Dari Nol ke Satu: Desain, Pengembangan, dan Umpan Balik Pasar dari Mesin Thermoforming Tiga Stasiun
Pendahuluan
Mesin thermoforming tiga stasiun adalah peralatan yang banyak digunakan dalam industri manufaktur modern, yang secara khusus digunakan untuk memproses bahan termoplastik menjadi produk dengan bentuk yang diinginkan melalui pemanasan dan pembentukan cetakan. Dengan meningkatnya permintaan produk plastik dalam produksi industri, mesin thermoforming stasiun tunggal tradisional tidak dapat lagi memenuhi persyaratan produksi yang efisien. Desain dan pengembangan mesin thermoforming tiga stasiun muncul. Kelahirannya telah melalui beberapa tahapan penting. Berikut ini akan diperkenalkan proses pengembangannya secara rinci.
1. Mulai mendesain
Titik awal desain mesin thermoforming tiga stasiun berasal dari pemahaman yang mendalam tentang permintaan pasar dan efisiensi produksi. Ide awalnya adalah menambah jumlah stasiun sehingga proses pemanasan, pembentukan, dan pendinginan dapat dilakukan secara bersamaan, sehingga sangat memperpendek siklus produksi. Titik awal desain mekanis biasanya berasal dari model produk, gambar atau sampel yang disediakan oleh pelanggan. Desain pada tahap ini terutama berfokus pada keseluruhan struktur dan prinsip kerja peralatan.
Tim desain perlu mempertimbangkan cara mencapai kerja kolaboratif multi-stasiun di bawah premis untuk memastikan stabilitas peralatan, sehingga dapat meningkatkan efisiensi produksi secara keseluruhan. Tahap desain tidak hanya melibatkan optimalisasi struktur mekanis, tetapi juga memerlukan penelitian mendalam tentang teknologi utama seperti distribusi panas dan kontrol tekanan.
2. Pemilihan bahan
Sangatlah penting untuk memahami jenis bahan lembaran yang akan digunakan oleh produk. Pilih bahan yang sesuai (seperti degradasi pati, fotodegradasi, PP, PS, PET, PVC, PLA, CPLA, CPET, kalsium karbonat, OPS, dan lembaran lainnya) untuk memastikan bahwa bahan tersebut mempertahankan karakteristik yang melekat selama proses ekstrusi dan menghindari ketidaknyamanan penyesuaian parameter yang sering dilakukan selama proses thermoforming. Pemilihan bahan secara langsung memengaruhi kualitas produk akhir dan stabilitas produksi.
Proses pemilihan material tidak hanya mempertimbangkan sifat fisik dan kimianya, tetapi juga perlu mengevaluasi efektivitas biaya dan dampak lingkungan dari material tersebut. Dengan peraturan lingkungan yang semakin ketat, pemilihan bahan yang mudah terurai dan ramah lingkungan telah menjadi bagian penting dari proses desain.
3. Persiapan koil
Setelah bahan ditentukan, kumparan yang akan diproses dipasang pada perangkat pelepas gulungan, yang memberikan jumlah lembaran yang tepat dengan akurasi yang tepat. Selanjutnya, lembaran dimasukkan ke dalam mesin thermoforming dan melewati pelat pemanas atas dan bawah. Suhu disesuaikan secara independen sesuai dengan bahan dan ketebalan untuk memastikan keakuratan proses pembentukan. Tahap persiapan koil adalah dasar dari seluruh proses thermoforming dan menentukan kelancaran proses selanjutnya.
Perangkat unwinding modern biasanya dilengkapi dengan sistem kontrol tegangan otomatis untuk memastikan bahwa lembaran selalu mempertahankan tegangan yang sesuai selama transmisi untuk menghindari cacat yang disebabkan oleh kekencangan yang tidak merata. Selain itu, sistem pengumpanan yang efisien dapat secara signifikan meningkatkan tingkat otomatisasi lini produksi, mengurangi operasi manual dan meningkatkan efisiensi produksi.
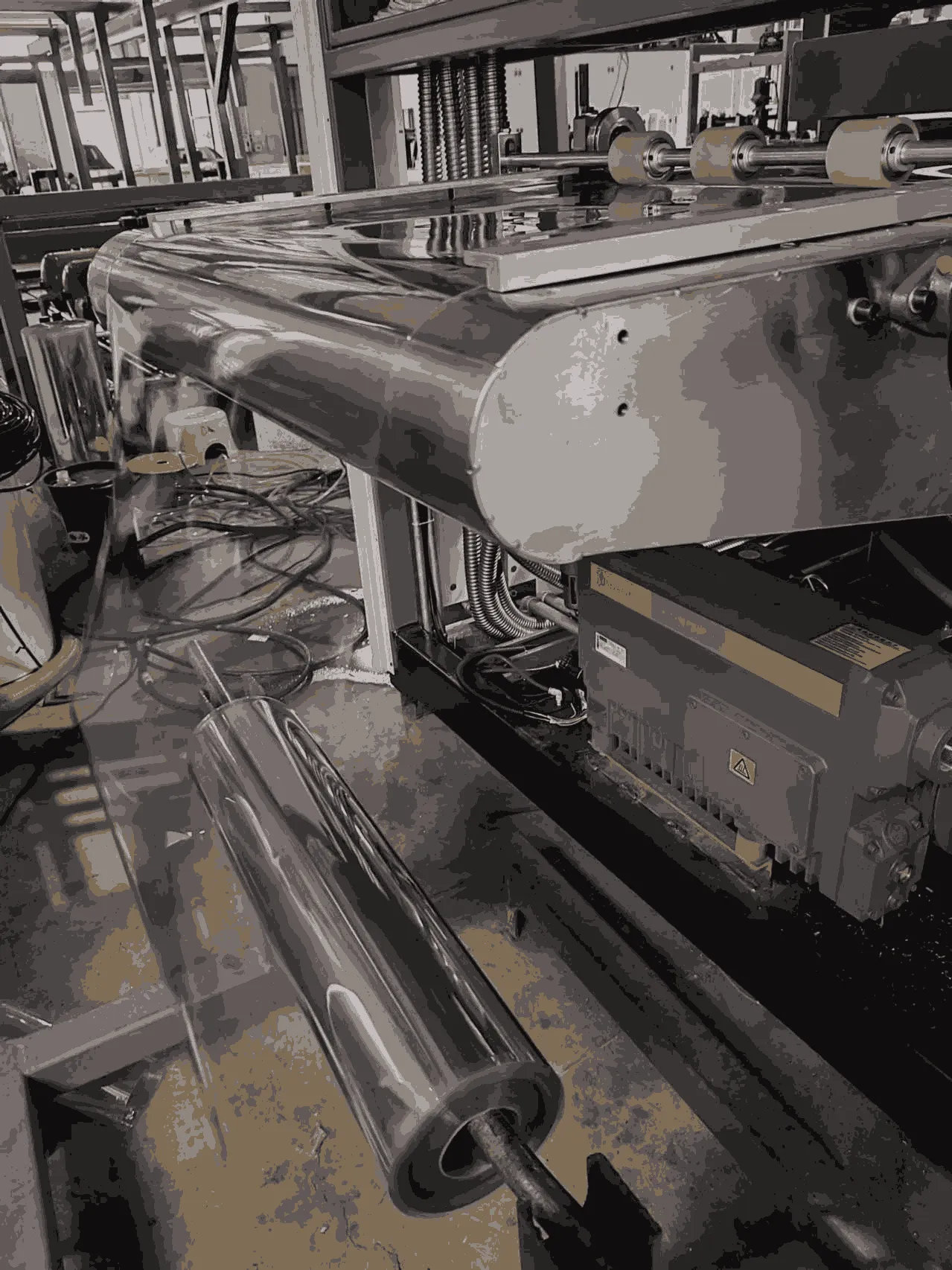
4. Kustomisasi cetakan
Berdasarkan karakteristik produk dan informasi material, rancanglah dengan cermat jumlah rongga dan waktu siklus cetakan yang diharapkan. Cetakan terdiri dari dua bagian, yang dipasang pada pelat bergerak dari mesin press siku vertikal. Desain dan pembuatan cetakan adalah penghubung utama dalam pengembangan mesin thermoforming, yang secara langsung berkaitan dengan bentuk, ukuran, dan kualitas permukaan produk. Cetakan presisi tinggi tidak hanya dapat meningkatkan tingkat kualifikasi produk, tetapi juga mengurangi pemborosan material dan keausan peralatan.
Desain cetakan tidak hanya perlu mempertimbangkan bentuk geometris produk, tetapi juga perlu mengoptimalkan sistem pendinginan cetakan untuk memastikan bahwa produk yang dicetak dapat dengan cepat didinginkan dan dibentuk, sehingga memperpendek siklus produksi. Teknologi pembuatan cetakan modern seperti pencetakan 3D dan pemesinan CNC presisi tinggi semakin meningkatkan akurasi dan kompleksitas pembuatan cetakan.
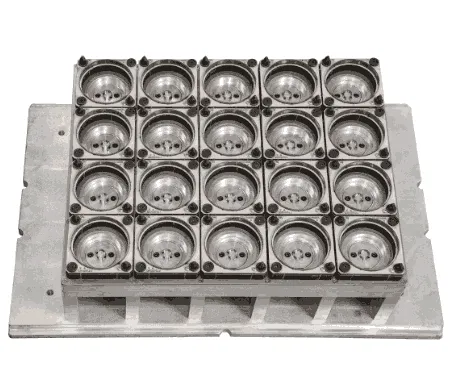
5. Cetakan plastik
Lembaran plastik datar dimasukkan ke dalam mesin, dan elemen pemanas memancarkan panas untuk membuat plastik menjadi lentur, meletakkan fondasi utama untuk tahap pencetakan. Plastik dilunakkan dengan pemanasan pertama, dikombinasikan dengan tekanan vakum atau tekanan udara, dan bahan dicetak dalam cetakan, dikeluarkan setelah pendinginan, dan diangkut ke stasiun berikutnya dengan rantai bergigi. Kunci teknis dari tahap pencetakan adalah mengontrol suhu pemanasan dan tekanan pencetakan untuk memastikan keseragaman dan stabilitas produk.
Suhu dan tekanan setiap stasiun harus dikontrol secara tepat selama proses pencetakan untuk menghindari cacat cetakan yang disebabkan oleh pemanasan yang berlebihan atau pendinginan plastik yang tidak merata. Peralatan pencetakan modern biasanya dilengkapi dengan sistem kontrol canggih yang dapat memantau dan menyesuaikan parameter produksi secara real time untuk memastikan kualitas produk yang konsisten.
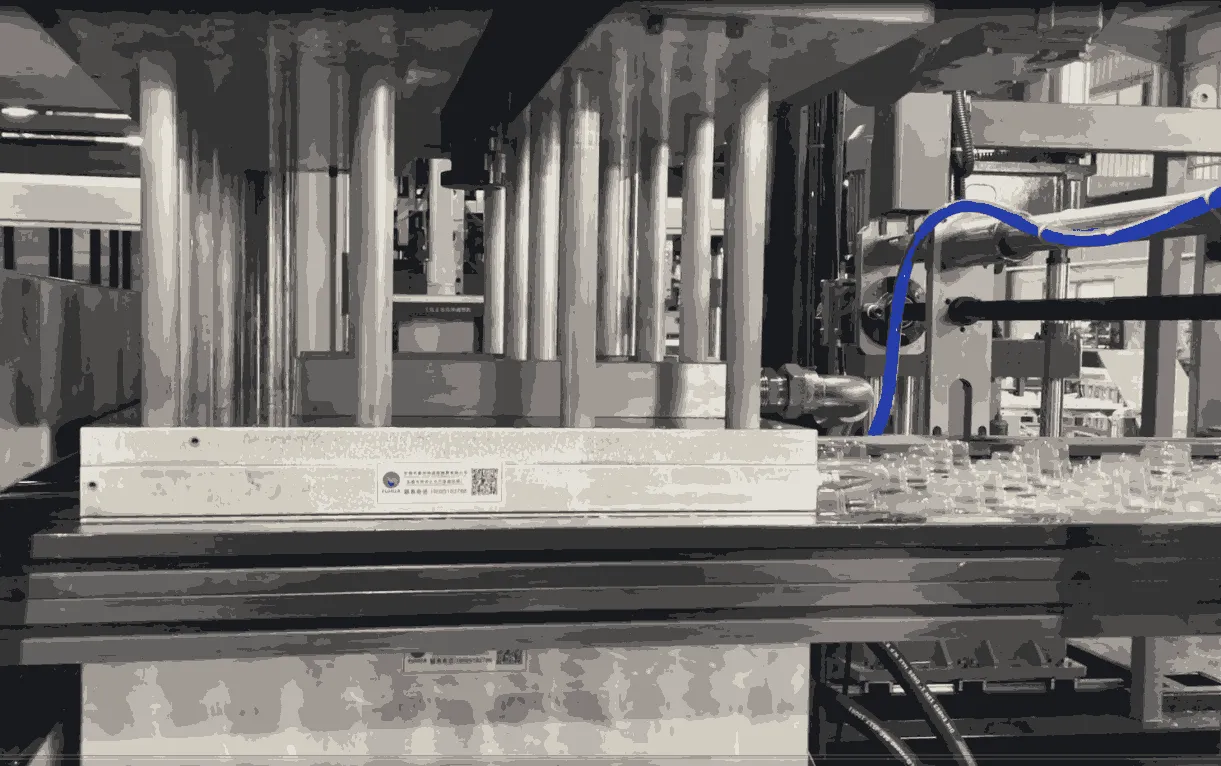
6. Pemotongan presisi
Di stasiun kedua, pemotongan bersih dilakukan oleh pelat pemanas resistansi untuk memastikan akurasi dan keseragaman ukuran produk dan memenuhi standar kualitas yang ketat. Produk yang dipotong dipasang ke pelat dan terus melewati mesin ke stasiun akhir. Keakuratan proses pemotongan secara langsung memengaruhi penampilan dan kinerja produk akhir, sehingga diperlukan peralatan pemotongan presisi tinggi dan teknologi kontrol canggih.
Proses pemotongan tidak hanya memerlukan akurasi dan kecepatan pemotongan, tetapi juga daur ulang limbah pemotongan. Dengan mengoptimalkan jalur pemotongan dan sistem penanganan limbah, limbah material dapat dikurangi secara efektif, dan perlindungan lingkungan serta manfaat ekonomi produksi dapat ditingkatkan.
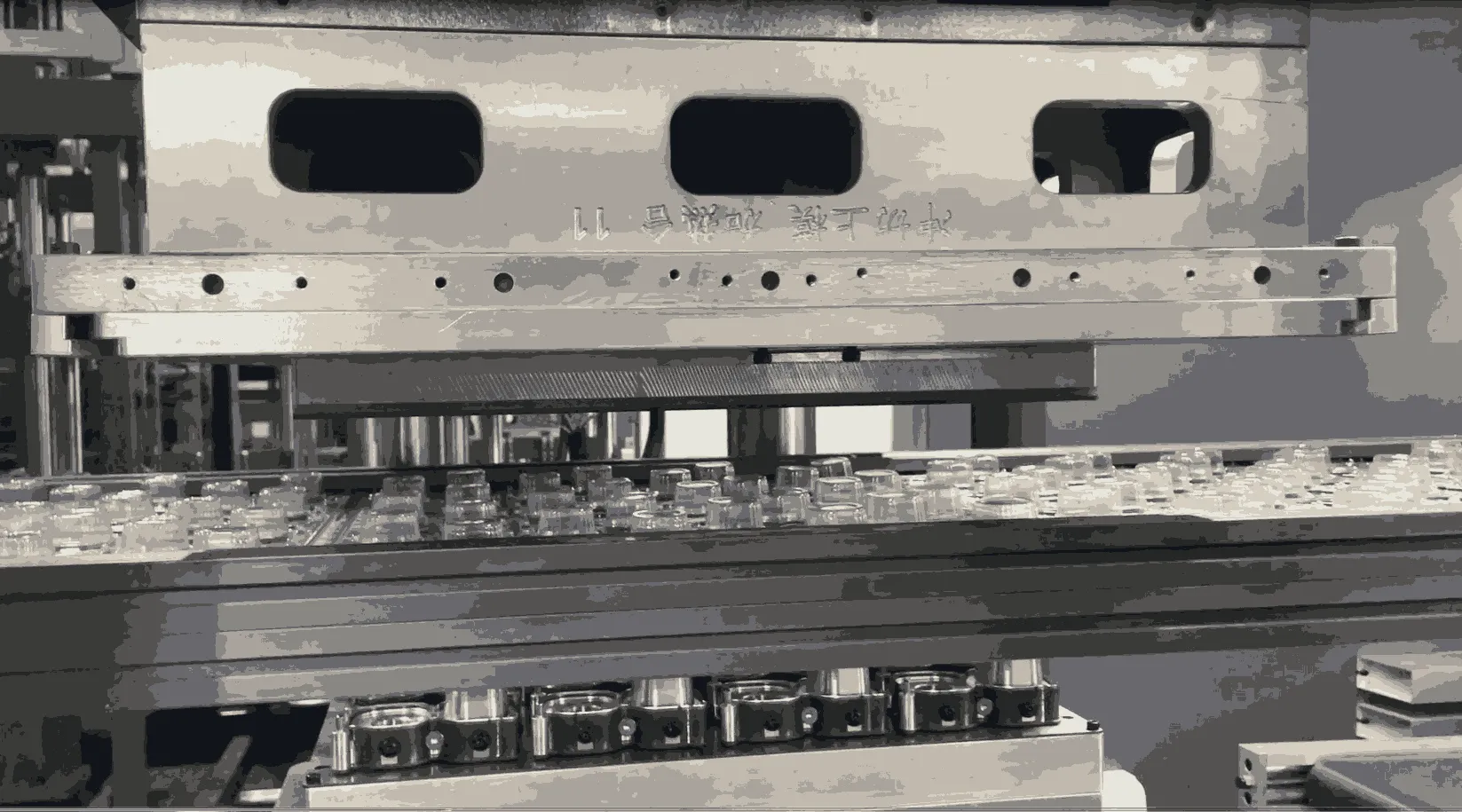
7. Penumpukan yang efisien
Di stasiun ketiga, produk ditumpuk dengan rapi dan diatur untuk penanganan dan pengemasan selanjutnya yang efisien. Penggunaan stasiun penumpukan tidak hanya menyederhanakan proses produksi, tetapi juga secara signifikan meningkatkan efisiensi produksi secara keseluruhan. Sistem penumpukan yang efisien dapat secara signifikan mengurangi operasi manual dan meningkatkan tingkat otomatisasi produksi, sekaligus memastikan konsistensi dan keandalan setiap batch produk.
Sistem penumpukan yang efisien sering kali menggabungkan sensor pintar dan perangkat lunak kontrol untuk secara otomatis menyesuaikan metode penumpukan sesuai dengan ukuran dan berat produk, memastikan kualitas penumpukan yang konsisten untuk setiap batch produk. Pada saat yang sama, sistem penumpukan otomatis juga dapat dihubungkan secara mulus dengan sistem pengemasan berikutnya untuk meningkatkan efisiensi seluruh lini produksi.
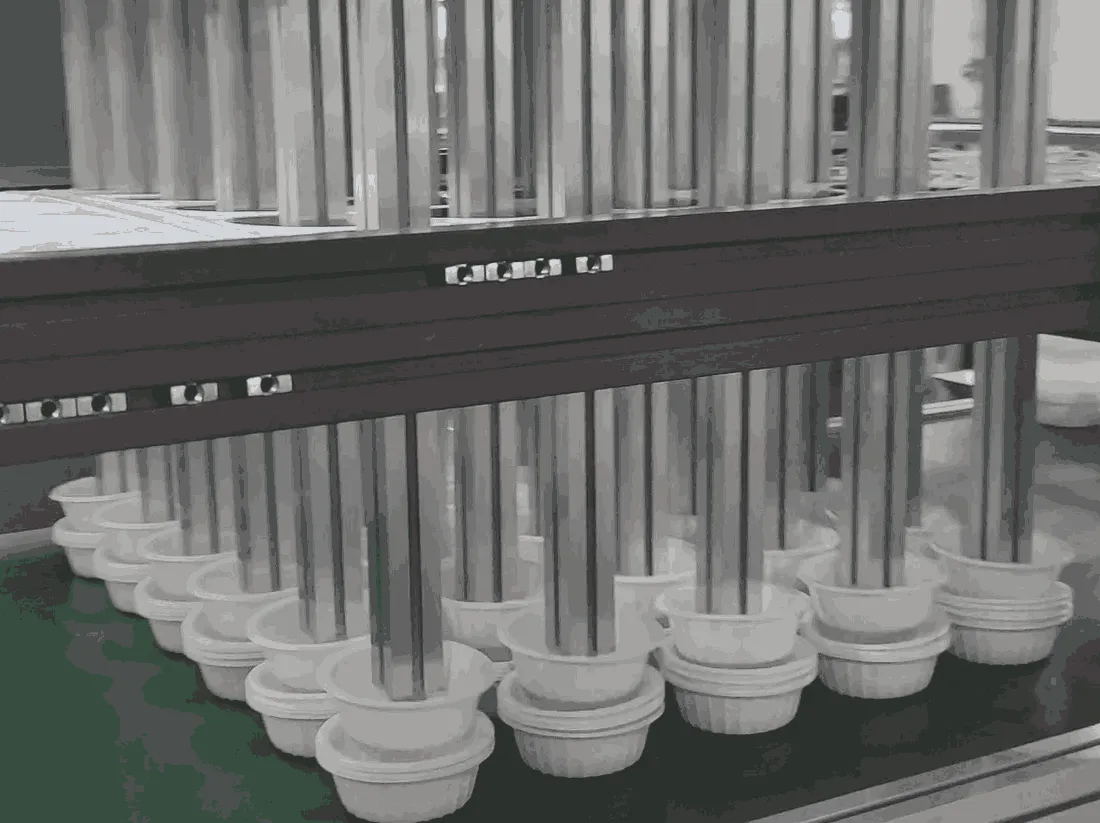
Penelitian dan pengembangan teknologi dan pengoptimalan desain
Setelah konsepsi pencetakan, tim R&D mulai menangani masalah teknis. Desain mesin thermoforming tiga stasiun perlu menyelesaikan beberapa masalah teknis, termasuk:
Keseragaman distribusi panas: Pastikan distribusi panas yang seragam di setiap stasiun untuk menghindari cacat produk selama proses pencetakan. Distribusi panas yang seragam dapat dicapai melalui teknologi kontrol pemanasan yang canggih dan desain pemanas yang dioptimalkan.
Akurasi cetakan: Meningkatkan akurasi pembuatan cetakan untuk memastikan kualitas produk cetakan. Teknologi pemrosesan CNC presisi tinggi dan proses kontrol kualitas yang ketat adalah kunci untuk mencapai cetakan presisi tinggi.
Kontrol otomasi: Memperkenalkan sistem kontrol otomasi canggih untuk meningkatkan kenyamanan pengoperasian dan efisiensi produksi peralatan. Sistem kontrol otomasi modern tidak hanya dapat mencapai kontrol peralatan yang tepat, tetapi juga mengoptimalkan proses produksi melalui sensor dan analisis data.
Selama proses penelitian dan pengembangan teknologi, eksperimen dan pengujian berkelanjutan diperlukan untuk memverifikasi kelayakan dan potensi optimalisasi skema desain. Melalui simulasi komputer dan pengujian laboratorium, kinerja peralatan dalam produksi aktual dapat diprediksi sebelumnya, sehingga mengurangi siklus pengembangan dan biaya.
Pembuatan dan pengujian prototipe
Setelah skema desain ditentukan, prototipe pertama mesin thermoforming tiga stasiun diproduksi. Melalui serangkaian pengujian dan penyesuaian, performa dan stabilitas peralatan terus dioptimalkan. Selama pengujian, aspek-aspek berikut ini difokuskan:
Efisiensi produksi: Dibandingkan dengan peralatan stasiun tunggal tradisional, efisiensi produksi mesin thermoforming tiga stasiun meningkat secara signifikan. Dengan mengoptimalkan parameter proses dan struktur peralatan, kecepatan produksi yang lebih tinggi dan konsumsi energi yang lebih rendah dapat dicapai.
Kualitas produk: Dengan menyesuaikan suhu pemanasan dan tekanan pencetakan, pastikan bahwa produk yang dicetak memenuhi standar kualitas yang diharapkan. Produk berkualitas tinggi tidak hanya dapat memenuhi permintaan pasar, tetapi juga meningkatkan daya saing pasar perusahaan.
Keandalan peralatan: Memastikan keandalan dan daya tahan peralatan melalui uji operasi jangka panjang. Peralatan yang andal dapat mengurangi waktu henti dan meningkatkan kesinambungan serta stabilitas produksi.
Selama pengujian, tim R&D akan merekam dan menganalisis berbagai data, mencari tahu faktor utama yang memengaruhi kinerja peralatan, dan melakukan perbaikan yang ditargetkan. Melalui pengujian dan pengoptimalan yang berulang-ulang, parameter peralatan dan prosedur pengoperasian yang optimal akhirnya ditentukan.
Dimasukkan ke dalam produksi dan umpan balik pasar
Setelah melalui berbagai pengujian dan perbaikan, mesin thermoforming tiga stasiun akhirnya mulai digunakan di pasar. Karena kapasitas produksinya yang efisien dan kualitas produk yang sangat baik, mesin ini dengan cepat mendapatkan pengakuan pasar. Umpan balik pengguna semakin mendorong pengoptimalan dan peningkatan peralatan. Data dan umpan balik dalam penggunaan aktual tidak hanya dapat membantu meningkatkan desain peralatan, tetapi juga memandu penelitian dan pengembangan produk baru.
Pengumpulan umpan balik pasar merupakan dasar yang penting untuk perbaikan peralatan. Melalui kerja sama yang erat dengan pelanggan, produsen dapat secara tepat waktu memahami kebutuhan pengguna dan perubahan pasar, dengan cepat menyesuaikan strategi produksi dan arah R&D, serta mempertahankan daya saing pasar.
Peningkatan dan inovasi yang berkelanjutan
Untuk beradaptasi dengan permintaan pasar yang terus berubah dan kemajuan teknologi, penelitian dan pengembangan mesin thermoforming tiga stasiun tidak berhenti. Produsen terus memperkenalkan teknologi baru, seperti sistem kontrol cerdas, teknologi pemulihan energi, dll., Untuk lebih meningkatkan kinerja dan efek penghematan energi peralatan. Di masa depan, dengan penerapan teknologi seperti kecerdasan buatan dan data besar.