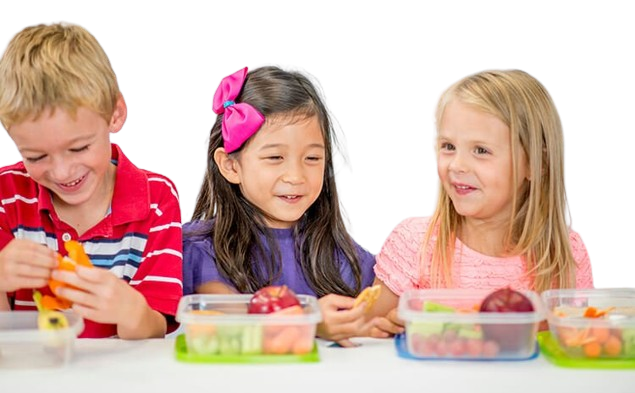
How to Handle Water Ingress in Thermoforming Machines
Introduction
Thermoforming machines, commonly referred to as vacuum forming machines, are critical assets in various industries. They are used to shape plastic sheets into specific forms, serving applications in packaging, automotive, medical devices, and consumer goods. However, like any sophisticated equipment, thermoforming machines are susceptible to operational issues, one of which is water ingress. Water ingress can lead to severe damage, operational disruptions, and costly repairs if not addressed promptly and effectively. This article provides a comprehensive guide on handling water ingress in thermoforming machines, detailing preventive measures, immediate responses, and long-term solutions to ensure minimal downtime and optimal machine performance.
Understanding Water Ingress in Thermoforming Machines
Water ingress refers to the unwanted penetration of water into the internal components of a thermoforming machine. This can occur due to various reasons, such as:
- Environmental Factors: High humidity, flooding, or accidental spills can introduce water into the machine.
- Cooling System Leaks: Thermoforming machines often use water-based cooling systems. Leaks in these systems can cause water ingress.
- Condensation: In environments with significant temperature fluctuations, condensation can form inside the machine, leading to water accumulation.
- Maintenance Errors: Inadequate sealing after maintenance or repairs can allow water to enter the machine.
Consequences of Water Ingress
Water ingress can have several detrimental effects on thermoforming machines, including:
- Electrical Short Circuits: Water can cause short circuits in the machine’s electrical components, leading to malfunctions or complete failure.
- Corrosion: Prolonged exposure to water can cause corrosion of metal parts, compromising the machine’s structural integrity.
- Reduced Efficiency: Water ingress can disrupt the machine’s normal operation, reducing efficiency and output quality.
- Increased Maintenance Costs: Repairing damage caused by water ingress can be expensive and time-consuming, increasing overall maintenance costs.
Preventive Measures
Preventing water ingress is crucial to maintaining the longevity and efficiency of thermoforming machines. Here are some preventive measures:
1. Regular Maintenance and Inspection
Conduct regular maintenance and inspections to identify and fix potential sources of water ingress. Key areas to focus on include:
- Seals and Gaskets: Check for wear and tear in seals and gaskets and replace them as needed to prevent leaks.
- Cooling System: Inspect the cooling system for leaks and ensure all connections are secure.
- Condensation Control: Install dehumidifiers in areas prone to condensation and ensure proper ventilation.
2. Environmental Control
Control the environment around the thermoforming machine to minimize the risk of water ingress:
- Humidity Control: Use industrial dehumidifiers to maintain optimal humidity levels in the production area.
- Flood Prevention: Implement measures to prevent flooding, such as installing drainage systems and raising the machine off the floor.
3. Proper Training
Ensure that all personnel operating and maintaining the thermoforming machine are properly trained to handle the equipment and recognize early signs of water ingress.
4. Protective Enclosures
Install protective enclosures around sensitive components to shield them from water exposure. This is particularly important for electrical components and control panels.
Immediate Response to Water Ingress
If water ingress occurs, it is crucial to take immediate action to mitigate damage. Follow these steps:
1. Shut Down the Machine
Immediately shut down the thermoforming machine to prevent further damage and ensure safety. Disconnect the machine from the power supply to avoid electrical hazards.
2. Identify the Source
Quickly identify the source of the water ingress. This could be a leak in the cooling system, a spill, or condensation. Understanding the source will help in addressing the issue effectively.
3. Remove Water
Carefully remove any visible water from the machine using absorbent materials, vacuum cleaners designed for water, or specialized drying equipment. Ensure that the machine is completely dry before proceeding.
4. Inspect for Damage
Thoroughly inspect the machine for any signs of damage caused by water ingress. Key areas to check include:
- Electrical Components: Look for signs of short circuits or corrosion.
- Mechanical Parts: Check for rust, corrosion, or other physical damage.
- Cooling System: Inspect for leaks and ensure all components are dry.
5. Dry and Clean Components
Dry and clean all affected components. Use compressed air to remove moisture from hard-to-reach areas. If necessary, use electronic cleaning solutions to remove any residue.
6. Test and Restart
Once the machine is dry and inspected, perform a series of tests to ensure all components are functioning correctly. Gradually restart the machine and monitor its performance closely for any signs of issues.
Long-Term Solutions
To prevent future water ingress and ensure the long-term reliability of your thermoforming machine, consider implementing the following solutions:
1. Upgrade Sealing Mechanisms
Invest in high-quality seals and gaskets that are resistant to water and environmental factors. Regularly inspect and replace these components as part of your maintenance schedule.
2. Enhance Cooling Systems
Upgrade the cooling system to include leak detection sensors and automatic shutoff valves. These features can quickly identify and mitigate leaks, preventing water ingress.
3. Implement Remote Monitoring
Install remote monitoring systems that provide real-time data on the machine’s condition, including temperature, humidity, and potential water ingress. These systems can alert you to issues before they cause significant damage.
4. Improve Environmental Controls
Invest in advanced environmental control systems to maintain optimal conditions around the thermoforming machine. This includes better HVAC systems, humidity controls, and flood prevention measures.
5. Regular Training and Updates
Regularly train your staff on best practices for operating and maintaining the thermoforming machine. Stay updated with the latest industry standards and technologies to improve your preventive measures.
6. Comprehensive Maintenance Plans
Develop and implement comprehensive maintenance plans that include routine inspections, preventive maintenance, and prompt repairs. Document all maintenance activities and use this information to identify trends and potential issues.
Conclusion
Water ingress in thermoforming machines can lead to significant operational disruptions and costly repairs. However, by understanding the causes, consequences, and preventive measures, businesses can effectively manage and mitigate the risks associated with water ingress. Implementing immediate response strategies and long-term solutions ensures the reliability and efficiency of thermoforming machines, minimizing downtime and enhancing productivity.
Investing in high-quality components, advanced monitoring systems, and comprehensive maintenance plans not only protects your thermoforming machines from water ingress but also extends their lifespan and improves overall operational efficiency. By taking proactive steps and staying vigilant, B2B users can maintain the performance and longevity of their thermoforming machines, ensuring consistent and high-quality production.