¿Qué es un reductor?
Un engranaje reductor, también conocido como reductor de engranajes o caja de engranajes, es un componente mecánico crucial que se utiliza para reducir la velocidad de rotación de un motor y, al mismo tiempo, aumentar el par de salida. Este proceso es esencial en diversas aplicaciones industriales, incluidas las máquinas de termoformado, donde se requiere un control preciso de la velocidad y la potencia para garantizar un rendimiento óptimo.
En un engranaje reductor, la función principal es convertir el movimiento de rotación de alta velocidad en una salida de menor velocidad y mayor par, lo que lo convierte en un elemento vital para controlar la maquinaria y accionar componentes en el proceso de producción. Esta conversión permite un funcionamiento más suave, una mayor eficiencia energética y un manejo más eficaz de cargas pesadas. La clave para entender cómo funciona un engranaje reductor reside en la relación de transmisión, que dicta la cantidad de reducción de velocidad y aumento de par.
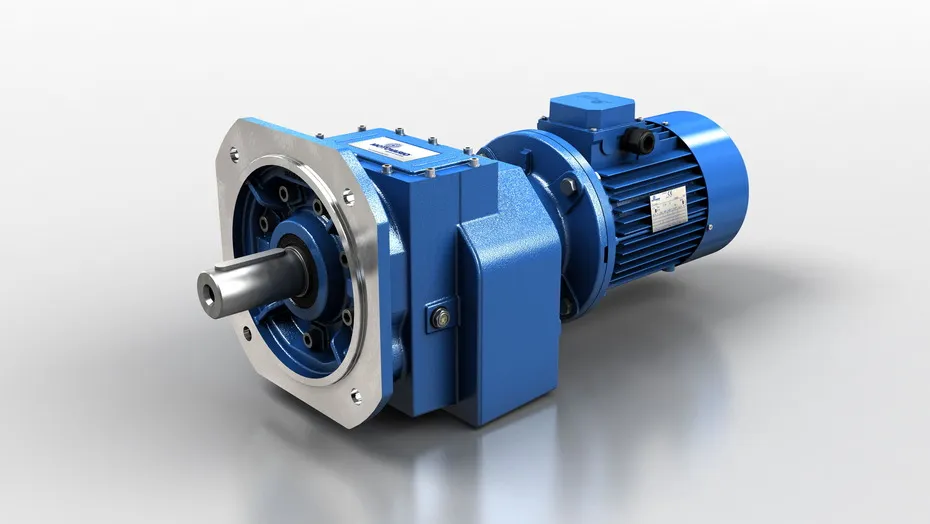
Funcionamiento de un reductor
Los reductores suelen constar de dos o más engranajes: un engranaje motriz (conectado al motor) y un engranaje conducido (conectado al eje de salida). Los dos engranajes funcionan con tamaños diferentes, siendo el engranaje motor más pequeño y el engranaje conducido más grande. Esta diferencia de tamaño determina cuánto se reducirá la velocidad y cuánto aumentará el par. La mecánica básica de un engranaje reductor consta de los siguientes pasos:
1.Relación de transmisión: La relación de transmisión es el factor más importante para determinar la reducción de la velocidad y el aumento del par. Cuando gira el engranaje motriz más pequeño, acciona el engranaje conducido más grande, que gira más despacio pero genera mayor fuerza.
2.Reducción de velocidad: Debido al menor tamaño del engranaje motriz y al mayor tamaño del engranaje conducido, el engranaje mayor se mueve a menor velocidad, pero con mayor fuerza. Esto se conoce como reducción de velocidad, en la que una velocidad de rotación mayor se convierte en una menor.
3.Aumento del par: A medida que disminuye la velocidad de rotación, aumenta proporcionalmente el par (fuerza de rotación). Esta característica es especialmente beneficiosa en aplicaciones que requieren un par elevado para mover objetos pesados o vencer resistencias, como los componentes de una termoformadora.
Tipos de reductoras
Existen varios tipos de reductores, cada uno con características únicas que los hacen adecuados para distintas aplicaciones:
- Engranajes rectos:Los engranajes rectos son el tipo más básico de engranaje, con dientes rectos alineados en paralelo al eje. Suelen utilizarse en cajas reductoras para aplicaciones de velocidad baja a media, y ofrecen una solución sencilla y eficaz para muchas necesidades industriales.
- Engranajes helicoidales:Los engranajes helicoidales tienen los dientes dispuestos en ángulo con respecto al eje, lo que permite un funcionamiento más suave y silencioso en comparación con los engranajes rectos. Se utilizan mucho en aplicaciones que requieren un mayor rendimiento y son especialmente eficaces cuando es necesario reducir el ruido y las vibraciones.
- Engranajes cónicos:Los engranajes cónicos se utilizan para transmitir potencia entre ejes que no son paralelos, normalmente en ángulo recto. Suelen utilizarse en sistemas mecánicos más complejos en los que se necesitan cambios direccionales en la transmisión de potencia.
- Engranajes helicoidales:Los engranajes helicoidales están formados por un tornillo (sinfín) y un engranaje (rueda helicoidal). Esta configuración proporciona una elevada reducción del par en un diseño compacto, lo que los hace ideales para aplicaciones en las que las limitaciones de espacio son un problema.
Aplicaciones de los reductores
Los reductores se utilizan en una amplia gama de aplicaciones industriales en las que es esencial un control preciso de la velocidad y un aumento del par. Algunos de los usos más comunes son:
- Máquinas de termoformado:En las máquinas de termoformado, los engranajes reductores controlan la velocidad de varias etapas del proceso, como las estaciones de formado, corte y apilado. Al reducir la velocidad del motor, el engranaje permite un movimiento preciso de las láminas de plástico, los moldes y otros componentes, garantizando una calidad de producción constante.
- Sistemas transportadores:Los sistemas transportadores se basan en engranajes reductores para regular la velocidad de las cintas, garantizando que los materiales se muevan a una velocidad controlada y constante. Esto es especialmente importante en las plantas de fabricación a gran escala, donde la manipulación eficiente de materiales es crucial.
- Equipos industriales:Los reductores también se utilizan en diversos tipos de maquinaria industrial, como equipos de envasado, maquinaria agrícola y fabricación de automóviles, donde se requiere un par elevado para accionar aplicaciones de gran potencia.
Ventajas de utilizar un reductor
El uso de reductores ofrece varias ventajas, sobre todo en máquinas industriales como los sistemas de termoformado. Algunas de las ventajas más significativas son:
- Control mejorado:Los reductores proporcionan un control preciso de la velocidad y el par, lo que resulta esencial en aplicaciones que requieren un movimiento constante y fiable. En las máquinas de termoformado, esto permite un funcionamiento suave en las distintas fases del proceso.
- Mayor par motor:Una de las principales ventajas de utilizar un reductor es el aumento del par motor. Al reducir la velocidad del motor se obtiene un mayor par de salida, necesario para accionar componentes pesados o para tareas que impliquen una resistencia significativa.
- Eficiencia energética:Al optimizar la velocidad del motor y convertirla en par, los reductores pueden ayudar a mejorar la eficiencia energética de la maquinaria. Esto puede dar lugar a un menor consumo de energía, lo que reduce los costes operativos a lo largo del tiempo.
- Diseño compacto:Los reductores suelen ser compactos, lo que les permite encajar en máquinas con espacio limitado. A pesar de su reducido tamaño, pueden proporcionar la transmisión de potencia necesaria para accionar componentes grandes y pesados en máquinas como los sistemas de termoformado.
- Durabilidad:Diseñados para soportar grandes cargas y un uso continuo, los reductores están hechos para durar. Esto los hace ideales para la exigente naturaleza de las máquinas de termoformado, que a menudo funcionan en entornos de muchos ciclos.
- Funcionamiento suave:Los engranajes reductores ayudan a reducir las vibraciones y garantizan un funcionamiento suave, lo que es fundamental para la precisión que requieren las máquinas de termoformado. Esto se traduce en un rendimiento más silencioso y uniforme de la máquina.
- Personalización:Los reductores están disponibles en una gran variedad de relaciones, lo que permite personalizarlos para satisfacer las necesidades específicas de una máquina determinada. Ya se trate de ajustar la velocidad o el par, los engranajes pueden adaptarse para optimizar el rendimiento de la máquina en diversas aplicaciones.
Desventajas de las reductoras
Aunque los reductores ofrecen numerosas ventajas, hay que tener en cuenta algunas limitaciones y contrapartidas:
- Tamaño y peso:En función de la relación de reducción, el tamaño y el peso del conjunto de engranajes pueden aumentar considerablemente. Esto puede hacer que la termoformadora sea más voluminosa, reduciendo su compacidad y dificultando potencialmente su mantenimiento.
- Complejidad y coste:Los reductores de alta calidad pueden ser complejos de diseñar y fabricar, lo que se traduce en mayores costes iniciales. Los costes de mantenimiento también pueden ser mayores debido a la necesidad de conocimientos y piezas especializados.
- Requisitos de mantenimiento:El mantenimiento regular es necesario para garantizar el rendimiento a largo plazo de los reductores. Esto incluye la lubricación y la sustitución ocasional de componentes como juntas, cojinetes o engranajes. Un mantenimiento inadecuado puede reducir la eficacia o provocar averías en los engranajes.
- Generación de calor:La fricción dentro de los engranajes puede generar calor, sobre todo cuando se reducen las velocidades de forma significativa. Esto puede requerir sistemas de refrigeración adicionales para evitar el sobrecalentamiento y posibles daños en la máquina.
- Pérdidas de eficiencia:A pesar de sus ventajas, los reductores no están exentos de inconvenientes. Parte de la energía se pierde inevitablemente debido a la fricción y la generación de calor, lo que reduce la eficiencia global del sistema. La pérdida de eficiencia puede ser más pronunciada si la relación de transmisión es demasiado alta.
- Velocidad limitada:Los reductores están diseñados para funcionar dentro de unos márgenes de velocidad específicos. Las variaciones extremas de velocidad pueden no ser ideales para determinadas aplicaciones, lo que limita su flexibilidad en máquinas que requieren una amplia variedad de velocidades para diferentes series de producción.
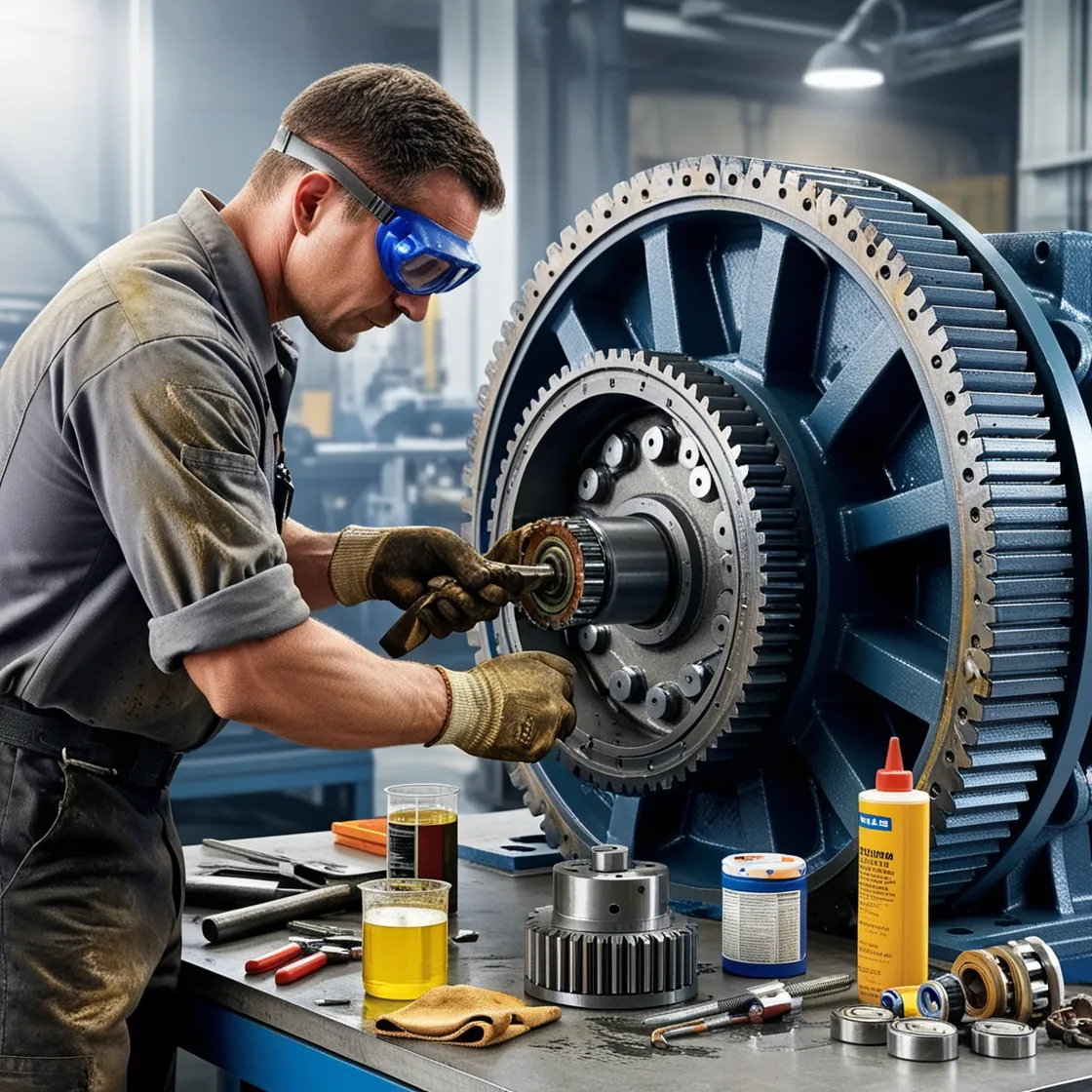
Potencia nominal de los reductores de velocidad
La potencia nominal de un reductor de velocidad (reductor de engranajes) se refiere a la cantidad de potencia mecánica que puede manejar mientras convierte la velocidad en par. Este factor es crucial a la hora de seleccionar el tipo adecuado de reductor para aplicaciones específicas, especialmente en máquinas de termoformado, donde la potencia nominal determina cuánta carga puede soportar eficientemente el sistema.
Los reductores de velocidad tienen diferentes potencias, cada una de ellas adecuada para aplicaciones específicas:
1.Reductores de velocidad de baja potencia (hasta 1 CV o 750 W): Suelen utilizarse en maquinaria pequeña o aplicaciones industriales ligeras. Son compactas, rentables y eficientes para cargas pequeñas, pero no pueden realizar tareas pesadas.
2.Reductores de velocidad de potencia media (de 1 a 10 CV o de 750 W a 7,5 kW): Se suelen encontrar en maquinaria industrial, cintas transportadoras pequeñas y medianas y máquinas de uso moderado, como pequeños sistemas de termoformado. Ofrecen un buen equilibrio entre potencia y tamaño.
3.Reductores de velocidad de alta potencia (de 10 a 100 CV o de 7,5 kW a 75 kW): Se utilizan en máquinas industriales de mayor tamaño y aplicaciones de alto par, como las grandes termoformadoras. Están diseñados para soportar cargas pesadas y un funcionamiento continuo a largo plazo.
4.Reductores de velocidad de muy alta potencia (100 CV o 75 kW y superiores): Se utilizan en las aplicaciones más pesadas, como acerías, cementeras y sistemas de termoformado a gran escala. Estos reductores son capaces de manejar salidas de par extremadamente altas y funcionan con gran eficiencia.
Factores clave que influyen en la selección de la potencia nominal
A la hora de elegir la potencia adecuada para un reductor de velocidad, hay que tener en cuenta varios factores:
- Requisitos de par:Un par más alto requiere una potencia más elevada, por lo que es esencial elegir la relación de transmisión y el tamaño adecuados para soportar las cargas previstas.
- Relación de reducción de velocidad:Una reducción significativa de la velocidad requiere un reductor más potente para soportar el aumento de carga y mantener la eficiencia.
- Tamaño y carga de la máquina:Las máquinas más grandes o las que manejan cargas más pesadas necesitan reductores de potencia más altos para garantizar un funcionamiento suave y eficaz.
- Ciclo de trabajo:Las operaciones continuas o las condiciones de carga variable pueden requerir reductores de velocidad más robustos para mantener el rendimiento a largo plazo.
- Eficiencia:Los reductores de mayor potencia suelen ser más eficaces para aplicaciones de par elevado, pero tienen un coste inicial y una demanda de mantenimiento mayores.
Conclusión
Los reductores son componentes integrales de las máquinas de termoformado, ya que ofrecen el control necesario sobre la velocidad y el par para garantizar un funcionamiento eficaz. Aunque tienen algunas limitaciones, como el tamaño, el coste y las necesidades de mantenimiento, sus ventajas, como el aumento del par, la mejora del control y la eficiencia energética, los hacen muy valiosos en aplicaciones industriales. Conocer las diferentes potencias y sus aplicaciones puede ayudar a los fabricantes a seleccionar el reductor adecuado para satisfacer las demandas específicas de sus procesos de producción, garantizando un rendimiento constante y de alta calidad y un funcionamiento eficaz de la maquinaria.