脱模过程中的常见挑战
脱模系统在带来巨大效益的同时,也会遇到影响生产效率和产品质量的挑战。以下是脱模过程中面临的一些典型问题:
粘连部件:模具与成型产品之间的粘连是一个常见问题,通常是由于冷却不足或模具设计缺陷造成的。如果零件不能完全脱离模具,就会导致生产延误、缺陷,甚至损坏模具和成品。

变形或损坏:壁薄或结构复杂的零件在脱模过程中特别容易变形或开裂。过大或不均匀的顶出力会导致这些零件变形、开裂或失去原有形状,从而导致质量缺陷和更高的废品率。
机械磨损:连续使用脱模系统会导致机械部件磨损,例如顶针、滑块和推杆。随着时间的推移,这种磨损会影响系统的可靠性,导致维护需求增加、效率降低和计划外停机。
材料残留:先前成型周期的残余塑料材料会在模具中积聚,特别是在使用气动或液压顶出的系统中。这种积聚可能会堵塞通气孔,影响系统性能,并导致后续循环中的零件质量不佳。
解决方案
- 涂抹脱模剂:使用脱模剂可以大大减少粘附问题,使零件拆卸更加顺畅。这对于设计复杂的模具尤其有用。
- 优化冷却和弹射力: 调整冷却时间,确保零件在顶出前充分凝固。同样,也要校准顶出力,使其均匀,最大限度地降低部件在移除过程中变形或损坏的风险。
- 进行定期维护: 安排例行维护以检查和更换磨损的部件,确保平稳运行并延长系统的使用寿命。这包括清洁模具表面以防止材料堆积,以及检查机械部件的磨损迹象。
通过积极解决这些问题并实施有效的策略,制造商可以提高生产质量、减少停机时间并延长脱模系统的运行寿命。
脱模技术的进步
随着制造业对精度、效率和可持续性的要求越来越高,脱模系统在先进技术的帮助下不断发展。这些创新技术不仅解决了常见的难题,还提高了生产率,最大限度地减少了停机时间,并改善了系统的整体性能。其中一些关键的进步包括
1. 智能传感器
智能传感器的引入实现了对力、温度和定时等关键参数的实时跟踪,从而改变了脱模系统。这些传感器可在脱模过程中提供精确控制,确保施加的力最佳且一致。通过持续监测模具条件,智能传感器有助于减少误差、防止零件损坏、提高整体零件质量,同时优化生产周期。
益处:
- 更精确地控制弹射过程。
- 实时调整,防止缺陷。
- 提高生产的可靠性和一致性。
2. 自适应机器人技术
融合了人工智能(AI)和机器学习的机器人系统正变得越来越多才多艺。这些机器人能够适应不同的形状、尺寸和材料,并相应地调整其动作和力量。这种灵活性使它们在处理精密或复杂部件时特别有用。通过减少人工参与,这些机器人还有助于加快生产周期。
益处:
- 灵活且可编程,适用于不同形状和尺寸的产品。
- 提高处理精密或复杂零件的精度。
减少对人工干预的依赖,提高自动化程度和效率。
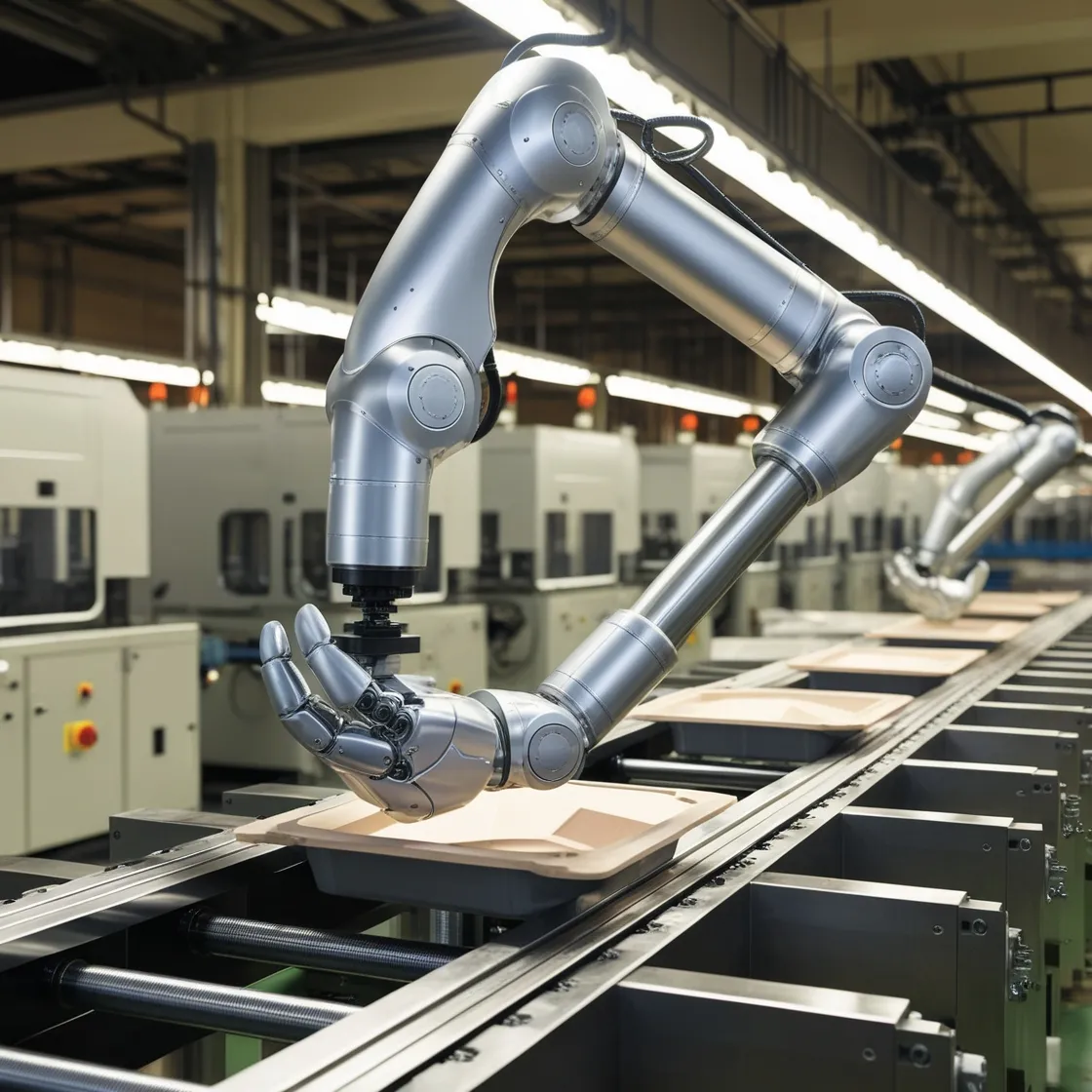
3. 自润滑组件
材料技术的进步催生了脱模系统自润滑部件的诞生。用于顶针、滑块和其他运动部件的材料可减少摩擦和磨损,从而无需频繁润滑。这不仅降低了维护要求,还延长了部件的使用寿命,确保运行更顺畅,停机时间更短。
益处:
- 减少维护需求和停机时间。
- 提高系统组件的耐用性,延长其使用寿命。
运行更顺畅,摩擦更少,提高了整体效率。
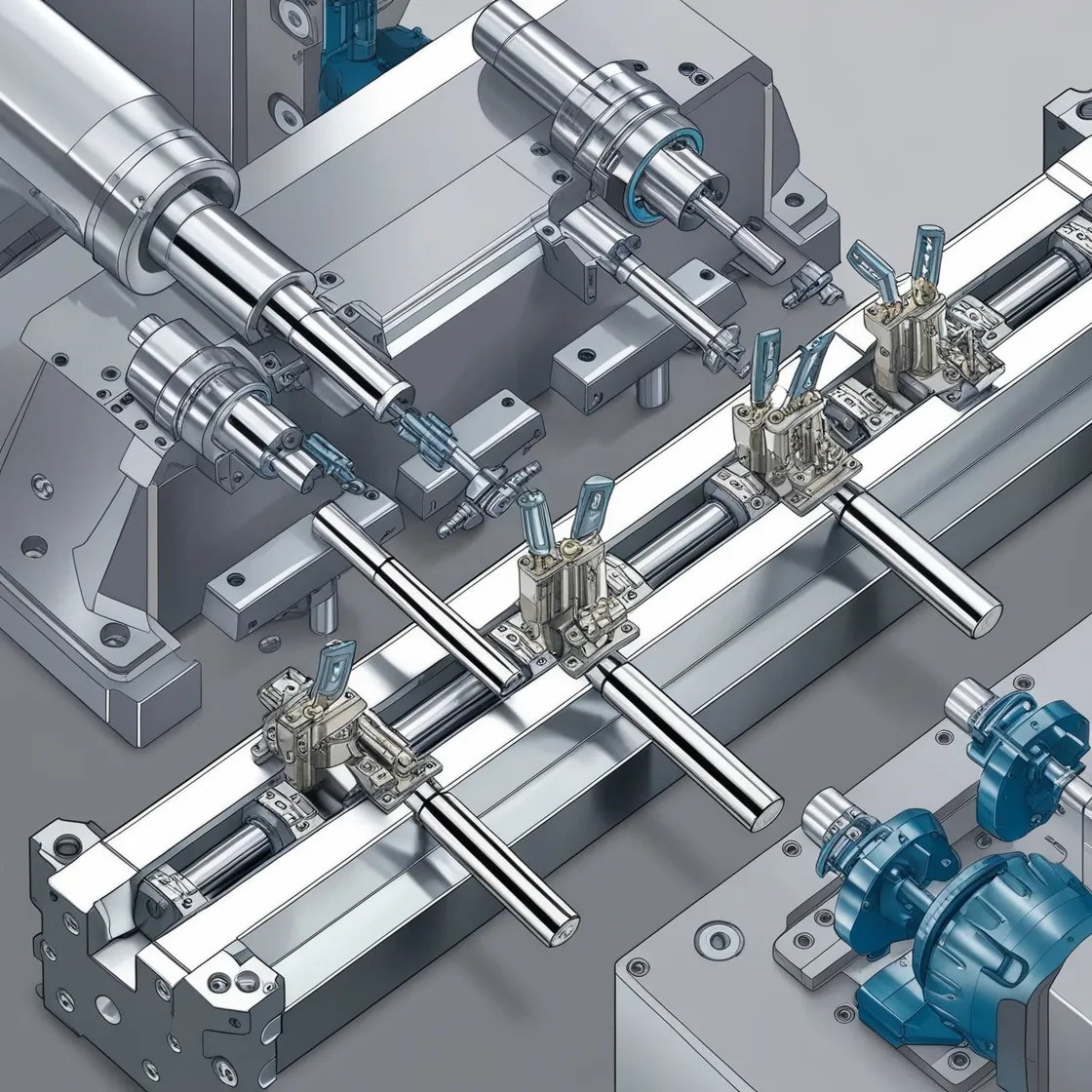
4. 环保系统
随着可持续发展成为制造商的首要任务,高能效气动和液压系统越来越受欢迎。这些生态友好型系统旨在最大限度地减少能源使用、降低对环境的影响并降低运营成本。通过优化压缩空气和液压油的使用,这些系统在提供高性能的同时,还能促进节能和减少碳足迹。
益处:
- 降低能耗,减少对环境的影响。
- 通过节能系统设计节约成本。
- 符合可持续发展标准,减少碳足迹。
通过采用这些先进技术,制造商可以提高生产效率、降低运营成本并保持高质量的产出。这些创新使我们有可能满足对更快、更精确和环境可持续的生产流程日益增长的需求。
脱模系统的未来趋势
随着热成型行业的不断发展,重点正转向更高的自动化程度、更强的可持续性和更量身定制的解决方案。未来的脱模系统将采用最先进的技术和做法,这些技术和做法将在未来数年内影响整个行业。以下是预计将主导该领域的一些主要趋势:
1. 提高自动化程度
脱模系统的未来在于全自动生产线,其中机器人脱模解决方案将成为标准,尤其是在大批量生产环境中。自动化将简化从开模到部件顶出的整个生产流程,减少人工干预,最大限度地降低出错风险。这些先进的系统将提高速度、准确性和一致性,使大规模生产管理变得更加容易,同时又不影响零件质量。
预期效益:
- 提高生产速度,降低劳动力成本。
- 部件处理更加精确和一致。
- 减少人工干预,提高运行效率。
2. 与 IoT(物联网)集成
通过物联网(IoT)整合智能技术将彻底改变脱模系统。通过将脱模设备连接到物联网网络,制造商将获得实时监控系统性能和接收预测性维护警报的能力。这种连接将为系统健康状况提供有价值的洞察力,从而在故障发生前进行抢先维修,最大限度地减少停机时间,并优化维护计划,实现最长正常运行时间。
预期效益:
- 实时监控关键系统参数。
- 预防设备故障的预测性维护。
- 通过数据驱动的洞察力改进决策。
3. 可持续做法
随着人们对环境问题的日益关注和对企业责任的重视,热成型行业正将可持续发展放在首位。未来的脱模系统将注重环保设计,最大限度地降低能耗、减少材料浪费并优化资源利用。通过采用高能效气动或液压系统等可持续发展实践,制造商可以与全球可持续发展目标保持一致,减少碳足迹,降低运营成本。
预期效益:
- 降低能源消耗和运营成本。
- 通过优化资源管理降低对环境的影响。
- 遵守日益严格的环境法规。
随着这些趋势的发展,热成型行业脱模系统的未来将以更高的自动化程度、更智能的连接性、更可持续的实践和更大的定制化为特征。通过采用这些创新技术,制造商将能够实现更高的效率、更好的质量控制和更可持续的生产方式。
结论
设计有效的脱模系统需要深入了解产品的几何形状、材料特性、周期时间要求和维护需求。虽然部件粘连、变形和机械磨损等难题很常见,但可以通过正确的系统设计和定期维护加以解决。脱模技术的进步,如智能传感器、自适应机器人技术和环保系统,正在为热成型行业设定新的标准。采用这些创新技术不仅能帮助制造商优化生产流程,还能在竞争日益激烈、以可持续发展为导向的市场中保持领先地位。通过同时考虑设计因素和技术进步,企业可以实现更高的效率、更低的运营成本和更好的产品质量。