Thermoforming molds are essential in manufacturing plastic parts by shaping heated plastic sheets into specific forms. The choice of mold material directly impacts the efficiency, durability, and quality of the production process. This article explores various materials used to manufacture thermoforming molds, including aluminum, steel, composites, and phenolic resins. Each material offers distinct benefits, and selecting the right one depends on the specific needs of the thermoforming process, such as cycle times, part complexity, and cost efficiency.
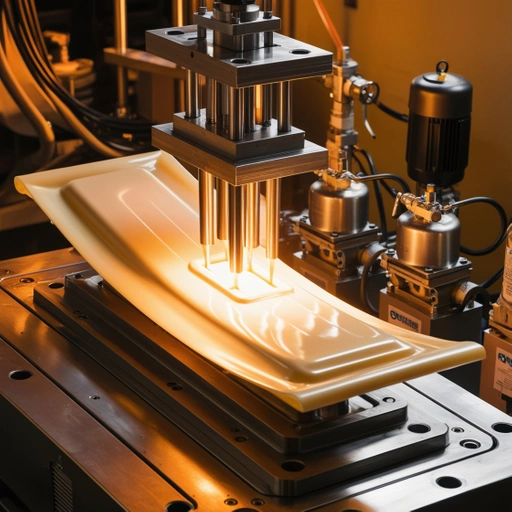
1. Aluminum Molds
Aluminum is one of the most commonly used materials for thermoforming molds. Its widespread use is due to a combination of affordability and excellent properties that suit industrial production.
Key Advantages of Aluminum Molds
Thermal Conductivity: Aluminum’s superior thermal conductivity enables it to absorb and distribute heat evenly across the mold’s surface. This property reduces heating time and shortens each production cycle, a critical factor in high-volume manufacturing. Faster cycles not only boost productivity but also lower energy consumption, resulting in significant savings.
Strength-to-Weight Ratio: Aluminum is both lightweight and strong, providing the structural stability required for repeated mechanical stress. Its reduced weight minimizes wear on equipment, which extends the lifespan of machinery used in the process.
Corrosion Resistance: Aluminum resists corrosion even when exposed to high temperatures and plastic materials such as PP, PS, or PET. This stability minimizes maintenance costs and extends the mold’s life.
Aluminum molds are particularly suitable for industries that require frequent production with short cycle times and reliable performance, making them a popular choice across various thermoforming applications.
2. Steel Molds
Steel, especially stainless steel, is another prominent material used in thermoforming mold manufacturing. Steel molds are known for their exceptional mechanical properties, durability, and ability to produce complex, high-precision parts.
Key Benefits of Steel Molds
Wear Resistance: Steel molds maintain performance even under continuous use, making them ideal for high-intensity production environments. The material’s resistance to physical wear extends the mold’s life and ensures consistent output over time.
Precision and Complexity:Steel molds are highly processable, allowing the creation of detailed geometries, sharp edges, and intricate designs. This makes them suitable for producing complex parts with fine details and high-quality surface finishes.
High Tensile Strength: Steel retains dimensional stability under high temperatures, preventing deformation, cracking, or other issues during the repeated heating and cooling cycles of thermoforming. This reliability ensures consistent mold performance.
Steel molds are particularly favored in applications where precision, durability, and high production volumes are essential.
3. Composite Molds
In recent years, the use of composite materials such as epoxy and carbon fiber-reinforced polymer (CFRP) has increased. These materials offer unique benefits in terms of strength, weight, and energy efficiency.
Characteristics of Composite Molds
Dimensional Stability and Strength:Composite molds are lightweight yet strong enough to handle high-pressure forming processes effectively.
Thermal Insulation: While composites have lower thermal conductivity than metal molds, they offer better thermal insulation, improving energy efficiency during the molding cycle.
Composite molds are a good choice for applications where lightweight design and energy savings are prioritized, though they may not be as durable as metal molds for long-term use.
4. Phenolic Resin Molds
Phenolic resin molds are widely used in scenarios where cost-effective solutions are required. These molds provide excellent thermal and chemical stability while being affordable, making them ideal for short-term or low-volume production projects.
Key Advantages of Phenolic Resin Molds
Thermal Stability:Phenolic resin molds can maintain shape and dimensional accuracy under high temperatures, ensuring consistent performance over repeated thermal cycles.
Chemical and Abrasion Resistance:These molds resist corrosion from chemicals and wear from physical friction, maintaining their effectiveness even when used with various plastic materials like PE, PP, or PET.
Surface Finish Quality:Phenolic resin molds produce smooth, high-quality surfaces, reducing the need for additional polishing or finishing.
Cost Efficiency:Due to their low production and maintenance costs, phenolic resin molds are ideal for prototype manufacturing, trial products, and short production runs.
Phenolic resin molds provide companies with a flexible, economical solution, especially when rapid production or limited budgets are involved.
How Does a Thermoforming Mold Work?
A thermoforming mold plays a critical role in shaping plastic sheets into final products. The process involves heating a plastic sheet to a pliable state, placing it over the mold, and forming it into the desired shape through vacuum or pressure. Below is a step-by-step overview of how thermoforming molds work:
1. Heating the Plastic Sheet
The process begins with clamping and heating a plastic sheet—typically made from PET, PP, PS, or PVC—until it becomes soft but not melted. The heating temperature generally ranges between 140°C and 180°C, depending on the plastic material.
2. Mold Contact
Once the sheet reaches the desired temperature, it is positioned over the mold. The mold can either have a convex (positive) or concave (negative) shape, depending on the design.
Vacuum Forming:A vacuum system pulls the heated plastic tightly against the mold surface, ensuring the material conforms to the mold’s shape.
Pressure Forming:Compressed air applied from above the plastic and vacuum from below allow for finer details and sharper edges to form.
Mechanical Assistance:Some molds use mechanical plugs or pistons to pre-stretch the plastic, ensuring uniform wall thickness in deep-drawn parts.
3. Cooling and Shaping
Cooling the formed plastic is essential to preserve the product’s shape. Molds often have internal cooling channels to accelerate this step, preventing warping or shrinkage.
4. Trimming the Formed Part
Once the plastic cools and hardens, the part is separated from the sheet. Any excess material around the edges, known as “flash,” is trimmed. Large-scale operations often use automated CNC machines for precise cutting.
5. Final Touches
Post-processing steps such as drilling, embossing, or punching may follow. The surface finish of the product reflects the mold’s texture, eliminating the need for further polishing.
Examples of Thermoforming Molds
Thermoforming molds are used across a variety of industries. Below are some examples:
Clamshell Packaging Molds:Used for transparent packaging in consumer goods, made from PET or PVC.
Food Packaging Molds:Produce trays, lids, and containers for food items, typically using PP, PET, or PS.
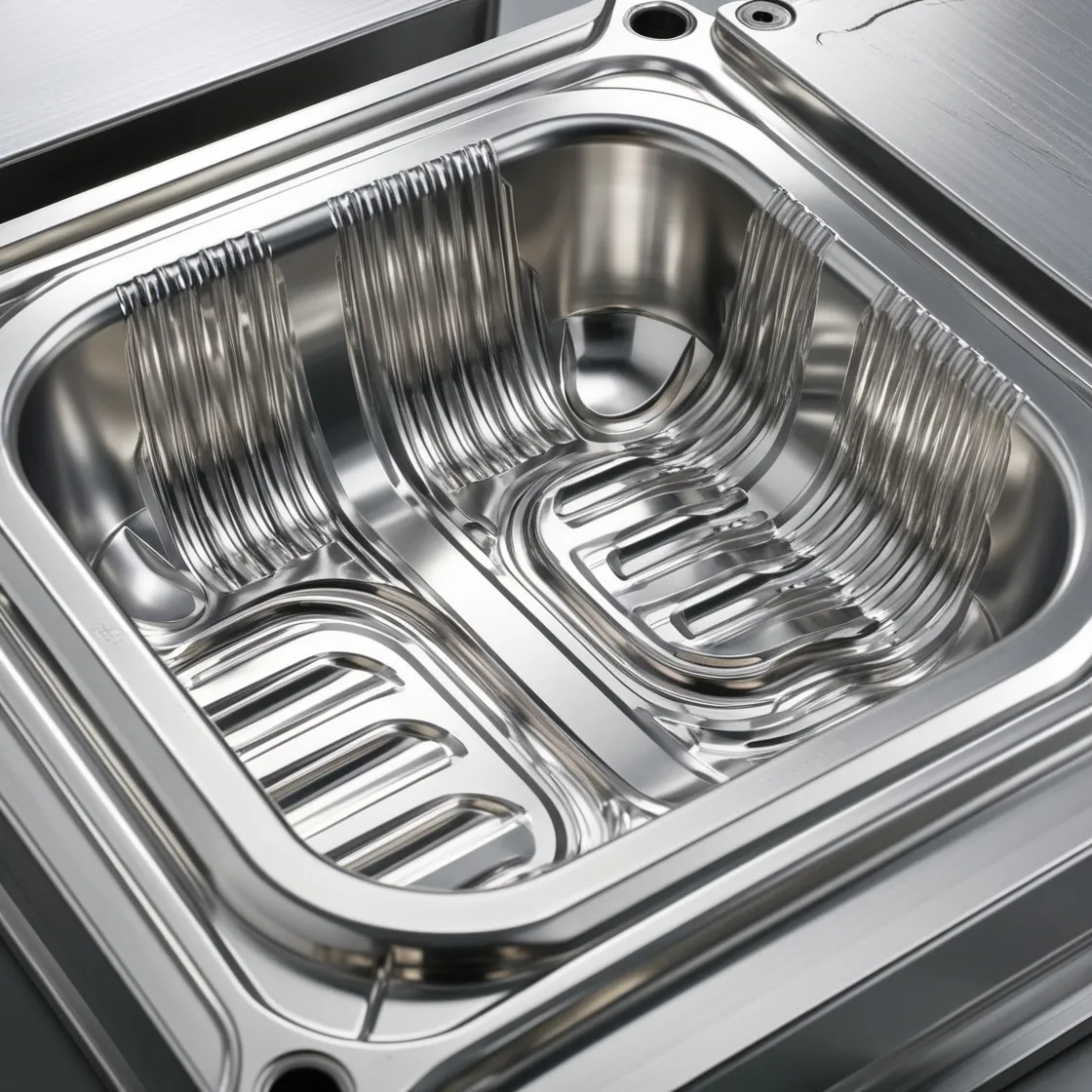
Medical Device Packaging Molds:Create sterile packaging for medical devices, using PET or high-barrier materials.
Disposable Cup and Lid Molds:Produce plastic drinkware with detailed ribbing or textures, using PP, PS, or PET.
Blister Packaging Molds:Form clear compartments for pharmaceuticals or small electronics, typically using PVC or PET.
Point-of-Sale Display Molds:Create custom trays and displays for retail environments, using PET or PVC.
Conclusion
Choosing the right material for thermoforming molds is crucial for ensuring successful production. Aluminum and steel offer high strength and durability, while composites provide lightweight, energy-efficient options. Phenolic resins excel in chemical resistance and surface finish quality, making them ideal for short-term projects. Ultimately, the choice of mold material depends on factors such as production cycle time, product complexity, and budget considerations. With the right mold material and design, businesses can achieve efficient and cost-effective thermoforming processes.
This comprehensive guide highlights the essential materials and their properties, ensuring that manufacturers make informed decisions for optimal production results.