The heart of the thermoforming machine: revealing the precision process of the molding station
Introduce
In the field of plastic processing, multi-station thermoforming machines are highly favored for their efficient and flexible production capacity. This article will introduce the molding station in the multi-station thermoforming machine in detail, explore its working principle, key components and application in modern manufacturing.
Working principle of the molding station
The molding station is the core link in the multi-station thermoforming machine, responsible for converting the heated plastic sheet into the required product shape. Its working principle mainly includes the following steps:
1. Conveying: The heated plastic sheet enters the molding station through the conveying system. The conveying system is generally composed of high-temperature resistant conveyor belts or rollers to ensure that the sheet will not deform or damage at high temperatures.
2. Positioning: The sheet is precisely positioned above the molding mold to ensure molding accuracy. This process is usually completed by an automated positioning device, combined with photoelectric sensors and mechanical limit devices to achieve high-precision positioning.
3. Molding: Through mechanical pressure or vacuum adsorption, the sheet is made to fit the mold surface to form the desired shape. There are two main molding methods:
Mechanical molding: Use mechanical pressure to press the sheet into the mold, suitable for thicker plastic materials.
Vacuum molding: Use vacuum to adsorb the sheet to the mold surface, suitable for thinner plastic materials, and can achieve finer surface details.
4. Curing: The molded plastic part is kept in the mold for a period of time to ensure the stability of the shape. The curing time varies depending on the plastic material, usually ranging from a few seconds to tens of seconds.
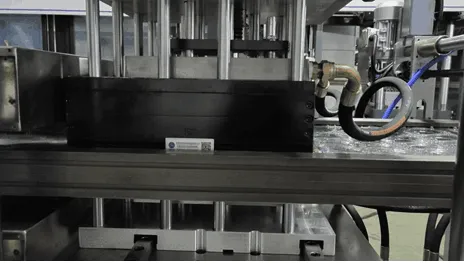
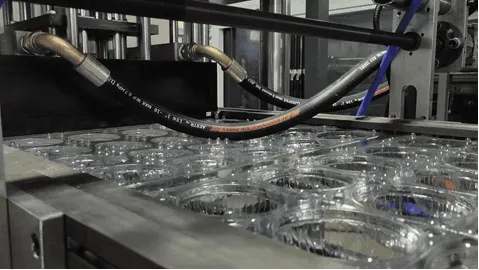
Key Components
The performance and efficiency of the molding station depends largely on the design and manufacturing quality of its key components, mainly including:
1. Mold: The precision-designed mold is the core of the molding station and directly affects the shape and size of the product. The mold material is usually made of high-strength steel or aluminum alloy, and is precision-machined and surface-treated to ensure its durability and precision.
2. Heating system: Ensure that the plastic sheet is evenly heated to provide the necessary temperature conditions for molding. The heating system generally uses electric heating elements or infrared heating lamps, combined with temperature sensors and control systems to achieve precise temperature control.
3. Pressure system: Provides sufficient pressure to make the plastic sheet fit tightly to the mold. The pressure system includes hydraulic systems and pneumatic systems, the former is suitable for high-pressure molding and the latter is suitable for low-pressure molding.
4. Control system: Precisely control various parameters in the molding process, such as temperature, pressure and time. Modern control systems usually use PLC (programmable logic controller) or industrial computers, and are equipped with touch screen interfaces for easy operation and monitoring.
Technical advantages
Multi-station thermoforming machines have the following technical advantages in the field of plastic processing:
1. High efficiency: The parallel working mode of multiple stations greatly shortens the production cycle and improves production efficiency. Each station can work independently, avoiding the problem that the entire production line is stagnant due to the failure of one station in traditional single-station equipment.
2. High precision: Accurate temperature control and molding pressure adjustment ensure the dimensional accuracy and consistency of the molded parts. This is especially important for the production of plastic products that require high precision and high consistency, such as medical devices and electronic product housings.
3. High adaptability: Suitable for the molding of a variety of plastic materials and complex shapes, which improves the flexibility and diversity of production. Multi-station thermoforming machines can quickly change molds to meet the production needs of different products.
4. High degree of automation: Highly automated production lines reduce manual intervention, reduce production costs and improve production stability. The automation system can not only improve production efficiency, but also reduce the problem of unstable product quality caused by human operation.
Maintenance and maintenance of multi-station thermoforming machines
In order to ensure the long-term stable operation of multi-station thermoforming machines, regular maintenance and maintenance are essential. Here are some key maintenance measures:
1. Regular inspection and cleaning: The various components of the equipment, such as molds, heating systems, pressure systems and control systems, need to be inspected and cleaned regularly. In particular, molds and heating systems are prone to accumulate dust and residues and must be kept clean to ensure normal operation.
2. Lubrication and replacement of wearing parts: Mechanical parts such as transmission systems and hydraulic systems need to be lubricated regularly to reduce friction and wear. For some wearing parts, such as seals and filters, they should be checked regularly and replaced in time.
3. Temperature and pressure calibration: The heating system and pressure system are key parts to ensure molding accuracy. The temperature sensor and pressure sensor should be calibrated regularly to ensure their measurement accuracy. At the same time, check the parameter settings of the control system to ensure that they are consistent with actual production requirements.
4. Electrical system maintenance: The electrical system includes parts such as control panels, motors and cables. It is necessary to regularly check the firmness of electrical connections and the integrity of the lines. Cables that are found to be aging or damaged should be replaced in time to prevent electrical failures.
5. Software update and backup: Modern multi-station thermoforming machines are usually equipped with advanced control software. Regularly check the software version and make necessary updates to ensure that the function and performance of the equipment are in the best condition. At the same time, regularly back up the data of the control system to prevent data loss due to unexpected situations.
6. Operator training: The stable operation of the equipment is inseparable from the correct operation and maintenance of the operator. Therefore, regular training of operators to improve their operating skills and maintenance knowledge is an important guarantee for the long-term stable operation of the equipment.
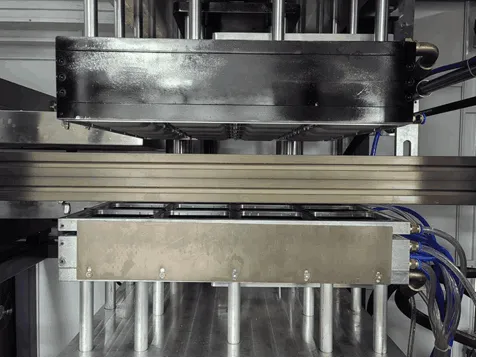
Future development trends
With the continuous advancement of technology, multi-station thermoforming machines are also constantly developing and innovating. Future development trends mainly include the following aspects:
1. Intelligence: Apply artificial intelligence technology to the control system of the thermoforming machine to achieve more intelligent production management and quality control. For example, optimize molding parameters through machine learning algorithms to improve production efficiency and product quality.
2. Environmental protection: Use energy-saving and environmentally friendly heating systems and materials to reduce energy consumption and environmental pollution. For example, develop molding processes that use degradable plastic materials to reduce the impact of plastic waste on the environment.
3. Modularity: Develop modular multi-station thermoforming machines to facilitate users to flexibly configure according to production needs. For example, the number of molding stations can be increased or decreased according to product types and output requirements to achieve higher production flexibility.
4. Multifunctionality: Integrate multiple molding processes on one device, such as thermoforming, injection molding and blow molding, to improve the comprehensive utilization rate of the equipment. For example, by replacing different types of molds, different products can be produced on the same device.
Conclusion
As an important equipment in the field of plastic processing, the precision process of the molding station of the multi-station thermoforming machine is the key to achieving efficient production and high-quality products. With the continuous advancement of technology, multi-station thermoforming machines will play an important role in more fields and provide strong support for the development of modern manufacturing industry.