Common Challenges in Demolding
While demolding systems bring significant benefits, they also encounter challenges that can affect production efficiency and product quality. Below are some of the typical issues faced during the demolding process:
Sticking Parts:Adhesion between the mold and the molded product is a frequent problem, often caused by inadequate cooling or flaws in mold design. If the part doesn’t separate fully from the mold, it can result in production delays, defects, or even damage to both the mold and the finished product.

Deformation or Damage:Parts with thin walls or delicate structures are particularly vulnerable to deformation or cracking during demolding. Excessive or uneven ejection force can cause these parts to warp, crack, or lose their intended shape, leading to quality defects and higher scrap rates.
Mechanical Wear:Continuous use of demolding systems can cause wear on mechanical components, such as ejector pins, slides, and pushers. Over time, this wear impacts the system’s reliability, leading to increased maintenance requirements, reduced efficiency, and unplanned downtime.
Material Residue:Residual plastic material from previous molding cycles can accumulate in the mold, particularly in systems using pneumatic or hydraulic ejection. This buildup may clog vents, impair system performance, and result in poor-quality parts in subsequent cycles.
Solutions:
- Apply Mold Release Agents:Using mold release agents can significantly reduce adhesion issues, facilitating smoother part removal. This is particularly useful for molds with intricate or complex designs.
- Optimize Cooling and Ejection Force: Adjust cooling times to ensure the parts are adequately solidified before ejection. Similarly, calibrate the ejection force to apply it evenly, minimizing the risk of part deformation or damage during removal.
- Conduct Regular Maintenance: Schedule routine maintenance to inspect and replace worn components, ensuring smooth operation and extending the life of the system. This includes cleaning mold surfaces to prevent material buildup and checking for signs of wear on mechanical parts.
By proactively addressing these issues and implementing effective strategies, manufacturers can enhance production quality, reduce downtime, and extend the operational lifespan of their demolding systems.
Advancements in Demolding Technology
With the increasing demand for precision, efficiency, and sustainability in manufacturing, demolding systems are evolving with the help of advanced technologies. These innovations not only tackle common challenges but also boost productivity, minimize downtime, and improve overall system performance. Some of the key advancements include:
1. Smart Sensors
The introduction of smart sensors has transformed demolding systems by enabling real-time tracking of critical parameters such as force, temperature, and timing. These sensors offer precise control during the demolding process, ensuring the forces applied are both optimal and consistent. By monitoring mold conditions continuously, smart sensors help reduce errors, prevent damage to parts, and improve overall part quality, while optimizing production cycles.
Benefits:
- More accurate control of the ejection process.
- Real-time adjustments to prevent defects.
- Increased reliability and consistency in production.
2. Adaptive Robotics
Robotic systems that incorporate artificial intelligence (AI) and machine learning are becoming increasingly versatile. These robots are able to adapt to different shapes, sizes, and materials, adjusting their movements and force accordingly. This flexibility makes them especially useful for handling delicate or complex parts. By reducing human involvement, these robots also help speed up production cycles.
Benefits:
- Flexible and programmable for varying product shapes and sizes.
- Enhanced precision in handling delicate or intricate parts.
Reduced reliance on manual intervention, increasing automation and efficiency.
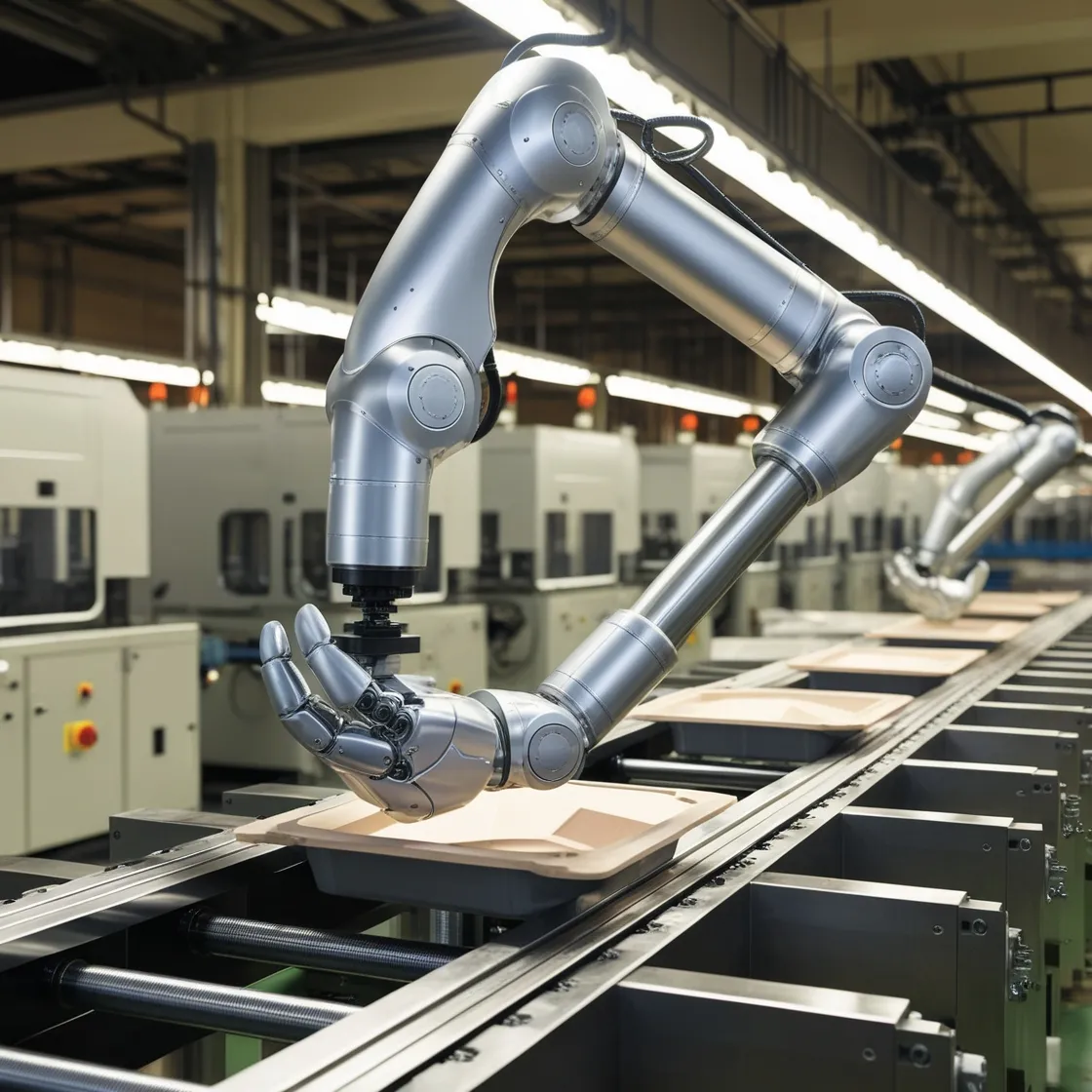
3. Self-Lubricating Components
Advances in materials have led to the creation of self-lubricating parts for demolding systems. Materials used in ejector pins, slides, and other moving components reduce friction and wear, eliminating the need for frequent lubrication. This not only decreases maintenance requirements but also extends the lifespan of parts, ensuring smoother operation with less downtime.
Benefits:
- Reduced maintenance needs and downtime.
- Enhanced durability and longer lifespan of system components.
Smoother operation with less friction, improving overall efficiency.
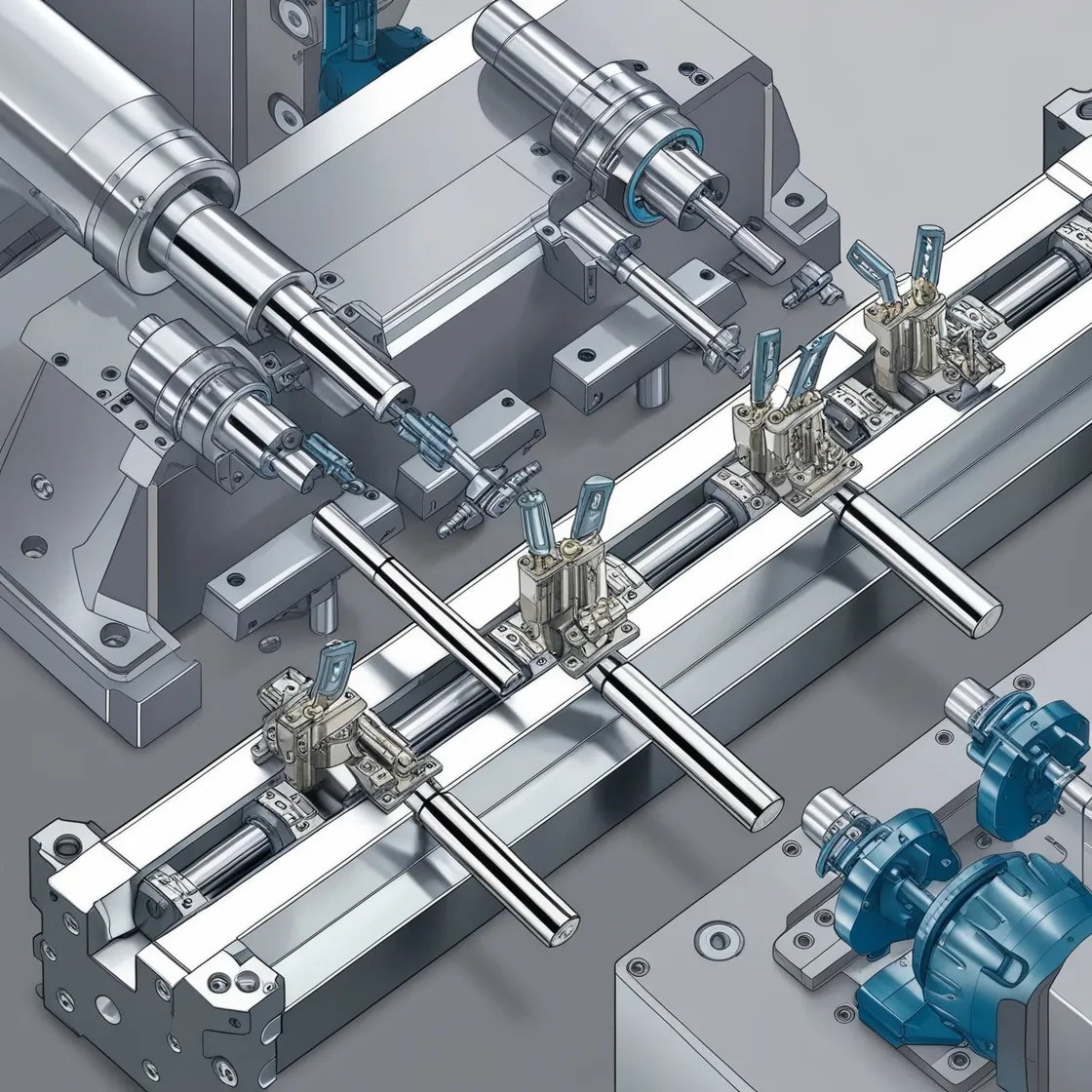
4. Eco-Friendly Systems
As sustainability becomes a major priority for manufacturers, energy-efficient pneumatic and hydraulic systems are gaining popularity. These eco-friendly systems are designed to minimize energy use, reduce environmental impact, and lower operational costs. By optimizing the use of compressed air and hydraulic fluids, these systems provide high performance while promoting energy savings and reducing the carbon footprint.
Benefits:
- Lower energy consumption and reduced environmental impact.
- Cost savings from energy-efficient system design.
- Compliance with sustainability standards and reduced carbon footprint.
By embracing these advancements, manufacturers can boost production efficiency, lower operational costs, and maintain high-quality output. These innovations make it possible to meet the increasing demand for faster, more precise, and environmentally sustainable production processes.
Future Trends in Demolding Systems
As the thermoforming industry continues to evolve, the focus is shifting toward greater automation, enhanced sustainability, and more tailored solutions. The future of demolding systems is poised to embrace cutting-edge technologies and practices that will shape the industry for years to come. Here are some key trends expected to dominate the field:
1. Increased Automation
The future of demolding systems lies in fully automated production lines, where robotic demolding solutions will become the standard, especially in high-volume manufacturing environments. Automation will streamline the entire production process, from mold opening to part ejection, reducing human intervention and minimizing the risk of errors. These advanced systems will enhance speed, accuracy, and consistency, making it easier to manage large-scale production without compromising part quality.
Expected Benefits:
- Higher production speeds and reduced labor costs.
- Greater precision and consistency in part handling.
- Increased operational efficiency with less manual intervention.
2. Integration with IoT (Internet of Things)
The integration of smart technology through the Internet of Things (IoT) will revolutionize demolding systems. By connecting demolding equipment to IoT networks, manufacturers will gain the ability to monitor system performance in real time and receive predictive maintenance alerts. This connectivity will provide valuable insights into system health, enabling preemptive repairs before malfunctions occur, minimizing downtime, and optimizing maintenance schedules for maximum uptime.
Expected Benefits:
- Real-time monitoring of critical system parameters.
- Predictive maintenance to prevent equipment failure.
- Improved decision-making through data-driven insights.
3. Sustainable Practices
With growing environmental concerns and an emphasis on corporate responsibility, the thermoforming industry is prioritizing sustainability. Future demolding systems will focus on eco-friendly designs that minimize energy consumption, reduce material waste, and optimize resource use. By adopting sustainable practices, such as energy-efficient pneumatic or hydraulic systems, manufacturers can align with global sustainability goals, reduce their carbon footprint, and lower operational costs.
Expected Benefits:
- Reduced energy usage and operational costs.
- Lower environmental impact through optimized resource management.
- Compliance with increasingly stringent environmental regulations.
As these trends unfold, the future of demolding systems in the thermoforming industry will be characterized by increased automation, smarter connectivity, more sustainable practices, and greater customization. By embracing these innovations, manufacturers will be able to achieve higher efficiency, better quality control, and a more sustainable approach to production.
Conclusion
Designing effective demolding systems involves a deep understanding of product geometry, material properties, cycle time requirements, and maintenance needs. While challenges such as sticking parts, deformation, and mechanical wear are common, they can be mitigated through proper system design and regular maintenance. The advancements in demolding technology, such as smart sensors, adaptive robotics, and eco-friendly systems, are setting new standards for the thermoforming industry. Embracing these innovations will help manufacturers not only optimize their production processes but also stay ahead in an increasingly competitive and sustainability-driven market. By addressing both design considerations and technological advancements, businesses can achieve higher efficiency, lower operational costs, and better product quality.