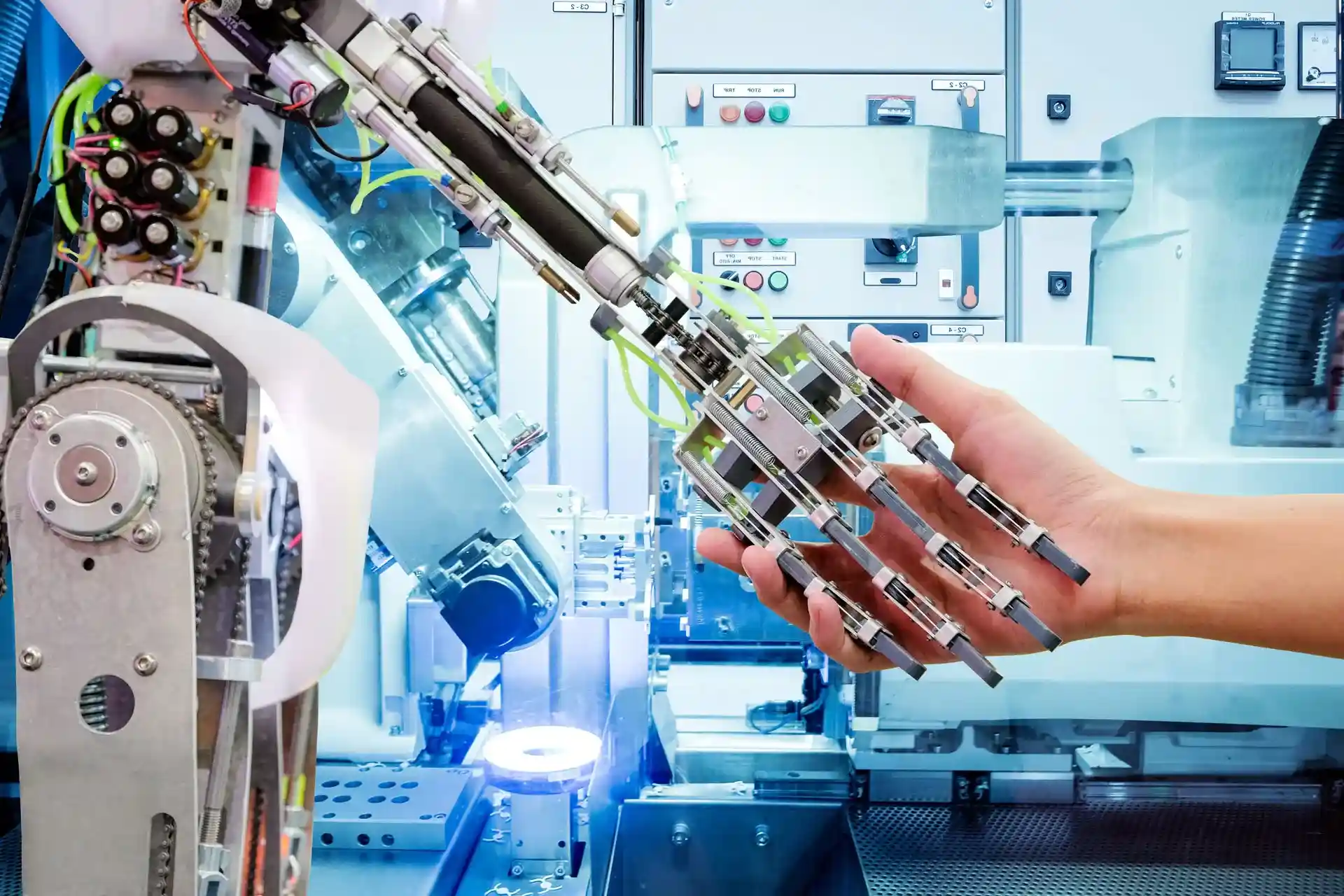
降低热成型中的废品率:技术与工艺
导言
在竞争激烈的现代制造业中,减少废料是实现经济和环境可持续发展的关键因素。在热成型行业,高废品率会严重影响盈利能力和资源效率。本文探讨了旨在最大限度降低热成型操作中废品率的各种技术和工艺,为寻求优化生产的制造商提供了全面的指导。
了解热成型中的废料
热成型中的废料是指不属于成品的任何材料,包括边角料、缺陷部件和设置板。高废品率可能由几个因素造成:
- 重大不一致
- 加热不当
- 模具设计不当
- 修剪效率低下
降低废品率的技术
1.先进的供暖系统
热成型过程中产生废料的主要原因之一是塑料板加热不均匀或不当。先进的加热系统可确保温度分布均匀,这对实现一致的材料特性至关重要。
红外线加热
红外线加热系统利用辐射传热均匀加热塑料板。它们能精确控制加热过程,减少过热或加热不足的可能性。
案例研究:精密热成型公司
- 问题 由于加热不均匀,废品率高。
- 解决方案 安装了多区域红外线加热系统,以控制温度分布。
- 结果 废品率降低了 20%,提高了整体材料利用率和产品质量。
2.自动化流程控制
工艺控制自动化可在热成型过程中进行实时调整,减少误差并提高一致性。
PLC 系统
可编程逻辑控制器 (PLC) 可以自动控制热成型工艺的各个方面,从温度控制到真空和压力设置。
案例研究:AutoForm 塑料公司
- 问题 人工流程控制导致产品质量不稳定。
- 解决方案 采用 PLC 系统实现加热、成型和冷却循环自动化。
- 结果 废品率降低了 15%,零件质量更加稳定,周期时间缩短。
3.高精度模具
模具设计在热成型工艺中起着至关重要的作用。高精度模具可确保零件成型的精确性和可重复性,从而减少材料浪费。
数控加工模具
计算机数控 (CNC) 加工可制造出高精度和高重复性的模具,最大限度地减少缺陷并提高零件的一致性。
案例研究:MoldMasters 公司
- 问题 模具尺寸不一致导致缺陷频发。
- 解决方案 所有热成型操作均过渡到数控加工模具。
- 结果 废品率降低了 25%,产品的均匀性和匹配性也得到了显著改善。
4.材料选择和测试
为热成型工艺选择合适的材料对于减少废料至关重要。不同的材料具有不同的特性,会影响成型性和最终产品质量。
材料测试
在全面生产前进行彻底的材料测试,有助于确定最适合应用的材料,减少试验和错误造成的浪费。
案例研究:PolyForm 解决方案
- 问题 由于使用了容易开裂的材料,废品率很高。
- 解决方案 进行了广泛的材料测试,并改用更合适的混合聚合物。
- 结果 30% 降低了废品率,提高了产品的耐用性和性能。
5.高效修剪技术
切边是热成型工艺的重要组成部分,但也可能成为废料的重要来源。采用高效的修边技术可以大大减少废料。
激光修剪
激光修边可实现精确、干净的切割,最大限度地减少材料浪费,提高边缘质量。
案例研究:TrimTech Industries
- 问题 人工修剪操作造成的过度浪费。
- 解决方案 投资购买了一套激光修剪系统,用于精确切割。
- 结果 废品率降低了 18%,零件美观度和尺寸精度也得到了提高。
降低废品率的流程
1.精益生产原则
采用精益生产原则有助于在整个热成型过程中识别和消除浪费。
准时制(JIT)生产
JIT 生产最大限度地减少了多余库存,降低了生产次品的几率。
案例研究:LeanForm LLC
- 问题 生产过剩和库存缺陷导致废品率居高不下。
- 解决方案 实施 JIT 生产,只在需要时才生产零件。
- 结果 随着库存管理的改善和存储成本的降低,废品率下降了 20%。
2.统计过程控制(SPC)
SPC 包括使用统计方法监测和控制生产过程,确保生产过程充分发挥其潜力。
控制图
控制图有助于跟踪流程变异性,并识别可能表明潜在问题的趋势。
案例研究:SPC 塑料公司
- 问题 产品质量不稳定,导致废品率高。
- 解决方案 利用控制图实施 SPC,监控关键工艺参数。
- 结果 通过实时处理工艺变异问题,使废品率降低了 15%。
3.持续改进(Kaizen)
Kaizen(改善)侧重于在生产过程中进行持续的、渐进的改进,以减少浪费和提高效率。
员工参与
鼓励员工发现问题并提出改进建议,可以为减少废品提供创新解决方案。
案例研究:Kaizen 热成型机
- 问题 废品率居高不下,却没有明显的解决办法。
- 解决方案 发起 "Kaizen(改善)"倡议,让全体员工参与寻找减少浪费的机会。
- 结果 废品率降低了 22%,工艺效率和员工士气不断提高。
4.培训和技能发展
训练有素的操作员不容易犯错,从而导致报废。投资于持续培训和技能发展至关重要。
认证计划
认证计划可确保操作人员了解最佳实践和最新技术。
案例研究:CertiForm 塑料
- 问题 操作员失误导致高废品率。
- 解决方案 对所有机器操作员实施认证计划。
- 结果 废品率降低 17%,操作员的能力和对工艺的理解得到提高。
5.预防性维护
对热成型设备进行定期维护可以防止故障发生,减少缺陷的出现。
定期维护
实施预防性维护计划可确保所有设备处于最佳工作状态。
案例研究:MaintenForm 公司
- 问题 设备故障频发,导致废品率居高不下。
- 解决方案 制定预防性维护计划,定期检查和维修设备。
- 结果 废品率降低了 20%,提高了机器的可靠性和正常运行时间。
结论
要降低热成型的废品率,需要采用包括先进技术、高效工艺和持续改进战略在内的多方面方法。通过投资先进的加热系统、自动化流程控制、高精度模具和高效的修边技术,制造商可以显著减少材料浪费。此外,采用精益生产原则、统计过程控制和持续改进措施,还能进一步提高生产效率和产品质量。
Precision Thermoforming Inc.、AutoForm Plastics、MoldMasters Corp.、PolyForm Solutions、TrimTech Industries、LeanForm LLC、SPC Plastics、Kaizen Thermoformers、CertiForm Plastics 和 MaintenForm Inc.的真实案例研究说明了这些战略的成功实施。每家公司都解决了各自面临的具体挑战,在减少废料方面取得了重大改进,从而提高了盈利能力和可持续发展能力。
随着热成型行业的不断发展,减少废料仍将是制造商的首要任务。通过采用新技术和优化工艺,企业可以取得长期成功,并为更可持续的未来做出贡献。