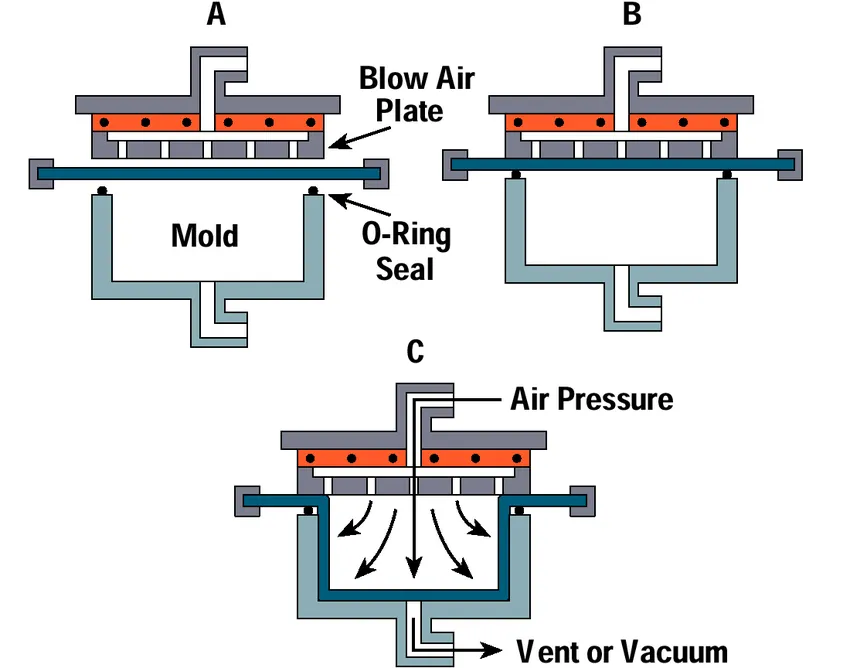
Optimizing Cycle Times in Thermoforming Processes
Introduction
In the competitive world of plastic manufacturing, optimizing cycle times in thermoforming processes is crucial for enhancing productivity, reducing costs, and maintaining high-quality standards. Thermoforming, a process that involves heating plastic sheets and forming them into specific shapes using molds, is widely used across various industries, including packaging, automotive, and medical devices. This article explores strategies for optimizing cycle times in thermoforming processes, providing detailed insights and real-life case studies to illustrate effective implementation.
Understanding Cycle Times in Thermoforming
Cycle time in thermoforming refers to the total time required to complete one production cycle, from heating the plastic sheet to ejecting the finished part from the mold. It consists of several stages:
- Heating Time: The time taken to heat the plastic sheet to the required forming temperature.
- Forming Time: The time needed to shape the heated plastic sheet using the mold.
- Cooling Time: The duration for cooling the formed plastic to retain its shape.
- Ejection Time: The time required to remove the finished part from the mold.
- Loading and Unloading Time: The time spent on loading raw materials and unloading finished products.
Each stage impacts the overall cycle time, and optimizing these phases can lead to significant improvements in productivity and cost-efficiency.
Strategies for Optimizing Cycle Times
1. Advanced Heating Systems
One of the critical factors in reducing cycle times is the efficiency of the heating system. Advanced heating technologies, such as infrared (IR) heaters and ceramic heaters, can provide faster and more uniform heating compared to traditional systems.
Case Study: High-Speed Infrared Heating at Plastipack
บริษัท: Plastipack
Industry: Packaging
Challenge: Plastipack faced long heating times, leading to extended cycle times and limited production capacity.
Solution: The company upgraded to high-speed infrared heating systems, which offer rapid and uniform heating.
Implementation: The IR heaters were installed in the thermoforming machines, reducing the heating time by 30%. The new system allowed precise temperature control, ensuring consistent material properties.
Result: Plastipack experienced a 25% reduction in overall cycle time, leading to a significant increase in production throughput and a decrease in energy consumption.
2. Efficient Mold Design and Cooling
Optimizing mold design and cooling systems can drastically reduce forming and cooling times. Using materials with high thermal conductivity and incorporating advanced cooling channels can enhance the cooling efficiency.
Case Study: Optimized Cooling Channels at AutoForm
บริษัท: AutoForm
Industry: Automotive
Challenge: Long cooling times due to inefficient mold design, resulting in bottlenecks and increased production costs.
Solution: AutoForm redesigned their molds using aluminum, which has better thermal conductivity than steel. Additionally, they integrated advanced conformal cooling channels.
Implementation: The new molds were manufactured using 3D printing technology to create complex cooling channels that conformed to the shape of the parts.
Result: Cooling times were reduced by 40%, and overall cycle times decreased by 20%. This led to a 15% increase in production efficiency and improved part quality due to uniform cooling.
3. Automation and Robotics
Integrating automation and robotics into the thermoforming process can significantly reduce loading, unloading, and ejection times. Automated systems ensure consistent and rapid handling of materials, reducing human error and increasing overall efficiency.
Case Study: Robotic Integration at MedPlast Solutions
บริษัท: MedPlast Solutions
Industry: Medical Devices
Challenge: Manual loading and unloading processes were time-consuming and prone to errors, leading to extended cycle times.
Solution: MedPlast Solutions integrated robotic arms into their thermoforming lines to automate the loading and unloading processes.
Implementation: The robotic arms were programmed to handle plastic sheets and finished parts with precision. Sensors and vision systems ensured accurate placement and quality inspection.
Result: The automation reduced loading and unloading times by 50%, resulting in a 20% decrease in overall cycle times. The consistent handling improved product quality and reduced waste, contributing to a higher yield.
4. Process Monitoring and Control
Implementing real-time process monitoring and control systems helps identify bottlenecks and optimize each stage of the thermoforming process. Advanced sensors and software can provide valuable data for making informed decisions.
Case Study: Real-Time Monitoring at PackPro
บริษัท: PackPro
Industry: Consumer Goods Packaging
Challenge: Inconsistent cycle times due to lack of real-time monitoring and process control, leading to unpredictable production schedules.
Solution: PackPro implemented a real-time monitoring system integrated with their thermoforming machines.
Implementation: Sensors were installed to monitor key parameters such as temperature, pressure, and cycle time. The data was analyzed using specialized software to identify inefficiencies and optimize settings.
Result: Real-time monitoring enabled PackPro to reduce cycle time variability by 15% and achieve more predictable production schedules. The ability to quickly adjust parameters based on data insights led to a 10% reduction in overall cycle times and improved product consistency.
5. Material Selection and Pre-treatment
Choosing the right materials and pre-treating them can also influence cycle times. Materials with faster heating and cooling properties, as well as pre-treatments that improve thermal conductivity, can enhance the thermoforming process.
Case Study: Material Optimization at EcoPack
บริษัท: EcoPack
Industry: Sustainable Packaging
Challenge: Long cycle times due to the use of standard plastic sheets with poor thermal properties.
Solution: EcoPack switched to high-performance plastic materials with better thermal properties and incorporated pre-treatment processes to enhance material conductivity.
Implementation: The new materials were tested for their thermoforming properties, and pre-treatment processes such as surface roughening were applied to improve heat transfer.
Result: The optimized materials and pre-treatments reduced heating and cooling times by 20%, leading to a 15% reduction in overall cycle times. The improved thermal properties also enhanced the quality of the final products.
Conclusion
Optimizing cycle times in thermoforming processes is essential for achieving higher productivity, cost savings, and improved product quality. By implementing advanced heating systems, efficient mold design, automation, real-time monitoring, and material optimization, manufacturers can significantly enhance their thermoforming operations.
The real-life case studies of Plastipack, AutoForm, MedPlast Solutions, PackPro, and EcoPack illustrate the tangible benefits of these strategies. Each company successfully addressed their specific challenges and achieved substantial improvements in cycle times, leading to increased efficiency and competitiveness.
As the manufacturing industry continues to evolve, adopting these optimization strategies will be crucial for staying ahead of the competition and meeting the growing demands of customers. By continuously innovating and refining their processes, manufacturers can ensure sustainable growth and success in the dynamic market of thermoforming.