Desafíos comunes en el desmoldeo
Aunque los sistemas de desmoldeo aportan importantes ventajas, también se enfrentan a problemas que pueden afectar a la eficacia de la producción y a la calidad del producto. A continuación se indican algunos de los problemas típicos a los que se enfrenta el proceso de desmoldeo:
Piezas pegajosas:La adherencia entre el molde y el producto moldeado es un problema frecuente, a menudo causado por una refrigeración inadecuada o defectos en el diseño del molde. Si la pieza no se separa completamente del molde, pueden producirse retrasos en la producción, defectos o incluso daños tanto en el molde como en el producto acabado.

Deformación o daños:Las piezas con paredes finas o estructuras delicadas son especialmente vulnerables a la deformación o agrietamiento durante el desmoldeo. Una fuerza de expulsión excesiva o desigual puede hacer que estas piezas se deformen, se agrieten o pierdan la forma prevista, lo que provoca defectos de calidad y un mayor índice de desechos.
Desgaste mecánico:El uso continuado de los sistemas de desmoldeo puede desgastar los componentes mecánicos, como los pasadores eyectores, las correderas y los empujadores. Con el tiempo, este desgaste afecta a la fiabilidad del sistema, lo que provoca un aumento de los requisitos de mantenimiento, una reducción de la eficiencia y tiempos de inactividad imprevistos.
Residuos materiales:El material plástico residual de ciclos de moldeo anteriores puede acumularse en el molde, especialmente en sistemas que utilizan expulsión neumática o hidráulica. Esta acumulación puede obstruir los orificios de ventilación, afectar al rendimiento del sistema y dar lugar a piezas de baja calidad en ciclos posteriores.
Soluciones:
- Aplique agentes desmoldeantes:El uso de agentes desmoldeantes puede reducir significativamente los problemas de adherencia, facilitando un desmoldeo más suave de las piezas. Esto es especialmente útil para moldes con diseños intrincados o complejos.
- Optimizar la refrigeración y la fuerza de eyección: Ajuste los tiempos de enfriamiento para garantizar que las piezas se solidifican adecuadamente antes de la expulsión. Del mismo modo, calibre la fuerza de expulsión para aplicarla uniformemente, minimizando el riesgo de deformación o daño de la pieza durante la extracción.
- Realice un mantenimiento periódico: Programe un mantenimiento rutinario para inspeccionar y sustituir los componentes desgastados, garantizando un funcionamiento sin problemas y prolongando la vida útil del sistema. Esto incluye la limpieza de las superficies del molde para evitar la acumulación de material y la comprobación de los signos de desgaste de las piezas mecánicas.
Si abordan estos problemas de forma proactiva y aplican estrategias eficaces, los fabricantes pueden mejorar la calidad de la producción, reducir los tiempos de inactividad y prolongar la vida útil de sus sistemas de desmoldeo.
Avances en la tecnología de desmoldeo
Con la creciente demanda de precisión, eficiencia y sostenibilidad en la fabricación, los sistemas de desmoldeo están evolucionando con la ayuda de tecnologías avanzadas. Estas innovaciones no sólo abordan retos comunes, sino que también aumentan la productividad, minimizan el tiempo de inactividad y mejoran el rendimiento general del sistema. Algunos de los avances clave son:
1. Sensores inteligentes
La introducción de sensores inteligentes ha transformado los sistemas de desmoldeo al permitir el seguimiento en tiempo real de parámetros críticos como la fuerza, la temperatura y el tiempo. Estos sensores ofrecen un control preciso durante el proceso de desmoldeo, garantizando que las fuerzas aplicadas sean óptimas y constantes. Al supervisar continuamente las condiciones del molde, los sensores inteligentes ayudan a reducir errores, evitar daños en las piezas y mejorar la calidad general de las piezas, al tiempo que optimizan los ciclos de producción.
Beneficios:
- Control más preciso del proceso de expulsión.
- Ajustes en tiempo real para evitar defectos.
- Mayor fiabilidad y coherencia en la producción.
2. Robótica adaptativa
Los sistemas robóticos que incorporan inteligencia artificial (IA) y aprendizaje automático son cada vez más versátiles. Estos robots son capaces de adaptarse a diferentes formas, tamaños y materiales, ajustando sus movimientos y fuerza en consecuencia. Esta flexibilidad los hace especialmente útiles para manipular piezas delicadas o complejas. Al reducir la intervención humana, estos robots también ayudan a acelerar los ciclos de producción.
Beneficios:
- Flexible y programable para diferentes formas y tamaños de productos.
- Mayor precisión en la manipulación de piezas delicadas o intrincadas.
Reducción de la dependencia de la intervención manual, aumentando la automatización y la eficacia.
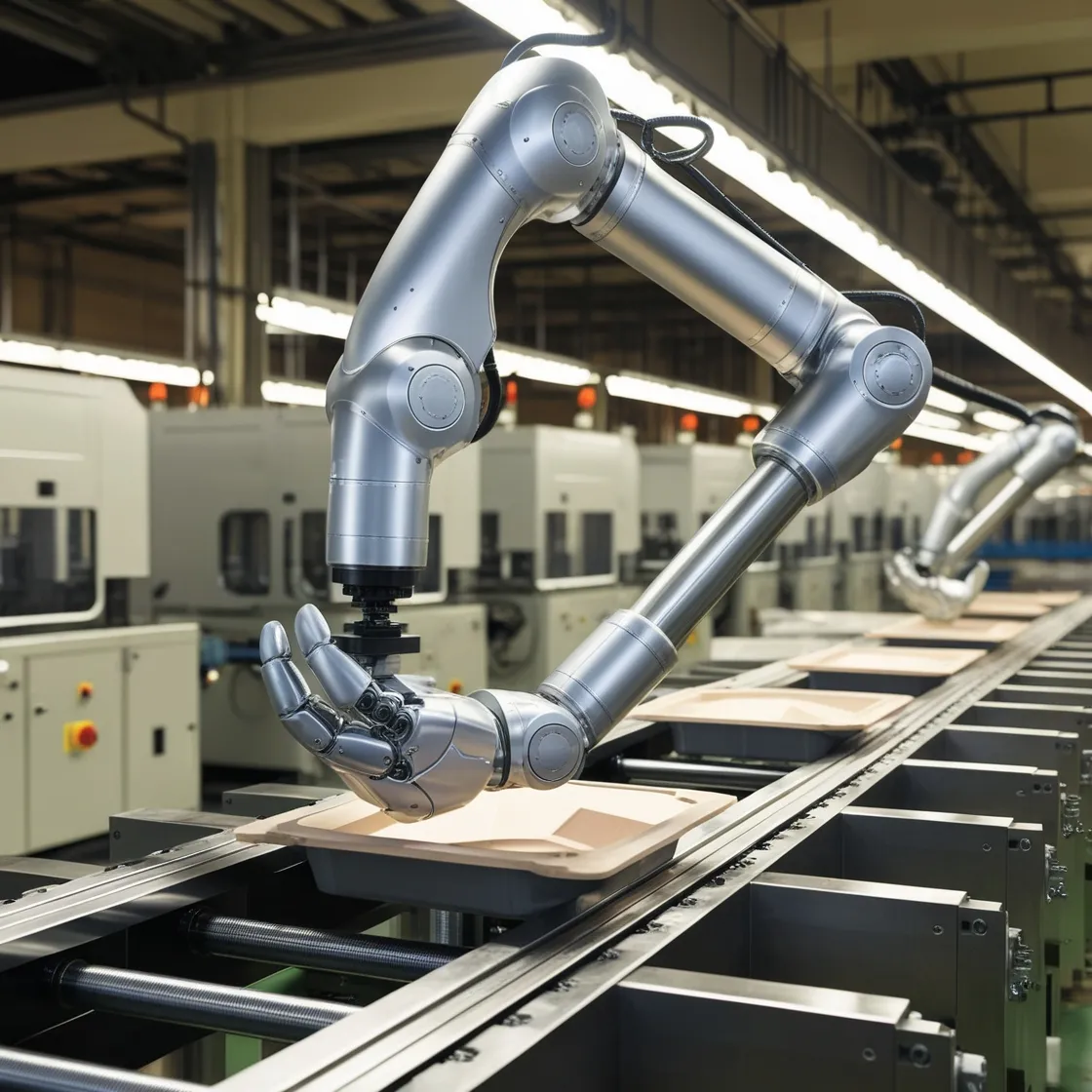
3. Componentes autolubricantes
Los avances en materiales han permitido crear piezas autolubricantes para sistemas de desmoldeo. Los materiales utilizados en pasadores eyectores, correderas y otros componentes móviles reducen la fricción y el desgaste, eliminando la necesidad de lubricación frecuente. Esto no sólo reduce los requisitos de mantenimiento, sino que también prolonga la vida útil de las piezas, garantizando un funcionamiento más suave con menos tiempo de inactividad.
Beneficios:
- Reducción de las necesidades de mantenimiento y de los tiempos de inactividad.
- Mayor durabilidad y vida útil de los componentes del sistema.
Funcionamiento más suave con menos fricción, lo que mejora la eficiencia general.
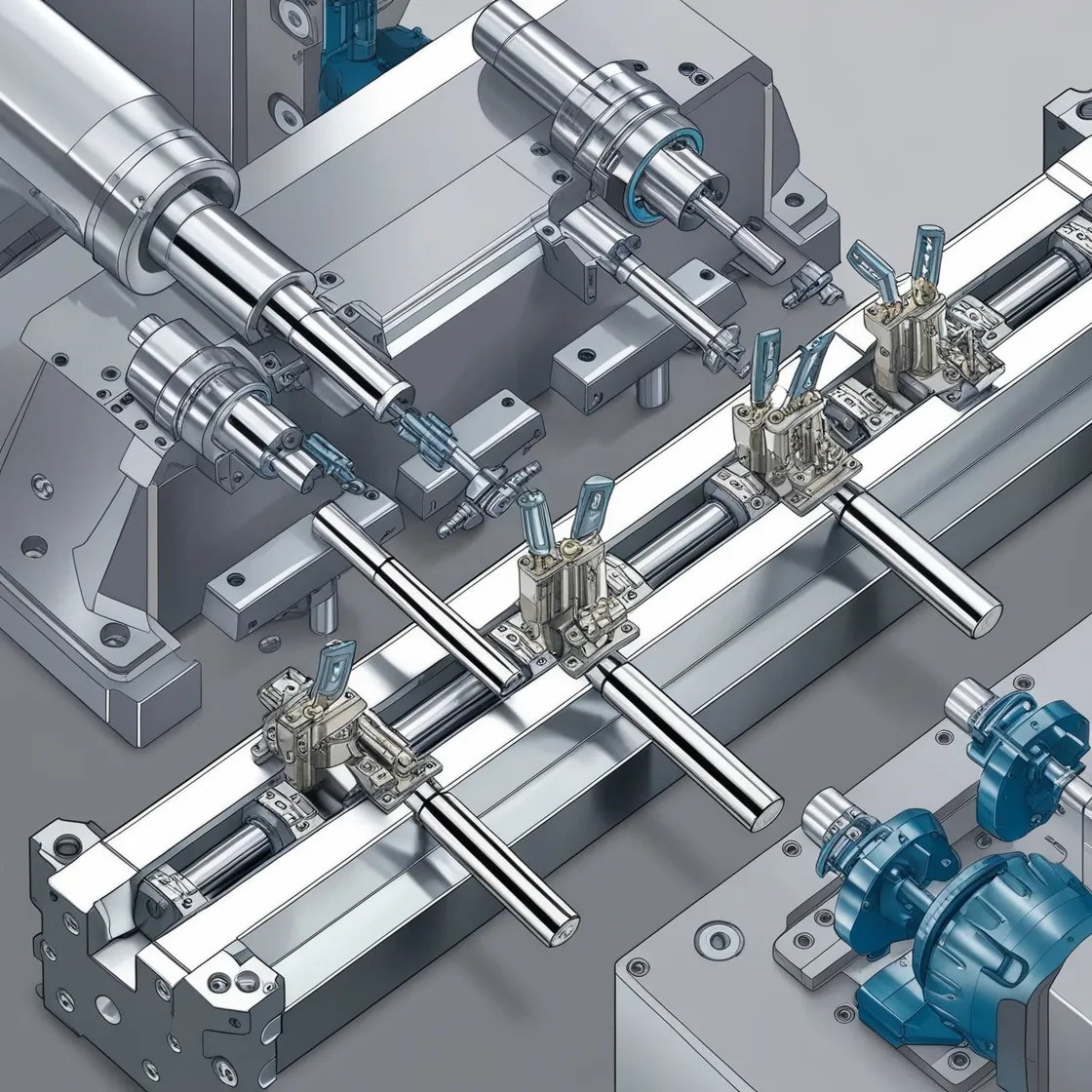
4. Sistemas ecológicos
A medida que la sostenibilidad se convierte en una prioridad fundamental para los fabricantes, los sistemas neumáticos e hidráulicos energéticamente eficientes ganan popularidad. Estos sistemas ecológicos están diseñados para minimizar el uso de energía, reducir el impacto medioambiental y disminuir los costes operativos. Al optimizar el uso del aire comprimido y los fluidos hidráulicos, estos sistemas proporcionan un alto rendimiento a la vez que fomentan el ahorro energético y reducen la huella de carbono.
Beneficios:
- Menor consumo de energía y menor impacto ambiental.
- Ahorro de costes gracias al diseño de sistemas energéticamente eficientes.
- Cumplimiento de las normas de sostenibilidad y reducción de la huella de carbono.
Al adoptar estos avances, los fabricantes pueden aumentar la eficiencia de la producción, reducir los costes operativos y mantener una producción de alta calidad. Estas innovaciones permiten satisfacer la creciente demanda de procesos de producción más rápidos, precisos y sostenibles desde el punto de vista medioambiental.
Tendencias futuras en sistemas de desmoldeo
A medida que el sector del termoformado sigue evolucionando, la atención se centra cada vez más en una mayor automatización, una mayor sostenibilidad y soluciones más personalizadas. El futuro de los sistemas de desmoldeo está preparado para adoptar tecnologías y prácticas de vanguardia que darán forma al sector en los próximos años. Estas son algunas de las tendencias clave que se espera que dominen el sector:
1. Mayor automatización
El futuro de los sistemas de desmoldeo está en las líneas de producción totalmente automatizadas, donde las soluciones de desmoldeo robotizadas se convertirán en la norma, especialmente en entornos de fabricación de gran volumen. La automatización agilizará todo el proceso de producción, desde la apertura del molde hasta la expulsión de la pieza, reduciendo la intervención humana y minimizando el riesgo de errores. Estos sistemas avanzados mejorarán la velocidad, la precisión y la uniformidad, facilitando la gestión de la producción a gran escala sin comprometer la calidad de las piezas.
Beneficios esperados:
- Mayor velocidad de producción y menores costes de mano de obra.
- Mayor precisión y consistencia en la manipulación de piezas.
- Mayor eficacia operativa con menos intervención manual.
2. Integración con IoT (Internet de las cosas)
La integración de tecnología inteligente a través del Internet de las Cosas (IoT) revolucionará los sistemas de desmoldeo. Al conectar los equipos de desmoldeo a las redes IoT, los fabricantes podrán supervisar el rendimiento del sistema en tiempo real y recibir alertas de mantenimiento predictivo. Esta conectividad proporcionará información valiosa sobre el estado del sistema, lo que permitirá realizar reparaciones preventivas antes de que se produzcan averías, minimizar el tiempo de inactividad y optimizar los programas de mantenimiento para obtener el máximo tiempo de actividad.
Beneficios esperados:
- Control en tiempo real de los parámetros críticos del sistema.
- Mantenimiento predictivo para evitar averías en los equipos.
- Mejora de la toma de decisiones gracias a la información basada en datos.
3. Prácticas sostenibles
Con la creciente preocupación por el medio ambiente y el énfasis en la responsabilidad corporativa, la industria del termoformado está dando prioridad a la sostenibilidad. Los futuros sistemas de desmoldeo se centrarán en diseños ecológicos que minimicen el consumo de energía, reduzcan el desperdicio de material y optimicen el uso de los recursos. Mediante la adopción de prácticas sostenibles, como sistemas neumáticos o hidráulicos energéticamente eficientes, los fabricantes pueden alinearse con los objetivos globales de sostenibilidad, reducir su huella de carbono y disminuir los costes operativos.
Beneficios esperados:
- Reducción del consumo de energía y de los costes operativos.
- Menor impacto ambiental gracias a una gestión optimizada de los recursos.
- Cumplimiento de una normativa medioambiental cada vez más estricta.
A medida que se desarrollen estas tendencias, el futuro de los sistemas de desmoldeo en la industria del termoformado se caracterizará por una mayor automatización, una conectividad más inteligente, prácticas más sostenibles y una mayor personalización. Al adoptar estas innovaciones, los fabricantes podrán lograr una mayor eficiencia, un mejor control de calidad y un enfoque más sostenible de la producción.
Conclusión
El diseño de sistemas de desmoldeo eficaces implica un profundo conocimiento de la geometría del producto, las propiedades del material, los requisitos de tiempo de ciclo y las necesidades de mantenimiento. Aunque los problemas como las piezas que se pegan, la deformación y el desgaste mecánico son comunes, pueden mitigarse mediante un diseño adecuado del sistema y un mantenimiento regular. Los avances en la tecnología de desmoldeo, como los sensores inteligentes, la robótica adaptativa y los sistemas ecológicos, están estableciendo nuevos estándares para la industria del termoformado. Adoptar estas innovaciones ayudará a los fabricantes no sólo a optimizar sus procesos de producción, sino también a mantenerse a la vanguardia en un mercado cada vez más competitivo y orientado a la sostenibilidad. Al tener en cuenta tanto las consideraciones de diseño como los avances tecnológicos, las empresas pueden lograr una mayor eficiencia, menores costes operativos y una mejor calidad del producto.