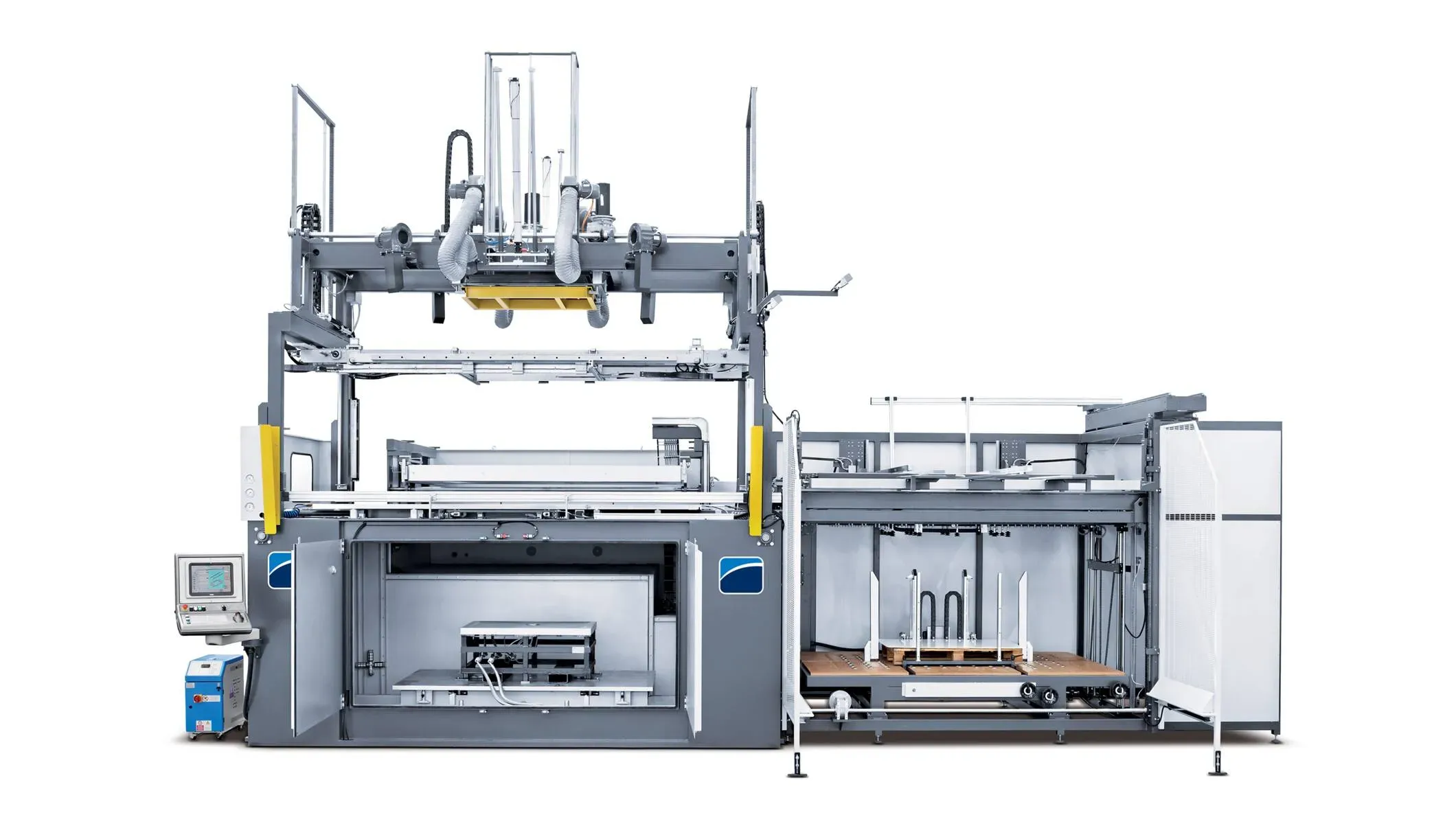
Improving Material Utilization in Thermoforming Operations
Introduction
Material utilization is a critical factor in the efficiency and cost-effectiveness of thermoforming operations. Maximizing the use of raw materials not only reduces waste and environmental impact but also enhances profitability and competitiveness. This article explores strategies for improving material utilization in thermoforming processes, providing detailed insights and real-life case studies to illustrate effective implementation.
Understanding Material Utilization in Thermoforming
Material utilization in thermoforming refers to the ratio of the actual amount of material used in the final product to the total amount of material initially loaded into the machine. High material utilization means that a greater percentage of the input material is converted into finished products, minimizing waste and reducing costs. Key factors influencing material utilization include sheet thickness, cutting patterns, mold design, and process parameters.
Strategies for Improving Material Utilization
1. Optimizing Sheet Thickness
One of the most direct ways to improve material utilization is by optimizing the thickness of the plastic sheets used in thermoforming. Using the minimum thickness necessary to meet product specifications can significantly reduce material consumption.
Implementation:
- Conduct a thorough analysis of product requirements to determine the optimal sheet thickness.
- Use finite element analysis (FEA) software to simulate product performance and identify areas where material thickness can be reduced without compromising quality.
- Implement quality control measures to ensure consistent sheet thickness during production.
Case Study: Reducing Sheet Thickness at PackRight
Company: PackRight
Industry: Packaging
Challenge: PackRight aimed to reduce material costs by optimizing the thickness of their thermoformed packaging products.
Solution: The company conducted an FEA study to determine the minimum thickness required for their products while maintaining structural integrity. They then implemented new quality control processes to ensure consistent sheet thickness.
Result: PackRight achieved a 15% reduction in material usage, leading to significant cost savings and improved material utilization. The quality of the final products remained high, with no compromise on performance.
2. Advanced Cutting and Trimming Techniques
Efficient cutting and trimming processes can significantly enhance material utilization by minimizing scrap and maximizing the use of the plastic sheet.
Implementation:
- Invest in high-precision cutting and trimming equipment to reduce material waste.
- Use nesting software to optimize cutting patterns and maximize the number of parts produced from each sheet.
- Implement automated trimming systems to ensure consistent and accurate cuts.
Case Study: Nesting Software at AutoTrim
Company: AutoTrim
Industry: Automotive
Challenge: AutoTrim faced high material waste due to inefficient cutting patterns in their thermoforming process.
Solution: The company adopted advanced nesting software to optimize cutting layouts and minimize scrap. They also invested in high-precision trimming equipment to enhance cutting accuracy.
Result: AutoTrim reduced material waste by 20%, significantly improving material utilization. The optimized cutting patterns allowed for more parts to be produced from each sheet, enhancing overall productivity.
3. Enhancing Mold Design
Efficient mold design can reduce material waste by ensuring uniform material distribution and minimizing excess material usage.
Implementation:
- Design molds with uniform wall thickness to reduce material waste.
- Use multi-cavity molds to produce multiple parts simultaneously, enhancing material efficiency.
- Implement mold flow analysis to identify and address areas of potential material waste.
Case Study: Uniform Wall Thickness at MedForm
Company: MedForm
Industry: Medical Devices
Challenge: MedForm experienced material waste due to non-uniform wall thickness in their thermoformed medical device components.
Solution: The company redesigned their molds to ensure uniform wall thickness and conducted mold flow analysis to optimize material distribution.
Result: MedForm reduced material waste by 25%, improving material utilization and reducing production costs. The redesigned molds also enhanced product quality and consistency.
4. Process Parameter Optimization
Optimizing process parameters such as temperature, pressure, and cycle time can enhance material utilization by improving the forming efficiency and reducing defects.
Implementation:
- Use real-time monitoring systems to track and adjust process parameters for optimal performance.
- Implement statistical process control (SPC) to identify and eliminate process variations.
- Conduct regular maintenance and calibration of equipment to ensure consistent operation.
Case Study: Real-Time Monitoring at CleanPack
Company: CleanPack
Industry: Consumer Goods Packaging
Challenge: CleanPack faced inconsistent material utilization due to variations in process parameters during thermoforming.
Solution: The company implemented real-time monitoring systems to track key process parameters and make adjustments as needed. They also used SPC to identify and address process variations.
Result: CleanPack improved material utilization by 18%, reducing waste and enhancing product consistency. The real-time monitoring system allowed for immediate adjustments, ensuring optimal process performance.
5. Recycling and Reuse of Scrap Material
Recycling and reusing scrap material can further improve material utilization by reducing the need for new raw materials.
Implementation:
- Implement an in-house recycling system to process and reuse scrap material.
- Use regrind material in non-critical parts to reduce the consumption of virgin materials.
- Work with suppliers to develop closed-loop recycling programs for plastic sheets.
Case Study: In-House Recycling at EcoTherm
Company: EcoTherm
Industry: Sustainable Packaging
Challenge: EcoTherm aimed to reduce their environmental impact by recycling and reusing scrap material in their thermoforming process.
Solution: The company invested in an in-house recycling system to process scrap material and reintroduce it into production. They also worked with suppliers to develop a closed-loop recycling program for their plastic sheets.
Result: EcoTherm reduced their reliance on virgin materials by 30%, significantly improving material utilization. The recycling initiatives also enhanced the company’s sustainability efforts and reduced overall production costs.
6. Material Selection
Choosing materials that are easier to process and have better forming properties can enhance material utilization.
Implementation:
- Select materials with high formability and low shrinkage rates to reduce waste.
- Work with material suppliers to develop custom formulations that optimize forming efficiency.
- Conduct material trials to evaluate and compare the performance of different plastics.
Case Study: Custom Material Formulation at FlexiForm
Company: FlexiForm
Industry: Consumer Electronics
Challenge: FlexiForm sought to improve material utilization by selecting materials with better forming properties for their thermoformed electronic components.
Solution: The company collaborated with material suppliers to develop custom plastic formulations that optimized forming efficiency and reduced waste. They conducted extensive material trials to evaluate performance.
Result: FlexiForm improved material utilization by 22%, reducing waste and enhancing product quality. The custom formulations provided better forming properties, leading to more efficient production processes.
7. Employee Training and Best Practices
Training employees on best practices and efficient material handling techniques can significantly enhance material utilization.
Implementation:
- Conduct regular training sessions on efficient material handling and process optimization.
- Develop standard operating procedures (SOPs) for material handling and process control.
- Encourage continuous improvement and feedback from employees to identify and address inefficiencies.
Case Study: Employee Training at PackTech
Company: PackTech
Industry: Industrial Packaging
Challenge: PackTech faced inconsistent material utilization due to a lack of standardized procedures and employee training.
Solution: The company implemented a comprehensive training program focused on efficient material handling and process optimization. They also developed SOPs to standardize best practices.
Result: PackTech improved material utilization by 15%, reducing waste and enhancing production efficiency. The training program empowered employees to identify and address inefficiencies, fostering a culture of continuous improvement.
Conclusion
Improving material utilization in thermoforming operations is essential for enhancing productivity, reducing costs, and minimizing environmental impact. By optimizing sheet thickness, implementing advanced cutting and trimming techniques, enhancing mold design, optimizing process parameters, recycling and reusing scrap material, selecting the right materials, and training employees, companies can achieve significant improvements in material utilization.
The real-life case studies of PackRight, AutoTrim, MedForm, CleanPack, EcoTherm, FlexiForm, and PackTech demonstrate the tangible benefits of these strategies. Each company successfully addressed their specific challenges and achieved substantial improvements in material utilization, leading to cost savings, enhanced sustainability, and improved product quality.
As the manufacturing industry continues to evolve, focusing on material utilization will be crucial for maintaining competitiveness and meeting the growing demands for sustainable and cost-effective production practices. By continuously innovating and refining their processes, manufacturers can ensure long-term success and contribute to a more sustainable future.