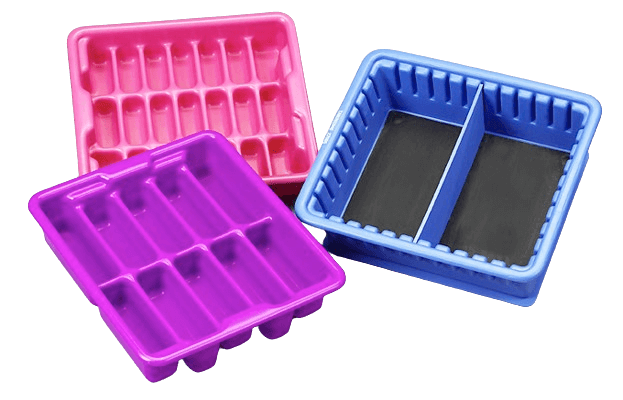
The Three Solutions for Plastic Material Processing Experts
In the realm of plastic material processing, efficiency, precision, and innovation are paramount. Whether it’s molding, extrusion, or thermoforming, the challenges faced by plastic material processing experts are diverse and demanding. To address these challenges effectively, experts seek solutions that optimize production processes, improve product quality, and drive innovation. In this article, we will explore three key solutions that empower plastic material processing experts to overcome these challenges, supported by specific case studies to illustrate their real-world application and impact.
Introduction to Plastic Material Processing Solutions
Plastic material processing encompasses a wide range of techniques and technologies, each with its own set of challenges and opportunities. From injection molding to blow molding and beyond, experts in this field are constantly seeking innovative solutions to enhance efficiency, accuracy, and quality in their operations. The following three solutions represent some of the most effective approaches to addressing these challenges and achieving success in plastic material processing.
Solution 1: Advanced Molding Technologies
Overview:
Advanced molding technologies encompass a range of techniques and processes that leverage cutting-edge innovations to optimize the molding process. From high-speed injection molding to multi-material molding and micro-molding, these technologies offer unprecedented levels of precision, flexibility, and efficiency.
Case Study: Precision Automotive Components
Company: ABC Molding Solutions
Challenge: ABC Molding Solutions, a manufacturer of automotive components, faced challenges in producing complex geometries and tight tolerances required for precision parts. Traditional molding methods were unable to meet the stringent quality standards and production volumes demanded by their customers.
Solution: ABC Molding Solutions implemented advanced molding technologies, including high-speed injection molding and micro-molding, to produce precision automotive components with exceptional accuracy and repeatability. By optimizing process parameters and tooling designs, they achieved significant improvements in part quality and cycle times.
Result: By leveraging advanced molding technologies, ABC Molding Solutions improved part quality, reduced cycle times by 20%, and increased production volumes to meet growing customer demand. Their ability to produce precision automotive components with unmatched accuracy and efficiency strengthened their position in the market and enhanced customer satisfaction.
Solution 2: Intelligent Process Control Systems
Overview:
Intelligent process control systems utilize advanced sensors, data analytics, and automation to monitor and optimize every aspect of the plastic material processing process. By collecting real-time data, analyzing performance metrics, and making data-driven adjustments, these systems ensure optimal process efficiency and product quality.
Case Study: Optimized Extrusion Processes
Company: XYZ Extrusion Technologies
Challenge: XYZ Extrusion Technologies, a manufacturer of plastic extrusion products, faced challenges in achieving consistent product quality and maximizing production efficiency. Variations in material properties, processing conditions, and equipment performance resulted in quality defects and production delays.
Solution: XYZ Extrusion Technologies implemented an intelligent process control system equipped with advanced sensors and data analytics capabilities. By continuously monitoring key process parameters such as temperature, pressure, and material flow rate, the system identified deviations and made real-time adjustments to optimize extrusion processes.
Result: By leveraging intelligent process control systems, XYZ Extrusion Technologies achieved significant improvements in product quality, reducing defect rates by 30% and improving production efficiency by 25%. The system’s ability to detect and correct process variations in real-time enhanced overall operational reliability and customer satisfaction.
Solution 3: Innovative Thermoforming Technologies
Overview:
Innovative thermoforming technologies leverage advancements in materials science, machine design, and process optimization to push the boundaries of what’s possible in thermoforming. From advanced heating systems to digital twin simulations and 3D printing integration, these technologies enable manufacturers to achieve unparalleled levels of flexibility, customization, and efficiency.
Case Study: Customized Packaging Solutions
Company: DEF Thermoforming Innovations
Challenge: DEF Thermoforming Innovations, a provider of packaging solutions, faced challenges in meeting the diverse needs of their customers for custom packaging designs and small batch production. Traditional thermoforming methods limited their ability to produce complex shapes and designs efficiently.
Solution: DEF Thermoforming Innovations adopted innovative thermoforming technologies, including digital twin simulations and 3D printing integration, to streamline the design and production process. By simulating forming processes digitally and rapidly prototyping designs with 3D printing, they accelerated product development cycles and enabled quick iteration of custom packaging solutions.
Result: By embracing innovative thermoforming technologies, DEF Thermoforming Innovations improved their ability to deliver customized packaging solutions with shorter lead times and higher precision. The integration of digital twin simulations and 3D printing reduced design iterations by 50% and enabled them to meet the demands of their customers for custom designs and small batch production effectively.
Conclusion
The three solutions outlined above represent powerful tools and strategies for plastic material processing experts to overcome challenges, drive innovation, and achieve success in their operations. By leveraging advanced molding technologies, intelligent process control systems, and innovative thermoforming technologies, experts can optimize production processes, improve product quality, and meet the evolving demands of their customers. Real-world case studies illustrate the tangible benefits and transformative impact of these solutions, highlighting their effectiveness in driving efficiency, precision, and innovation in plastic material processing operations. As the industry continues to evolve, embracing these solutions will be essential for staying ahead of the curve and maintaining a competitive edge in the dynamic world of plastic material processing.