From Zero to One: The Design, Development, and Market Feedback of the Three-Station Thermoforming Machine
Introduction
The three-station thermoforming machine is a widely used equipment in modern manufacturing industry, which is specially used to process thermoplastic materials into products of desired shapes through heating and mold forming. With the increasing demand for plastic products in industrial production, traditional single-station thermoforming machines can no longer meet the requirements of efficient production. The design and development of the three-station thermoforming machine came into being. Its birth has gone through several key stages. The following will introduce its development process in detail.
1. Design start
The design starting point of the three-station thermoforming machine comes from a deep understanding of market demand and production efficiency. The original idea is to increase the number of stations so that the heating, forming and cooling processes can be carried out simultaneously, thereby greatly shortening the production cycle. The starting point of mechanical design usually comes from product models, drawings or samples provided by customers. The design at this stage mainly focuses on the overall structure and working principle of the equipment.
The design team needs to consider how to achieve multi-station collaborative work under the premise of ensuring the stability of the equipment, so as to improve the overall production efficiency. The design stage not only involves the optimization of the mechanical structure, but also requires in-depth research on key technologies such as heat distribution and pressure control.
2. Material selection
It is crucial to understand the type of sheet material that the product will use. Select appropriate materials (such as starch degradation, photodegradation, PP, PS, PET, PVC, PLA, CPLA, CPET, calcium carbonate, OPS and other sheets) to ensure that they maintain their inherent characteristics during the extrusion process and avoid the inconvenience of frequent parameter adjustments during the thermoforming process. The choice of materials directly affects the quality of the final product and the stability of production.
The material selection process not only considers its physical and chemical properties, but also needs to evaluate the cost-effectiveness and environmental impact of the material. With the increasingly stringent environmental regulations, the selection of degradable and environmentally friendly materials has become an important part of the design process.
3. Coil preparation
After the material is determined, the coil to be processed is installed on the unwinding device, which delivers the right amount of sheet with precise accuracy. Subsequently, the sheet is fed into the thermoforming machine and passes between the upper and lower heating plates. The temperature is independently adjusted according to the material and thickness to ensure the accuracy of the forming process. The coil preparation stage is the basis of the entire thermoforming process and determines the smooth progress of subsequent links.
Modern unwinding devices are usually equipped with automatic tension control systems to ensure that the sheet always maintains appropriate tension during transmission to avoid forming defects caused by uneven tightness. In addition, an efficient feeding system can significantly improve the automation level of the production line, reduce manual operations and improve production efficiency.
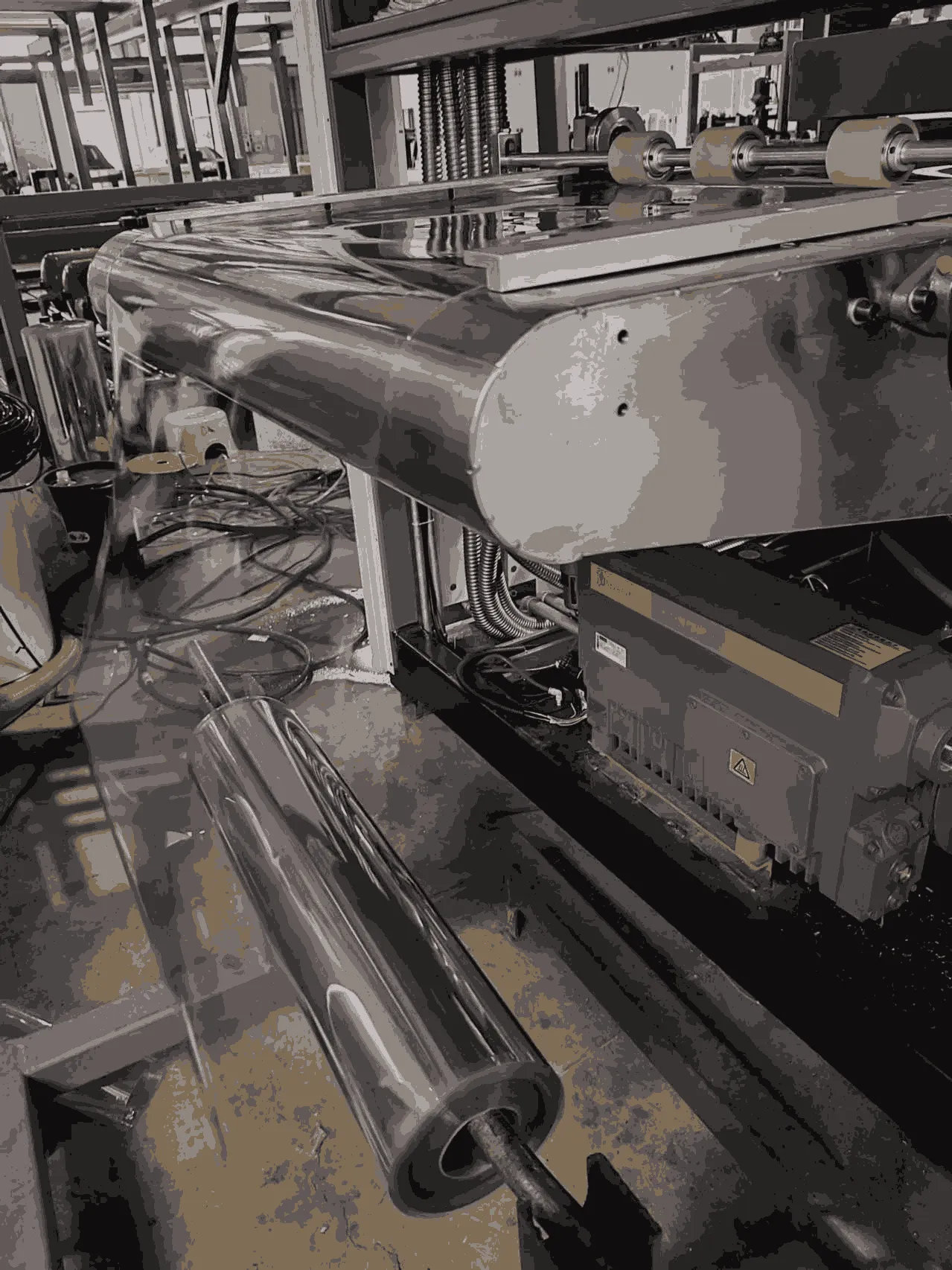
4. Mold customization
Based on product characteristics and material information, carefully design the number of cavities and expected cycle time of the mold. The mold consists of two halves, which are installed on the movable platen of the vertical elbow press. The design and manufacture of the mold is a key link in the development of the thermoforming machine, which is directly related to the shape, size and surface quality of the product. High-precision molds can not only improve the product qualification rate, but also reduce material waste and equipment wear.
Mold design not only needs to take into account the geometric shape of the product, but also needs to optimize the cooling system of the mold to ensure that the molded product can be quickly cooled and shaped, thereby shortening the production cycle. Modern mold manufacturing technologies such as 3D printing and high-precision CNC machining have further improved the manufacturing accuracy and complexity of the mold.
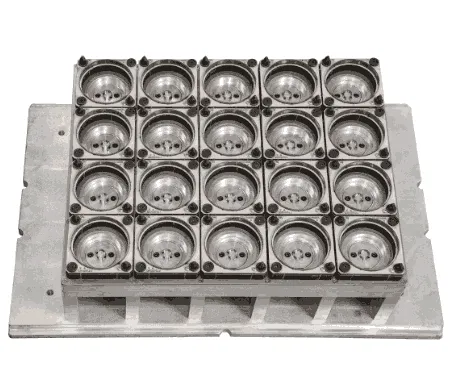
5. Plastic molding
The flat plastic sheet is introduced into the machine, and the heating element emits heat to make the plastic pliable, laying a key foundation for the molding stage. The plastic is softened by the first heating, combined with vacuum pressure or air pressure, and the material is molded in the mold, removed after cooling, and transported to the next station by a toothed chain. The technical key to the molding stage is to control the heating temperature and molding pressure to ensure the uniformity and stability of the product.
The temperature and pressure of each station need to be precisely controlled during the molding process to avoid molding defects caused by excessive heating or uneven cooling of the plastic. Modern molding equipment is usually equipped with advanced control systems that can monitor and adjust production parameters in real time to ensure consistent product quality.
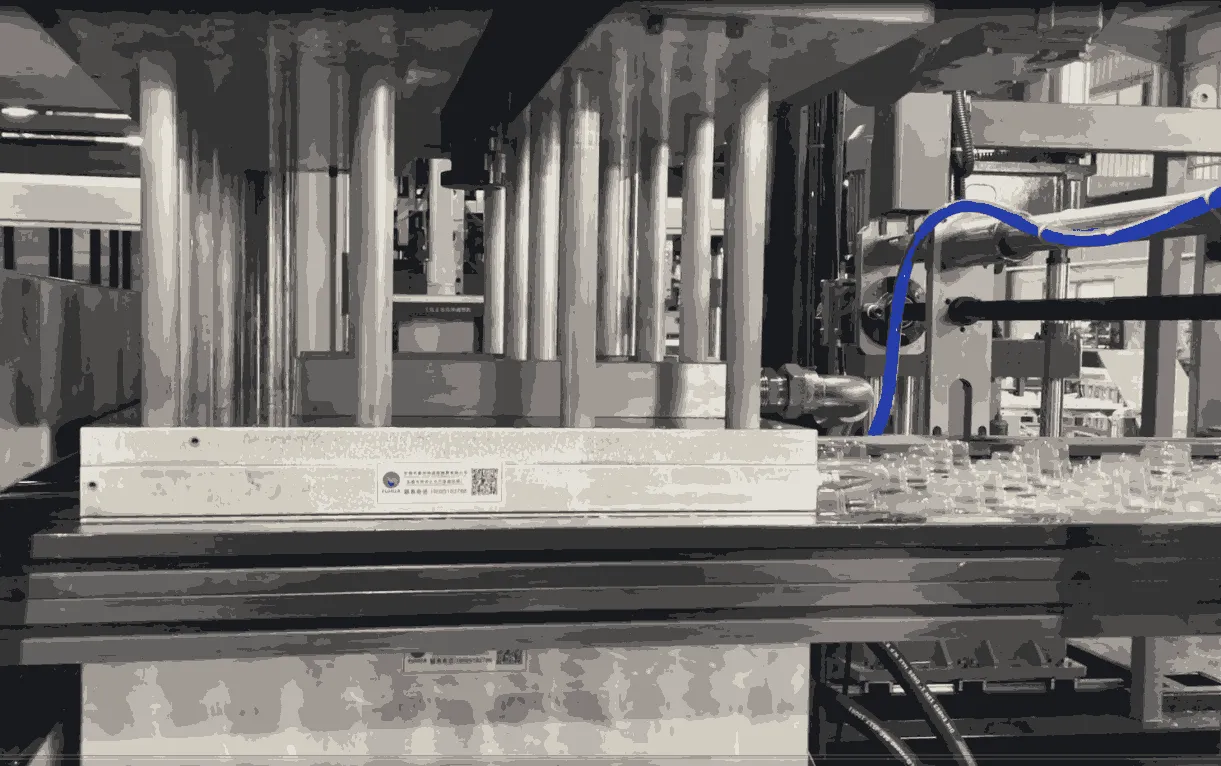
6. Precision cutting
At the second station, clean cutting is performed by the resistance heating plate to ensure the accuracy and uniformity of product size and meet strict quality standards. The cut product is attached to the plate and continues to pass through the machine to the final station. The accuracy of the cutting process directly affects the appearance and performance of the final product, so high-precision cutting equipment and advanced control technology are required.
The cutting process requires not only cutting accuracy and speed, but also the recycling of cutting waste. By optimizing the cutting path and waste handling system, material waste can be effectively reduced, and the environmental protection and economic benefits of production can be improved.
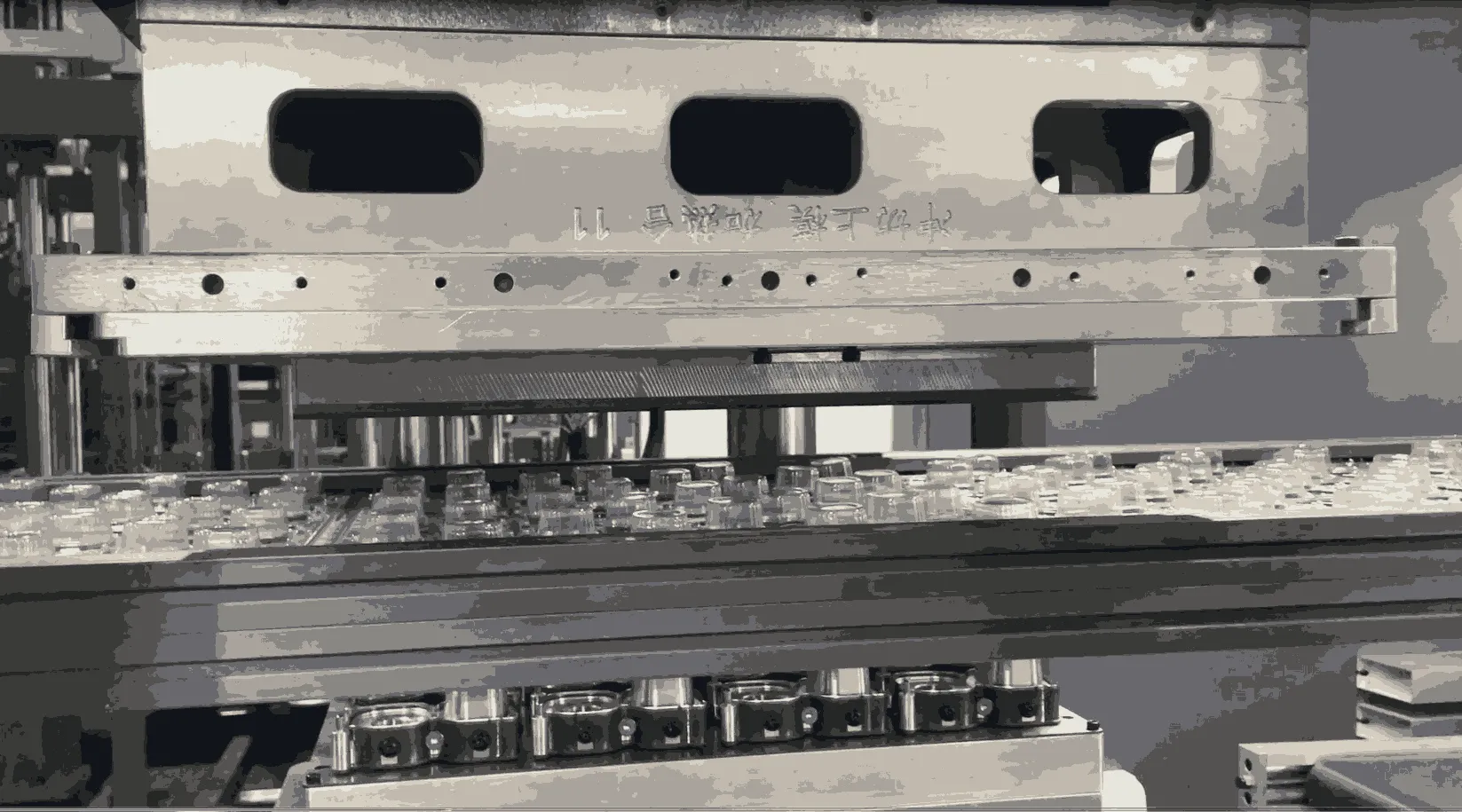
7. Efficient stacking
In the third station, products are neatly stacked and organized for efficient subsequent handling and packaging. The use of stacking stations not only simplifies the production process, but also significantly improves the overall production efficiency. An efficient stacking system can significantly reduce manual operations and improve the automation level of production, while also ensuring the consistency and reliability of each batch of products.
Efficient stacking systems often combine smart sensors and control software to automatically adjust the stacking method according to the size and weight of the product, ensuring consistent stacking quality for each batch of products. At the same time, the automated stacking system can also be seamlessly connected with the subsequent packaging system to improve the efficiency of the entire production line.
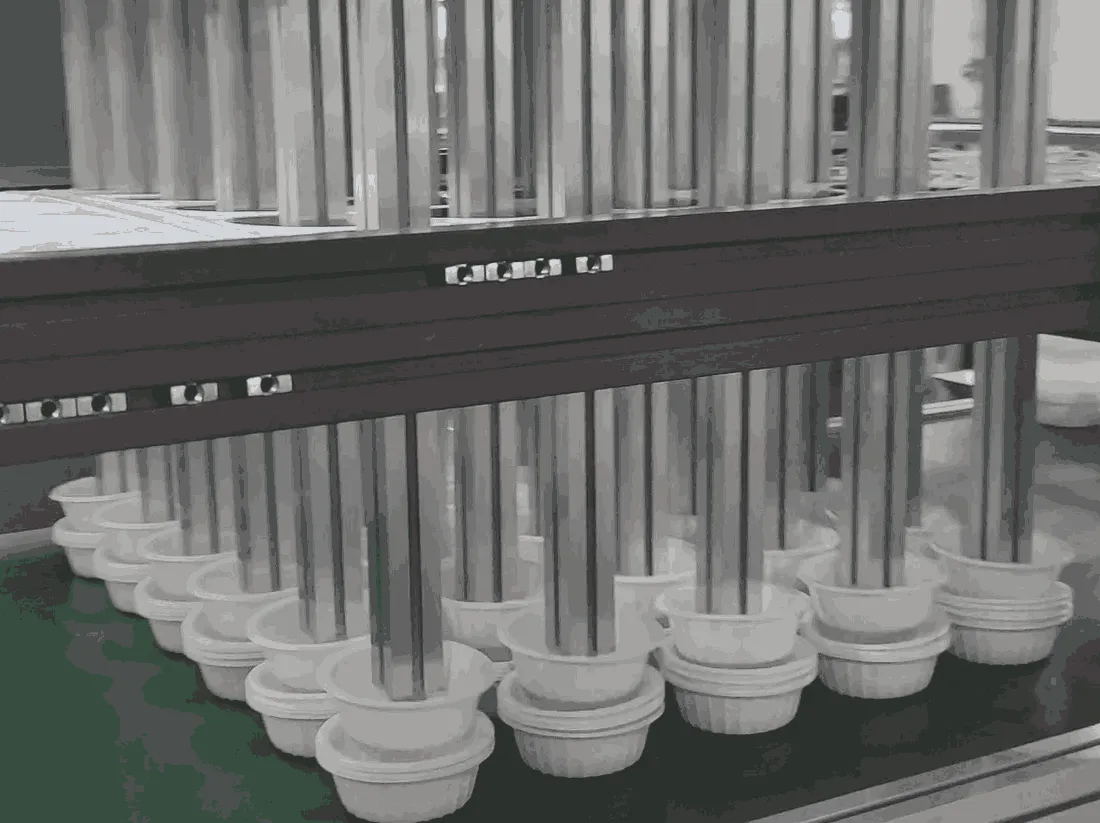
Technology R&D and design optimization
After the conception of molding, the R&D team began to tackle technical problems. The design of the three-station thermoforming machine needs to solve multiple technical problems, including:
Uniformity of heat distribution: Ensure uniform heat distribution at each station to avoid product defects during the molding process. Uniform heat distribution can be achieved through advanced heating control technology and optimized heater design.
Mold accuracy: Improve the manufacturing accuracy of the mold to ensure the quality of the molded product. High-precision CNC processing technology and strict quality control process are the key to achieving high-precision molds.
Automation control: Introduce advanced automation control systems to improve the operation convenience and production efficiency of the equipment. Modern automation control systems can not only achieve precise control of the equipment, but also optimize the production process through sensors and data analysis.
During the process of technology research and development, continuous experiments and tests are required to verify the feasibility and optimization potential of the design scheme. Through computer simulation and laboratory tests, the performance of the equipment in actual production can be predicted in advance, reducing the development cycle and cost.
Prototype manufacturing and testing
After the design scheme was determined, the first prototype of the three-station thermoforming machine was manufactured. Through a series of tests and adjustments, the performance and stability of the equipment are continuously optimized. During the test, the following aspects were focused on:
Production efficiency: Compared with traditional single-station equipment, the production efficiency of the three-station thermoforming machine is significantly improved. By optimizing the process parameters and equipment structure, higher production speed and lower energy consumption can be achieved.
Product quality: By adjusting the heating temperature and molding pressure, ensure that the molded products meet the expected quality standards. High-quality products can not only meet market demand, but also enhance the market competitiveness of enterprises.
Equipment reliability: Ensure the reliability and durability of the equipment through long-term operation tests. Reliable equipment can reduce downtime and improve the continuity and stability of production.
During the test, the R&D team will record and analyze various data, find out the key factors affecting the performance of the equipment, and make targeted improvements. Through repeated testing and optimization, the optimal equipment parameters and operating procedures are finally determined.
Put into production and market feedback
After many rounds of testing and improvement, the three-station thermoforming machine was finally put into use on the market. Due to its efficient production capacity and excellent product quality, it quickly won market recognition. User feedback further promoted the optimization and upgrading of the equipment. The data and feedback in actual use can not only help improve the design of the equipment, but also guide the research and development of new products.
The collection of market feedback is an important basis for equipment improvement. Through close cooperation with customers, manufacturers can timely understand user needs and market changes, quickly adjust production strategies and R&D directions, and maintain market competitiveness.
Continuous improvement and innovation
In order to adapt to the ever-changing market demand and technological progress, the research and development of three-station thermoforming machines has not stopped. Manufacturers continue to introduce new technologies, such as intelligent control systems, energy recovery technologies, etc., to further improve the performance and energy-saving effects of equipment. In the future, with the application of technologies such as artificial intelligence and big data.