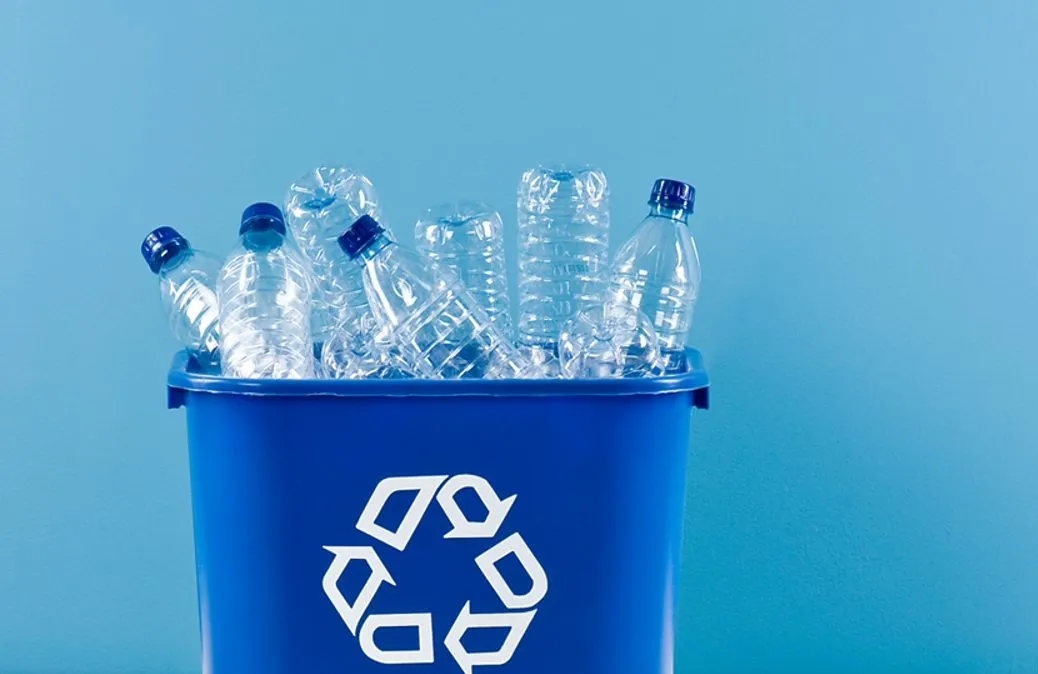
Transformación digital en el termoformado: El papel del IoT y la Industria 4.0
En el panorama en rápida evolución de la fabricación, la transformación digital se ha convertido en una fuerza fundamental que impulsa la innovación y la eficiencia. El termoformado, una versátil técnica de procesamiento de plásticos, no es una excepción a esta transformación. Con la llegada de tecnologías como el Internet de las Cosas (IoT) y la Industria 4.0, las máquinas de termoformado están experimentando cambios significativos, revolucionando la forma en que se fabrican los productos de plástico. En este artículo, exploramos el papel del IoT y la Industria 4.0 en la transformación digital del termoformado, examinando cómo estas tecnologías están remodelando el sector e impulsando el valor para las empresas.
Introducción a la transformación digital en el termoformado
El termoconformado es un proceso de fabricación que consiste en calentar una lámina de plástico hasta una temperatura flexible, darle una forma específica mediante un molde y, a continuación, enfriarla para crear un producto acabado. Tradicionalmente, las máquinas de termoformado se manejaban manualmente o con una automatización limitada. Sin embargo, el auge de las tecnologías digitales ha dado paso a una nueva era de automatización, conectividad y toma de decisiones basada en datos en el termoformado.
El papel del IoT en el termoformado
1. Supervisión y control en tiempo real
Los sensores IoT integrados en las máquinas de termoformado recopilan datos en tiempo real sobre diversos parámetros, como la temperatura, la presión y el tiempo de ciclo. Estos datos se transmiten a una plataforma centralizada donde pueden analizarse y visualizarse en tiempo real. Los operarios pueden supervisar a distancia el rendimiento de la máquina, identificar posibles problemas y tomar decisiones informadas para optimizar los procesos de producción.
Caso práctico 1: Supervisión remota en ABC Packaging Solutions ABC Packaging Solutions, una empresa de termoformado, implementó sensores IoT en sus máquinas de termoformado para supervisar parámetros cruciales como la temperatura de calentamiento y la alineación del molde. Gracias a la supervisión en tiempo real, pudieron detectar desviaciones en los parámetros del proceso y tomar medidas correctivas a distancia, lo que redujo el tiempo de inactividad y aumentó el tiempo de actividad de la máquina en 15%.
2. Mantenimiento predictivo
Al analizar los datos históricos y supervisar el rendimiento de la máquina en tiempo real, la tecnología IoT permite realizar un mantenimiento predictivo de las máquinas de termoformado. Los algoritmos de análisis predictivo pueden detectar patrones y anomalías indicativos de posibles fallos en los equipos. Este enfoque proactivo permite programar las actividades de mantenimiento antes de que se produzcan problemas, lo que minimiza el tiempo de inactividad y maximiza el tiempo de actividad de la máquina.
Caso práctico 2: Implantación del mantenimiento predictivo en XYZ Plastics XYZ Plastics, una empresa de termoformado, implantó un programa de mantenimiento predictivo mediante sensores IoT y análisis de datos. Mediante el análisis de los datos de la máquina, identificaron signos tempranos de desgaste del equipo y posibles fallos. Esto les permitió programar el mantenimiento durante el tiempo de inactividad planificado, reduciendo el tiempo de inactividad no programado en 20% y ampliando la vida útil de la máquina.
3. Control de calidad mejorado
Los sensores habilitados para IoT proporcionan información detallada sobre el proceso de termoformado, lo que permite mejorar el control de calidad. Al supervisar parámetros como el grosor del material, la alineación del molde y las dimensiones del producto, los fabricantes pueden identificar defectos o desviaciones de las especificaciones en tiempo real. Las alertas automáticas pueden instar a los operarios a tomar medidas correctivas, garantizando una calidad constante del producto y reduciendo los residuos.
Caso práctico 3: Optimización del control de calidad en DEF Industries DEF Industries, una empresa de termoformado, implementó sensores IoT para la supervisión del control de calidad en tiempo real. Mediante el análisis de los datos recopilados durante el proceso de conformado, identificaron áreas de variabilidad e implementaron ajustes en el proceso para mejorar la consistencia del producto. El resultado fue una reducción de 30% en las tasas de rechazo y una mayor satisfacción del cliente.
El papel de la Industria 4.0 en el termoformado
1. Integración de sistemas ciberfísicos
La Industria 4.0 se caracteriza por la integración de sistemas ciberfísicos, en los que los procesos físicos se conectan a sistemas digitales a través de dispositivos IoT y redes de comunicación. Las máquinas de termoformado equipadas con capacidades de Industria 4.0 se convierten en sistemas interconectados que intercambian datos e información sin fisuras, lo que permite la toma de decisiones y la optimización en tiempo real.
Caso práctico 4: Integración ciberfísica en GHI Manufacturing GHI Manufacturing, una empresa de termoformado, integró sus máquinas de termoformado con un sistema de control centralizado como parte de su iniciativa Industria 4.0. Esto les permitió sincronizar los procesos de producción, optimizar la utilización de las máquinas y realizar un seguimiento de las métricas de producción en tiempo real. Como resultado, consiguieron un aumento de 25% en la eficacia general de los equipos (OEE) y redujeron los plazos de entrega en 15%.
2. Integración de la fábrica inteligente
Los principios de la Industria 4.0 van más allá de las máquinas individuales y abarcan instalaciones de producción enteras. Las empresas de termoformado están adoptando el concepto de fábrica inteligente, en la que máquinas, procesos y sistemas interconectados se comunican y colaboran de forma autónoma. A través de sistemas de control centralizados y gemelos digitales, los fabricantes obtienen visibilidad y control sobre todo el proceso de producción, impulsando la eficiencia y la agilidad.
Caso práctico 5: Implantación de una fábrica inteligente en JKL Plastics JKL Plastics, una empresa de termoformado, transformó sus instalaciones de producción en una fábrica inteligente integrando sensores habilitados para IoT y análisis de datos en sus procesos de fabricación. Mediante la captura y el análisis de datos de varias fases de producción, optimizaron la utilización de recursos, redujeron el consumo de energía en 20% y mejoraron la eficiencia general de la producción en 30%.
3. Optimización basada en datos
La Industria 4.0 permite optimizar los procesos de termoformado en función de los datos mediante análisis avanzados y algoritmos de aprendizaje automático. Mediante el análisis de grandes volúmenes de datos generados por sensores IoT, los fabricantes pueden identificar patrones, tendencias e ineficiencias en la producción. Esta información permite emprender iniciativas de mejora continua, como optimizar los tiempos de ciclo, reducir el desperdicio de material y mejorar la eficiencia energética.
Caso práctico 6: Optimización basada en datos en MNO Plastics MNO Plastics, una empresa de termoformado, aprovechó la analítica de datos y los algoritmos de aprendizaje automático para optimizar sus procesos de termoformado. Mediante el análisis de datos históricos de producción, identificaron cuellos de botella e ineficiencias en su flujo de trabajo. Gracias a la optimización y automatización de los procesos, consiguieron un aumento de 25% en el rendimiento de la producción y redujeron el desperdicio de material en 15%.
Conclusión
La transformación digital impulsada por las tecnologías IoT e Industria 4.0 está revolucionando el sector del termoformado, permitiendo a los fabricantes alcanzar nuevos niveles de eficiencia, calidad y agilidad. Al aprovechar el poder de los datos en tiempo real, el análisis predictivo y los sistemas interconectados, las empresas de termoformado pueden optimizar los procesos de producción, minimizar el tiempo de inactividad y responder rápidamente a las cambiantes demandas del mercado.
A medida que el ritmo de la innovación se acelera y la tecnología sigue evolucionando, el papel del IoT y la Industria 4.0 en el termoformado será cada vez más importante. Las empresas que adopten estas tecnologías y adapten sus operaciones en consecuencia obtendrán una ventaja competitiva en el panorama cada vez más digitalizado de la fabricación, posicionándose para el éxito y el crecimiento a largo plazo.