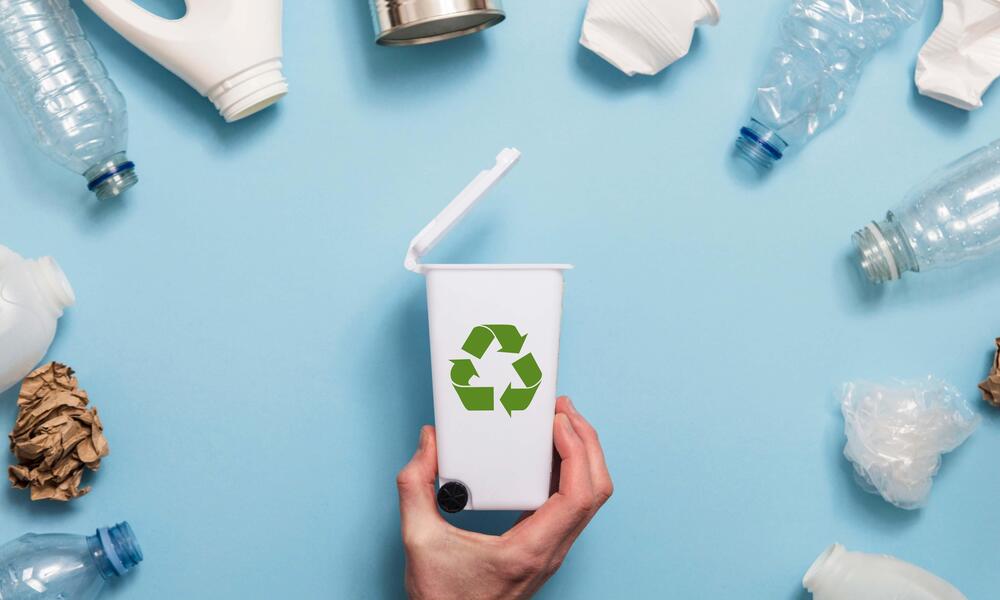
Thermoforming Large Parts: Equipment and Process Considerations
Introduction
Thermoforming is a widely used manufacturing process for creating plastic parts by heating a plastic sheet until it becomes pliable, then forming it into a specific shape using a mold. When it comes to producing large parts, the process presents unique challenges and requires specialized equipment and careful process considerations. This article delves into the key factors involved in thermoforming large parts, exploring the equipment necessary, process adjustments, and real-life case studies to illustrate successful applications.
Equipment for Thermoforming Large Parts
1. Large Format Thermoforming Machines
The backbone of any large part thermoforming operation is the thermoforming machine itself. These machines must be capable of handling large plastic sheets and providing the necessary heating and forming capabilities.
Key Features:
- Size and Capacity: Machines must accommodate large sheet sizes, often exceeding 4 feet by 8 feet.
- Heating Systems: Powerful and uniform heating systems to ensure consistent plastic pliability across the entire sheet.
- Forming Stations: Robust forming stations capable of applying sufficient pressure and maintaining precise control during the forming process.
Case Study: Thermoform Technologies Inc.
Company: Thermoform Technologies Inc.
Industry: Automotive and Aerospace
Challenge: Needed to produce large, complex parts for vehicle interiors and aerospace components.
Solution: Invested in a large format thermoforming machine with advanced heating and pressure systems. The machine had a forming area of 6 feet by 10 feet and utilized infrared heaters for uniform temperature distribution.
Result: Achieved high-quality, large parts with consistent thickness and structural integrity, meeting stringent industry standards.
2. Multi-Zone Heating Systems
Uniform heating is crucial for large parts to avoid uneven material flow and defects. Multi-zone heating systems provide precise temperature control across different sections of the plastic sheet.
Benefits:
- Temperature Control: Different zones can be set to different temperatures to ensure even heating.
- Energy Efficiency: Targeted heating reduces overall energy consumption by heating only necessary areas.
Case Study: Multi-Zone Heating at AeroForm
Company: AeroForm
Industry: Aerospace
Challenge: Inconsistent heating led to defects in large thermoformed parts.
Solution: Implemented a multi-zone heating system in their thermoforming machine. This system allowed for precise temperature control across the sheet.
Result: Improved part quality with fewer defects, leading to higher customer satisfaction and reduced material waste.
3. Advanced Vacuum and Pressure Forming Systems
For large parts, maintaining uniform pressure and vacuum across the entire mold surface is essential to avoid defects such as thinning or warping.
Key Considerations:
- Vacuum Distribution: Ensure even vacuum application to prevent localized thinning.
- Pressure Systems: High-pressure forming systems can help achieve better detail and reduce cycle times.
Case Study: PrecisionForm Systems
Company: PrecisionForm Systems
Industry: Industrial Equipment
Challenge: Needed high-detail, large parts for industrial machinery housings.
Solution: Invested in an advanced vacuum and pressure forming system. The system included a high-capacity vacuum pump and pressure forming capabilities.
Result: Produced large parts with intricate details and consistent thickness, significantly enhancing the durability and aesthetic quality of the final products.
Process Considerations for Large Part Thermoforming
1. Material Selection
Choosing the right material is crucial for large part thermoforming. The material must be durable, easy to form, and suitable for the part’s end-use environment.
Common Materials:
- ABS (Acrylonitrile Butadiene Styrene): Known for its strength and durability.
- HDPE (High-Density Polyethylene): Offers excellent impact resistance and chemical stability.
- Polycarbonate: Provides high clarity and heat resistance, ideal for transparent parts.
Case Study: Material Selection at BuildTech
Company: BuildTech
Industry: Construction
Challenge: Required large, durable parts for outdoor construction applications.
Solution: Chose HDPE for its impact resistance and durability in outdoor conditions. Conducted extensive material trials to ensure performance.
Result: Successfully produced large construction components that withstood harsh environmental conditions, leading to longer part life and reduced maintenance costs.
2. Mold Design and Fabrication
Large parts require well-designed molds to ensure consistent quality and minimize defects. Mold design should account for material shrinkage, cooling rates, and part removal.
Considerations:
- Material Flow: Ensure the mold allows for even material distribution.
- Cooling Systems: Integrated cooling channels can help control the cooling rate and reduce cycle times.
- Part Ejection: Design for easy part removal to avoid damage during demolding.
Case Study: Mold Design at MegaMold
Company: MegaMold
Industry: Heavy Equipment
Challenge: Needed to design molds for large, complex parts with intricate details.
Solution: Used advanced CAD software and 3D printing for prototyping mold designs. Integrated cooling channels and designed the mold for easy part ejection.
Result: Produced high-quality, detailed parts with reduced cycle times and minimized defects, enhancing overall production efficiency.
3. Process Control and Automation
Consistent process control is vital for producing large parts. Automation can enhance precision and reduce human error, leading to higher quality and repeatability.
Automation Components:
- Robotic Handling: For precise and repeatable placement of plastic sheets and finished parts.
- Real-Time Monitoring: Sensors and software for monitoring temperature, pressure, and vacuum levels during the process.
- Automated Trimming: Ensures consistent and accurate trimming of finished parts.
Case Study: Automation at AutoTherm
Company: AutoTherm
Industry: Automotive
Challenge: Required consistent quality and high throughput for large automotive parts.
Solution: Implemented robotic handling systems for material loading and unloading, along with real-time process monitoring. Automated trimming stations were added for finishing.
Result: Achieved consistent quality and increased production throughput. Automation reduced human error and downtime, leading to higher overall efficiency.
4. Quality Control and Inspection
For large parts, ensuring quality and consistency is critical. Implementing thorough quality control measures can help identify and address defects early in the process.
Techniques:
- Visual Inspection: Regular checks for surface defects and inconsistencies.
- Dimensional Analysis: Using precision measuring tools to verify part dimensions and tolerances.
- Non-Destructive Testing: Techniques such as ultrasonic testing to detect internal defects.
Case Study: Quality Control at SafeGuard Plastics
Company: SafeGuard Plastics
Industry: Safety Equipment
Challenge: Needed to ensure the structural integrity of large safety components.
Solution: Implemented a comprehensive quality control program, including visual inspection, dimensional analysis, and ultrasonic testing.
Result: Reduced defect rates and ensured high-quality, reliable safety components, leading to enhanced customer trust and compliance with safety standards.
Conclusion
Thermoforming large parts presents unique challenges that require specialized equipment and careful process considerations. By investing in large format thermoforming machines, advanced heating systems, and precise vacuum and pressure forming systems, companies can achieve high-quality, consistent results. Additionally, optimizing material selection, mold design, process control, and quality inspection are essential steps in producing large thermoformed parts efficiently.
The real-life case studies of Thermoform Technologies Inc., AeroForm, PrecisionForm Systems, BuildTech, MegaMold, AutoTherm, and SafeGuard Plastics illustrate the successful implementation of these strategies. Each company addressed their specific challenges and achieved significant improvements in part quality, production efficiency, and customer satisfaction.
As the demand for large, complex plastic parts continues to grow across various industries, focusing on these key equipment and process considerations will be crucial for manufacturers to remain competitive and deliver high-quality products. By continuously innovating and refining their thermoforming operations, companies can ensure long-term success and meet the evolving needs of their customers.