 25%, with significant improvements in product uniformity and fit.
4. Material Selection and Testing
Selecting the right material for the thermoforming process is critical for minimizing scrap. Different materials have varying properties that can affect formability and final product quality.
Material Testing
Conducting thorough material testing before full-scale production helps identify the best material for the application, reducing trial-and-error waste.
Case Study: PolyForm Solutions
- Problem: High scrap rates due to using a material that was prone to cracking.
- الحل: Conducted extensive material testing and switched to a more suitable polymer blend.
- النتيجة: Reduced scrap rates by 30%, with enhanced product durability and performance.
5. Efficient Trimming Techniques
Trimming is an essential part of the thermoforming process, but it can also be a significant source of scrap. Implementing efficient trimming techniques can drastically reduce waste.
Laser Trimming
Laser trimming provides precise and clean cuts, minimizing material waste and improving edge quality.
Case Study: TrimTech Industries
- Problem: Excessive waste from manual trimming operations.
- الحل: Invested in a laser trimming system for precision cuts.
- النتيجة: Scrap rates reduced by 18%, with improved part aesthetics and dimensional accuracy.
Processes for Reducing Scrap Rates
1. Lean Manufacturing Principles
Adopting lean manufacturing principles can help identify and eliminate waste throughout the thermoforming process.
Just-In-Time (JIT) Production
JIT production minimizes excess inventory and reduces the chances of producing defective parts.
Case Study: LeanForm LLC
- Problem: High scrap rates due to overproduction and defective inventory.
- الحل: Implemented JIT production to produce parts only as needed.
- النتيجة: Scrap rates dropped by 20%, with better inventory management and reduced storage costs.
2. Statistical Process Control (SPC)
SPC involves using statistical methods to monitor and control the manufacturing process, ensuring that it operates at its full potential.
Control Charts
Control charts help track process variability and identify trends that may indicate potential issues.
Case Study: SPC Plastics
- Problem: Inconsistent product quality leading to high scrap rates.
- الحل: Implemented SPC with control charts to monitor key process parameters.
- النتيجة: Achieved a 15% reduction in scrap rates by addressing process variability issues in real-time.
3. Continuous Improvement (Kaizen)
Kaizen focuses on continuous, incremental improvements in the manufacturing process to reduce waste and improve efficiency.
Employee Involvement
Encouraging employees to identify and suggest improvements can lead to innovative solutions for reducing scrap.
Case Study: Kaizen Thermoformers
- Problem: Persistent high scrap rates with no apparent solution.
- الحل: Launched a Kaizen initiative involving all employees in identifying waste reduction opportunities.
- النتيجة: Scrap rates decreased by 22%, with ongoing improvements in process efficiency and employee morale.
4. Training and Skill Development
Well-trained operators are less likely to make mistakes that lead to scrap. Investing in ongoing training and skill development is crucial.
Certification Programs
Certification programs ensure that operators are knowledgeable about best practices and the latest technologies.
Case Study: CertiForm Plastics
- Problem: Operator errors leading to high scrap rates.
- الحل: Implemented a certification program for all machine operators.
- النتيجة: Reduced scrap rates by 17%, with higher operator competency and process understanding.
5. Preventive Maintenance
Regular maintenance of thermoforming equipment can prevent breakdowns and reduce the occurrence of defects.
Scheduled Maintenance
Implementing a preventive maintenance schedule ensures that all equipment is in optimal working condition.
Case Study: MaintenForm Inc.
- Problem: Frequent equipment failures resulting in high scrap rates.
- الحل: Established a preventive maintenance program with regular equipment checks and servicing.
- النتيجة: Scrap rates reduced by 20%, with improved machine reliability and uptime.
الخاتمة
Reducing scrap rates in thermoforming requires a multifaceted approach that includes advanced technologies, efficient processes, and continuous improvement strategies. By investing in advanced heating systems, automated process controls, high-precision molds, and efficient trimming techniques, manufacturers can significantly reduce material waste. Additionally, adopting lean manufacturing principles, statistical process control, and continuous improvement initiatives further enhances production efficiency and product quality.
The real-life case studies of Precision Thermoforming Inc., AutoForm Plastics, MoldMasters Corp., PolyForm Solutions, TrimTech Industries, LeanForm LLC, SPC Plastics, Kaizen Thermoformers, CertiForm Plastics, and MaintenForm Inc. illustrate the successful implementation of these strategies. Each company addressed their specific challenges and achieved substantial improvements in scrap reduction, leading to increased profitability and sustainability.
As the thermoforming industry continues to evolve, focusing on scrap reduction will remain a key priority for manufacturers. By embracing new technologies and optimizing processes, companies can achieve long-term success and contribute to a more sustainable future.