Choosing the right thermoforming control panel is crucial for ensuring efficient, safe, and precise operation in modern manufacturing environments. From user-friendly interfaces to real-time monitoring, a high-quality thermoforming control panel display can significantly enhance productivity and minimize downtime. This guide covers the most important features to consider, explains how they can impact production, and explores the future of thermoforming technology.
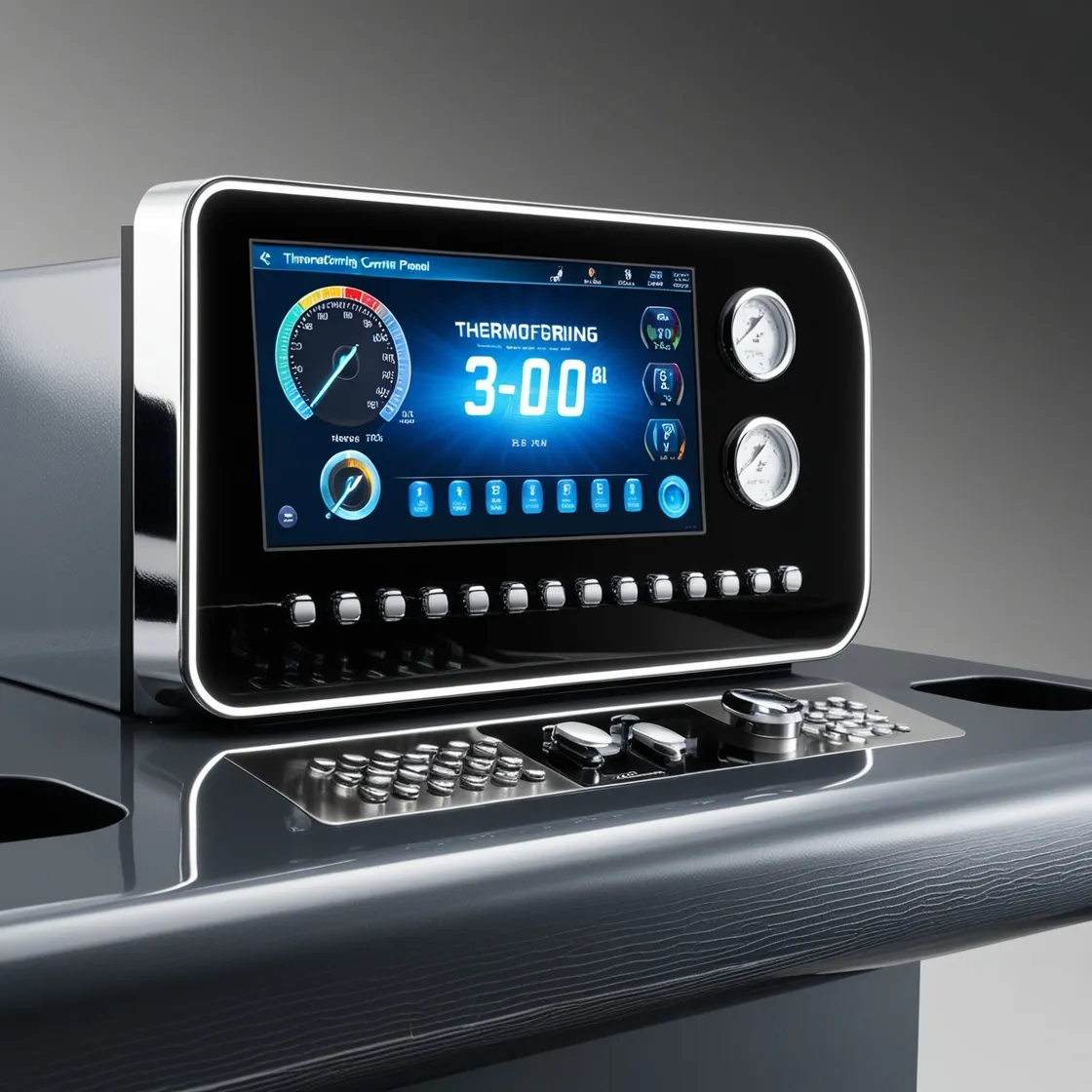
Introduction
In today’s competitive manufacturing landscape, the thermoforming control panel plays an integral role in optimizing production processes, maintaining high-quality standards, and reducing operational costs. Whether you’re manufacturing food packaging, automotive components, or medical devices, selecting a thermoforming control panel with the right features can streamline operations, enhance safety, and prevent costly downtime.
Why a High-Quality Thermoforming Control Panel Matters
The thermoforming control panel serves as the brain of your thermoforming machine. It allows operators to manage every aspect of the machine’s operation, from adjusting settings to troubleshooting errors. A well-designed thermoforming control panel enhances production efficiency, ensures high-quality output, and improves overall safety. The better the control panel, the easier it is for operators to control machines accurately and troubleshoot issues before they escalate.
For example, in industries where precision is essential—such as automotive or medical manufacturing—a reliable thermoforming control panel ensures that each product meets the highest standards. The control panel acts as a central hub for monitoring machine parameters like temperature, pressure, and cycle time. An operator using an intuitive thermoforming control panel can make quick adjustments, reducing the risk of errors and ensuring smooth production.
Key Features of a Modern Thermoforming Control Panel Display
User-Friendly Touchscreen Interface
A thermoforming control panel with a user-friendly touchscreen interface is indispensable for modern production environments. The ease of navigation offered by advanced touchscreens allows operators to perform complex tasks without requiring extensive training. Today’s thermoforming control panels often feature graphical representations of machine parts, making operations like adjusting settings or initiating machine functions more intuitive.
Imagine a production line producing PET packaging. An operator uses the thermoforming control panel to adjust the heating elements in real-time, ensuring precise thermoforming of the material. The touchscreen interface allows quick adjustments, minimizing material waste and maximizing efficiency.
Multi-Language Support for Global Operations
For companies with international operations, multi-language support in the thermoforming control panel is a critical feature. By enabling operators to switch between languages, these panels ensure that workers from different regions can use the machines effectively without confusion. In global production plants, having a thermoforming control panel that offers this flexibility reduces the risk of communication errors and ensures smoother operations.
Consider a manufacturing facility in Asia producing thermoformed plastic parts for global distribution. The team operates the machinery using a thermoforming control panel that supports English, Mandarin, and Spanish. This multi-language functionality ensures that all operators understand the system, regardless of their native language, and production runs without a hitch.
Real-Time Data Monitoring and Display
Real-time monitoring is a must-have feature in any modern thermoforming control panel. The ability to monitor crucial machine metrics—such as temperature, speed, and pressure—in real-time helps operators ensure consistent product quality and troubleshoot issues before they become significant problems. With real-time feedback, operators can immediately see if a machine is deviating from set parameters, allowing them to make necessary adjustments.
For instance, when thermoforming automotive parts, maintaining a stable temperature is crucial. A thermoforming control panel that displays real-time temperature data enables the operator to make instant corrections, ensuring that the parts meet safety and performance standards. This reduces the chances of defective parts and costly rework.
Remote Access and Control Features
Remote access is another essential feature of advanced thermoforming control panels. With remote monitoring capabilities, operators or technicians can control the machine from anywhere, allowing for greater flexibility and faster response times in case of an issue. This feature is especially useful for companies with multiple production lines or facilities in different locations.
For example, if a technician receives an alert from the thermoforming control panel regarding a machine error, they can access the panel remotely, diagnose the issue, and even adjust machine settings to fix the problem. This not only reduces downtime but also allows for centralized control of multiple machines from a single location.
Advanced Data Storage and Analytics
Data analytics and storage are becoming increasingly important in thermoforming operations. A thermoforming control panel that stores data on machine performance can provide valuable insights into production trends, identify inefficiencies, and help predict maintenance needs. By leveraging data collected from the thermoforming control panel, manufacturers can make data-driven decisions to optimize their production processes.
For instance, a factory producing custom thermoformed clamshell containers could use data from the thermoforming control panel to analyze cycle times and identify bottlenecks. With this information, operators can adjust machine settings to increase production efficiency and reduce downtime, resulting in higher output and lower operating costs.
Safety and Alarm Systems for Optimal Performance
Safety should always be a top priority in any manufacturing setting, and the thermoforming control panel plays a crucial role in maintaining a safe working environment. Modern control panels come equipped with advanced alarm systems that notify operators when the machine exceeds safe operating thresholds, such as temperature spikes or pressure fluctuations.
Imagine a scenario where a thermoforming machine begins to overheat during production. The thermoforming control panel would immediately alert the operator through both visual and auditory alarms, allowing them to take corrective action before any damage occurs. Some panels also feature automated shutdown systems, which halt operations when a critical issue is detected, preventing potential hazards and equipment failure.
Customization and Flexibility in Thermoforming Control Panels
Every manufacturing environment is unique, and customizable thermoforming control panels allow businesses to tailor machine settings to their specific production needs. From modifying the layout of the control interface to adding custom features, a flexible thermoforming control panel can significantly improve operational efficiency.
For example, a company producing a wide range of thermoformed products may frequently change production specifications. With a customizable thermoforming control panel, operators can create shortcuts for frequently used settings, adjust interface layouts, and ensure optimal visibility in varying lighting conditions.
IoT Integration and Industry 4.0 in Thermoforming Control Panels
The rise of Industry 4.0 has introduced the integration of IoT (Internet of Things) into thermoforming control panels. IoT-connected control panels can collect data from multiple machines, allowing operators to monitor production lines from a central location. This real-time data sharing across systems enhances machine efficiency, reduces energy consumption, and improves overall production quality.
A real-world example of this would be a multi-site manufacturer using IoT-enabled thermoforming control panels to oversee production across different locations. The centralized data allows them to spot performance trends, schedule maintenance, and ensure optimal machine settings remotely.
The Future of Thermoforming Control Panels
As technology evolves, we can expect future thermoforming control panels to become even more advanced. Features like augmented reality (AR) displays, voice-controlled interfaces, and AI-driven predictive maintenance are on the horizon. These innovations will further improve the efficiency and usability of thermoforming control panels, enabling even more precise control over production processes.
Imagine a future where an operator can control a thermoforming machine through voice commands or visualize machine operations in real-time using AR glasses. These innovations will likely be integrated into future thermoforming control panels, further enhancing productivity and reducing the potential for errors.
Maintaining and Troubleshooting Your Thermoforming Control Panel
Proper maintenance is essential to prolonging the life of your thermoforming control panel. Regular cleaning, software updates, and sensor calibration are basic tasks that help ensure the panel operates smoothly. Many modern thermoforming control panels come with built-in diagnostic tools that make troubleshooting easier and faster.
In case of malfunctions, the thermoforming control panel logs errors, which technicians can review to identify the root cause of the problem. Remote access to the thermoforming control panel also allows experts to troubleshoot and resolve issues without needing to be physically present.
Conclusion
Investing in a high-quality thermoforming control panel can revolutionize your production process by enhancing efficiency, safety, and precision. Features like touchscreen interfaces, remote access, real-time monitoring, and IoT integration ensure that businesses stay competitive in today’s fast-paced manufacturing environment. As technology advances, thermoforming control panels will continue to evolve, providing smarter, more connected solutions for manufacturers across industries.
FAQs
- Why is real-time monitoring important in a thermoforming control panel? Real-time monitoring allows operators to track crucial machine metrics and make adjustments on the go, ensuring that production remains smooth and efficient.
- Can a thermoforming control panel help reduce downtime? Yes, features like remote access and predictive maintenance in modern thermoforming control panels can help identify issues before they cause machine failure, reducing downtime.
- What is the benefit of IoT integration in thermoforming control panels? IoT integration enables thermoforming control panels to collect and analyze data from multiple machines, optimizing production efficiency and reducing energy consumption.
- How does a touchscreen interface improve the usability of a thermoforming control panel? A touchscreen interface simplifies navigation and operation, making it easier for operators to control machines and adjust settings without extensive training.
- Is customization possible with modern thermoforming control panels? Yes, many thermoforming control panels offer customization options, allowing operators to modify the interface layout and machine settings to meet specific production needs.