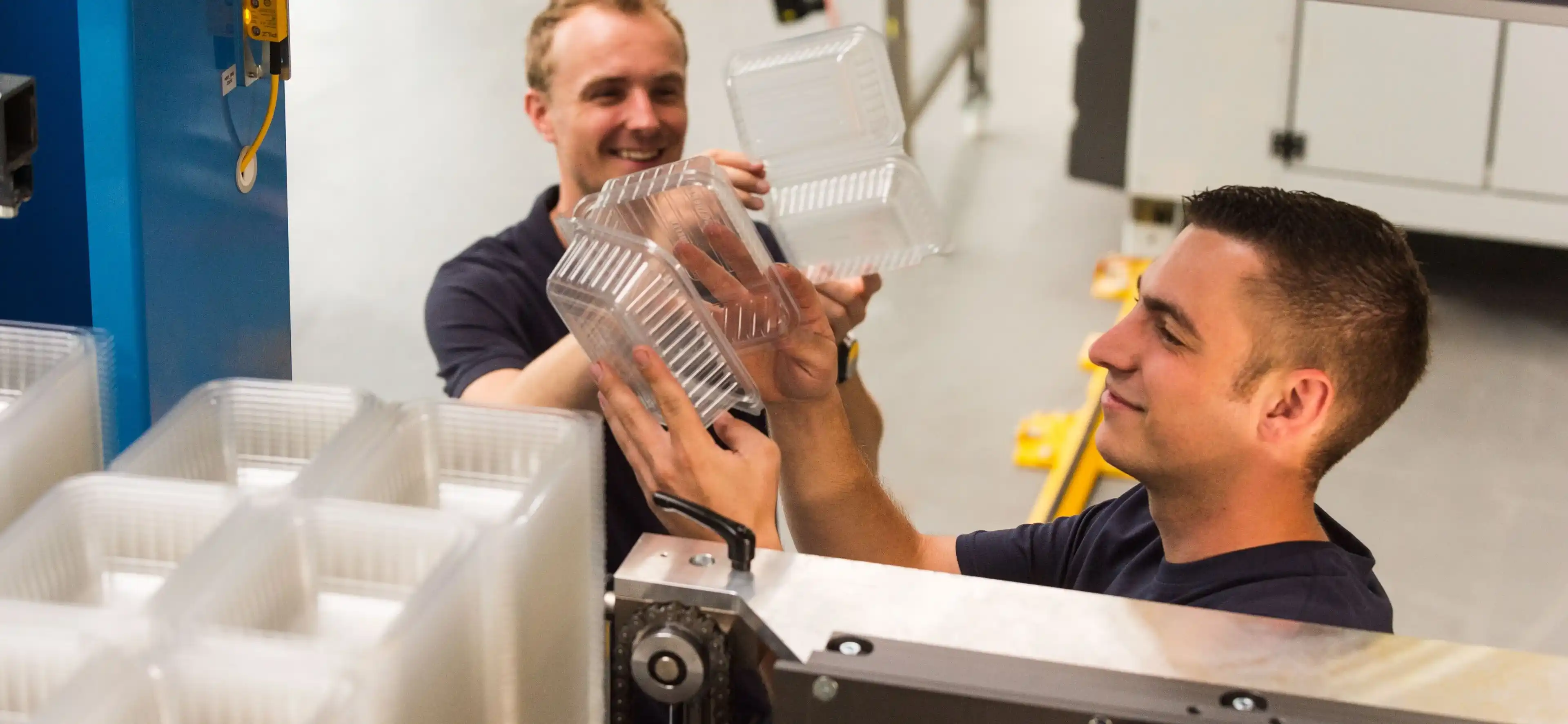
Adapting Thermoforming Machines for Biodegradable Plastics
Introduction
The shift towards sustainable manufacturing practices has prompted many industries to explore environmentally friendly materials and processes. One such advancement is the use of biodegradable plastics in thermoforming applications. Thermoforming, a process that involves heating plastic sheets and forming them into specific shapes using molds, is widely used across various sectors, including packaging, automotive, and medical devices. Adapting thermoforming machines to process biodegradable plastics presents both challenges and opportunities. This article explores the necessary modifications, benefits, and real-life case studies of integrating biodegradable plastics into thermoforming operations.
Understanding Biodegradable Plastics
Biodegradable plastics are designed to break down more quickly than traditional plastics through the action of microorganisms. Common types include polylactic acid (PLA), polyhydroxyalkanoates (PHA), and starch-based plastics. These materials offer several environmental benefits, such as reduced landfill waste and lower carbon footprints. However, they also present unique challenges in processing, requiring specific adaptations to thermoforming machines.
Modifications Required for Thermoforming Machines
1. Temperature Control
Biodegradable plastics often have different melting points and thermal properties compared to conventional plastics like PET or PVC. Therefore, precise temperature control is crucial to ensure optimal forming conditions and product quality.
Implementation:
- Upgrade heating elements to provide more accurate and uniform heat distribution.
- Integrate advanced temperature sensors to monitor and adjust the heating process in real-time.
- Implement programmable logic controllers (PLCs) for precise control over heating cycles.
2. Mold Design
Biodegradable plastics can exhibit different shrinkage rates and material flow characteristics. Adapting mold designs to accommodate these properties is essential for achieving consistent and high-quality products.
Implementation:
- Use materials with higher thermal conductivity for molds to facilitate faster and more uniform cooling.
- Incorporate adjustable venting systems to manage airflow and material flow during forming.
- Design molds with enhanced cooling channels to reduce cycle times and improve product consistency.
3. Handling and Storage
Biodegradable plastics are often more sensitive to moisture and temperature variations. Proper handling and storage are necessary to maintain material integrity and performance.
Implementation:
- Store biodegradable plastic sheets in climate-controlled environments to prevent degradation.
- Use moisture-resistant packaging for raw materials.
- Implement automated material handling systems to minimize human contact and contamination.
4. Compatibility with Additives
Biodegradable plastics may require specific additives to improve their processing and performance characteristics. Ensuring compatibility with these additives is vital for successful thermoforming.
Implementation:
- Test and validate additives such as plasticizers, stabilizers, and nucleating agents with biodegradable plastics.
- Adjust machine settings to accommodate the presence of additives.
- Work with suppliers to develop customized additive formulations that enhance the properties of biodegradable plastics.
Benefits of Adapting Thermoforming Machines
Environmental Sustainability
Using biodegradable plastics significantly reduces the environmental impact of plastic products. These materials decompose more quickly and safely, reducing landfill waste and pollution. Adapting thermoforming machines to process biodegradable plastics supports sustainable manufacturing practices and helps companies meet regulatory requirements and consumer demand for eco-friendly products.
Market Competitiveness
Adopting biodegradable plastics can enhance a company’s market competitiveness by appealing to environmentally conscious consumers. Offering sustainable product options can differentiate a brand and open new market opportunities, particularly in industries where sustainability is a key purchasing criterion.
Regulatory Compliance
Governments and regulatory bodies are increasingly imposing restrictions on single-use plastics and promoting the use of biodegradable materials. Adapting thermoforming machines to process biodegradable plastics ensures compliance with these regulations, avoiding potential fines and market access issues.
Innovation and Brand Image
Investing in sustainable technologies demonstrates a company’s commitment to innovation and environmental responsibility. This can enhance brand image and reputation, attracting customers, investors, and partners who value sustainability.
Real-Life Case Studies
Case Study 1: Sustainable Packaging Solutions
Company: GreenPack
Industry: Food Packaging
Challenge: GreenPack, a leading manufacturer of food packaging, faced growing demand for sustainable packaging solutions from major retailers and consumers. The company needed to adapt its thermoforming machines to process biodegradable plastics efficiently.
Solution: GreenPack partnered with a materials science company to develop custom PLA formulations suitable for their thermoforming applications. They upgraded their thermoforming machines with advanced temperature control systems and redesigned molds to accommodate the unique properties of PLA.
Implementation: The new setup included infrared heaters for precise temperature control and molds with enhanced cooling channels. GreenPack also implemented real-time monitoring systems to ensure consistent product quality.
Result: GreenPack successfully launched a range of biodegradable food packaging products, resulting in a 20% increase in sales and a strengthened market position. The company’s sustainable packaging solutions received positive feedback from retailers and consumers, enhancing brand loyalty and reputation.
Case Study 2: Automotive Interior Components
Company: EcoAuto
Industry: Automotive
Challenge: EcoAuto, an automotive parts manufacturer, sought to reduce the environmental impact of its interior components by switching to biodegradable plastics. The challenge was to adapt their existing thermoforming machines to process new materials like PHA.
Solution: EcoAuto collaborated with material scientists to optimize PHA formulations for thermoforming. They modified their machines to include more precise temperature controls and redesigned molds to handle the different material flow characteristics of PHA.
Implementation: The upgrades included installing advanced temperature sensors and implementing PLCs for better process control. EcoAuto also developed custom molds with improved cooling capabilities to ensure consistent quality and performance.
Result: EcoAuto successfully produced biodegradable interior components that met the automotive industry’s stringent performance and durability standards. The company achieved a 15% reduction in material costs and a 10% improvement in production efficiency. EcoAuto’s commitment to sustainability helped secure contracts with major automotive manufacturers seeking eco-friendly components.
Case Study 3: Medical Device Packaging
Company: MedBio
Industry: Medical Devices
Challenge: MedBio, a manufacturer of sterile medical device packaging, aimed to transition to biodegradable plastics to meet regulatory and environmental standards. The challenge was to maintain the high quality and sterility required for medical applications.
Solution: MedBio selected starch-based biodegradable plastics for their packaging and adapted their thermoforming machines accordingly. They invested in advanced heating and cooling systems to handle the unique properties of starch-based materials and ensure product sterility.
Implementation: The adaptations included integrating high-precision infrared heaters, upgrading molds for faster cooling, and implementing automated handling systems to minimize contamination risks. MedBio also collaborated with suppliers to develop biodegradable plastic formulations that met medical-grade standards.
Result: MedBio successfully launched a line of biodegradable medical device packaging, achieving compliance with regulatory standards and reducing environmental impact. The new packaging solutions enhanced the company’s reputation for innovation and sustainability, leading to increased market share and customer satisfaction.
Conclusion
Adapting thermoforming machines to process biodegradable plastics offers significant benefits in terms of environmental sustainability, market competitiveness, regulatory compliance, and innovation. While the transition presents challenges, such as modifying temperature control systems, redesigning molds, and ensuring material compatibility, the rewards are substantial.
The real-life case studies of GreenPack, EcoAuto, and MedBio illustrate how companies can successfully adapt their thermoforming processes to integrate biodegradable plastics. These companies not only met their sustainability goals but also achieved operational efficiencies, cost savings, and enhanced market positions.
As the demand for sustainable products continues to grow, investing in the adaptation of thermoforming machines for biodegradable plastics will become increasingly important. By embracing this transition, manufacturers can lead the way in sustainable manufacturing, meet regulatory requirements, and satisfy the evolving preferences of consumers and businesses alike.