How Thermoforming Cooling Systems Operate
Thermoforming involves shaping a heated thermoplastic sheet over a mould. The process relies heavily on energy, with the heating system consuming more than 70% of the energy requirement. Basic principles of thermoforming include heating, moulding, and cooling. Cooling plays a vital role in solidifying the formed sheet, ensuring product quality and integrity. Efficient cooling can reduce mould temperature by up to 70.3% within 25 seconds using pressurised air. A well-designed thermoforming cooling system enhances production speed and maintains high-quality standards in finished products.
Understanding the Thermoforming Process
Heating Phase
The heating phase in thermoforming sets the foundation for the entire process. Temperature control plays a crucial role in this stage. Consistent and accurate temperature regulation ensures that the thermoplastic sheet reaches the optimal pliability. This precision prevents defects and enhances product quality. Research highlights the importance of maintaining consistent temperature control for successful thermoforming.
Different types of materials require specific heating conditions. Common materials include polyethylene, polypropylene, and polyvinyl chloride. Each material has unique properties and melting points. Understanding these differences is essential for achieving the desired results. Material selection impacts the heating duration and temperature settings.
Moulding Phase
The moulding phase follows the heating stage. Mould design considerations significantly influence the final product’s shape and quality. Designers must account for factors like draft angles, undercuts, and surface finish. These elements ensure that the moulded part releases easily and maintains its intended form.
The impact on product shape and quality cannot be overstated. A well-designed mould leads to precise and consistent shapes. Quality improvements result from attention to detail during the moulding phase. The choice of mould materials also affects the outcome. Aluminium and steel are popular choices due to their durability and heat conductivity.
Understanding the Thermoforming Process
Heating Phase
The heating phase in thermoforming sets the foundation for the entire process. Temperature control plays a crucial role in this stage. Consistent and accurate temperature regulation ensures that the thermoplastic sheet reaches the optimal pliability. This precision prevents defects and enhances product quality. Research highlights the importance of maintaining consistent temperature control for successful thermoforming.
Different types of materials require specific heating conditions. Common materials include polyethylene, polypropylene, and polyvinyl chloride. Each material has unique properties and melting points. Understanding these differences is essential for achieving the desired results. Material selection impacts the heating duration and temperature settings.
Moulding Phase
The moulding phase follows the heating stage. Mould design considerations significantly influence the final product’s shape and quality. Designers must account for factors like draft angles, undercuts, and surface finish. These elements ensure that the moulded part releases easily and maintains its intended form.
The impact on product shape and quality cannot be overstated. A well-designed mould leads to precise and consistent shapes. Quality improvements result from attention to detail during the moulding phase. The choice of mould materials also affects the outcome. Aluminium and steel are popular choices due to their durability and heat conductivity.
The Cooling Phase in Thermoforming
Importance of Cooling
Cooling plays a crucial role in the thermoforming process. The cooling phase ensures that the formed thermoplastic sheet retains its shape and integrity. Proper cooling prevents warping and deformation, which can compromise product quality. A well-executed cooling phase enhances the structural integrity of the final product.
Cooling also influences production speed. Efficient cooling systems reduce the time needed for each cycle. Faster cooling leads to increased production rates. Manufacturers can produce more units in less time. This efficiency results in cost savings and higher output.
Types of Thermoforming Cooling Systems
Various types of thermoforming cooling systems exist to meet different production needs. Each system offers unique advantages.
Air Circulation Cooling
Air circulation cooling uses fans to circulate air around the mould. This method is effective for cooling heavy-gauge parts. Fans provide consistent airflow, which helps in even cooling. Air circulation is suitable for materials that do not require rapid cooling. This method is energy-efficient and cost-effective.
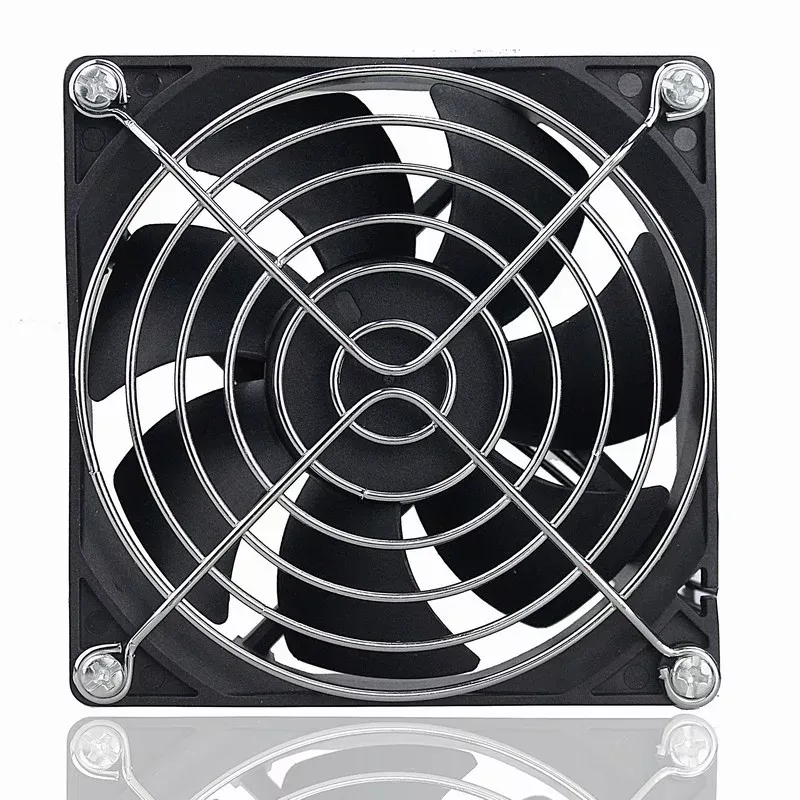
Liquid Cooling Systems
Liquid cooling systems involve circulating water or other liquids around the mould. This method provides faster cooling compared to air circulation. Liquid cooling is ideal for high-speed production environments. Water’s high thermal conductivity allows for rapid heat dissipation. Liquid cooling ensures uniform temperature distribution across the mould.
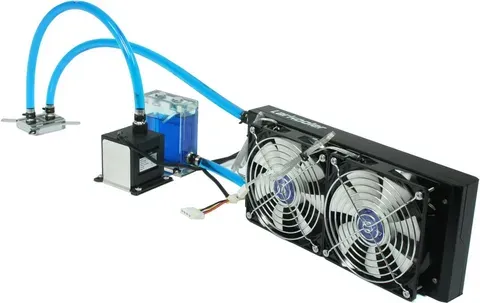
Comparative Data:
Air Circulation Cooling: Suitable for heavy-gauge parts, energy-efficient.
Liquid Cooling Systems: Faster cooling, ideal for high-speed production.
A combination of both air and liquid cooling can be used for optimal results. Some systems use humidified air containing water for enhanced cooling. The choice of cooling system depends on the material and production requirements.
Impact of Thermoforming Cooling Systems on Efficiency and Quality
Efficiency Improvements
Thermoforming cooling systems enhance production efficiency significantly. The reduction in production time stands as a primary benefit. Rapid cooling methods allow manufacturers to decrease cycle times. Shorter cycles enable higher throughput, which boosts overall productivity. Efficient cooling systems ensure that each product cools uniformly and quickly. This uniformity prevents bottlenecks in the production line.
Energy consumption considerations also play a crucial role in efficiency. Advanced thermoforming cooling systems optimise energy use. These systems utilise precise temperature control to minimise waste. Energy-efficient cooling reduces operational costs. Manufacturers can achieve sustainability goals through reduced energy consumption. This approach aligns with modern environmental standards.
Quality Enhancements
Thermoforming cooling systems contribute to quality enhancements in several ways. Aesthetic improvements become evident in the final products. Proper cooling prevents surface defects such as warping or uneven textures. The cooling phase ensures a smooth and consistent finish. High-quality aesthetics increase product appeal and marketability.
Durability and strength also improve with effective cooling. The cooling process solidifies the material’s structure. Solidification enhances the mechanical properties of the product. Products exhibit greater resistance to wear and tear. Enhanced durability extends the product’s lifespan. Customers benefit from reliable and long-lasting items.
Conclusion
In conclusion, thermoforming cooling systems play a pivotal role in both efficiency and quality. These systems reduce production time and energy consumption. They also enhance the aesthetic and structural qualities of products. Manufacturers gain competitive advantages through these improvements. Investing in advanced cooling technologies yields significant returns.
Efficient cooling systems in thermoforming processes offer numerous benefits. These systems ensure high product quality by preventing thermal deformation and enhancing structural integrity. Improved aesthetics result from uniform cooling, which eliminates surface defects. Efficient cooling reduces production time by accelerating cycle completion. This efficiency leads to lower operational costs and increased output. Manufacturers gain competitive advantages through optimised production processes. Cooling channels further enhance cooling rates and uniformity. The integration of advanced cooling technologies is crucial for achieving superior performance. Investing in these systems proves beneficial for both productivity and cost-effectiveness.