Introdução
O plastic sheeting machine is one of the most essential and widely used pieces of equipment in the modern plastic processing industry. Its primary function is to convert granular or pelletized plastic raw materials into continuous sheet products, which serve as foundational materials across a variety of industries.
From food packaging and electronic device casings to medical trays and automotive parts, plastic sheet production is deeply integrated into nearly every aspect of our daily lives and industrial systems. This article provides a comprehensive look at how a sheeting machine works, its role in different industries, common production issues, key machine configurations, and the technological innovations that are shaping the future of sheet extrusion.
What Is a Plastic Sheeting Machine?
A plastic sheeting machine, also referred to as a sheet extrusion machine, is industrial equipment designed to process thermoplastic materials—such as PP, PET, PS, PVC, or ABS—into flat sheet or film-like materials. These machines are capable of producing single-layer or multi-layer sheets that vary in thickness, transparency, and mechanical strength depending on the application.
The sheets produced can be used directly or further processed through thermoforming, cutting, or lamination to manufacture final products like disposable food trays, insulation panels, clamshell packaging, and more.
How a Plastic Sheeting Machine Works
The sheeting machine operates through a multi-stage process that transforms plastic pellets into finished sheets ready for industrial use. The key stages include:
1. Feeding & Melting
Raw plastic granules are loaded into the hopper, where they are fed into the barrel by a rotating screw. As the materials move forward, external heating elements and internal friction heat the plastic, gradually converting it into a uniform molten state. The screw shear action is critical for consistent material mixing.
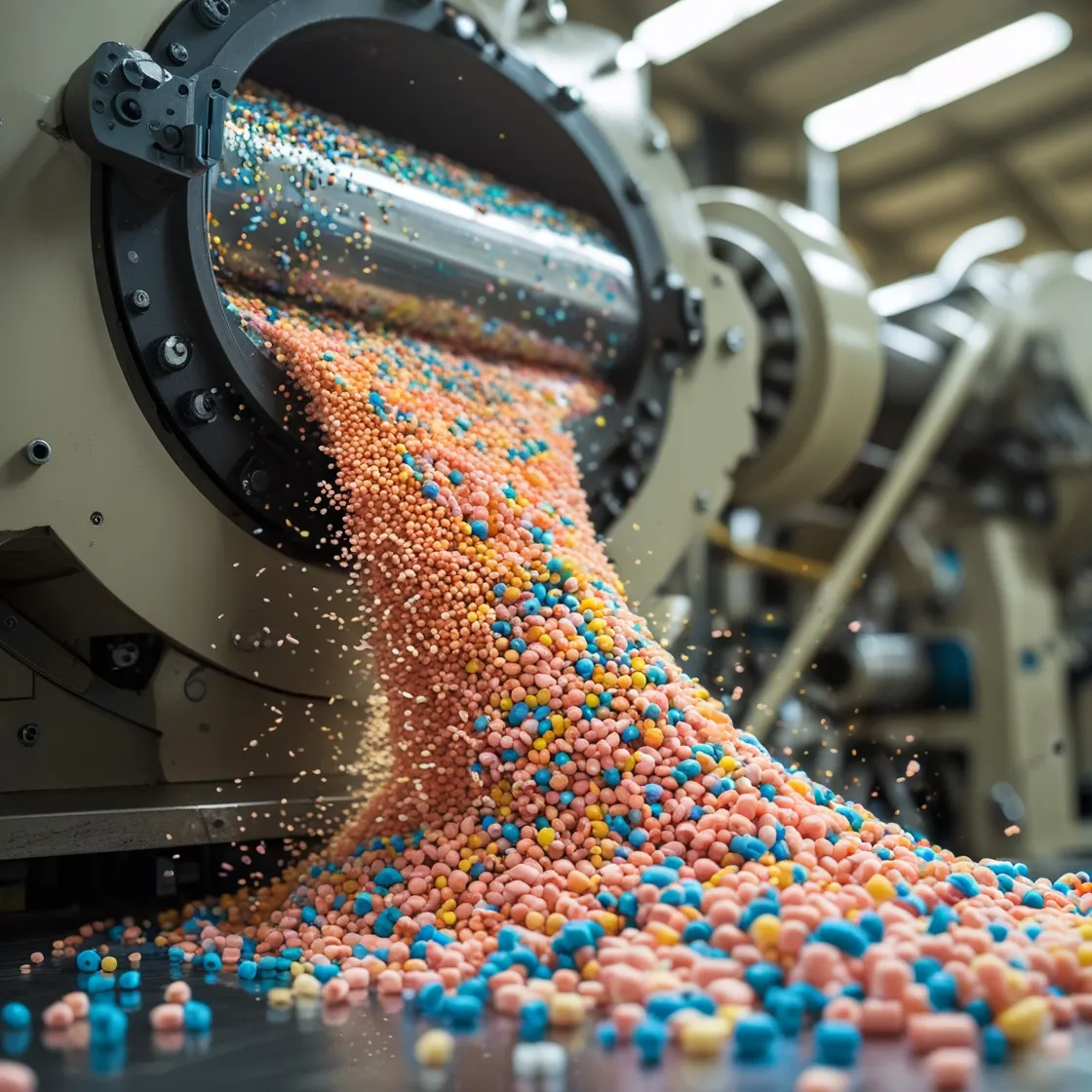
2. Extrusion Through Die Head
Once melted, the plastic is pushed through a flat die head, which determines the sheet’s width and thickness. The precision and temperature control of the die head significantly affect the uniformity and quality of the final product. Advanced die heads may include internal deckling systems for width adjustment and lip gap control.
3. Cooling & Shaping
The hot, soft sheet exits the die and enters a series of cooling rollers or chill rolls. These rollers cool the sheet rapidly, ensuring it solidifies evenly and gains structural integrity. Air knives or water sprays may also be used to assist the cooling process. The roller temperature, surface finish, and pressure directly impact the sheet’s surface clarity and thickness accuracy.
4. Haul-off & Cutting
After shaping, the sheet is pulled by a traction device at a consistent speed to avoid distortion. The sheet then passes through edge trimmers before reaching the winding or cutting unit. Depending on customer requirements, the sheet is either rolled into coils or cut into specific dimensions, often via a guillotine cutter or slitter rewinder.
Typical Machine Configuration
A standard plastic sheeting line includes:
Automatic feeder: Transfers raw material to the extruder
Single or twin-screw extruder: Melts and mixes the plastic
Screen changer & melt pump: Filters impurities and stabilizes pressure
T-die head: Shapes the molten plastic into a sheet
Three-roll calender: Smooths, shapes, and cools the sheet
Edge trimmer: Removes side scrap for recycling
Haul-off unit: Maintains consistent speed and tension
Winder or cutter: Finishes the product into rolls or sheets
Optional equipment may include corona treaters, anti-static bars, surface embossers, or automatic thickness gauges.
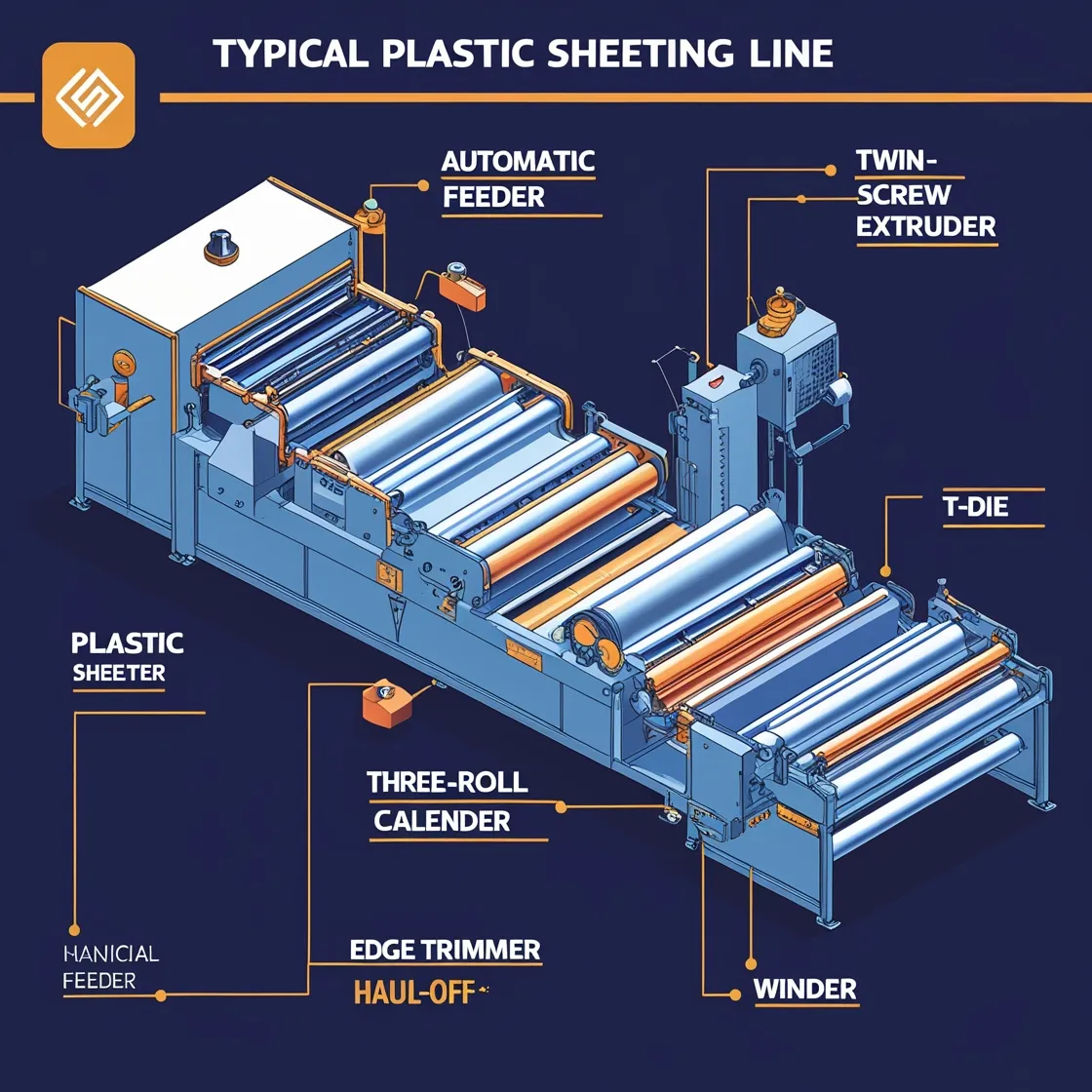
Key Applications of Plastic Sheeting Machines
The output from a plastic sheeting machine is used across numerous industries. Below are some of the most common applications:
1. Indústria de embalagens
One of the largest consumers of plastic sheets, the packaging industry uses extrusion sheets to produce:
Food-grade trays
Clamshell containers
Blister packs
Vacuum-formed packaging
Protective films
As consumer demand for safe, aesthetic, and functional packaging continues to grow, the importance of high-performance plastic sheet production becomes even more critical.
2. Electronics and Electrical Appliances
Plastic sheets are widely used in manufacturing casings and insulators for electronics. For instance:
ABS sheets are used for durable computer housings.
PS and PP sheets (with added flame retardants) are used in small appliances like hairdryers and electric kettles.
Insulating sheets prevent short circuits within devices.
3. Construction Materials
Plastic sheets can be used for:
Waterproofing membranes
Wall panels
Insulation boards
Decorative laminates
Their mechanical strength, chemical resistance, and thermal insulation make them ideal for building applications, especially in environments that require moisture control or thermal performance.
4. Indústria médica
Plastic sheet extrusion is vital in healthcare applications due to its ability to produce sterile, safe, and durable materials. Common medical products include:
Blister packaging for pharmaceuticals
Transparent medical trays
Disposable syringe covers
Infusion pump housings
These sheets meet strict hygiene and safety regulations and are often made from non-toxic, medical-grade plastics.
5. Automotive Sector
Lightweight plastic sheets are ideal for automotive applications:
Interior panels
Dashboard covers
Trunk liners
Battery casing separators
They help reduce vehicle weight, improve fuel efficiency, and resist impact and corrosion.
Common Problems in Sheet Production
Even the most well-maintained sheet extrusion lines can encounter issues such as:
Thickness inconsistency
Surface bubbles or pits
Poor edge quality
Sheet curling
These issues can be addressed through:
Precise temperature control
Stable melt pressure using gear pumps
Regular die cleaning
Proper raw material drying
Continuous monitoring systems, like laser thickness scanners, can also improve defect detection and process control.
Technology Trends: Smarter & Greener Machines
Modern plastic sheeting machines are moving toward:
Full automation: With touch-screen HMI and PLCs, operators can adjust settings quickly and safely.
IoT-enabled monitoring: Real-time data lets users track machine performance remotely.
Energy efficiency: High-efficiency motors, better insulation, and intelligent heating zones reduce power consumption.
Recycled and biodegradable materials: Machines are being upgraded to handle eco-friendly materials such as rPET, PLA, and starch-based polymers.
Conclusão
O plastic sheeting machine remains a pillar of industrial plastic manufacturing. Whether producing protective food packaging, advanced medical trays, or high-strength automotive panels, it enables large-scale, high-precision, and cost-effective sheet production.
With ongoing innovations in automation, quality control, and sustainability, sheeting machines are becoming smarter and more capable—ensuring they meet the growing demands of global industries now and in the future.