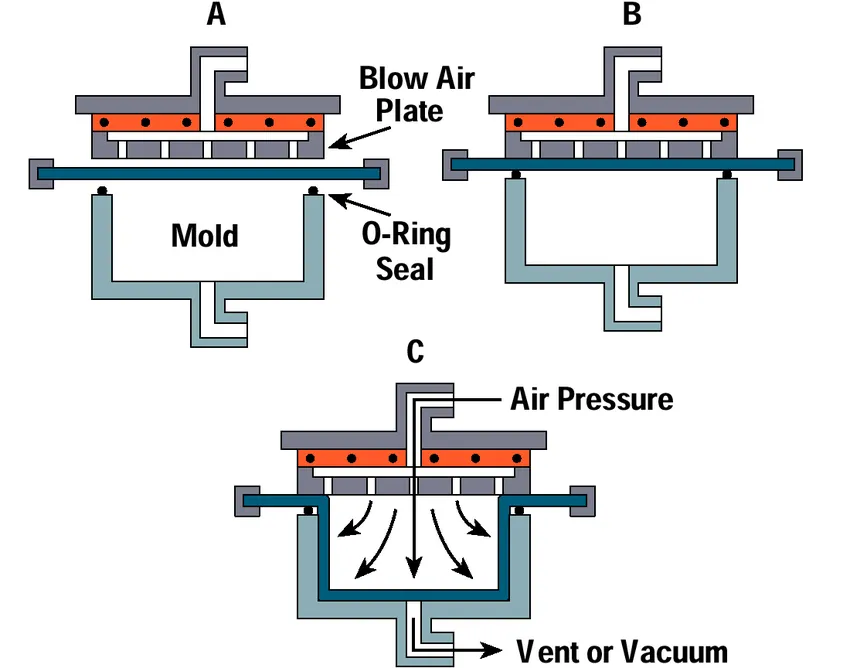
Otimização dos tempos de ciclo em processos de termoformagem
Introdução
No mundo competitivo do fabrico de plásticos, a otimização dos tempos de ciclo nos processos de termoformagem é crucial para aumentar a produtividade, reduzir os custos e manter padrões de alta qualidade. A termoformagem, um processo que envolve o aquecimento de folhas de plástico e a sua conformação em formas específicas utilizando moldes, é amplamente utilizada em várias indústrias, incluindo a de embalagens, automóvel e dispositivos médicos. Este artigo explora estratégias para otimizar os tempos de ciclo em processos de termoformagem, fornecendo informações detalhadas e estudos de caso reais para ilustrar uma implementação eficaz.
Compreender os tempos de ciclo na termoformagem
O tempo de ciclo na termoformagem refere-se ao tempo total necessário para completar um ciclo de produção, desde o aquecimento da folha de plástico até à ejeção da peça acabada do molde. É composto por várias fases:
- Tempo de aquecimento: O tempo necessário para aquecer a folha de plástico até à temperatura de formação necessária.
- Tempo de formação: O tempo necessário para moldar a folha de plástico aquecida utilizando o molde.
- Tempo de arrefecimento: A duração do arrefecimento do plástico formado para manter a sua forma.
- Tempo de ejeção: O tempo necessário para retirar a peça acabada do molde.
- Tempo de carga e descarga: O tempo gasto na carga de matérias-primas e na descarga de produtos acabados.
Cada etapa tem impacto no tempo total do ciclo, e a otimização destas fases pode conduzir a melhorias significativas na produtividade e na relação custo-eficácia.
Estratégias para otimizar os tempos de ciclo
1. Sistemas de aquecimento avançados
Um dos factores críticos na redução dos tempos de ciclo é a eficiência do sistema de aquecimento. As tecnologias de aquecimento avançadas, como os aquecedores de infravermelhos (IR) e os aquecedores de cerâmica, podem proporcionar um aquecimento mais rápido e mais uniforme em comparação com os sistemas tradicionais.
Estudo de caso: Aquecimento por infravermelhos de alta velocidade na Plastipack
Empresa: Plastipack
Indústria: Embalagem
Desafio: A Plastipack enfrentava longos tempos de aquecimento, o que levava a tempos de ciclo alargados e a uma capacidade de produção limitada.
Solução: A empresa actualizou os seus sistemas de aquecimento por infravermelhos de alta velocidade, que permitem um aquecimento rápido e uniforme.
Implementação: Os aquecedores IR foram instalados nas máquinas de termoformagem, reduzindo o tempo de aquecimento em 30%. O novo sistema permitiu um controlo preciso da temperatura, garantindo propriedades consistentes do material.
Resultado: A Plastipack registou uma redução de 25% no tempo total do ciclo, o que levou a um aumento significativo do rendimento da produção e a uma diminuição do consumo de energia.
2. Conceção e arrefecimento eficientes do molde
A otimização da conceção do molde e dos sistemas de arrefecimento pode reduzir drasticamente os tempos de moldagem e de arrefecimento. A utilização de materiais com elevada condutividade térmica e a incorporação de canais de arrefecimento avançados podem aumentar a eficiência do arrefecimento.
Estudo de caso: Canais de arrefecimento optimizados na AutoForm
Empresa: AutoFormulário
Indústria: Automóvel
Desafio: Tempos de arrefecimento longos devido a uma conceção ineficiente do molde, resultando em estrangulamentos e aumento dos custos de produção.
Solução: A AutoForm redesenhou os seus moldes utilizando alumínio, que tem melhor condutividade térmica do que o aço. Além disso, integraram canais avançados de arrefecimento conformal.
Implementação: Os novos moldes foram fabricados utilizando tecnologia de impressão 3D para criar canais de arrefecimento complexos que se adaptam à forma das peças.
Resultado: Os tempos de arrefecimento foram reduzidos em 40%, e os tempos de ciclo globais diminuíram em 20%. Isto levou a um aumento de 15% na eficiência da produção e melhorou a qualidade das peças devido ao arrefecimento uniforme.
3. Automação e robótica
A integração da automação e da robótica no processo de termoformagem pode reduzir significativamente os tempos de carga, descarga e ejeção. Os sistemas automatizados garantem um manuseamento consistente e rápido dos materiais, reduzindo o erro humano e aumentando a eficiência global.
Estudo de caso: Integração robótica na MedPlast Solutions
Empresa: Soluções MedPlast
Indústria: Dispositivos médicos
Desafio: Os processos manuais de carga e descarga eram morosos e propensos a erros, levando a tempos de ciclo prolongados.
Solução: A MedPlast Solutions integrou braços robóticos nas suas linhas de termoformagem para automatizar os processos de carga e descarga.
Implementação: Os braços robóticos foram programados para manipular com precisão as folhas de plástico e as peças acabadas. Os sensores e os sistemas de visão asseguram uma colocação exacta e um controlo de qualidade.
Resultado: A automatização reduziu os tempos de carga e descarga em 50%, resultando numa diminuição de 20% nos tempos de ciclo globais. O manuseamento consistente melhorou a qualidade do produto e reduziu o desperdício, contribuindo para um maior rendimento.
4. Monitorização e controlo do processo
A implementação de sistemas de monitorização e controlo de processos em tempo real ajuda a identificar estrangulamentos e a otimizar cada fase do processo de termoformagem. Sensores e software avançados podem fornecer dados valiosos para a tomada de decisões informadas.
Estudo de caso: Monitorização em tempo real na PackPro
Empresa: PackPro
Indústria: Embalagem de bens de consumo
Desafio: Tempos de ciclo inconsistentes devido à falta de monitorização em tempo real e de controlo do processo, conduzindo a calendários de produção imprevisíveis.
Solução: A PackPro implementou um sistema de monitorização em tempo real integrado nas suas máquinas de termoformagem.
Implementação: Foram instalados sensores para monitorizar parâmetros-chave como a temperatura, a pressão e o tempo de ciclo. Os dados foram analisados utilizando software especializado para identificar ineficiências e otimizar as definições.
Resultado: A monitorização em tempo real permitiu que a PackPro reduzisse a variabilidade do tempo de ciclo em 15% e conseguisse calendários de produção mais previsíveis. A capacidade de ajustar rapidamente os parâmetros com base em informações de dados levou a uma redução de 10% nos tempos de ciclo gerais e melhorou a consistência do produto.
5. Seleção de materiais e pré-tratamento
A escolha dos materiais corretos e o seu pré-tratamento também podem influenciar os tempos de ciclo. Os materiais com propriedades de aquecimento e arrefecimento mais rápidas, bem como os pré-tratamentos que melhoram a condutividade térmica, podem melhorar o processo de termoformagem.
Estudo de caso: Otimização de materiais na EcoPack
Empresa: EcoPack
Indústria: Embalagens sustentáveis
Desafio: Tempos de ciclo longos devido à utilização de folhas de plástico normalizadas com fracas propriedades térmicas.
Solução: A EcoPack mudou para materiais plásticos de alto desempenho com melhores propriedades térmicas e incorporou processos de pré-tratamento para melhorar a condutividade do material.
Implementação: Os novos materiais foram testados quanto às suas propriedades de termoformagem e foram aplicados processos de pré-tratamento, como o desbaste da superfície, para melhorar a transferência de calor.
Resultado: Os materiais optimizados e os pré-tratamentos reduziram os tempos de aquecimento e de arrefecimento em 20%, levando a uma redução de 15% nos tempos de ciclo globais. As propriedades térmicas melhoradas também aumentaram a qualidade dos produtos finais.
Conclusão
A otimização dos tempos de ciclo nos processos de termoformagem é essencial para alcançar uma maior produtividade, poupança de custos e uma melhor qualidade do produto. Ao implementar sistemas de aquecimento avançados, conceção eficiente de moldes, automação, monitorização em tempo real e otimização de materiais, os fabricantes podem melhorar significativamente as suas operações de termoformagem.
Os estudos de casos reais da Plastipack, AutoForm, MedPlast Solutions, PackPro e EcoPack ilustram os benefícios tangíveis destas estratégias. Cada empresa enfrentou com sucesso os seus desafios específicos e alcançou melhorias substanciais nos tempos de ciclo, levando a uma maior eficiência e competitividade.
À medida que a indústria transformadora continua a evoluir, a adoção destas estratégias de otimização será crucial para se manter à frente da concorrência e satisfazer as crescentes exigências dos clientes. Ao inovar e aperfeiçoar continuamente os seus processos, os fabricantes podem garantir um crescimento sustentável e o sucesso no mercado dinâmico da termoformagem.