Servo motors are crucial in modern automation and robotics, providing precision control over positioning, speed, and torque. Whether you’re in industrial automation or working with complex robotics, understanding servo motors and their operational principles can greatly enhance your ability to integrate them effectively. This guide explores servo motor components, the working mechanism, types, and significant advantages, helping you make informed decisions for your applications.
What is a Servo Motor?
A servo motor is a specialized DC motor equipped with a feedback system to allow precise control over position and movement. Unlike regular DC motors, servo motors are restricted to rotating within a specific range—typically between 90° and 180°—although some models can rotate up to 360°. The motor’s design enables controlled positioning within set angles, making it ideal for applications requiring accurate control, from robotics to industrial machinery.
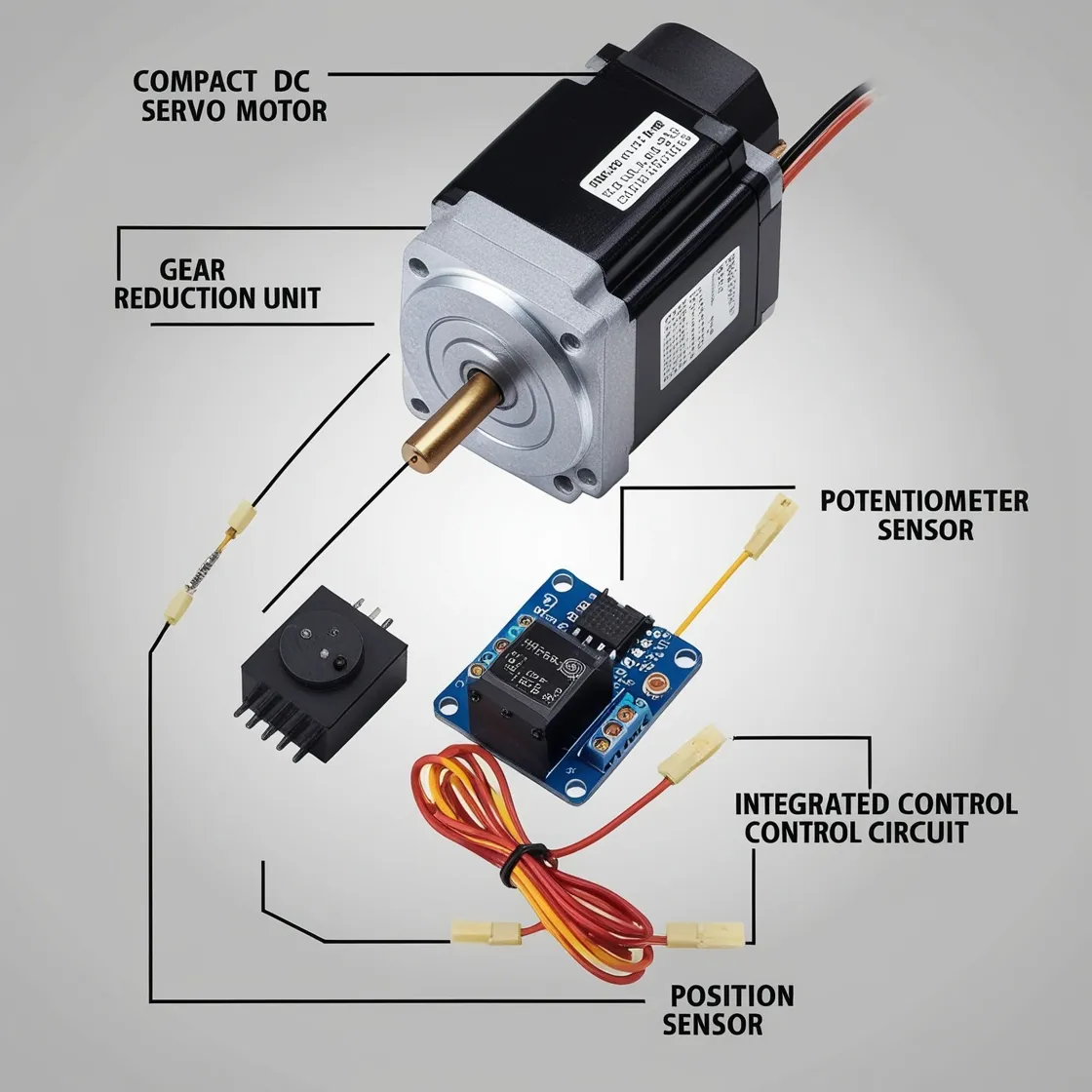
Key Components of a Servo Motor
Understanding the key components of a servo motor is essential for grasping how it works:
- DC Motor: The motor itself generates rotational movement.
- Gear Reduction Unit: Slows down motor speed to allow for more refined position control.
- Position-Sensing Device: Often a potentiometer, this sensor provides feedback to the control system, indicating the motor’s current position.
- Control Circuit: Processes the feedback and adjusts the motor’s position in response to the control signal.
Each component plays a critical role in enabling the servo motor to achieve precise control over its movements, setting it apart from other types of motors.
How Does a Servo Motor Work?
Servo motors operate by receiving a control signal that dictates the desired position of the shaft. The control circuit then applies power to the DC motor, adjusting its position until the shaft reaches the target angle. This process involves continuous monitoring of the current position through the position-sensing device (either an encoder or a potentiometer), ensuring consistent accuracy and alignment.
The servo motor control system continuously compares the motor’s position with the target position, adjusting as needed to maintain the desired angle. This control loop is what allows servo motors to deliver precise positioning in even the most demanding applications.
Electrical Connections in a Servo Motor
Servo motors typically include three main wires, each with a distinct purpose:
- Black Wire: Ground connection.
- Red Wire: Power supply.
- White/Yellow Wire: Control signal input.
These wires help the servo motor receive and process control signals to adjust movement and position.
Rotation and Movement
Servo motors achieve controlled angular movement by creating a rotating magnetic field through current flow in the windings. This magnetic field, together with an optical encoder for tracking rotations, enables precise positioning. To maintain accuracy, servo motor rotation is typically limited to around 200 degrees. This rotation limitation allows for precise control, essential for applications where exact positioning is critical.
Special Features of Servo Motors
Servo motors are packed with features that make them valuable in various automation and industrial applications:
- Torque Generation: Servo motors often use rare earth or permanent magnets to produce high torque efficiently, even in compact designs.
- Gear Material Options: Plastic gears are common in standard servo motors, while high-power models often use metal gears for added durability.
These features enhance the versatility and performance of servo motors, allowing for robust application in robotics, automation, and other fields requiring detailed control.
Comparing Motor Types in Servo Systems: AC vs. DC Motors
In servo systems, both AC and DC motors are commonly used, depending on the application requirements.
Asynchronous AC Motors
Primarily used in speed-controlled systems, asynchronous AC motors are suitable for applications requiring steady speed control rather than high performance. While not always ideal for precision applications, they are effective in systems where speed stability is the primary concern.
Synchronous AC Motors
Synchronous AC motors are a popular choice for high-performance servo systems. Driven by sinusoidal waveforms, synchronous motors offer smooth speed control down to 0 RPM with a steady torque profile. This type of motor is ideal for applications demanding high precision, such as CNC machinery and advanced automation systems.
Brushed DC Motors
Brushed DC motors feature a straightforward design and are relatively easy to control, making them common in basic applications. However, the brushes in these motors can wear out over time, affecting long-term reliability.
Brushless DC Motors (BLDC)
Known for reliability and efficiency, brushless DC motors are frequently used in industrial servo applications. These motors employ trapezoidal commutation and deliver an excellent balance of cost-effectiveness and performance. Although they may experience slight vibration at low speeds due to “cogging,” brushless DC motors remain a top choice for industrial applications.
In summary, brushless DC motors are preferred in most industrial settings due to their performance and cost-effectiveness.
Servo Motor Control with PLC Systems: Essential Components and Setup
Servo motor systems often require integration with Programmable Logic Controllers (PLCs), which act as intermediary controllers for advanced automation. The primary components needed include:
- PLC: Provides high-speed pulse output.
- Servo Drive: Acts as an intermediary, interpreting PLC signals.
- Servo Motor: The final actuator that responds to control signals.
Basic Operating Principle
The PLC generates command pulses, which the servo drive interprets and converts into motor rotation. The typical relationship is as follows:
- 1000 pulses= 1 complete rotation (360°).
- Example: 500 pulsesresult in a 180° rotation.
Pulse Signal Characteristics
- Frequency: Typically around 20 KHz.
- Total Pulse Count: Determines the rotation angle.
- Frequency Control: Controls motor speed, with higher frequencies enabling faster rotations.
PLC Requirements and Programming
For proper operation, the PLC must support high-speed pulse output and be capable of accurate pulse timing. Programming should include logic for pulse generation, frequency adjustment, and position control, as well as speed regulation through pulse frequency.
Key Advantages of Servo Motors
Servo motors offer a range of advantages, particularly in industrial and precision applications:
- Energy Efficiency: Servo motors consume power only when active and require minimal power in standby mode, resulting in lower operational costs.
- Low Noise: Quiet operation is ideal for environments with strict noise requirements, such as medical and food packaging industries.
- Programmability: Servo motors support programmable control, allowing for customized automation in different scenarios.
- Adaptability to Variable Conditions: Servo motors can manage complex conditions, maintaining consistent output even with fluctuating loads.
- Compact Design: Lightweight and easy to install, servo motors save space, making them suitable for automation in confined spaces.
- Minimal Maintenance Needs: Brushless servo motors require little upkeep, as they lack wear-prone brushes, which reduces downtime and maintenance costs.
- Precise Speed and Position Control: Servo motors maintain stable performance at varying speeds, enhancing efficiency and reducing material waste.
These benefits make servo motors a preferred choice for industries that require adaptability, accuracy, and long-term reliability.
What is Inside a Servo Motor?
Servo motors are composed of several key components working in a feedback loop:
- DC or AC Motor: Generates the rotation necessary for positioning.
- Gear Reduction Unit: Reduces output speed while increasing torque.
- Position Sensor: Monitors the motor’s current position.
- Control Circuit: Uses position feedback to regulate the motor’s position and speed.
- Output Shaft: Connects to the load and holds precise positioning.
- Wiring: Power, ground, and control wires.
- Permanent Magnets: Creates the rotating magnetic field essential for torque generation.
This feedback loop enables precise control, which is vital for applications in robotics, manufacturing, and automation.
Why Servo Motors Do Not Have Fans
Unlike traditional motors, servo motors are designed to minimize heat output through the following factors:
- High Efficiency: Servo motors convert most power into motion, minimizing excess heat.
- Intermittent Operation: They often work in short bursts, limiting heat buildup.
- Passive Heat Dissipation: Using aluminum casings or fins, servo motors naturally release heat.
- Low Noise and Vibration: Operating without a fan reduces noise, making servo motors suitable for applications requiring quiet operation.
- Brushless Design: Many servo motors are brushless, which generates less internal heat.
A close-up view of a high-performance electric motor showcasing its robust design and precision-engineered rotor.